In today’s environmentally conscious world, industrial energy management is increasingly recognized as an essential business practice and economic necessity, rather than an on-again, off-again activity driven by energy prices and geopolitical crises.
In this article, we examine the key elements of excellence in energy efficiency, and explore ways of pursuing energy excellence. Four main types of opportunities provide the savings: operational improvements, effective maintenance, engineered improvements and new technologies. We include experience from several companies in the chemical process industries (CPI) that have made great strides in raising efficiency and reducing energy consumption.
To support and maintain an effective energy-management system, it is important for CPI companies to establish a corporate culture that expects energy efficiency, motivates its employees, provides the organizational structure to facilitate savings, and develops the tools to achieve efficiency. Energy efficiency only improves when both processes and human behaviors change. Here, the “processes” include both physical plant and business processes.
Management versus efficiency
In some companies, the concept of “energy management” focuses primarily on recording and reporting energy use, and purchasing or selling energy streams. While these are important functions, they do nothing to improve the efficiency of energy utilization. Here, we use a broader definition of energy management, which includes actively working to reduce energy consumption by using energy more effectively.
“Energy efficiency” is another term with multiple meanings. The goal should not be the minimum use of energy, but the optimum use of energy — that is, the minimum use of energy, subject to a range of goals and constraints that include production requirements, environmental considerations and safety, among others.
Program components
No “silver bullet” for improving energy efficiency exists — there is no single method or approach that ensures optimal energy use in all situations. Those with a background in engineering tend to think in terms of technological options to improve energy performance — better heat recovery, more selective catalysts, higher-efficiency motors, improved process design and so on. Indeed, changing these components of physical plants can be a very powerful way of lowering energy usage. However, real-world energy efficiency is also a function of the behavior of both individuals and organizations. It follows that management and motivation are also critical factors in energy efficiency, and those factors require dramatically different types of expertise than purely technological solutions.
Comprehensive energy-management programs typically include corporate energy policies, reporting systems, benchmarking, corporate and local goals, various types of energy audits and assessments, and integration of energy-efficiency elements into engineering procedures and purchasing protocols.
Taken together, an effective energy-management program provides the motivation for the behavioral, technical and business changes necessary to improve energy efficiency.
Many resources are available to build an effective energy-management program. In the U.S., both the Dept. of Energy (www.energy.gov) [1] and the Environmental Protection Agency (www.epa.gov) [2] have been active in developing and promoting energy efficiency practices. Meanwhile, in 2011, the International Organization for Standardization (www.iso.org) launched ISO 50001:2011 to “support… organizations in all sectors to use energy more efficiently, through the development of an energy management system (EnMS)” [3].
Energy and the CPI
The CPI is one of the largest users of energy in the world, especially within its many continuous, large-scale, petroleum-refining and petrochemical-production facilities. However, the CPI also includes many smaller facilities, typically specialty plants, many of which run batch operations. There is therefore a great deal of diversity within the industry, and energy management programs must be tailored to the specific needs of individual companies and operating sites.
World-scale petroleum refineries and petrochemicals facilities have annual energy bills in the hundreds of millions or even billions of dollars, and energy used in the process is a major component of variable cost. In contrast, labor and safety and human-comfort systems, such as lighting and space heating, tend to be more dominant in many of the smaller, more specialized facilities that spend much less on energy.
Energy management is also very different for batch processes than for continuous ones. In particular, where many batch operators can apply “downtime shutdown strategies” to eliminate unneeded energy use for much of the time and thus gain “free” energy savings, this approach is not generally applicable in continuous processing.
The process sector does share some key systems and equipment. Steam systems are virtually ubiquitous, as are electric motors, heat exchangers, pumps and compressors. However, beyond these common elements there is great diversity, from distillation columns, catalytic reactors and centrifuges to kilns, crystallizers and belt dryers. Each system and each type of equipment has its own issues that must be considered within a comprehensive energy-management program.
