Corrosion under insulation (CUI) remains a persistent challenge at chemical process industries facilities, but the issue is receiving renewed attention amid a host of technologies, materials and methodologies for detection and prevention of CUI
Corrosion of process equipment, piping and structural elements is an ongoing problem at chemical process industries (CPI) facilities because of its potential to contribute to catastrophic failures, safety concerns and increased cost and effort for maintenance. The corrosion subcategory known as corrosion under insulation (CUI) is a particularly difficult challenge for plants to address as industrial sites continue to seek efficiency gains and avoid heat loss by insulating process equipment. By its nature, CUI is hidden from view, and it can progress quickly under certain circumstances. The renewed attention on CUI has been highlighted by new coating technologies and detection methods, aimed specifically at the problem of CUI.
Corrosion knowledge base
Professor Homero Castaneda-Lopez, the director of the National Corrosion and Materials Reliability Center at Texas A&M University (College Station, Tex.; www.tamu.edu), works with companies on improving corrosion performance for their assets, including testing different materials in various environments and identifying which control actions would be most effective at increasing safety and reliability. “The ultimate goal is to avoid all catastrophic incidents,” Castaneda-Lopez says, “and when you have aging infrastructure and assets, it requires that we be proactive, rather than reactive, at preventing corrosion.” In part, that requires closing the current knowledge gaps and developing a deeper and more widespread understanding of corrosion,” he notes.
“While most people on industrial sites have a general awareness about corrosion’s potential impact, there remains a great need for improving the knowledge base on corrosion, not only for chemical engineers, but also for mechanical engineers and others,” says Castaneda-Lopez.
Castaneda-Lopez says the issue of corrosion under insulation (CUI) has been garnering significant focus recently, because it remains a large problem for which there have not generally been efficient solutions. “It’s a stubborn problem that is going to be worse in the future,” he says.
Steven Reinstadtler, infrastructure market manager at Covestro LLC (Pittsburgh, Penn.; www.covestro.com) and committee chair with the Association for Materials Protection and Performance (AMMP; Houston; www.ampp.org), has also seen a renewed focus on CUI. “In the past, any solutions for CUI were extremely limited and individual components-based,” he says, “Now, while CUI remains a significant problem, some solutions are available that do address the issue, although they tend to be complex and involve multiple components working in concert, and so therefore, can be somewhat expensive,” Reinstadtler comments.
Environmental performance of anticorrosion Coatings
Aside from CUI prevention, another prominent trend in industrial coatings is the pursuit of enhanced environmental performance of anticorrosion coatings, in part by lowering the level of volatile organic compounds (VOCs) in the coatings and also by using bio-based materials.
Covestro’s Reinstadtler explains: “over the past few years, substantial VOC reductions have been achieved for coatings that are designed for more aesthetic purposes, and that don’t place such a premium on durability, such as architectural and decorative paints. But the push for lower-VOC coatings had not extended to the same degree to industrial protective coatings until now, because the need for performance and durability was so high.”
Now, regulators at the state and federal levels are taking a tougher look at lowering VOC requirements for industrial coatings, and possibly de-listing solvents that are currently exempt from VOC limits. As a result, coatings manufacturers are investing a lot of development effort toward making formulations that will address anticipated lowering of VOC levels and elimination of some exempt solvents for industrial coatings. VOC and solvent discussions relative to industrial coatings are happening now with the California Air Resources Board and the South Coast Air Quality Management District, Reinstadtler says, and will extend to other regulatory bodies in the future.
An example is the recent development by Covestro of a new technology using polyaspartic resins and unique aliphatic hardeners for anti-corrosion topcoats. Designed to “future-proof” the product line by meeting anticipated future regulations on lower VOCs and the delisting of exempt solvents, the new coating contains less than 100 g/L VOCs and does not use any exempt solvents, Reinstadtler says, explaining that the technology is a two-component system using Desmophen NH polyaspartic resins reacted with Desmodur aliphatic hardeners to create a polyaspartic coating. The system is scheduled be discussed in full detail at the AMMP conference this month.
The effort to reduce VOCs without compromising on anticorrosion performance has also been taken up by BASF SE (Ludwigshafen, Germany; www.basf.de). Although solvent-borne systems are still prominent in many direct-to-metal (DTM) coating applications, water-based binders are increasing in popularity because of the lower VOC profile offered by waterborne systems, as well as their ability to combine the physical characteristics of a top-coat system and a primer in one layer, reducing time and cost of application. BASF says “coatings formulators have struggled to obtain the same levels of performance with waterborne DTM coatings,” so the company developed Acronal Pro 770, “a new acrylic high-performance binder with improved corrosion protection compared to other one-component binders at the same DFT.”
