A Primer on pH Measurement
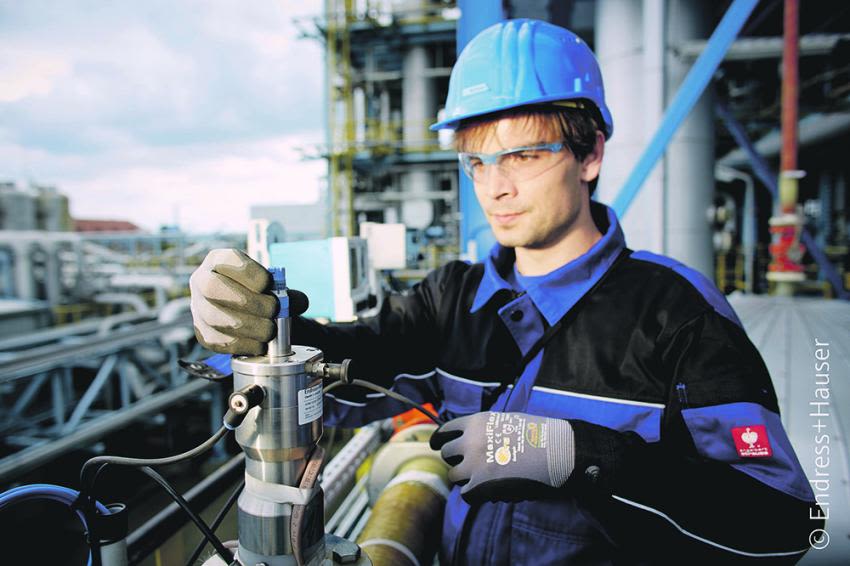
Understand the basic principles of operation and construction designs of glass membrane sensors can help in choosing the right pH sensor.
One of the most critical measurements in liquid chemical processing is pH. In this article, the importance of the sensor construction to ensure quality measurements is discussed, as well as the critical factors to consider when choosing a pH sensor. This article also explores the key differences between analog and digital sensors. Finally, readers will learn how digital sensors can improve workers’ safety while decreasing the maintenance efforts and lowering the possibility of measurement value drift.
Background
The glass electrode pH meter, as we know it today, was first invented by Arnold Beckman in 1934 [1]. As with many scientific breakthroughs, the impetus for the development of a new technology came from a specific market need. In this case, it was the citrus industry of California that called for an accurate measure of acidity that would not be influenced by the presence of sulfur dioxide preservatives. Beckman’s invention was based on the principle that measuring the activity of H + ions in a solution informs us about its concentration.
Beckman’s glass-tube electrode method of measuring pH is still used today. However, several developments have helped to improve the reliability and longevity of modern devices. pH measurement is not only critical in the citrus industry, other industries like pharmaceuticals, food and beverages, and water treatment all rely on accurate pH measurement (Figure 1). Understanding the functional principles of pH measurement and developments in the technology is key to choosing the most suitable pH sensor for each application.
Basic principles of pH measurement
In pure water, a small number of molecules dissociate into H+ and OH– ions:
H 2 O I H + + OH –
The extent of this dissociation can be described by the self-ionization constant of water, K w, which depends only on the temperature.

At 25°C, Kw = 1.01 ×10 –14 for pure water. When acids or bases are added to the water, the number of ions change, but Kwremains the same, which allows us to use a consistent pH scale for all aqueous solutions. An acid has a higher activity of H+ions than OH– ions, while a neutral solution has an equal activity of both. An alkaline solution has a lower activity of H+ ions than OH– ions. The relationship of pH and H+ activity, a(H+), is defined by a logarithmic equation:

In pure water, there is an equilibrium between H+ and OH–, so at 25°C, the activity of H+ is nearly 10–7. From Equation (2), the pH of pure water is –log 10 (10–7) = 7, which is defined as neutral. For concentrations of H+ greater than 10–7, the pH will be less than 7 (acidic) and for concentrations less than 10–7, the pH will be greater than 7 (alkaline).
A pH sensor is effectively an electrochemical cell that changes its electrical potential on a glass membrane based on the activity of H+ ions. The pH is directly proportional to the measured voltage. Because all other voltages in the cell are designed to remain constant, it is only the voltage generated across the glass membrane that represents the solution pH. The physical fundament of this voltage generation on the glass membrane is described by the Nernst equation:

Where:
U = sensor voltage, mV
U0 = voltage at pH 7.0, mV
R = gas constant
T = temperature, K
n = load of ion (H+ = 1)
F = Faraday constant
Converting from natural logarithms to base ten gives Equation (4)

Equation (4) is nearly a linear relationship between the measured voltage and pH, with a slope of approximately 59.16 mV/pH at 25°C.
