To confidently design, operate and troubleshoot solids-handling processes, engineers need to characterize powder flow in ways that relate to in-plant behavior. Universal powder testers provide the multi-faceted characterization that is necessary to reliably predict operational performance. This article examines the data that such instruments generate, and discusses their practical application.
While many process engineers would express confidence in their ability to effectively design and optimize plants for liquid and gas processing, even those with extensive experience are often challenged by powder-handling processes. The open literature offers only limited data and the links between actual process behavior and defined powder properties often appear tenuous and complex. However, for effective processing and design, it is essential to describe powder behavior in a process relevant way.
Dynamic flow characterization measures powders in motion, offering engineers an intuitively rational approach to characterization. The most advanced dynamic powder testers incorporate a range of methodologies, characterizing conventional bulk and shear properties to supplement dynamic measurement. Since powders can be measured in a consolidated, conditioned, aerated or even fluidized state, these universal powder testers generate information that relates closely to a wide range of processing conditions. Such data provide a firmer basis for design, and provide insight that rationalizes operational experience, enhancing the underlying knowledge base.
One of the most important aspects of powder behavior is flowability under real-world conditions. Getting a powder to flow smoothly through multiple unit operations, at the required flowrate, is often extremely difficult. Here we consider why powders exhibit variability, and addresses the issue of powder flow in some detail. A particular focus is the impact of applied force, the contrast between extruded or forced versus unconfined flow, and the implications of these for processing.
Powder fundamentals
Key to understanding powders is an appreciation of the reasons why behavior, especially flow properties, can change so radically under process plant conditions. Unfortunately many variables influence flowability. Some relate to the solid itself — particle size, shape, surface roughness or density, for example — while others are determined by the processing environment or system.
Primary examples of system variables include air content, electrostatic charge and moisture level. Maintaining consistency, during both measurement and processing is challenging, because it requires that all influential variables be kept constant (or at least controlled within limits).
Over time, the flow behavior of a powder that starts off its processing life with well-defined flow characteristics may change. For instance, as it passes through the plant, the powder may pick up or lose moisture, becoming tribo-charged or segregated, suffer from attrition or agglomeration (thereby changing size and/or shape), fluidize or become compacted. Each change will influence flowability.
This is why it is so important to understand the conditions to which the powder will be exposed as it moves through different unit operations. For example, during transport, powders may consolidate through vibration, while those in bulk storage in a silo, sack or hopper may consolidate under their own weight. Conversely, discharge from a container or sack usually increases aeration, which encourages the powder to flow freely — possibly too freely — potentially increasing the risk of flooding. If the moisture level of the storage or transport environment is not closely controlled, then this too is likely to influence downstream processing performance.
Knowing what demands the process is going to place on the powder is, however, only one side of the problem. The other is understanding the powder’s likely response. This is where the use of relevant measurement techniques plays an important role. Matching powder properties with the demands of the process is essential to robust, trouble-free operation. In contrast, a poor match will give rise to the problems that are routinely encountered by solids processors: variable flowrates, stoppages/blockages, sub-optimal finished product quality and excessively high manual-input requirements.
Measuring powders
![]() |
Over the decades, in an effort to produce tools that aid understanding, powder scientists and engineers have developed many different characterization techniques. Bulk, shear and dynamic properties are all now commonly used as input to the design and operating strategies, with universal powder testers incorporating all three types of measurement in a single instrument. Important bulk properties include density, compressibility and permeability, while shear properties define both the ability of a consolidated powder to transition from a stationary into a dynamic state, and the ease with which it will move against the surface of the process equipment. Dynamic properties relate directly to flowability, since they are measures of a powder in motion, and quantify cohesion as well as sensitivity to such influencing factors as aeration, consolidation, flowrate, moisture and electrostatic charge.
Core dynamic parameters, such as basic flowability energy (BFE) and specific energy (SE), quantify how easily a conditioned powder moves when it is subjected to compacting motion, and when disturbed in an unconfined way, respectively. By characterizing samples in a compacted, aerated or even fluidized state, the effect of air on the baseline BFE measurement, and hence on flow behavior, can be readily quantified. The effect of other variables such as flowrate and moisture content is equally easy to evaluate.
