Cutting edge technologies for recycling mixed plastics are being developed, and carefully chosen control valves will be critical for process viability and success
Since their introduction over a century ago, plastics have become a mainstay in all aspects of our life. They are in the clothes we wear, make up a significant part of most cars, appear in all types of food packaging and are integral in a broad collection of medical devices. Plastic production began to explode in the 1930s when production methods using ethylene, then considered a refinery waste product, were invented. Since then, production has ramped up almost exponentially.
Most of the produced plastic ends up in the environment — filling landfills, lining roadways, washing up on beaches, and choking waterways and oceans. Plastics degrade very slowly in the environment, and they instead tend to slowly break down into ever smaller pieces of plastic called microplastics.
Efforts to address this problem are being undertaken by governments and companies around the world. Some are working to replace plastics with more sustainable and biodegradable alternatives, while others are working to recycle plastics rather than following the single-use-and-discard model, which has dominated.
Recycling plastics is far more difficult than recycling other materials like steel or aluminum, because of the following:
- There are many different types of plastics, and each requires different solvents, has different melt points and has different molecular structures
- Separating plastic types from each other and from other non-plastic waste streams is extremely difficult and costly
- The recycling process temperatures are far lower than those of metals, so feed stream contaminants are not destroyed as they are in most metal recycling
- Depending on the recycling method and type of plastic, recycled product quality may not match virgin material
- Recycled plastics cost more than simply making new material, so the financial driver for recycling is not there
Recycling alternatives
There are pros and cons to the various approaches being taken to address the plastic waste problem. One solution is to simply burn the plastics as they are an excellent fuel source and can be incinerated along with all manner of refuse. This does keep them from entering the environment, but plastics do not burn cleanly, and when one considers the carbon footprint of petroleum production and refining to make plastics, combined with plastic production and incineration, the net environmental cost is quite high.
Other plastic recycling options include mechanical recycling, dissolution, depolymerization and pyrolysis.
Mechanical recycling separates plastics into individual types, then remelts them to create new plastic products. Some plastics, like polyethylene terephthalate (PET) bottles, are relatively easy to sort and work well with this process, and the bulk of recycled plastics currently fall into this category. However, this method is limited to only certain plastics that remelt well and sort easily, and few plastics fall into this category.
Dissolution uses solvents to selectively melt specific plastics for reuse. This method is relatively new and only a few plants are starting to come into production using this process. The energy cost is comparatively low, but the process is only efficient if the incoming plastic stream is of one type and easily sorted. There is also some question as to whether the process might allow feedstock contaminants to pass into the final product, so the resulting product may not be allowed in more sensitive applications, like food packaging.
Depolymerization uses specific chemical processes, such as methanolysis or glycolysis, to break down the long chain plastic polymers into monomer chemical building blocks. This requires more heat and energy, but the process can handle a broader range of variation in the feedstock. But depolymerization still requires some level of plastic sorting to ensure the incoming feed is compatible with the process, so it has limitations.
Pyrolysis can handle a broad range of plastics and requires very little sorting at all. The incoming feed can be a mix of most any plastic, which is chopped into small pieces and subjected to very high pressure and temperature in a reactor. Under these conditions, the plastics break down into a range of oils, light ends, naphtha and waxes, which are ultimately refined and sold as chemical feedstocks or fuels. The resulting flammable gases are burned as fuel to help offset energy costs.
The pyrolysis process
There are several large chemical companies pursuing pyrolysis solutions, and most of them have patented their chemical processes. The process diagram in Figure 1 shows a generic pyrolysis process, with most of the major chemical steps identified. Each plant will undoubtedly have some variation as the processes are new and under continuous improvement, but the overall content should be similar.
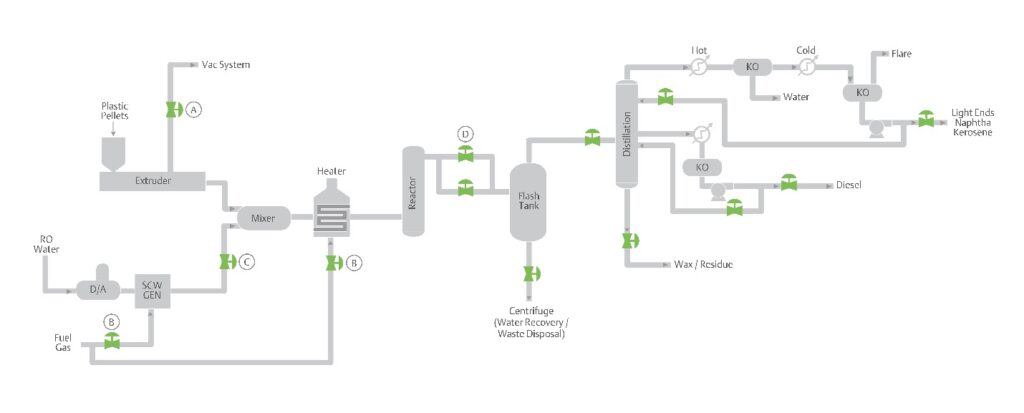
Figure 1. This process diagram illustrates the major chemical processes of a generic pyrolysis plant design
A pyrolysis plant can accept virtually all types of plastic, which can be a particular benefit when dealing with variable feedstocks. The incoming plastic does need to be separated from all non-plastic contaminants, but some level of infeed processing (not shown in Figure 1) may be required to remove paper and wash away rocks, grit, food contaminants and the like. The resulting plastic is usually ground up into smaller pieces and fed into the extruder.