The basic construction of a pH sensor includes certain components, as shown in Figure 2. It has two half cells joined in an electrochemical circuit.
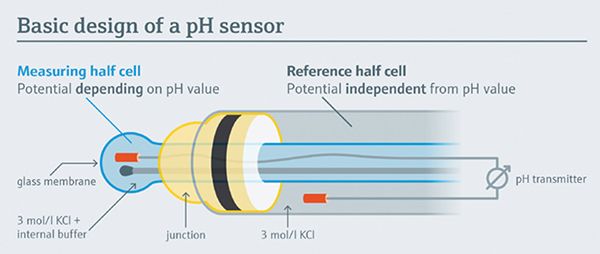
FIGURE 2. A basic pH sensor design is shown here
FIGURE 2. A basic pH sensor design is shown here
The reference half cell. The reference half-cell (Figure 2) has a silver chloride element attached to a silver wire, which is inserted into a glass tube often containing 3 mol/L potassium chloride solution and a carrier gel matrix. The gel stabilizes the potassium chloride and helps keep the diffusion and substance exchange via the junction low. For a stable and reliable measurement, the concentration of potassium chloride should remain stable as long as possible. A junction separates the reference solution from the test solution and plays a vital role in cell performance. The junction forms a galvanic connection and thus allows the flow of ions to enable the electrochemical circuit to function. However, it must not allow the reference solution to be contaminated by the test material, nor allow the potassium chloride electrolyte to diffuse out of the sensor.
The measuring half cell. The measuring half-cell also contains a silver wire and silver chloride element. But this half-cell is galvanically separated from the test solution and has a glass membrane bulb, which is sensitive to changes in pH. The internal buffer solution is potassium chloride, and the outside of the glass membrane is exposed to the test material. The difference in activity of H+ ions inside and outside the membrane creates a differential voltage, which is proportional to the pH of the test solution.
Ion exchange. A close-up view of the glass membrane (Figure 3) shows a gel layer on the inside and outside surface. This gel layer has a sophisticated structure that allows H+ ions to migrate and form a potential. Each pH sensor brand has its own unique gel formulation using specially developed glass mixtures.
Temperature compensation. A crucial factor for pH measurement is temperature compensation. Modern sensors come with an embedded temperature probe to measure the actual temperature of the test solution. This is crucial because an increase in temperature causes the H+ and OH– ions to become excited and increase their activity. Measuring the same acidic test solution will give a lower reading (more acidic) at a higher temperature than at a lower temperature, because the sensor detects an increase in H+ ion activity but not the corresponding increase in OH– ion activity. Temperature compensation allows the effects of temperature to be removed at the sensor so that the reading remains accurate regardless of temperature variations.
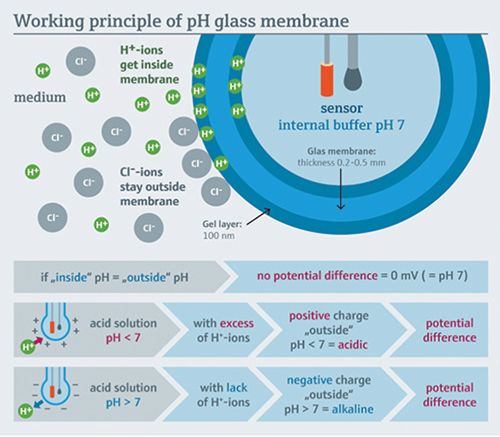
FIGURE 3. Ion exchange takes place at the glass membrane of a pH sensor
FIGURE 3. Ion exchange takes place at the glass membrane of a pH sensor
The electrochemical cell. Each element in the electrochemical circuit contributes to the voltage across the probe. However, only the voltage across the glass membrane represents the pH of the test solution. For this reason, all other voltages in the circuit should be minimized and kept as constant as possible.
The flow of ions through the sensor as it measures pH can have negative consequences over time. If too many ions flow out of the electrolyte solution, then the concentration of the reference cell will drift from its target value and impact the integrity of the results. On the other hand, if too many ions of the test solution flow into the electrolyte solution, this will become contaminated, resulting in erroneous readings.
