Low-Carbon Hydrogen: Considering Scale
The future of green hydrogen depends on the success of each stage of its ecosystem. Many factors are contributing to the critical infrastructure scaleup necessary to achieve industrial decarbonization
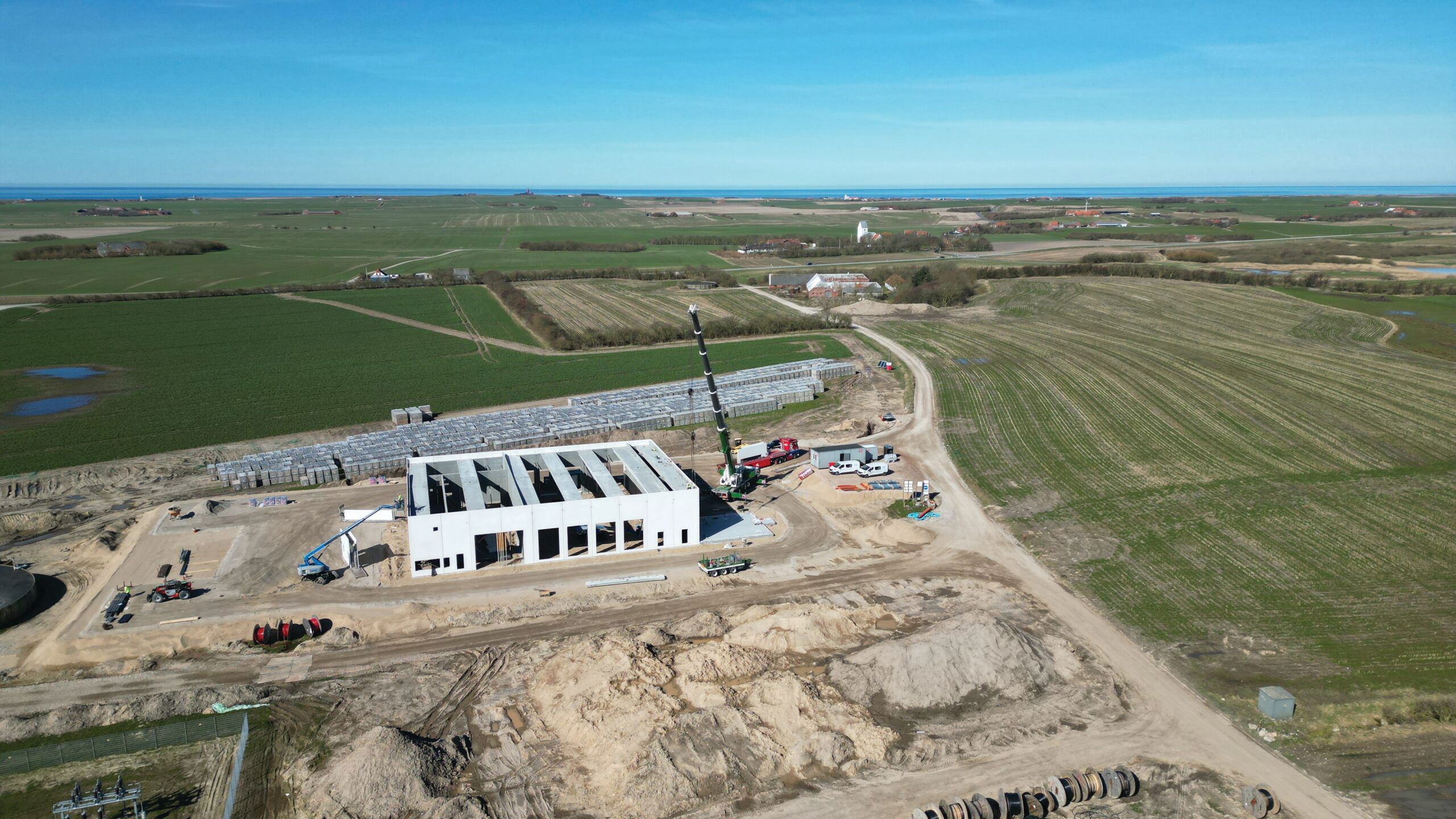
Globally, hydrogen is increasingly being considered as a critical part of industrial decarbonization strategies, both as an alternative fuel and as a method for decarbonizing manufacturing sectors that use hydrogen as a feedstock. Recently, incentives from the Inflation Reduction Act (IRA) have rapidly accelerated activity around low-carbon hydrogen projects in the U.S., aiming to increase the use of hydrogen as an energy source and the adoption of “green” hydrogen over traditional fossil-fuel-based “gray” hydrogen. As part of the IRA, significant funding from the U.S. Dept. of Energy (DOE; Washington D.C.; www.energy.gov) is being earmarked for Regional Clean Hydrogen Hubs — large-scale production and transport networks that will build out the full hydrogen value chain. These hubs include electrolyzers for producing green hydrogen from water, refueling stations for distributing it and fuel cells for converting it into electricity, as well as pipelines, tanks and other logistics infrastructure. Each hub has submitted a formal proposal, and funding selections will be announced later this year. As low-carbon hydrogen production proliferates throughout the U.S. and beyond, there are many critical factors being considered behind the scenes of this massive scaleup, including workforce concerns, hydrogen safety and storage, equipment supply chains and end use.