The “greening” of corrosion coatings extends to efforts to increase the bio-based content in coatings formulations as an alternative to petroleum-derived components. In that area, Covestro has developed Desmodur eco N, an aliphatic hardener containing 71% bio-based content. “It’s the first new aliphatic hardener in 30 years,” says Covestro’s Reinstadtler. While it was originally designed for the automotive sector, Desmodur eco N is now being evaluated for other sectors, he says.
The Desmodur eco N hardener is used with typical polyurethane resins. “It’s close to being a drop-in replacement for a traditional aliphatic hardener — there are similar properties in the final coating,” Reinstadtler says. Besides polyurethane clearcoats for the automotive sector, Covestro is testing the bio-based aliphatic hardener for other low-VOC applications, such as corrosion-resistant, light-stable topcoats for steel infrastructure, as well as roof and industrial concrete floor coatings.
Labor issues
Covestro’s Reinstadtler commented on a non-technology-related aspect to the corrosion protection field that has to do with personnel. “There’s a profound labor shortage of both skilled and unskilled labor surrounding the corrosion coatings field,” he says. And the labor shortage is connected to a drive for higher-durability coatings.
Although polyaspartic (an aliphatic polyurea) technology has been around for awhile, it is now playing an increasing role because of its potential ability to help save labor. Polyaspartic resins are similar to aliphatic polyurethanes, but they have an amine that reacts faster than existing resins, so coatings based on polyaspartics cure faster, Reinstadtler says. With this type of technology, less time is required between coats, and it can be applied thicker, so there are fewer coats required. Often, one coat can be eliminated while still fulfilling the coating-system thickness specification. This saves on labor needs. “Polyaspartics are one of the fastest-growing classes of topcoats right now,” he says.
Isolated and aggressive
CUI occurs when moisture mixes with contaminants in a “corrosion zone” between the interior of the insulation and the coating on the surface of the asset. “Moisture mixed with contaminants frequently enters this area through small gaps in the insulation system’s cladding,” explains Thomas Crenshaw, the downstream facilities subject matter expert at Sherwin-Williams’ (Cleveland, Ohio; www.sherwin-williams.com) protective and marine division. “The moisture and contaminants become trapped in the corrosion zone and face thermal cycling, eventually causing CUI,” he says.
CUI is a particularly vexing problem for plant personnel for several reasons, according to Crenshaw. When CUI occurs, it is typically in isolated locations and especially aggressive, so it may not be identified between inspection intervals, he explains (Figure 1). Also, engineers often fail to take into account that process equipment will experience upset conditions, which may include temperature spikes that exceed the applied coating’s exposure limits, causing the material to crack or blister. Planning ahead and specifying more robust materials to accommodate potential spikes is helpful, Crenshaw says.
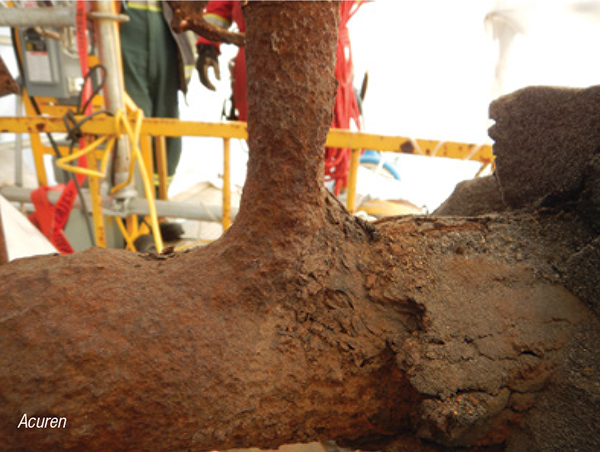
FIGURE 1. Corrosion under insulation (CUI) is a phenomenon that can be particularly aggressive when the presence of moisture is combined with contaminants at a steel surface, and so it can progress rapidly between asset inspection intervals
Heat-cycling and large temperature swings are important factors in CUI. The temperature swings don’t cause corrosion by themselves, but they cause coatings to crack and age rapidly, allowing corrosion to develop, Crenshaw says. “Shutdowns and turnarounds allow the process equipment to be at risk for significant corrosion, as condensation is likely to occur at lower temperatures, and that moisture will later boil on the steel surface when temperatures rise” (Figure 2). Steam-out cleaning and processes that normally experience temperature swings are other examples of situations that can lead to conditions that promote CUI.
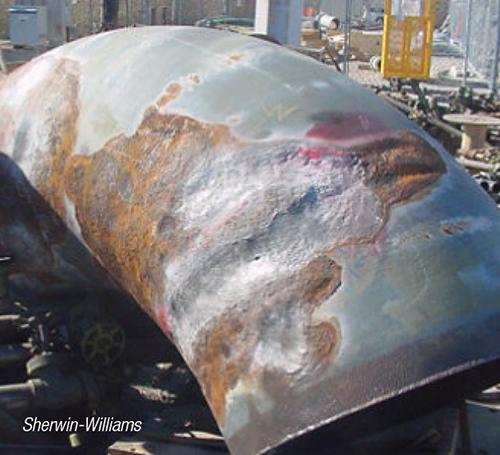
FIGURE 2. Heat-cycling is an important factor in causing CUI, because it can lead to condensation, which introduces moisture into the corrosion zone at the component surface
CUI-resistant coatings
Over the last decade, Sherwin-Williams has made numerous improvements to a silicone-based, inert multipolymeric matrix (IMM) coating aimed at preventing CUI on process equipment due to its resistance to thermal shock and cycling. The company’s Heat Flex 1200 coating is currently in its third generation, and most recently, the company added a curing additive to the formulation for improved mechanical protection. Sherwin-Williams says the Heat Flex 1200 IMM product met the most stringent pass criteria for oil-and-gas atmospheric systems and resisting stress corrosion cracking in accelerated CUI simulation testing with no cracking, flaking or rusting occurring before 265°C (509°F).
Another recent advancement in the company’s silicone-based anticorrosion coating line is the addition of micaceous iron oxide (MIO) flakes to the Heat Flex 1200 coating.
“The MIO flakes form a layered barrier that blocks moisture, oxygen and other elements from penetrating the coating and also deflects ultraviolet (UV) rays to minimize coating degradation from sunlight,” explains Crenshaw. “Considering the plate-like structure of the MIO pigment, it creates a very difficult path for water to permeate the coating and reach the substrate.”
Sherwin-Williams has also recently completed testing on the inclusion of MIO flakes in other coatings, some of which have shown promise for CUI resistance. Among them is a high-temperature epoxy phenolic — a two-component, amine-cured lining with excellent resistance to chemicals and hydrocarbons that showed promise in the laboratory as a CUI mitigator, achieving a maximum temperature rating of 205°C, the company says. Also, a MIO-filled high-temperature epoxy based on flake-filled advanced alkylated amide technology resisted CUI in temperatures ranging from cryogenic levels to 200°C (392°F).
“While MIO-enhanced coatings haven’t been historically viewed as a solution for CUI in various operations, successful laboratory tests for the coatings noted above give the industry hope for better CUI mitigation tools when assets require external insulation systems,” Crenshaw says.
Another CUI coating option focused on resisting temperature cycling comes from PPG Industries Inc. (Pittsburgh, Pa.; www.ppg.com). Last year, PPG launched its HI-TEMP 1027HD coating into the North American market. The coating is described as a next-generation, ambient-cure coating engineered for challenging CUI conditions. PPG says the product is “a high-build coating that offers dry-film thickness of 10 to 12 mils in a one-coat application.” The HI-TEMP 1027HD coating provides “excellent protection” against corrosion on pipes, vessels and construction parts when plants are in operation, the company says. The highly durable coating is formulated to withstand severe temperature cycles ranging from –320°F (–196°C) to 1,000°F (540°C), and resists dry exposure with intermittent temperature peaks of up to 1,200°F (650°C). “Because of its hardness and resistance to thermal shock and cycling, PPG HI-TEMP 1027HD coating more effectively protects these critical assets against corrosion. This can extend maintenance intervals and minimize the risk of unexpected shutdowns,” the company says.
HI-TEMP 1027HD coating also protects coated pipes, parts and assemblies in changing ambient temperature conditions. This is critical during shipping, because these components are commonly transported between continents and exposed to months of rain, snow, ultraviolet (UV) light and other environmental hazards, PPG notes.