Factors affecting measurement
While the general design and construction of a pH sensor must meet the overall functional requirements outlined above, there are certain factors that can significantly impact the integrity of results and the life span of a sensor. This is particularly important in plant environments where conditions are more hostile. A real-time online pH sensor is exposed to temperature fluctuations as well as contaminants, both of which contribute to measurement drift and shortening of its expected life. These probes should be calibrated regularly (up to daily) to ensure there is no drift on the readings. However, laboratory pH probes operate in far more stable environments and therefore experience less drift and have a longer life.
The three critical elements that could affect probe accuracy and reliability are the following:
- The liquid junction
- The glass membrane
- The ion trap
The liquid junction. The liquid junction (Figure 4) lies between the reference electrode and the test solution. It normally takes the form of a ceramic plug, but it could also be made from polytetrafluoroethylene (PTFE) or left as an open aperture. The purpose of this junction is twofold. It must allow the flow of ions between the reference electrolyte and the test solution. Without this flow of ions, there is no electrical circuit and there can be no accurate measure of pH. On the other hand, the junction must slow down diffusion to minimize the substance exchange between the reference electrolyte and the test solution. This prevents the reference electrolyte from “bleeding out,” thus changing the voltage of the reference electrode.
One way to maximize the junction performance is to use the high-quality ceramic material. The best ceramics have internal pores, which are consistent in size and distribution. Low-quality ceramics have too much variability in their internal structure. This variability means that each sensor behaves differently, making it challenging to develop consistent sensor performance. It is also possible for the ceramic pores to get plugged. If the blockage is severe, it may eventually prevent the flow of ions completely. This can happen if the pores in the ceramic are too big, allowing suspended particles from the test solution to wedge inside the pores.
Solid particles can also result from chemical reactions between the electrolyte and the test solution. Potassium, chloride and silver ions are all present at the junction from the electrolyte solution. Any of these components could potentially react with chemicals in the test solution, forming insoluble compounds. These may precipitate in the junction, blocking its pores.
The effect of solids formed by chemical reactions can be mitigated by using an ion trap.
The ion trap. An ion trap serves two primary purposes. Firstly, it prevents the silver ions from leaving the reference electrolyte; secondly, it prevents the pollutant ions from the test solution from contaminating the reference electrolyte. In this way, the ion trap inhibits the formation of precipitates at the junction and keeps the ceramic pores open for ion exchange.
The ion trap consists of small beads embedded in the gel and electrolyte behind the junction in the reference half-cell. The ion trap beads have exchange ions attached to them. An ion-exchange mechanism traps ions and prevents them from moving between the reference electrolyte and the junction using the beads.
As silver ions enter the top of the ion trap from the reference electrolyte, they come into contact with the beads. The silver ions replace the exchange ions at the top of the ion trap and the equivalent exchange ions are released from the beads at the bottom of the trap. The exchange ions do not precipitate and will not cause blockages in the ceramic junction.
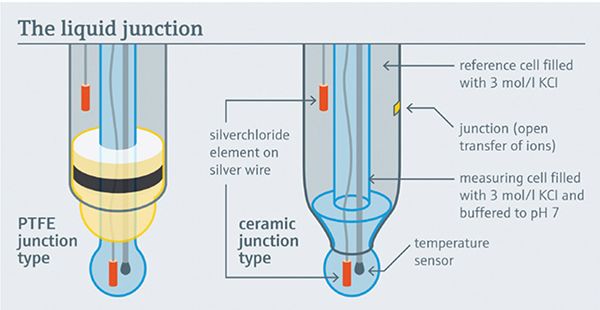
FIGURE 4. The liquid junction must allow the flow of ions between the reference electrolyte and the test solution. The junction must also minimize substance exchange between the reference and test solutions. Two junction designs are shown here
FIGURE 4. The liquid junction must allow the flow of ions between the reference electrolyte and the test solution. The junction must also minimize substance exchange between the reference and test solutions. Two junction designs are shown here
At the same time, pollutant ions are entering the ion trap from below. They also come into contact with the beads and exchange places with the exchange ions. The pollutants are, therefore, prevented from reaching the reference wire and interfering with the measurement.
Without an ion trap, the formation of precipitate in the ceramic junction would severely limit the life of the pH sensor. The ion trap is, therefore, a fundamental element for preserving the integrity of results for a longer time, thus extending the life span of the pH probe. This is particularly important in heavy or polluted chemical applications.