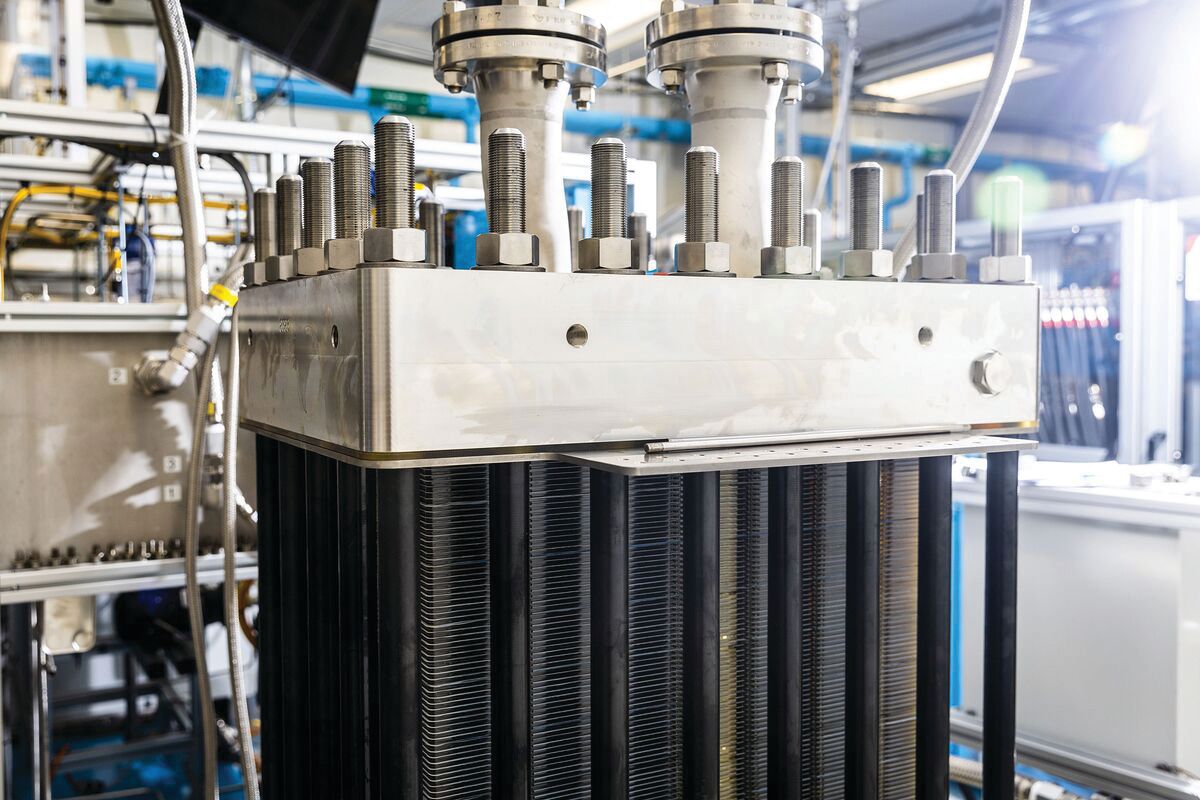
FIGURE 1. The supply chain for green hydrogen starts with the manufacture of electrolyzers and their associated components, including catalyst materials and membranes. 1. Photo credit: Chemours
FIGURE 1. The supply chain for green hydrogen starts with the manufacture of electrolyzers and their associated components, including catalyst materials and membranes. 1. Photo credit: Chemours
Electrolyzer supply chain
With the influx of low-carbon hydrogen projects being announced, the manufacture of electrolyzers and associated components is rapidly scaling up, with focus on economies of scale and automation. Simultaneously, advances in energy efficiency and durability from higher-performing membranes and catalysts are reducing upfront capital costs. “Upscaling electrolyzer production is one of the biggest potential bottlenecks for ramping up the hydrogen market. A substantial production increase is based, in turn, on a massive expansion of renewable energy capacities. Strategic investments along the whole value chain are key to preventing a long-term production restriction,” says Stefanie Kopchick, hydrogen business venture leader at The Chemours Company (Wilmington, Del.; www.chemours.com). Chemours is in a unique position as a manufacturer of electrolyzer components — namely, Nafion ion-exchange membranes — as well as a user of green hydrogen at some of its manufacturing sites. The company recently announced plans to invest $200 million to expand production capacities for ion-exchange materials at its plant in Villers-Saint-Paul, France, and is also partnering with TC Energy to install proton-exchange membrane (PEM) electrolyzers (Figure 1) to supply hydrogen for two Chemours manufacturing sites in West Virginia as part of the Appalachian Regional Clean Hydrogen Hub (ARCH2) proposal. “To further advance the decarbonization of our manufacturing processes at each site, Chemours plans to consume a portion of the produced clean hydrogen as a blended fuel with natural gas to fire existing boiler equipment,” adds Kopchick. To reach the hydrogen production capacities needed for industrial decarbonization, electrolyzer performance must continue to improve alongside manufacturing scale, particularly in terms of energy efficiency and durability of internal components. “We are constantly striving to increase the energy efficiency of our ion-exchange membranes, which have a direct impact on overall electrolyzer efficiency. At the same time, we are working to increase the durability of the membranes. Furthermore, lower costs can be achieved by reducing catalyst loading levels or shifting to alternative catalysts that don’t decrease efficiency or durability. In this area, Chemours is continuing development of ionomer dispersions, which allow precious metal catalysts to be used more efficiently and last longer in these applications,” says Kopchick.