Inside the extruder, the plastics are heated using electric heaters and mechanical heat from the extruder screws. The plastics melt and are combined into a homogenous mix. Some off gassing of chlorine-related gases may occur during this process.
The next step may vary by process, but at least one major pyrolysis process mixes the melted plastic with water above supercritical temperatures/pressures. This improves heat transfer of the resulting fluid and helps carry away a number of contaminants that may still be in the feed stream. The resulting water/plastic mix is passed through a heater and pushed through a reactor, which provides the required time, temperature and pressure to break the plastics down into a wide variety of hydrocarbon components.
The superheated, pressurized mix from the reactor then passes through a pressure letdown valve and enters a flash vessel. This is probably the most challenging part of the process due to the extensive off gassing, high pressure drop, high temperature and variable chemical makeup of the fluid.
Water and unreacted solids will leave the bottom of the flash vessel and be centrifuged to recover the water and dispose of the unreacted waste. The superheated hydrocarbons will pass into a distillation vessel, which will separate the hydrocarbon stream into diesel fuels, light ends/naphtha/kerosene and waxes. Water will also be split out and recovered for process use.
Control valve selection
Many of the valves in the pyrolysis process are similar to what is used in many petroleum refineries, with some notable differences. Specific valves shown in Figure 1 are discussed in the paragraphs below.
Valves associated with the extruder off-gas system (A on Figure 1) will not encounter very high pressure drops, but may encounter corrosive mixes of chlorine-related gases. Therefore, proper material selection is critical to ensure long-term performance, so end users should consult their automation vendor to help select the proper body and trim materials.
Valves controlling the natural gas feed to fired heaters (B on Figure 1) should be selected with higher tier positioners to provide tight control. Temperature control is particularly critical for the indirect fired heater, which must maintain a consistent exit temperature, despite variable feed flow and feedstock material variations. A single-seated globe valve (Figure 2) with a higher tier positioner, low emission packing, and possibly some noise attenuation trims will be a good choice.
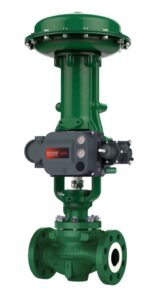
Figure 2. Control valves for natural gas/fuel gas service should include low emission packing and high diagnostic positioners, and they may require noise attenuation trims in some applications
The valve controlling supercritical water flow to the mix chamber (C on Figure 1) must be carefully sized and selected. Sizing valves for this application can be difficult since the standard sizing calculations may not apply. The trim and valve body must be designed for very high temperatures and pressures, and it may encounter very high pressure drops during start up conditions, which could cause cavitation issues (Figure 3). The internal components must be designed and chosen with care since the range of temperatures could create thermal expansion problems.
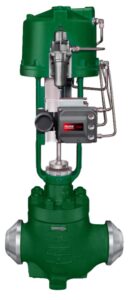
Figure 3. Supercritical water valves encounter very high pressure drops and temperatures, and must therefore be carefully designed to address thermal expansion, and cavitation issues during start up conditions
The most difficult application in the process will be the pressure letdown valves feeding the flash tank (D on Figure 1). These valves face an unforgiving process with high pressures and temperatures, extensive off-gassing, and a three-phase mixture of vapors, liquids and some unreacted solids, with the latter tending to plug ports. Very high pressure drops, velocities, erosion, and possibly chemical corrosion are likely. Due to the probability of valve damage in this application, many plants will likely have two valves in parallel, allowing them to service one while keeping the process in production.
The pressure letdown valve is at the heart of the process and must be chosen very carefully (Figure 4). The valve trim must be capable of handling extensive off gassing, liquids and some solids. Proper material selection will be paramount, since high velocity erosion, cavitation, and chemical attack will be encountered. Ultimately the valve will be damaged over time, so the valve must be designed with maintenance in mind.
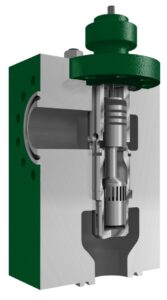
Figure 4. The most critical and difficult application of the process will be the pressure letdown valves that feed downstream flash tanks and distillation. The specialty valve design must handle three phase flow, elevated pressures and temperatures, cavitation, erosion, and chemical attacks
The remaining valves in the distillation section are similar to many refinery applications, with the main difference being the extensive mix of hydrocarbon constituents, which could pose material compatibility issues. Wax buildup and accumulation could be problematic in the bottom of the distillation column, so careful trim selection, as well as extensive heat trace of piping and valves, are necessary.
Final thoughts
The pyrolysis process design is still very much a work in progress, but several large plants are in construction or in the early stages of commissioning. Designs will probably change as production problems are encountered and better understood. In particular, the pressure letdown valves will likely require a number of iterations to find the right selection of trim design and materials which can withstand the process conditions and provide extended service life.
When faced with extremely difficult applications such as these, end users are wise to consult the valve design experts of their automation provider. Recent advances in additive manufacturing techniques have enabled new trim designs and specialty materials that in the past could not be economically produced. In this very competitive landscape, it is likely that the first company to achieve a viable and stable process will reap huge rewards, even as they address a difficult and burgeoning global problem.
Edited by Dorothy Lozowski
All Figures courtesy of Emerson
Authors
Heng Erjian is a control valve business development manager for Emerson’s Flow Controls products, concentrating on the chemical and power industries during his 13 years in this position. He graduated from Nanyang Technological University in Singapore with a Bachelor of Mechanical Engineering degree.
Kelly Chong Yi Ying is sales and application engineer for Emerson’s Flow Controls products, concentrating on the marine and chemical sectors during her five years in this position. She graduated from Curtin University with a Bachelor of Chemical Engineering degree.