The glass membrane. pH sensors are designed and constructed with the aim of keeping all the voltages in the electrochemical circuit small and unchanging. The only exception for this is the voltage across the glass membrane. This changing voltage represents the pH of the test solution. To achieve this, the membrane must be as sensitive as possible to minor changes in ion activity on either side of the glass.
The glass membrane is 0.2 to 0.5 mm thick. The gel layer on each side of the glass is thinner, at approximately 100-nm thickness. An essential element in the construction of the membrane is the doping of high concentrations of alkali metal oxides. These metal oxide ions allow the ion exchange from the solution into the gel layer, giving rise to the voltage change across the membrane.
Because ion activity changes with temperature, the characteristics of the glass must be suitable for the measuring conditions. Composition of the glass membrane is a highly confidential field of research for pH sensor manufacturers. Different glass membranes should be used for different temperature applications. Glass membranes are also designed for some specific chemical interactions, such as sterilization applications or test solutions containing hydrofluoric acid.
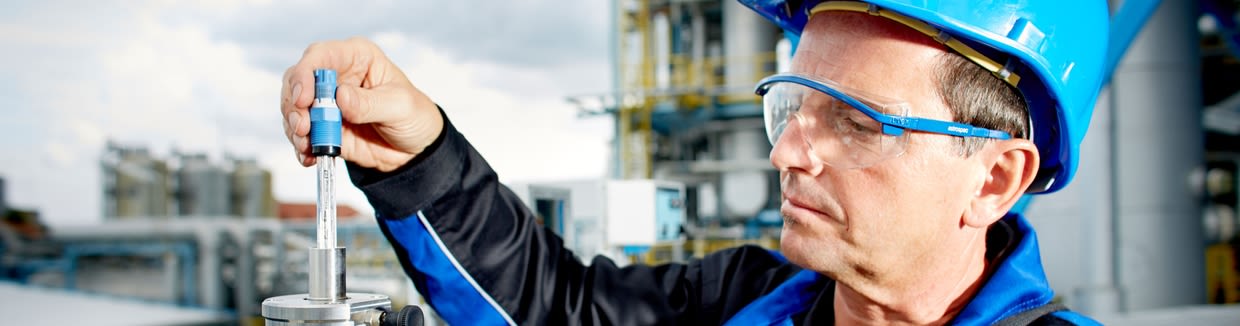
Digital versus analog sensors
Analog systems. Analog pH measurement installations consist of a sensor, a transmitter and a cable connecting the two together. The entire system works together to measure the pH, which is transmitted to a control system using a 4–20-mA signal or digital communication protocols. This means that the sensor is not a stand-alone device, but is dependent on the wiring and the transmitter to form a measurement loop. A significant disadvantage of this approach is that a change to a single component affects the pH measurement. For example, if the wire between the probe and transmitter is changed, the readings will change, and the entire system must be recalibrated.
Digital systems. Digital pH measurement systems contain all the components for measurement on the sensor itself. The cable from the sensor to the transmitter supplies power and transmits information digitally. Therefore, it does not affect the measurement. Changing the cables from the sensor to the transmitter will not affect the pH measurement, which eliminates the need for recalibration. When replacing a digital probe in the field, it can also be immediately commissioned, as long as it has been calibrated in a laboratory setting. Digital sensors are insensitive to moisture in the connections like analog sensors are, because these connections are not part of the measurement loop.
The hazards of field work. The chemical industry is often a hazardous environment, which uses products and materials that can cause serious injuries to operators or maintenance technicians. It is vital to keep personnel out of the field as much as possible to minimize the risk of accidents. Digital pH probes help achieve this because they can be replaced without field calibration. In contrast, analog systems must be recalibrated in the field after any component is changed, which prolongs the time a person must spend in the field working on the equipment. This leads to a higher safety risk and to increased maintenance costs due to the time that it takes to complete the task.
The benefits of information storage. Digital sensors also have the benefit of internal data storage, which captures critical information about the process and the condition of the sensor.
Calibration data can be stored in the head of a digital sensor. This enables the device to be calibrated in the laboratory before field installation. The device will read accurately without the need for field calibration checks. Digital devices store their original reference calibration along with the records of previous calibrations. This allows maintenance technicians to optimize the calibration frequency by monitoring the drift in the readings over time.