Workforce
The Hydrogen Hubs are bringing together industry, academia and government bodies to take advantage of the unique geographic, workforce and infrastructural benefits of their respective regions. Because the hubs are focused on commercial-ready technologies, rather than testing conceptual or research-focused endeavors, the role universities take is generally focused on honing workforce skills and fostering beneficial relationships with the communities where the projects will actually be executed. “Universities have a very important sort of ‘connective-tissue’ role to help align our manufacturing alliances, our government agencies and other university partners into a cohesive community,” explains Tim Filley, director of the Institute for Resilient Environmental and Energy Systems (IREES) at the University of Oklahoma (Norman; www.ou.edu), a partner in the HALO Hydrogen Hub (www.h2alo.org), a regional coalition between Arkansas, Louisiana and Oklahoma applying for funding from the DOE. “The hub is really about shovel-ready technologies, not R&D or pilot projects, so industries that have existing technologies that are ready to be put into the marketplace and scaled is what we’re seeking. We’re also thinking about the interface between local production and offtake,” he adds.
A key consideration in the economics of a hydrogen hub is the ability to utilize existing infrastructure and natural resources, which obviously varies greatly from region to region. “The ultimate goal is a vibrant hydrogen economy across the value chain with clean production, clean storage and clean use. We are broad in our perspective, in terms of end users, and we are thinking about leveraging the strengths of the three states — you can imagine that these states have enormous strengths in the petrochemicals industry and access to vast natural-gas reserves, but we also have abundant resources that allow us to produce green hydrogen through electrolysis. Those electrons that we’re using to produce hydrogen are going to come from various sources — from methane, as well as wind, solar and potentially nuclear power,” says Filley.
But natural resources and physical infrastructure are not the only factors supporting a hydrogen hub proposal — there are also complex considerations related to workforce, education and environmental and economic impacts to local communities. The hydrogen hubs fall under the major infrastructure and energy projects that are adhering to the Justice40 federal initiative, which aims to decrease the burden on communities that are disproportionately affected by pollution and the impacts of climate change. “With the Justice40 executive order in mind, we’re striving to progress environmental justice goals by thinking about diversity, equity, inclusion and accessibility, to ensure that benefits flow to those communities where we site the facilities,” says Filley. “We’re not just making sure we bring high-paying jobs locally, also we’re looking at past burdens to the societies in those areas — energy burdens, environmental burdens, job burdens and how we can rectify some of that. We’re connecting with social and manufacturing groups to build community-benefits plans, collaboratively,” notes Filley.
Storage
The regional U.S. hydrogen hubs are being designed to take advantage of existing infrastructure, industrial sites, natural resources and geology. Obviously, these factors vary greatly from region to region, making the proposals unique slices of the country’s energy landscape. A major piece of the puzzle is the region’s plan for hydrogen storage.
There are a number of complex challenges in storing hydrogen, and the preferred storage options may vary vastly based on geography, from underground storage to specialized ceramic tanks to liquid carrier molecules. “There are challenges specific to hydrogen just because it’s a much smaller, much more reactive molecule. For storage subsurface, we have to consider its geochemical reactivity, as well as how hydrogen is going to impact the microbial communities underground, and if that impact is going to cause loss of hydrogen inventory,” explains Shadi Salahshoor, senior technical leader of the Hydrogen Technology Center at GTI Energy (Des Plaines, Ill.; www.gti.energy). GTI Energy is leading a number of research projects focused on hydrogen storage, with special focus on evaluating the subsurface storage of hydrogen in aquifers and depleted oil-and-gas reservoirs. “A key angle in subsurface storage is the compatibility of hydrogen with downhole equipment. There are ongoing projects researching hydrogen blending into pipelines that involve a great deal of pipeline and wellhead equipment that must be compatible with hydrogen,” says Salahsoor. Hydrogen’s diffusivity — another result of its small size — is another aspect to consider, as hydrogen can potentially diffuse through underground geologic formations, causing inventory loss
or contamination.
GTI is a partner on the DOE’s H2@Scale project in Texas, which can be thought of as a “proto-hub,” since it is smaller in scale than the proposed regional hubs, but encompasses the entire hydrogen value chain in one project. “We have hydrogen production, storage and end-use all on site. Basically, we have an electrolyzer and methane reforming onsite producing hydrogen, which is utilized by a fuel cell,” says Salahshoor. She notes that for this project, aboveground storage tanks are being used, but that for a larger-scale project, underground storage would be preferable due to the equipment footprint required for the necessary storage volumes. “If you want to store tons and tons of hydrogen, you might need a massive number of tanks, which can be really tricky to handle with all the safety and environmental aspects,” she adds.
For the large-scale hydrogen projects being proposed, hydrogen producers must consider a somewhat different mindset than on smaller projects. “For decarbonizing industry, we need to start thinking about these hydrogen-storage needs on the same scale as natural gas. There aren’t many commercial, or even pilot-scale projects now, but in the next 5–10 years, we are going to see several pilots showing the feasibility of different storage methods,”
emphasizes Salahshoor.
Currently, one of the most economically and technically feasible methods for long-duration, large-scale hydrogen storage is in underground geologic formations, explains Claire Behar, chief commercial officer of Hy Stor Energy LP (Jackson, Miss.; www.hystorenergy.com). Hy Stor is leading the Mississippi Clean Hydrogen Hub, reportedly the largest of the proposed hubs, which aims to utilize the state’s significant volume of salt caverns for underground hydrogen storage. “The hub will bring together the production, storage and delivery of carbon-free hydrogen, but to really reach scale in a resilient fashion, we must focus on the geologic storage aspect. Mississippi really has geology and geography that is unparalleled globally. Not many locations have so much unutilized salt geology,”
says Behar.
The hub will couple the salt-cavern storage with electrolytic hydrogen production, using solely off-grid renewable-energy sources, including solar, onshore wind and geothermal power. For hydrogen delivery, there will be a dedicated hydrogen pipeline and planned truck transport, as well as transport access from the Mississippi River and nearby Gulf Coast ports. Furthermore, notes Behar, port access will enable the export of green hydrogen to international markets. “We’re looking at decarbonizing the current industries in our region and some maritime transport, while also attracting new green manufacturing firms,” she adds.
A major incentive for new parties to join the hub is support to demonstrate new technologies for electrolyzers and other critical components in the hydrogen supply chain. “We’re creating a circular ecosystem where startups can come and prove their renewable technologies. They can test their run hours and durations outside the laboratory and take advantage of being connected to the salt cavern storage and a flexible, non-intermittent supply of hydrogen. It will be very exciting bringing these new renewable technologies to life.”
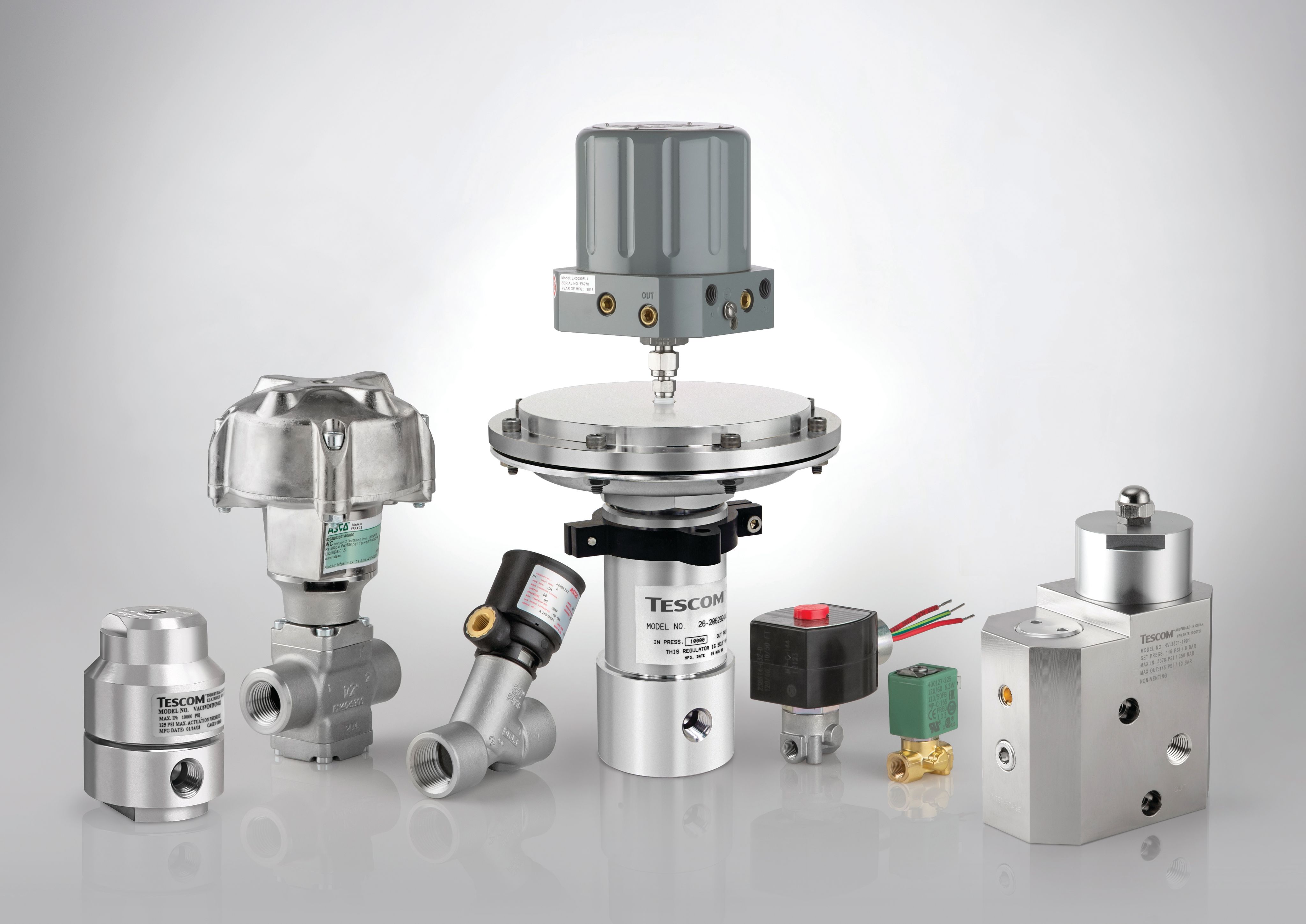
FIGURE 2. In hydrogen fuel cells, several components work together to control hydrogen and ensure that fuel is dispensed correctly, including valves and regulators. Photo credit: Emerson
FIGURE 2. In hydrogen fuel cells, several components work together to control hydrogen and ensure that fuel is dispensed correctly, including valves and regulators. Photo credit: Emerson
Safe hydrogen handling
No matter how hydrogen is produced, it must be handled as safely as possible. It can be explosive when not handled properly, especially at the high pressures required for many transport and end-use options. “As it moves throughout the value chain, hydrogen is subject to pressures of up to 15,000 psi, and, like many fuels, can be explosive when not handled properly. To achieve a landscape that can effectively and safely meet demand, it is critical that companies identify technologies that can reliably and efficiently control hydrogen fuel, from production through end use. This requires high-pressure solutions across the hydrogen ecosystem,” says Akilah Doyle, global product marketing manager at Emerson (St. Louis, Mo.; www.emerson.com). While the components for hydrogen storage and transportation have been well-demonstrated, large-scale electrolyzers and fuel cells require some additional safety and control considerations. “For an electrolyzer to work effectively and safely, the flow of water, hydrogen and oxygen, must be precisely controlled. Reliable valves, backpressure regulators and an intelligent programmable logic controller (PLC) can provide a high level of media control,” explains Doyle. There are essentially four control layers in an electrolyzer that work in tandem to provide the control needed to ensure safe and efficient operation: the valves controlling media flow (including backpressure regulators and pneumatic shutoff valves); the actuation technology (including valve islands and solenoid pilot valves); the PLC; and the supervisory control and data acquisition (SCADA) system. Doyle notes that some valves in the system will require
IP66 protection.
For fuel cells, the requirements are similar, but because hydrogen is the feed rather than the product, high-pressure storage is crucial as it helps to maximize system fuel usage. “The hydrogen storage tanks cannot be run to empty due to pressure constraints, so enabling efficient fuel delivery to the fuel-cell stack with minimal losses is critical. The system must be able to operate consistently across a range of operating modes — acceleration, deceleration, stopping and idling, which all require varying hydrogen flow demands. This stable system operation is aided through a design that employs positive, high-pressure fuel shutoff and is achieved through use of a reliable hydrogen regulator,” says Paul Kondratyev, global product marketing manager at Emerson. Such regulators minimize the risk of leaks and can extend the lifecycle of fuel cells by ensuring they have an even amount of hydrogen dispersed across them while in use (Figure 2).
