Agglomeration converts fine powder particles into larger ones by introducing external forces. Major benefits for solids processors include dust reduction, easier handling, more complete utilization of raw materials and densification. Agglomerating particles happens by a variety of means, including mixing with a liquid, applying pressure and heating. This reference reviews equipment for these approaches.
Tumble-growth agglomeration
In the first stage of wet agglomeration, fine powder, liquid and binder are combined in a mixing chamber. Fine particles are wetted with an appropriate liquid, typically water. Surfactants or other chemicals can be added to improve the wettability of the solid particles and improve pellet formation. Next, moist particles are joined together to form green (wet) agglomerates. Green particles are generated by first forming nuclei, which then grow into larger aggregates by layering or coalescence. Nucleation and aggregate growth may take place in separate pieces of equipment. For example, agglomerates from a pin mixer can be fed into a disk pelletizer. The final stage is drying or curing, which takes place in a separate device.
Binders are frequently introduced to improve the agglomerates’ crush strength. In a wet tumble-growth process, powder, liquid and additives are fed continuously into the chamber, where the wetted mass is then sheared or kneaded until the liquid is evenly distributed and the granules have the desired size and strength. Examples of organic binders are waxes, rosin, starch and alginates. Inorganic binders include alkali silicates, bentonite and various aqueous solutions and dispersions. The major criteria for selecting a binder are cost, availability, compatibility with the product’s final use, and its ability to give the agglomerates their desired crush strength.
Tumble-growth agglomeration equipment tends to have lower capital costs than the other methods, but costs may be higher if drying is required. Agglomerates produced by tumble-growth technologies tend to have a lower bulk density and a wider particle-size distribution as compared to other agglomeration methods. Popular wet agglomeration equipment includes pin mixers, plough mixers, disc pelletizers, fluidized beds and other technologies. Dry agglomeration is similar to wet, but it uses less wetting agent.
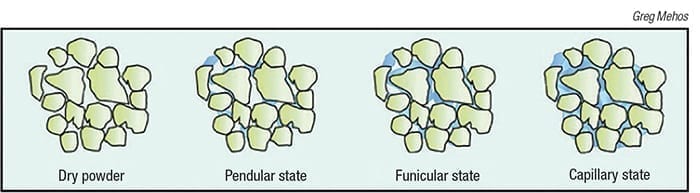
Figure 1. When liquid is added to powder, the agglomerates formed typically have their optimal strength at 40–90% of their full saturation amount
Pressure agglomeration
Because attractive forces between particles intensify as the distance between them decreases, applying pressure can lead to exceptionally strong agglomerates. Pressure agglomeration falls into two general categories: roll compaction and die compaction. Roll compactors use a mechanical force to press powder. Fine particles are fed between two counter-rotating rolls, which draw material into the gap between them. The powder is compressed into a sheet if smooth roles are used, or formed into strips if the compactor is equipped with corrugated rollers. The sheet or strips are then fed through a flake breaker. The agglomerates are irregular in shape, but often have sufficient flowability. The powder is fed by gravity or with a feeder. The equipment works best when the powder is de-aerated before it reaches the rolls. Die compaction also relies on mechanical forces to press fine powders, but also allows agglomerates with a desired shape.
Pressure agglomeration equipment tends to have higher capital costs, but lower operating costs, than tumble-growth agglomeration. Agglomerates formed by pressure have a higher bulk density, but may be more prone to attrition.
Heating agglomeration
Extruders can heat powders to temperatures high enough to cause melting or sintering. Two types of extruders are used — ram extruders are used batch-wise, while screw extruders are for continuous processing.
In a ram extruder, powder is fed into a barrel equipped with a die plate and then isolated by a hydraulically-driven piston. The powder is then forced toward the die. The barrel may be heated (although temperatures rise due to friction, even without external heating). The entire plug of powder does not necessarily have to reach its melting point, because only a thin layer of liquid needs to be sheared between the wall and the plug. The extruder is equipped with cutters immediately downstream of the die plate. Because high pressures are generated, the feed material must have a low moisture content. Otherwise, the liquid will flash upon leaving the die plate and potentially fracture the pellets that are formed.
Auger or screw extruders comprise four sections: feed, conveying, melting or sintering, and pumping. A feed hopper contains the powder material and allows it to enter the screw beneath its outlet. The conveying section is followed by the melt or sintering section. Friction or a heated barrel increases the temperature of the conveyed powder. Pressure is generated by pumping the material through a die plate or restricted orifice. Cutters are used to convert the extrudate into pellets.
Editor’s note: Material in this column comes from: Mehos, G. and Kozicki, C., Choosing Agglomeration Equipment, Chem. Eng., October 2017, pp. 51–57.
Sponsored by: