Calibration-free, modular and automated gas analyzers offer benefits to the chemical process industries
While there are countless types of gas analysis instruments available, users of every type are asking for technologies that require less of their time. Processors are demanding instruments that require minimal calibration and maintenance, as well as units that are modular and capable of self diagnostics and other automated functions to save labor and plant resources. Fortunately, providers of analytical devices are meeting these needs by changing the way gas measurement is addressed in the chemical process industries (CPI).
Reduced maintenance and calibration
“When we first launched products into the gas-analysis space, we began by speaking to our processing customers and found that running and maintaining gas analysis instruments, in an effort to get proper performance and fulfill safety requirements, was absorbing a lot of resources in chemical and petrochemical plants,” says Jean-Nicolas Adami, manager of business development for gas analytics, Mettler-Toledo AG, Process Analytics (Urdorf, Switzerland; www.mt.com). “End users were spending a lot of time on maintenance and preemptive tasks, such as calibration of instruments.”
In addition, Adami says, many processors were taking extractive measurements, meaning a sample of gas is taken from the process, conditioned and finally analyzed. “This is often done to protect the instruments from dust, gas, corrosion, condensation and other harsh conditions,” he explains. “However, there’s a lot of time spent maintaining such a process and system.”
Jesse Underwood, product manager for TDLS analyzers with Yokogawa Corp. of America (Sugar Land, Tex.; www.yokogawa.com/us), agrees. “Any time you can eliminate sample extraction, sample transport and sample systems, you reduce time spent on analysis and eliminate failure points in the overall analysis system,” he says.
For this reason, both Mettler-Toldeo and Yokogawa provide in-situ tunable diode laser (TDL) spectrometers, in addition to extractive TDL systems, as an alternative to traditional instruments for single-gas measurement in the CPI.
TDL analysis technology offers “significant” benefits to end users, suggests Adami. Most notably, “they [TDL spectrometers] don’t suffer from instrument drift, which is common for just about every type of technology,” he says. “Using a tunable diode laser provides the ability to lock onto an emission frequency so there’s no chance for drift. In addition, the high selectivity of the TDL instrument means there’s no reason what-so-ever to perform calibration if installed properly in stable process conditions,” explains Adami. (Although instruments must still be verified in accordance with applicable regulations.)
And, when used to replace extractive sampling systems, the reduction in hands-on maintenance time is even greater, says Underwood. “Typical extraction systems require a minimum of monthly preventive maintenance, while in-situ systems require maintenance on demand, meaning there is no preventive maintenance for tasks such as changing filters and traps in a sampling system,” says Underwood.
Another perk of this technology is that because in-situ analysis is made directly inside the process pipe, it is more accurate than extractive sampling. “Think of all the changes that can happen when the gas goes through the sampling system,” says Adami. “For example, you have to extract moisture from the gas, which may change the concentration of the gas, which, in turn, means processors can’t be 100% sure that the measured value is representative of what’s really going on inside the process.”
In addition, Underwood says TDL analysis technology is safer in many potentially explosive applications. “Most analytical techniques require that the sensor be exposed to the process, which can be a source of potential hazard once those are heated during the process. But, because it employs a non-contacting sensor, a TDL-based measurement device does not provide an ignition source,” he says.
To bring these benefits to processors, Yokogawa offers the In-Situ Tunable Diode Laser Spectroscopy (TDLS200) with TruePeak technology (Figure 1), which is a technique that allows measurements to be taken with direct absorption, making the device immune to background gas interference, says Underwood. It was designed to make fast, accurate measurements on near-infrared (NIR) absorbing gases in harsh process environments, where conditions may include high temperature or pressure and corrosive, aggressive and high-particulate-content materials. It is suitable for applications such as combustion control; monitoring of CO, CH4 and moisture to enable burner flame-out; measurement of O2 on flare lines, alkylation units and gas plants; and the monitoring of CO and O2 on fluid catalytic cracking units for safety and catalyst regeneration.
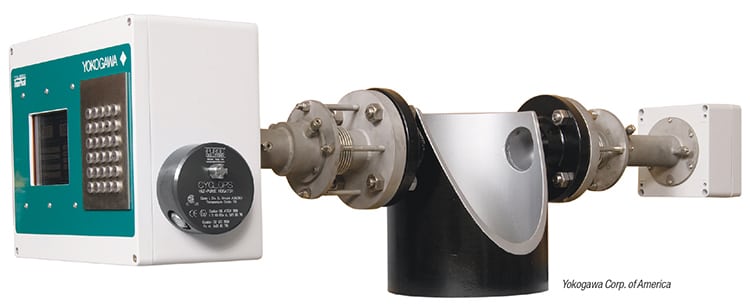
FIGURE 1. The TDLS200 with TruePeak was designed to make fast, accurate measurements on near-infrared absorbing gases in harsh process environments
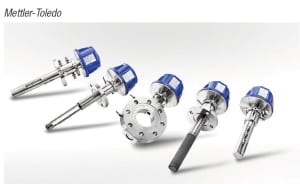
FIGURE 2. The GPro 500 TDL series offers interference-free, drift-free TDL technology along with a folded optical path principle, which simplifies alignment
Mettler-Toledo brings to the table its GPro 500 TDL series (Figure 2), which offers interference-free, drift-free TDL technology. What makes Mettler Toledo’s TDL instruments different is the folded optical path principle. “One drawback of many TDL analyzers on the market that employ a separate laser source and a separate detector is the alignment,” he explains. The laser is a very focused stream, but in some across-the-stack installations, it is possible to lose alignment. For example, if the pipe is very large in diameter, it is subject to vibrations, or one side has more thermal expansion than the other, he says. To solve this problem, we developed a probe design with a folded optical path. This means the laser source and detector are placed in one head that contains all the electronics and is mounted on one side of the pipe or vessel and a probe goes inside the process gas stream containing the reflecting element in the tip. We fold the beam over and back to the analyzer so it’s similar to having a mirror in the process that reflects back into the detector. Simply put, it provides the effect of a solid object that doesn’t require alignment.”
