Bulk-solids handling is a critical aspect of many product manufacturing processes throughout the CPI, but the field is often underappreciated. Research centers that specialize in bulk-solids handling and particle technology are important resources for expanding knowledge and solving technical challenges
Processes involving solid materials are very common throughout the chemical process industries (CPI), with many estimates suggesting that at least 70% of industrial processes involve the handling, conveying or processing of bulk solids materials. However, despite the prevalence of solids-handling processes and their importance to the production of many end products, solids-handling science and practice often remains underappreciated and poorly understood. In part, the gaps in understanding are a function of the complexity of bulk-solids-handling operations, and also because bulk-solids education is generally only cursorily included in most undergraduate mechanical and chemical engineering degree programs.
Specialized research centers focused on the study of bulk solids in industrial processes bridge some of the gaps in understanding by providing both education on bulk-solids-handling processes and equipment for students and working engineers, and conducting industry-relevant research on the behavior of powders and other solid materials at industrial sites (see sidebox, below).
Research Centers Focused on Bulk-Solids Processes
The following research centers focus on processes involving bulk solids and powders.
Kansas State University Bulk Solids Innovation Center (BSIC; Salina, Kan.; bulk-solids.k-state.edu). BSIC has six laboratories for conducing industry-sponsored research, and a full-scale bulk-solids test bay. BSIC provides material properties testing, short courses, product and equipment testing, research, and consulting services.
Wolfson Centre for Bulk Solids Research and Technology at the University of Greenwich (U.K.; gre.ac.uk/engsci/research/groups/wolfsoncentre). The center offers consultancy, research and short courses for industries that handle powder or granular materials.
Centre for Bulk Solids and Particle Technology at the University of Newcastle (Callaghan, N.S.W., Australia; newcastle.edu.au/research/centre/cbspt/). The center works in conjunction with TUNRA Bulk Solids (TBS; bulksolids.com.au), an organization that provides high-level professional consulting and contract research service to the resources, process and manufacturing industries.
The Center for Particulate Products and Processes (CP3; engineering.purdue.edu/CP3) at Purdue University (West Lafayette, Ind.; www.purdue.edu). This integrated laboratory is shared among several different departments with connections to solids materials handling. CP3 has a pilot-scale facility for the study of powders.
Institute of Solids Process Engineering and Particle Technology at the University of Technology Hamburg (Germany; tuhh.de). Led by professor Stefan Heinrich, this center focuses on the industrial applications of fluidized-bed technology.
Particle Technology Research Center at Western University (London, Ont., Canada; powders.ca). The center is dedicated to research, development and innovation in particle technology.
Center of Excellence in Particle and Material Processing Technology (PMPT) at Chulalongkorn University (Bangkok, Thailand; research.chula.acc.th). This center focuses on nano-functional particulate materials synthesis and application, and bio-functional particulate materials synthesis and application.
Particle Engineering Research Center (PERC) at the University of Florida (Gainesville, Fla.; perc.ufl.edu). The center’s vision is to innovate and transform particle science and technology advances into useful applications.
Centre for Industrial Bulk Solids Handling at Glasgow Caledonian University (Glasgow, Scotland, U.K.; gcu.ac.uk). This center is directed by professor Don McGlinchey, who provides consulting services.
Engineering Research Center for Structured Organic Particulate Systems (C-SOPS) at Rutgers University (New Brunswick, N.J.; c-sops.org). The center brings together a cross-disciplinary team of researchers to work with industry leaders and regulatory authorities to improve the way pharmaceuticals, foods and agriculture products are manufactured. C-SOPS partners include the New Jersey Institute of Technology, Purdue University, the University of Puerto Rico at Mayaguez, and more than 40 industrial consortium member companies.
A complex, multidisciplinary field
The lack of expertise in solids processing results from several factors: some having to do with the nature of the field, and others having to do with logistical challenges in education. “Solids handling is a complex and multidisciplinary area that requires expertise from mechanics, materials science and chemical engineering,” says Raju Dandu, director of the Bulk Solids Innovation Center (BSIC) at Kansas State University at Salina (bulk-solids.k-state.edu). “Further, there is a lack of clearly defined common core knowledge for undergraduate and graduate education between and across the complex bulk solids discipline,” he explains.
The field of solids handling includes a wide range of diverse substances, complicating efforts to generate models that work well across multiple situations. Mike Bradley, director of the Wolfson Centre for Bulk Solids Handling Technology at the University of Greenwich (U.K.; bulksolids.com), explains: “Every powder is different — even powders with the same name, and made to the same specification, will often display very different handling and flow properties if they are made in different plants. So you can’t just draw conclusions from experience or available data.”
“You need to get samples of the powder and characterize them in relevant ways — not just the particles sizes, densities, moisture contents and so on, but their bulk behavioral properties, such as flow properties measured in a shear tester, or pneumatic conveying properties measured in a pipeline test rig and so on. Without undertaking those steps… design is no better than guesswork,” Bradley says.
Paul Mort, director of the Center for Particulate Products and Processes (CP3) at Purdue University (West Lafayette, Ind.; www.purdue.edu), echoes the challenges of solids flow properties. “Particle morphology is a critical parameter, and it affects how the substance flows in processes. Often particle shapes are complex and varied, and information on shape is not often included in specifications for materials,” he says.
The field of solids handling is full of “exceptions,” notes Todd Smith, business and strategy manager at BSIC. Because many solid materials defy modeling, and often, the equations used to determine design parameters don’t predict real-world behavior, it’s very difficult to write educational textbooks and resources for those who are studying this area, Smith says.
But even if such resources were available, institutions of higher learning face challenges in offering additional courses in bulk-solids handling. The existing chemical and mechanical engineering undergraduate program curricula in the U.S. are already full at 120–128 credit hours, leaving little time for specialized solids courses. BSIC’s Dandu says incorporating a wide range of multidisciplinary knowledge, as well as information on evolving technologies, into the curriculum can be difficult, because doing so requires close coordination among several different university departments and faculty. Additional hurdles include establishing access to experienced faculty and to a range of teaching resources, software and equipment.
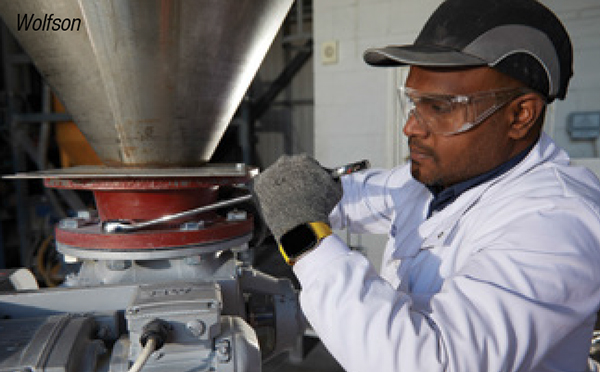
FIGURE 1. Solids handling involves multiple disciplines, including mechanical engineering, materials science, chemical engineering and others
Student interest
Before graduates are produced, however, students must be attracted to the bulk-solids field as an area of study. Achieving this has proven to be difficult as well. “Despite the industrial world’s significant dependence on bulk solids handling operations, this discipline remains relatively unknown, when compared to related fields like mechanical and chemical engineering,” says Dandu.
In part because of this lack of awareness generally, generating significant student interest in bulk-solids handling can be an uphill battle. “Most students will not take an interest in the final year option to study bulk-materials handling,” says the Wolfson Centre’s Bradley. “Despite the ubiquity and importance of bulk-solids handling across all process engineering disciplines — and the great career opportunities available — very, very few students take the unit in bulk solids handling,” he explains.
The result is a shortage of engineering graduates with an emphasis in bulk-solids handling. “Considering that bulk solids make up more than 80% of items transported around the world, it is crucial to address the need for comprehensive education in bulk-solids handling as an option in both chemical and mechanical engineering,” BSIC’s Dandu says. “Offering a certificate program in bulk-solids handling can be an effective solution to meet this need.”
Wolfson Centre’s Bradley remarks, “I’d like to see powders and particulates included as part of the entire educational curriculum — liquids, gases and solids are studied at all levels of schooling and in college-level courses. Powders are just as important, not just to industry but in the natural environment as well.”
However, there are forces working to overcome these challenges, including partnerships between academic centers and industry that are often observed in bulk-solids research centers. “Industry partners can provide funding, expertise, opportunities for practice-based teaching, and real-world challenges to academic researchers,” Dandu explains. “As a result, educational programs are incorporating and sustaining interdisciplinary research and training, leading to inter- and intra-departmental activities, such as developing interdisciplinary courses, creating interdisciplinary degree programs and introducing interdisciplinary faculty appointments.” Graduates of such programs are “better equipped with a broader understanding of bulk-solids systems and the ability to work effectively across different fields to meet industry workforce needs,” he adds.
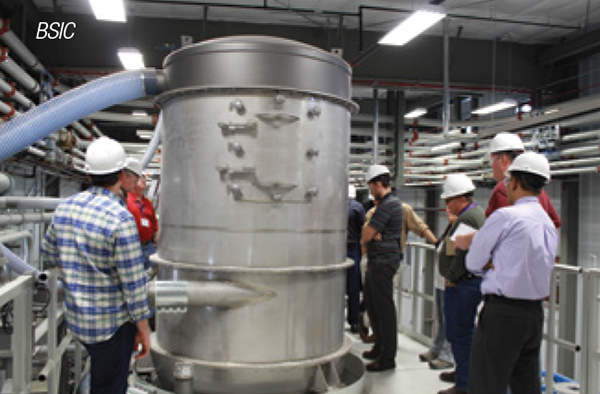
FIGURE 2. Academic research centers focused on solids provide opportunities for companies to solve real-world industrial problems
Addressing industrial issues
Because only a relatively few engineering graduates have a specialized knowledge of solids, and because large companies have, for the most part, phased out in-house R&D laboratories with a focus on powders and solids, academic research centers in bulk solids have taken on a critical role in supporting both education and collaborative research.
“A significant part of BSIC’s role is to provide continuing education focused on solids-handling processes,” comments Smith. And for research, no other public entities are studying solids handling, “so there’s no overall ‘go-to’ place for technology improvement,” he says. Much of the research funding at BSIC and other centers comes from companies that are experiencing manufacturing challenges and looking to solve a problem in solids handling or processing.
Of Wolfson Centre, Bradley says most of its consultancy services to industry, whether for new plant design or troubleshooting, use techniques and knowledge generated in Wolfson’s own research projects. In addition, the center runs short courses and conferences to present findings and educate interested parties.
“And quite a few of our Ph.D. students are sponsored by companies who use or make powders, or powder-handling equipment, and that can be a great way to generate not just new knowledge, but also an expert for their team.” Bradley says.
“Applications knowledge for solids handling is the bottleneck,” says BSIC’s Smith. A lot of the knowledge is gained case by case, he adds, and BSIC is trying to share information with processing companies.
Examples of how research centers have helped solids-industrial clients are as varied as the solids themselves. BSIC’s Smith talks about how BSIC often helps with process scaleup. In one example, a company changed product recipes, and the alteration worked well at laboratory scale, but caused problems at full scale. BSIC staff worked to figure out what was needed to make the large-scale process work with the new recipe.
Other examples of industrially relevant research conducted at BSIC include an analysis of fluidization of powder to improve a bagging operation, research to identify strategies for reducing product degradation during conveying operations; projects to improve understanding of abrasion resistance; dust safety and others, Smith says.
At Wolfson, Bradley says research projects related to handling food products and ingredients are a constant source of work at the center, and pharmaceutical materials are also common. Troubleshooting and re-engineering of plants that handle biomass and waste materials as feedstocks has been one of the main growth areas at Wolfson in recent years. “These are very challenging materials to handle and a lot of projects have huge failures that result from failing to do enough work to make sure the handling equipment is properly suited to the feedstock they will handle,” Bradley says.
One recent research project at Wolfson involved developing a “Virtual Formulation Laboratory,” aimed at companies designing powder formulations, often in food and pharma, but in other areas as well. “This has produced a software tool that formulators can use to predict how a potential new formulation will behave in manufacturing, based on information about the ingredients. Then they can see if it’s likely to be problematic, and try out adjustments to the formulation to make it easier to manufacture, all from the desk,” Bradley explains.
Additive manufacturing (AM; 3D printing) is also a fast-growing area that requires a great deal of solids-handling know-how, since the starting materials are often in powder form. Bradley and Perdue’s Paul Mort both mention AM as an active area of research, often for automotive and aerospace applications. “Powder quality is really critical to finished part quality — a rogue particle can cause a flaw in a part that will scrap it — so we’re doing a lot of research in that area,” Bradley says.
Pneumatic conveying
Pneumatic conveying is a prominent topic at bulk-solid research centers, both in research and for education (for a brief overview of pneumatic conveying, see the article on pp. 44–45). “In pneumatic conveying, a lot of the work comes in simply blowing the powder, measuring the relationship between air flow, solids flow and pressure drop in the pipeline, then using this information to design a new system,” Bradley says. “But a surprisingly common issue we study is how materials of the same specification but made in different plants or bought from different suppliers, compare in handling.”
In short courses, the two most popular subject areas have always been pneumatic conveying, and discharge from hoppers and silos, Bradley says. Companies come to us to get a better understanding of how to buy, manage and use these technologies, he notes, but safety issues — especially electrostatics, explosions, silo failure and so on also attract a lot of attention.
At BSIC, Smith says pneumatic conveying is also its most popular continuing education short course. “There are lots of variations in how to do it, and it’s relatively easy to grasp the basic concepts of the process, but it’s hard to understand how to troubleshoot, and often difficult to work out why certain materials behave in particular ways,” he says.
Reaching into the future
BSIC director Raju Dandu says the megatrends of digital transformation and sustainability are set to significantly impact bulk-solids research and education, and the educational and industry communities must embrace and incorporate these technologies. “Digital technologies, such as design and analysis, simulation software, artificial intelligence, machine learning, virtual reality, augmented reality and data analytics, are enabling researchers to gain a better understanding of the behavior of bulk-solids storage, conveying, and handling, leading to the design of more efficient systems.” Additionally, Dandu says, “these technologies are being integrated into educational programs, providing students with hands-on experience using state-of-the-art tools for bulk-solids research and systems design, as they address problem-, project- and outcome-based learning.”
The focus of the CPI on sustainability is “driving the development of new processes and technologies for handling bulk solids that are more energy-efficient, produce less waste, consume less water, and have a lower environmental impact,” Dandu comments. “Educational programs are also incorporating sustainability principles, product- and systems-lifecycle management and circular-economy concepts into their curricula, providing students with the knowledge and skills needed to design and operate sustainable bulk-solids systems.”
Both digital transformation and sustainability “encourage a multidisciplinary approach to bulk-solids research and education, bringing together experts from different fields,” Dandu says, and are also “driving greater collaboration between academia and industry in the field of bulk solids.”
Scott Jenkins