Conditioning the sample prior to measurement is an important preparation step, involving closely prescribed, gentle displacement of the powder. Excess air is released from an overly aerated bed, while a consolidated sample is broken up. The goal in either case is to achieve a homogeneous, loosely packed, slightly aerated powder bed. This conditioning step ensures high reproducibility, which supports the sensitivity of dynamic characterization. Techniques that fail to employ such a preparation step are likely to provide results that are a function of the way the powder was handled and loaded by the operator, as much as they reflect true differences between test samples.
The following case study highlights the type of information that can be generated using a universal powder tester, focusing on the contrast between forced and unconfined flow behavior. As the results illustrate, powders that flow freely when unconfined can “lock up” and exert high resistance to forced flow, while more cohesive materials, which flow poorly under gravity, extrude when forced to flow.
Case study
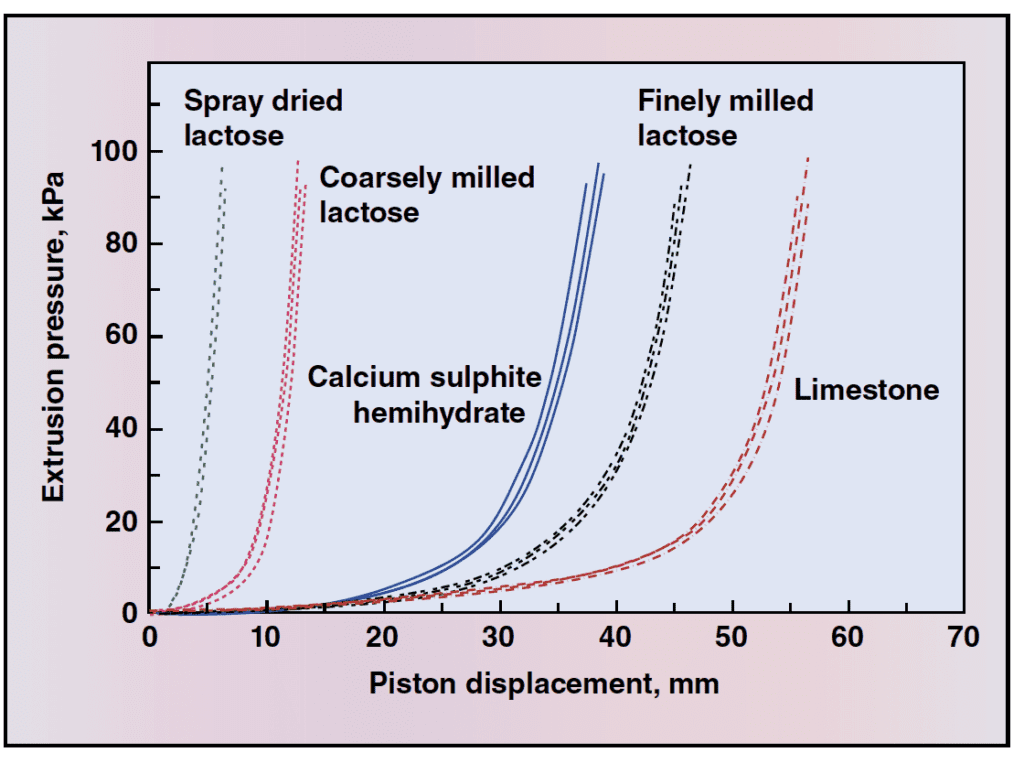
Figure 2. This figure shows the extrusion pressure as a function of piston displacement for five different powders (at piston velocity of 10 mm/s). As the piston pushes down on the powder extrusion, pressure rises to an imposed limit at which point extrusion is stopped
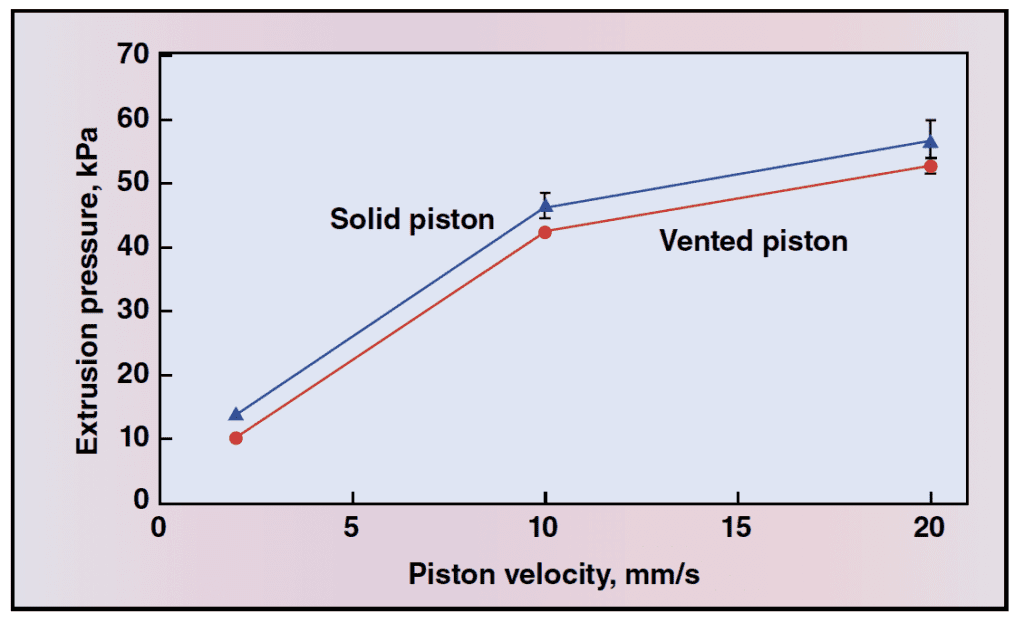
Figure 3. This figure shows the influence of piston type
and extrusion speed on the extrusion performance of
limestone powder. Faster extrusion speeds are more
efficient, but the type of piston used has little impact
Investigating the extrusion behavior of different powders. Physical and flow properties (dynamic, bulk and shear) were measured for five different materials: limestone (CRM116), three grades of lactose (spray dried, coarsely milled and finely milled) and calcium sulphite hemihydrate. A universal powder tester was used, employing standard methodologies for all flow measurements [ 1, 2, 3]. Fitting the instrument with an extrusion device also enabled the extrusion behavior of the powders to be studied (Figure 1).