Coatings as insulation
A different approach addressing CUI is to eliminate the “corrosion zone” between an asset’s coating and the interior of traditional insulations, such as mineral wool. A new coating now undergoing trials at Sherwin-Williams has the potential to eliminate CUI altogether in many applications by acting as its own insulation, thus alleviating the need for traditional insulation. The coating creates a monolithic barrier that bonds to the surface of the asset, leaving no gaps or corrosion zone for moisture to get close to the substrate.
The newly developed insulative coating allows for a maximum temperature exposure of 177°C (350°F) with excursions to 205°C (400°F) permitted, plus a higher temperature limit anticipated in the future, according to Sherwin-Williams’ Crenshaw. “This higher thermal performance rating means the coating can be used on a wide range of heated assets, enabling owners to forgo traditional insulation systems and eliminate the issue of CUI in more applications,” he says. Further, the coating’s thermal performance is retained over time, in contrast to traditional insulation systems, which lose performance when they become laden with moisture, he adds.
Sherwin-Williams has based the new coating on existing products designed for CUI, but the coating is applied much thicker than any other now on the market, Crenshaw remarks — up to 10 mm dry-film thickness in one or two coats, plus a topcoat to seal and smooth the finish. “At that thickness, the coating retains heat similarly to traditional insulation, as proven in forward-looking infrared (FLIR) imaging taken on a ground storage tank being tested with the coating,” Crenshaw says (Figure 3).
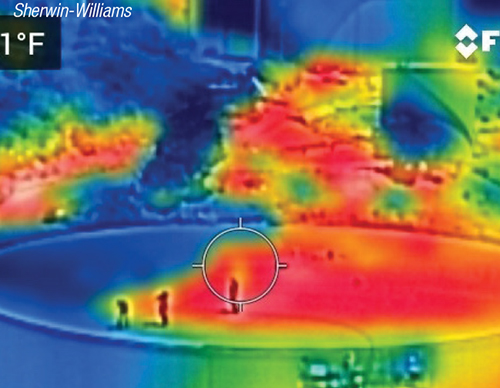
FIGURE 3. An industrial anticorrosion coating under development by Sherwin-Williams serves as its own insulation. Infrared imaging, like the one shown here, illustrates the heat-retention ability of the coating where it is applied (blue color) compared to where it is not (red-orange color)
Alloying
In a marked departure from other anticorrosion approaches using organic coatings to prevent moisture from contacting a component surface, the company EonCoat LLC (Fuquay-Varina, N.C.; www.eoncoat.com) has taken a fundamentally different approach to corrosion prevention that involves the formation of an inert passivated layer at the carbon-steel surface. Rather than applying a polymeric coating, the EonCoat system chemically bonds with iron at the component’s surface to create a protective layer of iron-magnesium-phosphate compounds that are inert, explains EonCoat founder Tony Collins.
On top of this protective alloy layer, EonCoat creates a layer of ceramic material made of phosphates and silicates. “If the alloy layer gets damaged, this ceramic will leach a little phosphate onto the steel and fix the alloy layer,” Collins says, adding that the healing mechanism lasts for the life of the asset.
After first introducing a coating for atmospheric corrosion a decade ago, EonCoat more recently introduced a variation of the coating that is specifically designed for CUI. EonCoat CUI/High-Temperature Coating is similar in principle to the original product, but contains additives to resist thermal shock, Collins points out.
Use of the EonCoat CUI coating product has expanded recently, spurred by positive results from field testing by Chevron Corp. (San Ramon, Calif.; www.chevron.com). Chevron tested the EonCoat CUI coating at its Pascagoula, Miss. petroleum refinery and found that the EonCoat system prevented CUI on surfaces that had been intentionally scratched and mechanically damaged after 335 hours of exposure to salt fog.
Collins says the EonCoat system also offers other advantages as well, including an application process that is not affected by high humidity and requires minimal surface preparation, and no concerns about VOCs and hazardous air pollutants.
CUI detection advancements
Another dimension in addressing the problem of CUI at industrial sites is its detection on in-service equipment, piping and structural elements at a plant site. Technological improvements in the methods and instruments that detect the presence of CUI are also making their way to plant sites.
Brian Anderson, director of advanced technologies at the materials testing company Acuren Group Inc. (Webster, Tex.; www.acuren.com), says companies are starting to accept the need to invest in comprehensive CUI programs to avoid costly failures. Among the keys to such a program is ensuring physical access to the assets on the part of technicians. Acuren has pioneered innovative methods to allow roped access by technicians to inspect and test process equipment, pipes, storage tanks and structures.
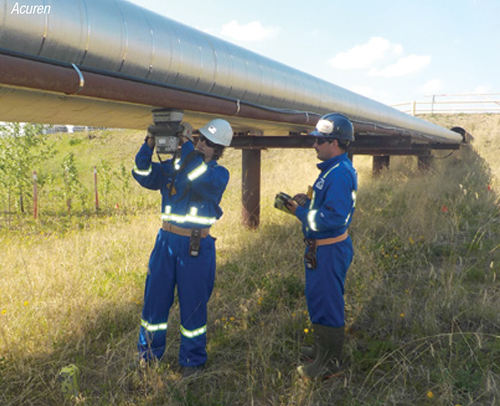
FIGURE 4. Technicians use non-destructive testing to detect the presence of moisture, an indication of where CUI may be a problem
Once the equipment is accessible, instruments for non-destructive testing (NDT), such as real-time radiography (RTR) and moisture detection imaging, become critical. “For CUI testing, RTR is really taking off at the moment,” Anderson says. In RTR, X-ray radiation is used to generate digital images of the outer profile of equipment that is covered by insulation, without the need to remove any insulation. For example, RTR can detect changes to the outer diameter of a pipe that might indicate corrosion.
Acuren is currently developing new versions of its radiography instruments with enhanced capabilities for measuring insulation surfaces that are aimed at increasing the speed and effectiveness of testing while reducing costs, Anderson says.
Since the presence of water is a prerequisite for CUI, NDT methods that can detect moisture, such as Compton backscatter, can be used. As X-rays hit an object, some are absorbed, producing a transmission X-ray image, and others are scattered (Compton scattering). Backscatter images are formed from the X-rays that are scattered back toward the X-ray source. Compton scattering is material-dependent, with the lower-atomic-number materials scattering more strongly than the higher-numbered ones, Hydrogen, being a low atomic number, returns higher Compton backscatter, so areas that have higher levels of hydrogen (from water) can indicate the presence of moisture and can reveal locations that might be susceptible to CUI, Anderson says.
As part of its comprehensive CUI program, Acuren has also developed a proprietary method for moisture detection using the Compton backscatter method, known as Moisture Detection Imaging (MDI). Acuren MDI does not require any insulation removal and can scan large areas rapidly to confirm the presence of moisture without being affected by temperature conditions.
Remotely operated aerial drones are also becoming important tools for screening for and assessing CUI at industrial sites. Jennifer Dowdle, materials engineer and senior inspector at Acuren, says that while drones will not be suitable for all situations, they have been used by Acuren to carry out initial assessments of assets for CUI. In those cases, the drones were outfitted with infrared thermography sensors and ultrasonic probes for performing follow-up thickness measurements, she says.
Digitalization increases the need for COatings that protect Electronics
Digital transformation initiatives are increasing the need for corrosion resistance of electronic components. “Connected devices require more reliability when deployed in harsh environments,” says Ryan Moore, marketing manager for HZO Inc. (Morrisville, N.C.; www.hzo.com). Moore’s company is developing a range of nano-engineered coatings for protecting electronic components from corrosion. These coatings allow compact electronics to be coated with thinner layers.
“Conventional coatings may provide reliability, but they must be applied in thick layers to allow a product to be truly dependable. So, the sheer thinness of the coatings are an important performance characteristic,” Moore says. Nanoscale engineering also allows for more customization because more materials can be used, he adds.
HZO is developing new coating materials, as well as application processes and equipment for coating components, such as printed circuit boards for computers. Last year, the company received ISO 9001 certification for its facility in Vietnam.
Dow Inc. (Midland, Mich.; www.dow.com) recently introduced Dowsil CC-2588, a tough, abrasion-resistant conformal coating designed to protect printed circuit boards from humidity and corrosion. The silicone-based coating has “extremely low” VOC content and cures at room temperature. “While traditional silicones offer good resistance to humidity and chemicals, they may lack abrasion resistance because of their rubbery nature,” Dow says. “However, Dow’s new DOWSIL material, once cured, is comparable to other resin conformal coatings in terms of toughness.
Scott Jenkins