Green hydrogen in practice
Although there is much discussion about the ballooning production capacities of green hydrogen required for numerous upcoming decarbonization projects, there isn’t as much discussion about the current state of operating green-hydrogen plants. French company Lhyfe (Paris; www.lhyfe.com), a “pure player” in the production and distribution of green and renewable hydrogen, started up a production facility in Bouin, Vendee, France in September 2021 that produces up to 1,000 kg/d of green hydrogen (Figure 3). “A unique aspect of this plant is that it sources seawater, so we don’t take any water from the utility grid. We treat the seawater so that it is comparable to demineralized water for electrolyzer use,” explains François Hoche, industry market manager at Lhyfe. Furthermore, he adds, the plant sources its renewable power directly from a nearby wind park, so it is essentially “behind the meter,” meaning that it does not draw from the local power grid. The major hydrogen users for the site are in the mobility and logistics sectors. “One of the main customers of the facility is a logistics and distribution center operated by grocery chain Lidl. At this center, they have converted more than 120 forklifts to run on green hydrogen,” says Hoche. At Lhyfe’s site, produced hydrogen is compressed and loaded onto tube trailers for transport to users. “In order to transport as much hydrogen as possible, we compress the hydrogen and we have different sizes of containers that are used to distribute the hydrogen to the final customers. In what we call the ‘small industry’ market, users may consume only one or two containers per week, so we switch containers with each delivery, bringing a full one to site and taking an empty one back to the factory,” he adds.
In addition to two under-construction plants in France, Lhyfe has also announced several other projects throughout Europe, including SeaLhyfe, located in the Atlantic Ocean off the coast of northwestern France, which is said to be the world’s first offshore hydrogen-production pilot project (Figure 4). “When we talk about renewable hydrogen, it’s important to realize that the dependence on renewable energy sources makes it crucial to look for the largest possible intensity of renewable power, but many sources have the inconvenience of being intermittent. So we’re looking at offshore production to maximize energy intensity,” says Hoche. In June, SeaLhyfe began production of offshore green hydrogen using a 1-MW electrolyzer capable of producing up to 400 kg/d of hydrogen. From September 2022 to May 2023, the SeaLhyfe module was moored in the Port of Saint-Nazaire. During this time, Lhyfe conducted a series of startup and validation tests to optimize system performance. The company also developed a software platform for remote management of the unit. Now, the SeaLhyfe unit has been towed 20 km offshore and connected to the site’s subsea hub using an umbilical cable designed specifically for use in hydrogen applications. Following the success of SeaLhyfe, the company, as part of the HOPE consortium, has received a €20-million grant to commercialize a much larger 10-MW offshore green-hydrogen unit, capable of around 4 m.t./d of production.
Ammonia production is one of the most promising avenues for industrial decarbonization using green hydrogen. Not only is ammonia a much-needed commodity product for manufacture of fertilizer and other products, it also has great promise as a heavy-duty transport fuel and energy carrier for hydrogen itself. A recently announced project in Denmark is coupling electrolysis of water into green hydrogen with the production of ammonia, all powered by renewable energy, in what is being called the world’s first dynamic, green “power-to-ammonia” plant. “We’ve been converting hydrogen into ammonia for decades, so we know how to handle it, and we know how to store it in a safe manner,” says Jeppe Bentzen, business development director at ABB Energy Industries in Denmark (ABB; Zurich, Switzerland; www.abb.com) on the benefits of green ammonia. ABB is collaborating with project partners Skovgaard Energy A/S (Lemvig, Denmark, www.skovgaard.dk), Topsoe A/S (Lyngby, Denmark; www.topsoe.com) and Vestas (Aarhus, Denmark; www.vestas.com) on the new plant, called Renewable Dynamic Distributed Ammonia Plant (REDDAP), which aims to begin production in 2024 with an anticipated production capacity of 5,000 metric tons per year (m.t./yr) of green ammonia for fertilizer and marine fuels. Construction on the site is currently underway (Figure 5).
A notable benefit of dynamic power-to-X plants is that they make their product when conditions are positive — the sun is shining and the wind is blowing — and they can ramp down production when the energy source is not present, but this type of operation poses some specific challenges. “The groundbreaking part of this project is that it’s the first power-to-ammonia project that is running in fully dynamic mode, meaning that it is directly coupled to its own renewable energy power generation. Since the plant is not pulling energy out from the grid, it will be pushing the limits of the electrolyzers’ operating envelope. This also means that on a technology perspective, we will need to install and deliver a very solid electrical backbone for the plant. This is also a challenge where we want to push the limits of the technology,” adds Bentzen. Currently, ABB is working on simulations to evaluate electrolyzer and electrical-system resilience, detailing design and integrated control systems, under such dynamic conditions. The planned site for the project has access to 12 MW of existing wind-turbine power, and there are also 50 MW of newly constructed solar panels nearby. According to Skovgaard Energy, this is the first of several planned power-to-ammonia plants.