Users of devices that measure moisture in Cl2 are also looking for reduced maintenance requirements associated with calibration and the harsh environment, says Rob Leiter, technical sales representative with MEECO, Inc. (Warrington, Pa.; www.meeco.com). “The real challenge in this application comes from the environment that can corrode almost any metal, including stainless steel,” he says. His company offers the NastyBoy online analyzer for measuring moisture in Cl2 (Figure 3), which provides durability through the use of materials that resist Cl2 gas and the moisture in Cl2 gas, and via a design that isolates the electronics from the flow system. Combined, these features help reduce the total cost of ownership and result in less maintenance.
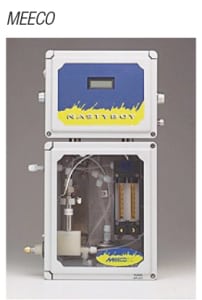
FIGURE 3. The NastyBoy online analyzer for measuring moisture in Cl2 uses materials that resist Cl2 gas and a design that isolates the electronics from the flow system
Specifically, the analyzer technology is based on Faraday’s law of electrolysis, so the cell absorbs and electrolyzes moisture at fractional parts-per-million or other units of measure. All of the sample moisture (100%) is absorbed by a phosphorus pentoxide film, which covers two spirally wound electrodes that are embedded in a hollow glass tube. When the sample gas enters the cell at a known flowrate, the film absorbs all the water molecules present. By applying an electrical potential (voltage) to the electrodes, each absorbed water molecule is electrolyzed, generating a finite current. This current is precise and proportional to the amount of absorbed water. It is, therefore, an exact, direct measurement of the water vapor present in the sample gas.
An added bonus of this technology, according to Leiter, is that the electrolytic cells used do not require calibration in this application, which greatly reduces labor time and costs associated with calibration.
Modular systems
“In the chemical industry there are many combustible gases that occur as byproducts of production processes,” says Torsten Haug, managing director of Union Instruments GmbH (Karlsruhe, Germany; www.union-instruments.com). “The traditional way to deal with this is flaring the gas with a flare stack. The future will likely see us using these gases for energy production in combustion processes. Therefore, it is important to know the gas properties which are influencing the combustion processes.”
For this reason, he says, the market needs a variety of instruments that offer high reliability and easy maintenance, such as automatic calibration and validation functions. Instruments such as BTU analyzers or online measurement of the Wobbe index, heating value, air demand and gas density for all fuel gases and flare gases, will be needed, as well as a variety of sensors with different measuring ranges. Non-dispersive infrared (NDIR) sensors, electrochemical sensors, paramagnetic sensors and acoustic cells will all be needed, and sometimes several may be needed for a single application, he says.
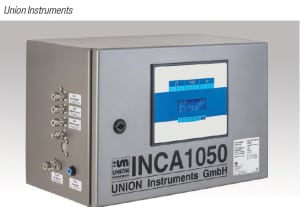
FIGURE 4. The INCA is a modular device platform for multi-component gas analysis with a particular focus in the biogas and natural-gas industries
In response, his company offers INCA (Figure 4), which is a modular device platform for multi-component gas analysis with a particular focus in the biogas and natural gas industries. It is similar to modular construction systems, with blocks for active gas sampling and gas processing, as well as sensors, controllers, data processing and communication combined to form reliable analysis systems.
“The standardized modules enable a variety of customized solutions for specific analysis tasks and combine optimal analysis results for less cost,” Haug says. “The user benefits from the convenience of the modular system, in which individual components can be replaced directly in the field. When equipped accordingly, INCA enables sequential switchover of the measuring technology to different sample gas streams from up to ten measuring points, for example such as sampling from multiple fermenters in biogas plants.”
Automation
Analyzers that are smaller and smarter are becoming increasingly sought after, as well, says Hank Braly, vice president of sales and marketing with Baseline, a MOCON company (Lyons, Colo.; www.baseline.com). “Processors want an instrument that can take care of itself via automated calibration against known standards, diagnostics and the ability to connect remotely over the Internet so that we can remotely diagnose, service and make adjustments to instruments located in the field,” he says.
At the same time, he adds, reducing the size of the devices is also a goal. “A lot of these instruments are being incorporated into systems with other components, so we are reducing the size of our analyzers. Both the smaller size and automated functions are being made possible due to the increase in processing capabilities of microprocessors that allow us to provide more continuous diagnostics and more sophisticated ways of handling the data.”
In addition to offering automatic and remote calibration, Baseline’s Series 9100 gas chromatograph for single- and multi-gas monitoring (Figure 5), contains integrated software, eliminating the need for an additional computer. Data collection is in universal text format with user-definable data export utilities for reports and chromatograms.
Similarly, the company’s fully automated Series 9000 Hydrocarbon Analyzer (Figure 6) also offers an automatic calibration feature that enhances the long-term analytical stability of the instrument. Automatic flame-ionization detector (FID) ignition, automatic shutoff sample, fuel and combustion air, remote operation via RS-232 and Ethernet, and software that allows for remote monitoring and control are also featured.
Whether your gas analysis need is for reduced maintenance, modular instrumentation or automated systems, or any combination of these characteristics, it is likely that analyzer manufacturers are developing a measurement device that will meet your requirements to reduce the labor and other plant resources that were once associated with taking gas measurements. ■
Joy LePree