During extrusion tests, a piston forces a conditioned sample of known volume through a 25-mm bore cylinder and out of an 18-mm diameter orifice. During the test, the compressing piston moves down at constant speed until a force limit is reached, at which point the amount of extruded powder is weighed to determine an extrusion percentage: the mass of extruded material compared to the initial mass of powder in the cylinder. Compression tests were carried out using a vented piston, which allows air to escape through the piston face, and the results were compared to data obtained during compression with a solid piston. Compression speed was also investigated by varying the axial speed of the piston.
A comparison of the extrusion results for the different materials shows markedly differentiated behavior. The limestone extrudes relatively easily, with almost half of the material extruding from the orifice before the force limit is reached. By comparison, the coarsely milled and spray-dried lactose (which have an extrusion percentage of 3.5 and 2.9%, respectively) extrude far less easily. Plotting the pressure rise observed during extrusion (Figure 2) shows that for the limestone, pressure increases relatively slowly, rising more rapidly only when the piston starts to obstruct the outlet to the orifice (Figure 1). Conversely, with less easily extruded materials, the piston travels a much shorter distance before reaching the force limit.
Figure 3 illustrates the effect of extrusion speed and piston type for limestone. As shown, extrusion is more successful when the piston moves at higher rates, thereby reducing the time available for the entrained air to escape under compression. By contrast, the type of piston used has less of an effect.
Extrusion behavior correlates particularly well with BFE, permeability and the ratio of generated normal stress to shear stress (Figure 4). This provides some insight into observed behavior. The relatively low permeability of the limestone highlights its reluctance to release air, a common feature of more cohesive materials. Powder beds containing larger or more spherical particles, such as the two coarse lactose grades for example, present little resistance to air flow. Finer particles on the other hand tend to form agglomerates that entrain air, retaining it within the sample.
Figure 4. This figure shows the correlation between powder extrusion performance
and powder flow characteristics. Extrusion performance correlates directly with permeability, and is inversely related to both BFE and the ratio of generated normal stress to shear stress
The measurement of BFE subjects the powder to a compacting downward force, so it is closely akin to extrusion testing. As the blade pushes through the limestone sample the entrained air acts as a cushion, minimizing the flow zone and the forces acting on the blade. In contrast, pushing the blade through a coarsely milled lactose bed is much more difficult. Since there is little air present, the force transmits rapidly through the bed to the blade, the flow zone expands and the resulting BFE measurement is high (Figure 5). This is exactly analogous to the extrusion pressure profiles. With coarse materials, the compressing force transmits through the entire bed, which behaves more like a continuous solid, locking up and exerting significant resistance. With finer materials, the entrained air dampens this effect and lubricates the flow.
The anomalous BFE result for spray-dried lactose is attributed to the spherical nature of the particles, which helps to reduce flow energy, in comparison to the coarsely milled lactose with its irregular morphology. However, the ability of the regular spherical particles to lock up and resist flow when more closely confined is reflected in the ratio of normal stress to shear stress.
This parameter, which broadly echoes the trends in BFE and extrusion percentage, is governed by the efficiency with which particles pack together. When particles are sheared in a horizontal plane, stresses radiate in all directions.
The result is a tendency for the powder to dilate, as particles need to move upward in order to move relative to one another in the horizontal plane. When particles are efficiently packed together, the stresses generated axially are relatively high, for the same reasons explained previously in relation to a high BFE: there are relatively few air spaces to accommodate the dilation. The relatively low shear stresses between the larger particles is further explanation for the larger generated ratio of normal stress to shear stress.
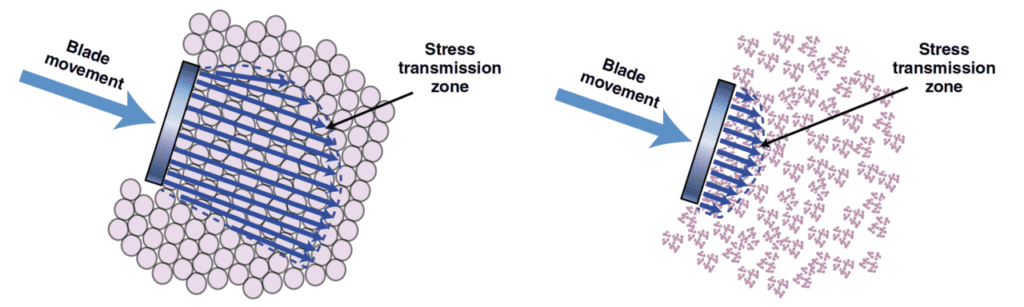
Figure 5. In forced flow behavior of non-cohesive and cohesive powders, entrained air in the cohesive sample absorbs the motion of the blade, but with a closely packed powder the stress transmission zone is much larger, giving higher values of BFE
In this study, lower extrusion rates resulted in a smaller extrusion percentage, regardless of piston type. This is because a slower piston speed forces entrained air from the sample, making it more resistant to flow. This is supported by the flow rate index (FRI), which shows that the limestone is 2.06 times less likely to flow at low flowrates. The irrelevance of piston type confirms that it is the rate of air released from the bed via the extrusion orifice, rather than through the piston face, that controls this effect. Rapid extrusion encourages the retention of entrained air, maximizing the extrusion percentage. It is likely that the extrusion percentage for powders with lower FRI values would be less sensitive to piston speed.