Energy efficiency opportunities
Opportunities to improve plant performance, and thus enhance energy efficiency across the CPI, fall into four main categories: operational improvements, effective maintenance, engineered improvements, and new technologies. In each area, robust energy-management programs can support the behavioral and process changes needed to capture and maintain savings and efficiency improvements.
Operational improvements. Many operational improvements can be captured at low or no cost. Before committing to projects that require capital expenditure, it is prudent to ensure that existing equipment is being used to its full advantage — to pick up the “low-hanging fruit.” This idea is illustrated in the following example: A project was planned to expand a process unit in a chemical plant. The expansion required a significant increase in cooling-water flow, and as the existing cooling-water pumps were already fully loaded, a new pump was included in the project scope. However, during a project review, the need for the new cooling-water pump was challenged, so the cooling-water system was surveyed.
Over the years, the cooling-water system had been expanded and modified several times to accommodate changes that had taken place at the site. The changes included two additional pumps and several branches in the piping, so the cooling-water system had become quite complex over time.
During the survey, it was found that cooling water was still flowing through a section of the plant that had been abandoned several years before. When the isolation valves for this section of piping were closed, the cooling-water circulation rate dropped significantly. This freed up sufficient capacity to eliminate the need for the new pump in the expansion project, which reduced the project cost by $500,000 and saved $200,000/yr in electricity costs to run the additional pump.
Operating practices tend to become ingrained over time. In the example above, no one questioned the position of the isolation valves in the unneeded cooling water circuit. More generally, operators may religiously follow procedures that were developed when the plant first started up, even though the requirements of the plant have changed over time. For example, these changes could be due to new feedstocks, different product slates, changes in throughput or a host of other factors.
Another way that operating practices can become skewed is by extending short-term responses to specific problems. For example, a cooler may be bypassed in cold weather, or a preheat exchanger may be taken out of service during a plant upset. These modified configurations can remain in place and become the new normal, and they can remain that way for years.
The immediate response when we become aware that operating conditions are suboptimal is to adjust the process (for instance, shutting the isolation valves in the cooling-water example). However, this is only a short-term fix. The next operating shift will very likely reverse the change and restore the status quo. Furthermore, plant conditions are constantly changing — the right solution today may not be the right one tomorrow or next month. We need more than just a one-time change to ensure that we get the most from our existing facilities. Additional energy-management steps might include the following:
- Modify operating-procedure documentation
- Carry out additional operator training
- Add control valves
- Implement realtime optimization systems
- Implement performance monitoring systems and key performance indicators (KPIs)
One area that often yields significant opportunities for operational improvements is the steam system — especially more complex steam systems that include steam turbines. These systems are subject to significant demand changes, and they often get out of balance. This can lead to steam venting or excessive use of steam letdowns, or both. Close monitoring, together with steam models and realtime optimization, can yield substantial improvements in energy efficiency and savings in net energy costs.
Effective maintenance. Another part of getting the most out of existing facilities is to ensure that the equipment is properly maintained. Our primary focus here is maintenance of the equipment and systems that have the largest impact on energy use — for example, heat exchangers, especially those in preheat services.
Heat-exchanger cleaning programs are an important part of many energy-management programs. This area has become quite sophisticated, with both improved cleaning techniques (Figure 1) and better tools for assessing appropriate cleaning intervals for the heat exchangers. However, the best cleaning methods and the most elegant optimization of cleaning intervals are of little use when communication fails [4].
FIGURE 1. Heat-exchanger cleaning programs have become an important part of energy-management systems. Shown here is hydroblasting equipment for cleaning shell-and-tube heat exchangers
Courtesy of NLB
During the course of a crude-unit preheat-train study in a petroleum refinery, one of the heat exchangers was found to be out of service. The records showed that this particular heat exchanger had been idle for more than three months. Further investigation revealed that the heat exchanger had been cleaned, and the work had been completed within a couple of weeks. The maintenance supervisor notified the shift supervisor that the cleaning was complete, but shift personnel were busy with other activities, and the heat exchanger could not be brought back into service before the shift ended. Unfortunately, the shift supervisor failed to advise the next shift about the situation. There was no follow-up, and the cleaned exchanger remained out of service for two and a half months.
When the unit manager was informed, the heat exchanger was brought back into service in just a few hours. The energy loss during the period that the heat exchanger had been left idle after the cleaning was worth over $100,000.
In this case, the key problem was a breakdown in communication. Better systems were needed for tracking the status of maintenance jobs on the unit. A simple electronic reminder system, for example, could have alerted the operators to the need to bring the heat exchanger back online.
In addition to heat exchangers, there are several other key systems and types of equipment that need careful attention and preventive maintenance to maintain energy-efficient operations. These include furnaces and boilers, steam traps and insulation, as well as compressors, pumps and turbines.
Engineered improvements. Additions and upgrades to plant facilities can lead to significant improvements in energy efficiency. Invariably, these upgrades require significant input from engineering personnel to identify, evaluate and design the projects. Opportunities can cover a wide range in scale and type, such as the following:
- Simple piping changes
- Localized insulation projects (Figure 2)
- Replacements of electric driver systems (such as installing variable-frequency electric drives)
- Adding heat exchangers, steam turbines, distillation columns or other major equipment items
- New control schemes
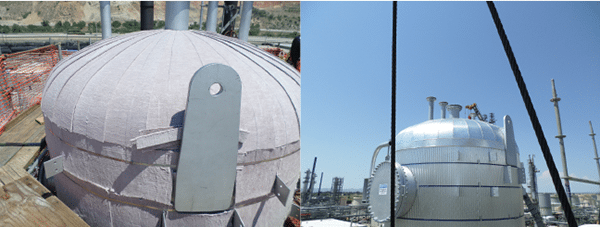
FIGURE 2. Localized insulation projects, such as the one shown here on the top head of a distillation column, are examples of engineered upgrades that can lead to improvements in energy efficiency
Courtesy of Aspen Aerogels
A robust energy-management system tracks opportunities, including their costs, values and timing required for implementation, so that engineered improvements can be planned, budgeted and executed.
New technologies. Engineered improvements typically use established equipment types and apply proven solutions to identified problems. In contrast, solutions that incorporate new (“breakthrough”) technologies generally require some amount of validation through research and development. Thus, the amount of time required to implement new technologies is higher and their degree of technical and financial risk greater than for engineered improvements.
Some of the largest energy-efficiency improvements in the CPI have come through technological breakthroughs. For example, the development of the low-pressure polyethylene process in the 1950s was a major advance over the older high-pressure process, and the new process used much less energy per unit of production. A more familiar example for most people is the rise in recent years of compact fluorescent lights and light-emitting diodes (LEDs), which provide dramatic energy savings compared to the familiar incandescent bulbs. Technological advances have also improved some of the key equipment items that impact energy usage, such as heat exchangers and distillation columns, and incorporating some of the new types of equipment that are now commercially available can often lead to improved engineering solutions.
Identifying improvements
![]() |
FIGURE 3. Many steam-trap vendors provide services to maintain steam-trap populations within process facilities |
Some energy inefficiencies are endemic to the industry, and it does not require much effort to identify opportunities to improve them. This is particularly true of certain types of routine maintenance activities. For example, over time, a steam system will develop leaks and a certain percentage of its steam traps will fail, and boilers and furnaces need periodic tune-ups to remain in top condition. The question is not whether these situations create opportunities to improve energy efficiency, but rather how large the opportunities are, and what are the best ways to capture them. Many steam-trap vendors provide services to maintain steam-trap populations (Figure 3), and there are also companies that specialize in repairing steam leaks and tuning up furnaces and boilers.
Identifying most other types of energy-efficiency improvements requires a more concerted effort. Here are some effective approaches:
High-level site audits. High-level site audits can be used as a first step to identify where energy is used across a facility. This exercise will sometimes find specific inefficiencies, but its main purpose is to highlight and quantify major energy users, so they can be subjected to more detailed evaluation later.
Site assessments. Site assessments are typically carried out by a team of specialists that spends a period of time at a facility examining the operation of the main energy systems and major energy-consuming equipment. A typical team might include specialists in fired heaters, steam and power systems, rotating equipment, distillation operations, heat exchangers, and process design, although other specialties may participate, depending on the needs of the site. The team’s role is to identify inefficiencies and define opportunities that generally include improvements in operating practices and maintenance, as well as facility upgrades.
PFD reviews. Process flow diagram (PFD) reviews [5] are structured brainstorming sessions designed to tease out opportunities to improve plant operations and upgrade facilities. The procedure for a PFD review is similar to that customarily used for hazard and operability (HAZOP) studies. Plant operations and technical support personnel, with assistance from energy-efficiency specialists, review each of the main streams, equipment items and systems to identify inefficiencies and areas of opportunity.
Heat-integration studies. Heat-integration studies, focusing on improving heat recovery, are also a major source of improvement opportunities on many sites. Some heat-integration opportunities are very simple and can easily be identified in a PFD review. However, some are more complex, and specialized techniques — most commonly pinch analysis [6] — are needed to capture them.
Steam-system modeling. Steam-system modeling and realtime optimization are also widely used to identify inefficiencies in steam systems, and to define improvements both in operating strategies and facilities (Figure 4).
FIGURE 4. Steam-system modeling can reveal inefficiencies and help to define improvements both in facilities and operating strategies
Courtesy of Soteica Visual MESA
Lengthy research and development programs are generally needed to create breakthrough technologies — although occasionally they appear serendipitously. Typically only companies with strong research and development programs can venture into this field, although an alert energy manager should always be on the lookout for breakthroughs that are relevant to his or her technology.
Employee suggestions yield many very attractive energy-efficiency opportunities. Employees are most familiar with the processes and practices of their site, and many of them — including some who do not have a strong technical background — have the ability to “think outside the box.” These people represent a very fruitful resource, and their input into energy management should be encouraged. Some companies do this with competitions that reward the best ideas, either monetarily or in other ways. Welcoming and acting on employee suggestions is a visible and valuable way to change corporate and site culture.
Evaluating opportunities
Coming up with an idea is important, but it is only one step along the efficiency path. Opportunities must be screened to quantify their benefits and to estimate their implementation costs. They should also be tested for unintended consequences (for example, adverse effects on production) and for safety implications. First, the use of quick screening methods is effective in eliminating ideas that are impractical or clearly uneconomic. The remaining “high-graded” ideas can then be passed on to the appropriate organization within the company (operations department, maintenance, engineering, research and development) for further evaluation and possible implementation.
Managing the energy program
Most companies within the CPI, even small companies, have at least one person with the title “energy manager.” However, the roles played by these people can vary considerably from company to company. In almost all cases, the energy manager reports on energy usage and trends. This activity is often integrated into larger management systems. In some cases, the energy manager’s role also includes a commercial component, with energy purchases or sales. However, if a company is committed to improving energy efficiency, it is essential that the greater part of the energy manager’s job focuses on identifying and implementing energy-efficiency improvements. Remember that energy efficiency will only improve with changes in both processes and behaviors.
In order to save energy, it is important first to know where and how it is being used. It follows that an important part of the energy manager’s job, especially in the early stages of an energy management program, is tracking, quantifying and benchmarking energy use. These activities highlight the most promising areas for improvement, which can then be targeted for further investigation.
Early in an energy-management program, it is a good idea to focus on simple, low-risk opportunities that can be counted on to yield energy savings with a good return on investment. Examples include steam-leak repairs, steam-trap maintenance, steam-system balancing and other easy operating changes. Successes in these areas provide credibility for the program, and the savings that they generate can provide funding for more capital-intensive projects as the program matures.
As discussed earlier in this article, energy-efficiency opportunities can be found in a great many different areas. No energy manager can expect to have the technical expertise to handle them all, so his or her role is primarily the management of resources — especially the human resources that provide the necessary skills. This requires close working relationships with the operations, maintenance, engineering and research functions within the company. It also requires reaching out to external resources where appropriate.
The energy manager should not underestimate his or her impact as a recruiter and a cheerleader. Energy managers can equip their coworkers with study results, tools and funding help, and those people can then affect energy efficiency. Real culture change arises from the people themselves. When energy managers can draw attention to good behaviors and successes, it provides reinforcement. This might be as simple as a “thank you” to a shift team that improves its energy performance. Recognition could also include a celebratory meal, a writeup in a company newsletter, publicity through an industry award, or any number of other ways of rewarding good performance.
Success stories
Many companies have reported great successes in their energy-management programs, and the energy successes are manifested in the companies’ financial results. Here we summarize success stories from three very different companies within the CPI.
ExxonMobil Corp. (Irving, Tex.; www.exxonmobil.com) is one of the largest corporations in the world by any measure, with nearly 75,000 employees worldwide [7] and earnings of $45 billion in 2012 [8]. Its integrated business includes oil-and-gas exploration and production, petroleum refining, chemicals and electric power.
ExxonMobil started its Global Energy Management System (GEMS) in 2000. By 2009, the company reported that the program had identified savings opportunities of between 15% and 20% at its manufacturing sites, and had captured over 60% of these savings [9]. The company also reported significant investments in cogeneration facilities that simultaneously produce electricity and useful heat or steam. Cogeneration facilities represent a significant improvement in efficiency over traditional methods of producing steam and power separately, and they also result in lower emissions.
CCP Composites (Corbevoie, France; www.ccpcomposites.com) is a world leader in the production and distribution of gel coats, composite polyester resins, coatings, resins and emulsions, with a total of 14 plants worldwide.
CCP Composites’ Houston plant participated in a pilot of the Dept. of Energy’s “Superior Energy Performance (SEP)” plant certification program. SEP combines ISO-50001 compliance with an energy-management system and audited energy-efficiency improvements, and participating companies can achieve various levels of certification based on their achievements. CCP Composites achieved Gold certification in 2011, with a 14.9% improvement in energy efficiency over a two-year period. This saved 31,700 million Btu of energy, and enabled the company to capture $250,000/yr in cost savings. The savings were largely due to short-term actions and low-cost investments that have reduced natural gas demand in the process-heating and steam systems. The success at the Houston facility demonstrates that even small plants — with the appropriate corporate commitment, support and strategy — can reap significant benefits from the implementation of an energy-management system [10].
Eastman Chemical Co. (Kingsport, Tenn.; www.eastman.com) is a global producer of specialty chemicals, including a broad range of advanced materials, additives and functional products and fibers. The company employs approximately 14,000 people around the world, and its 2013 revenues were approximately $9.4 billion [11].
Eastman has a long history of energy-management successes. The company ran a concerted study in the early 2000s to generate project ideas for energy efficiency, and many improvements were made — especially on the two sites that together accounted for over 90% of the company’s energy use. However, in 2010, there was a major change, as the company announced an aspirational goal to inspire radical improvement and made a public pledge to the Dept. of Energy’s Better Buildings, Better Plants Program [1] to reduce energy intensity by 25% over ten years with a baseline of 2008, the year Eastman became an Energy Star Partner [2]. Its current program has strong executive-level backing and a multimillion dollar budget allocated to energy efficiency projects [12]. The program is robust, including not only strong technical components, but also broad support and input from many internal organizations and engagement of employees at all levels. It has the following three guiding principles:
- Ensure the accuracy of utility information
- Maximize operating efficiency
- Incorporate energy efficiency in capital investment decisions
- Eastman’s efforts are paying off.
Energy intensity improved 8% from the baseline year of 2008 through 2013. The improvement was worth $28 million in 2013 based on current production and energy prices.
Closing thoughts
Energy efficiency is an important factor in economic and environmental performance in the CPI, and many companies have made significant reductions in their energy intensity, with corresponding savings in energy costs. Four main types of opportunities provide the savings: operational improvements, effective maintenance, engineered improvements and new technologies. Many tools and techniques are available to help in identifying the opportunities at any specific facility, and a robust energy-management program supports the behavioral and process changes needed to foster efficiency improvements. Energy savings are material to company performance, and a culture of efficiency improvement can continue to pay benefits for years to come.
Edited by Scott Jenkins
References
1. U.S. Dept. of Energy, Better Plants Program, energy.gov/eere/amo/better-plants/, accessed July 31, 2014.
2. U.S. Environmental Protection Agency, Energy Star Program, www.energystar.gov, accessed July 31, 2014.
3. International Organization for Standardization, “ISO 50001 — Energy Management,” www.iso.org/iso/home/standards/management-standards/iso50001.htm, accessed May 14, 2014.
4. Rossiter, A.P., Back to the Basics, Hydrocarbon Engineering, 12 (9), pp. 6973, 2007.
5. Rossiter, A.P. and Davis, Joe L., Jr., Identify Process Improvements for Energy Efficiency, Chem. Eng. Prog., 110 (9), pp. 53–58, 2014.
6. Rossiter, A.P., Improve Energy Efficiency via Heat Integration, Chem. Eng. Prog., 106 (12), pp. 3342, 2010.
7. ExxonMobil Corp., ExxonMobil Corporate Citizenship Report, 2013.
8. ExxonMobil Corp., ExxonMobil Annual Report, 2012.
9. ExxonMobil Corp. ExxonMobil Annual Report, 2009.
10. U.S. Dept. of Energy, “CCP Composites Achieves Superior Energy Performance Gold Certification,” superiorenergyperformance.energy.gov/pdfs/ccp_casestudy.pdf, accessed July 31, 2014.
11. Eastman Chemical Co., Company Profile, www.eastman.com/Company/About_Eastman/Pages/Profile.aspx, accessed July 31, 2014.
12. Nolen, Sharon, “Energy Management: When Good is not Enough,” 36th Industrial Energy Technology Conference, New Orleans, La., May 2023, 2014.
Authors
Alan Rossiter is president of Rossiter & Associates (4421 Darsey St., Bellaire, TX 77401; Phone: 713-823-3980; Email: [email protected], www.rossiters.org/associates), a process-improvement consulting company specializing in industrial energy efficiency. Clients include ExxonMobil, Natural Resources Canada, Syncrude Canada, ConocoPhillips, Sasol, LyondellBasell, Valero and Hess. Rossiter has more than 30 years of process engineering and management experience, including ten years with Imperial Chemical Industries (ICI) in England, and more than 60 publications, including three books. He has a Ph.D. in chemical engineering from the University of Cambridge, is a chartered engineer (U.K.) and a registered professional engineer (Texas), and was the 2010 Chair of the South Texas Section of the AIChE.
Beth Jones was, for several years, the worldwide energy manager for LyondellBasell Industries, after various positions in process engineering management and optimization in her 25 years within Lyondell Basell and its predecessor companies. She retired in 2013 to enjoy new adventures — a transfer to England with her husband and a subsequent invitation to work on a book, “Energy Management and Efficiency for the Process Industries,” with Rossiter. Jones has a B.S.Ch.E. from Oklahoma State University, and is a Certified Energy Manager.
Note: the book “Energy Management and Efficiency for the Process Industries” by Rossiter and Jones will be published in early 2015.