Mary Page Bailey
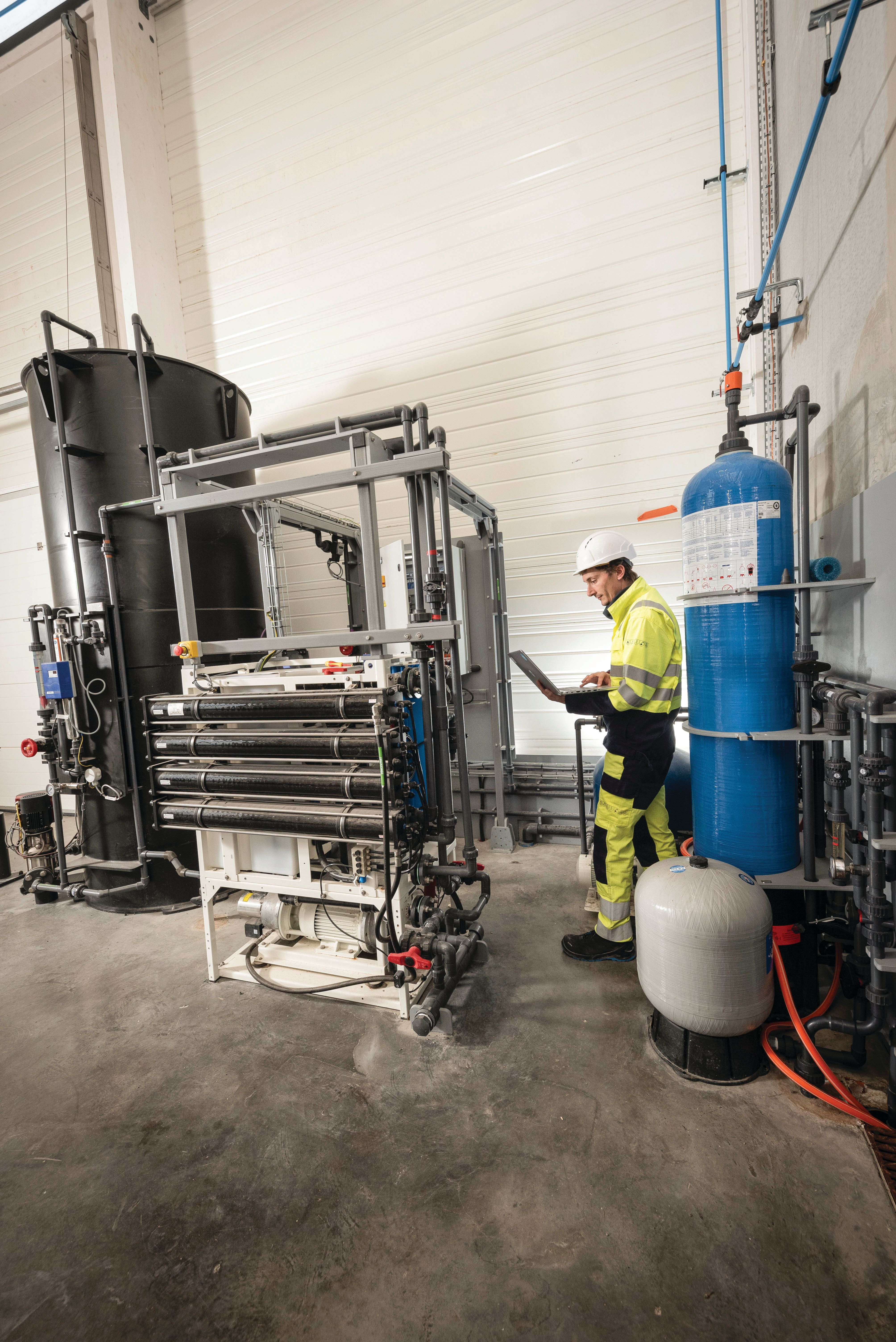
FIGURE 3. Lhyfe’s plant in Bouin produces up to 1,000 kg/d of green hydrogen via electrolysis. Photo credit: Lhyfe
FIGURE 3. Lhyfe’s plant in Bouin produces up to 1,000 kg/d of green hydrogen via electrolysis. Photo credit: Lhyfe
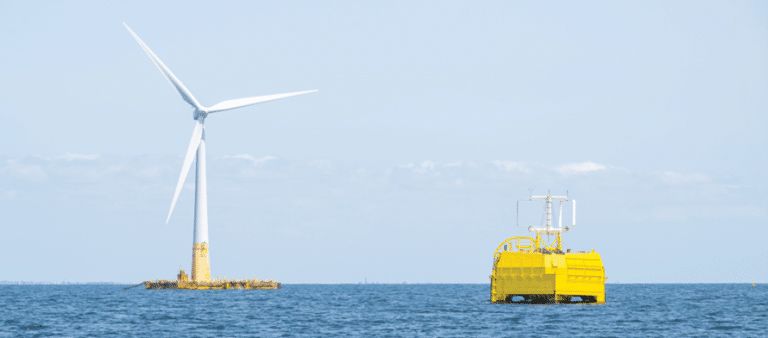
FIGURE 4. The SeaLhyfe project is said to be the world’s first offshore hydrogen-production pilot to begin operation. Photo credit: Lhyfe
FIGURE 4. The SeaLhyfe project is said to be the world’s first offshore hydrogen-production pilot to begin operation. Photo credit: Lhyfe
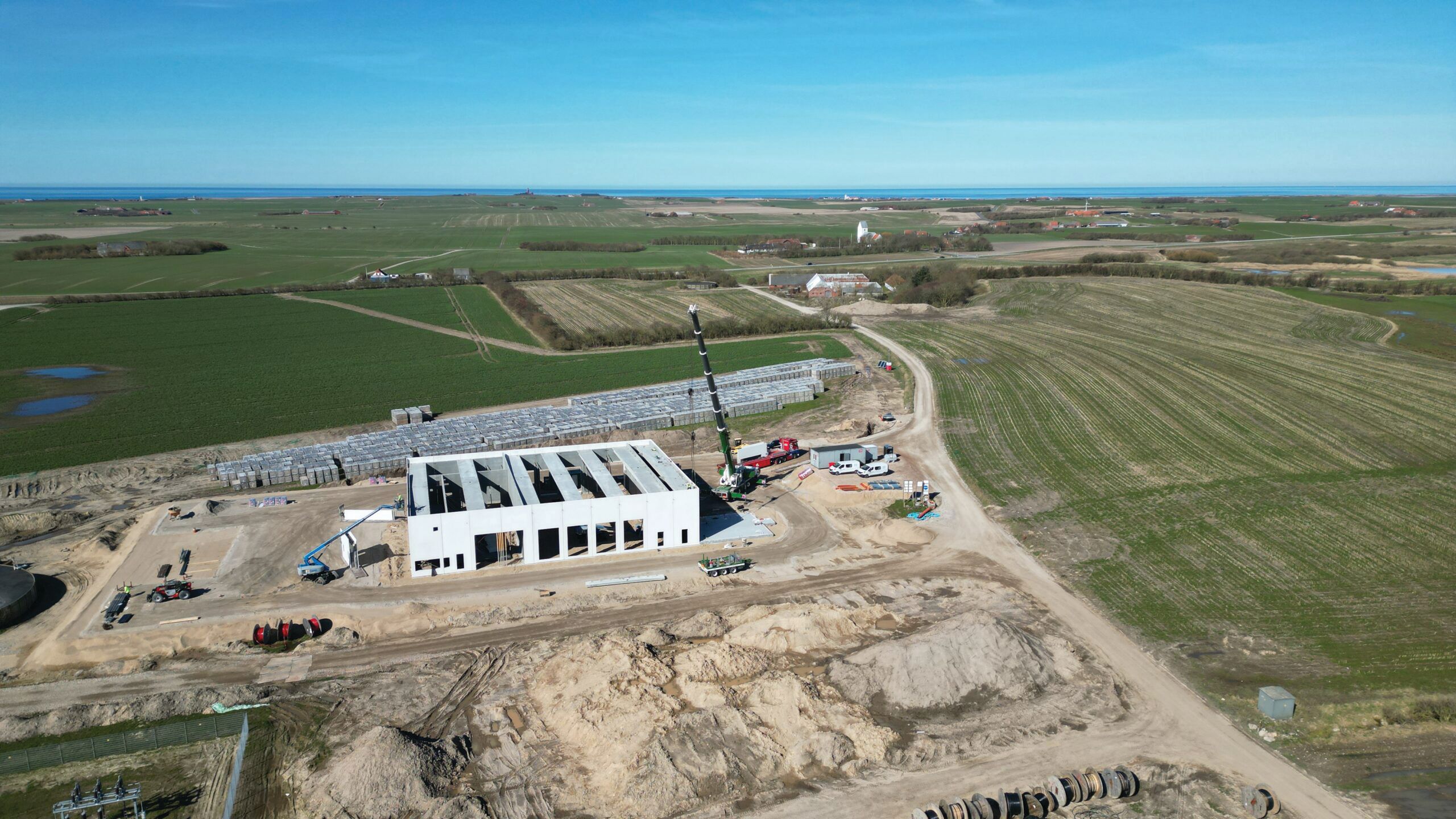
FIGURE 5. Construction has begun on the world’s first dynamic power-to-ammonia plant, which will use electrolysis-based hydrogen as a feedstock. Photo credit: Skovgaard Energy
FIGURE 5. Construction has begun on the world’s first dynamic power-to-ammonia plant, which will use electrolysis-based hydrogen as a feedstock. Photo credit: Skovgaard Energy