Optimization efforts
Characterizing powders as described above clearly generates a database of information; however, it also raises the question of how best to use the results for process optimization. One approach is to analyze the demands of the process and see whether the powder has properties that are a “good fit.” Consider the process of tablet manufacture, where powder is required to flow efficiently under gravity into the die, and then demonstrate sufficient bulk stiffness to compress efficiently into a tablet.
Powders with a high extrusion percentage are likely to contain excess air and result in fill weight variability. When compressed, the low bulk stiffness means the punch will have to travel further to achieve the same compaction force, creating some tablets that are undersized. Conversely, powders that lock up and resist extrusion are likely to compact uniformly under the extreme stresses imposed, resulting in tablets with good mechanical strength and consistent size and dissolution characteristics. Powders with high values of BFE and permeability, and low values of SE and compressibility are therefore likely to be more consistent during tablet manufacture, resulting in tablets with the desired properties.
When the focus is on using an existing piece of equipment for a new material or troubleshooting an operation, efforts to develop a comprehensive characterization can leverage operational experience in a way that improves operations. Consider, for example, a screw feeder that is used to convey material from one point in the process to another, at a facility that handles a range of powders. With some products the equipment works well but with others it does not and a poorly performing material is only detected once it is in the conveyor.
Here, comparing the properties of materials that are easily conveyed with those that are not leads to the definition of a specification for optimal operation. Instead of simply knowing that powder A performs poorly while powder B is fine, it becomes clear that establishing threshold values — for instance, BFE in the range a to b or permeability below x — will help to define acceptability. In this way, if a new material is introduced, operational performance can be predicted before it goes into the plant. If there is no choice but to process a material that does not suit the equipment, then informed modifications can be made to process settings on the basis of understanding behavior.
This latter approach of rationalizing operational experience in terms of reproducibly measurable parameters is a powerful way of deriving maximum benefit from information that already exists within the company. Experience is, by its nature, empirical and specific. On the other hand, an understanding of what gives rise to certain types of behavior is knowledge that is more generic and widely applicable, and therefore has great value.
Comparing powder properties is especially effective for addressing batch-to-batch variability, in a feed for instance. Consider the case in which a material is sourced from two different suppliers. Both meet the defined specification, but detailed process monitoring shows that flow from the feed hopper is much more erratic with one material compared to the other. In this case the specification is not controlling a variable relevant to performance. However, measuring a range of parameters for both materials is likely to identify a difference. A particular powder’s response to air or its propensity to segregate could influence in-hopper behavior. Defining the initial specification more closely on the basis of in-depth characterization eliminates the problem and provides a blueprint for alternative supplies.
Closing thoughts
Powder processing is undoubtedly a challenge, but modern universal powder testers can help. They provide comprehensive characterization of a range of dynamic, bulk and shear properties. Dynamic measurements of a conditioned, compacted, aerated or fluidized sample in motion are especially relevant for processing applications and provide an intuitively sensible approach for process engineers. Such tests provide a sensitive, reproducible and reliable method of quantifying powder flowability and also measure the impact of variables such as air content, degree of compaction and flowrate.
References
1. Cooke, J., and Freeman, R., The Flowability of Powders and the Effect of Flow Additives, In World Congress on Particle Technology, Orlando, U.S., 2006.
2. Freeman, R., Measuring the Flow Properties of Consolidated, Conditioned and Aerated Powders — A Comparative Study Using a Powder Rheometer and a Rotational Shear Cell, Powder Technology, 174, pp. 25–33, 2007.
3. Freeman, R.E., Cooke, J.R., and Schneider, L.C.R., Measuring shear properties and normal stresses generated within a rotational shear cell for consolidated and non-consolidated powders, Powder Technology, 190, pp. 65–69, 2009.
4. University of Cambridge, Powder and Paste Processing website. www.cheng.cam.ac.uk/research/groups/paste/current/slr.html
Author
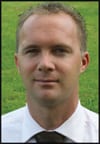