Digital sensors also store critical operating information. For example, they record extreme temperature or pH events that could reduce the life span of the sensor or its current accuracy. This information is vital for predictive maintenance and for assessing the health of a sensor. Advanced applications can use this information to develop models and create alerts when a calibration or maintenance intervention is required.
For those instruments used in sterile applications, the digital head can store the history of clean-in-place (CIP) and sterilize-in-place (SIP) cycles. The frequency of these cycles affects calibration optimization, as well as expected life.
All these benefits are only available from digital pH sensors, which store information in the digital head so that it can be accessed by software applications or maintenance technicians for improved maintenance and better accuracy.
Future trends in pH sensors
There have been significant advances in the design and construction of pH sensors since the original glass electrode pH sensor was invented by Beckman. New junction designs using high-quality ceramic or Teflon materials offer much better and durable performance than former designs and materials. Glass membranes have also improved. They are optimized for different applications, with each one having its own advantages and disadvantages. The ion trap is the high point of design innovations for pH sensors and has played a major role in increasing their life span.
Current developments focus on the digitalization and the use of information to improve predictive maintenance and reduce the safety risk for personnel. For example, equipment-health monitoring applications are becoming more sophisticated and more accurate at predicting problems before they affect the quality of results.
In the near future, pH sensors are likely to store even more information about their use and their operating conditions. Availability of this information in cloud-based applications will enable higher-level monitoring and analysis to improve their performance. These systems will enable users to optimize their maintenance intervals, reduce their costs and extend the life span of their sensor.
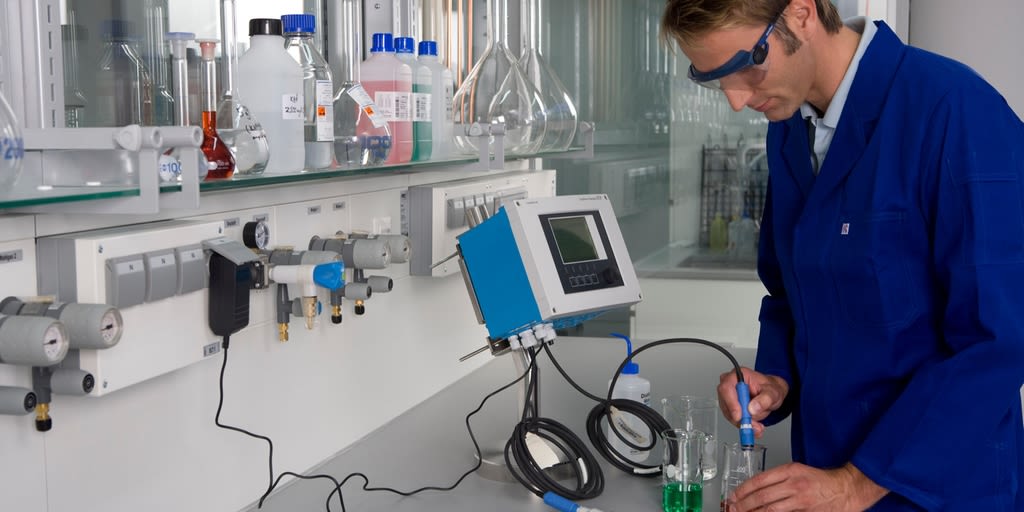
References
1. American Chemical Soc., Development of the Beckman pH Meter, www.acs.org/content/acs/en/education/whatischemistry/landmarks/beckman.html
2. Siwek, Nik, The Importance of pH Measurement, Water Technology, December 15, 2020, www.watertechonline.com/industry/article/14185604/the-importance-of-ph-measurementprint
3. Siwek, Nikodem, Select the Proper pH Sensor, Chem. Processing, October 26, 2021, www.chemicalprocessing.com/articles/2021/select-the-proper-ph-sensor/
Author
Colin Ziegler is product manager for pH and ORP Sensors at Endress+Hauser Liquid Analysis (Endress+Hauser Conducta GmbH+Co. KG, Dieselstrasse 24, 70839 Gerlingen, Germany; Email: [email protected]; Website: www.ehla.endress.com). He started his career at Endress+Hauser as a service engineer, where he was in charge of different areas. After moving into product management, he was first responsible for the global portfolio of conductivity sensors, later moving to pH and ORP, where he now focuses mainly on the chemical, power and energy, oil-and-gas, mining, minerals and water/wastewater industries. He holds a Ph.D. in biochemistry from the Karlsruhe Institute of Technology.