This article examines the measures — both global and local — that chemical processors are taking to instill sustainability into everyday operations
Although discussions about sustainability in the chemical process industries (CPI) are usually geared toward making processes more environmentally sound, there are a number of aspects that encompass longterm sustainability for processors. These may include safety, personnel, data management and activism in the community. This article highlights some recent sustainability endeavors from across the CPI.
Making use of CO2
Reducing carbon dioxide (CO2) emissions has become a cornerstone of sustainability plans, but concerns about CO2 are not a recent development. With origins dating back 30 years, Covestro AG’s (Leverkusen, Germany; www.covestro.com) Dream Production project has been investigating the feasibility of utilizing carbon from CO2 gas as a chemical building block. A major challenge is CO2’s inert, stable nature, which makes it unlikely to react with other substances. In cooperation with the CAT Catalytic Center in Aachen, Germany, the Dream Production team discovered a zinc-based catalyst that enables efficient reactions between high-energy epoxides and CO2without any cumbersome side reactions. The result is the incorporation of CO2 into polyols — important precursor chemicals that are typically petroleum-based. This catalysis breakthrough led the company to invest €15 million in a manufacturing plant in Dormagen, Germany that uses CO2 to produce a range of polyols for flexible foams. Operations at the plant, which has a production capacity of 5,000 metric tons per year (m.t./yr), commenced at a grand opening ceremony on June 17, 2016. The CO2 is sourced from a neighboring ammonia plant, effectively taking the CO2 that would be released as a greenhouse gas and putting it back into the production process. The site-sourced CO2 also offsets the portion of petroleum-based raw materials required.
Covestro is confident in the scalability of the process, and also plans to license the technology to other polyol producers. While the Dormagen plant is currently focused on foam production, other types of novel plastics could also be manufactured. Currently, researchers are developing a similar continuous process to manufacture CO2-based polyether carbonate polyurethanes, which are precursors for elastomers. Individual batches of the material have been produced at laboratory scale. The company is particularly excited about the future opportunities of the Dream Production process, says Covestro chief sustainability officer Richard Northcote. “It opens a whole new arena of carbon chemistry. If we can use it in mattress foam, where else can we use it?”
One of the flagship projects of Saudi Basic Industries Corp. (SABIC; Riyadh, Saudi Arabia; www.sabic.com) is the CO2 utilization and purification plant at the United site in Jubail, Saudi Arabia, which was completed in 2015 (Figure 1). The facility, said to be the world’s largest CO2 purification plant, captures CO2 byproduct from the concentrated vent streams of an ethylene glycol (EG) production unit. The captured CO2 is compressed and purified, and then transported through a 25-km pipeline grid to affiliate sites, where the CO2 serves as a feedstock. The United plant uses a patented process to capture and purify up to 500,000 m.t./yr of CO2 from the EG process. The plant has been running since late 2015, and SABIC anticipates reaching full operating rates during 2016. While the purified CO2 is currently supplied to affiliate processors making urea, methanol and 2-ethylhexanol, the company says that the CO2 is of high enough purity for use in the food and medical industries. Along with CO2, the purification process can be designed to produce a stream of purified water suitable for boiler feedwater.
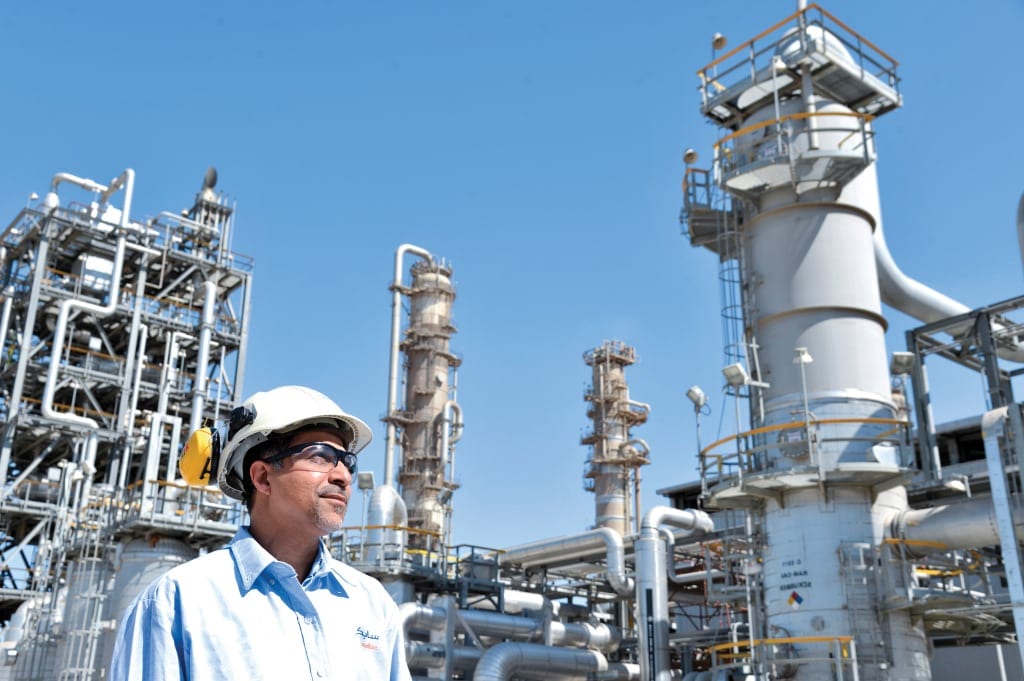
Figure 1. SABIC’s United CO2 purification plant captures carbon dioxide from an ethylene glycol process and distributes it as a raw material to other production units
Corporate integration
To view sustainability from an overarching, company-wide standpoint, Eastman Chemical Co. (Kingsport, Tenn.; www.eastman.com) takes a holistic approach. “We set sustainability goals and targets at the corporate level, and they are driven across the company through the leadership of our Sustainability Council,” explains Eastman director of sustainability Cathy Combs. Consisting of five senior executives representing a cross-section of the company, the Sustainability Council was established in 2010. “Our sustainability strategy continues to evolve, and we have streamlined our goals into a scorecard of aspiration goals intended to drive continuous improvement,” says Combs.
To address the sustainability performance of the company’s product portfolio and to create a corporate-wide appraisal system, Clariant (Muttenz, Switzerland; www.clariant.com) developed the Portfolio Value Program (PVP) beginning in 2013. The program contains 36 sustainability criteria and focuses on assessment and continuous improvements of the product portfolio. Taking the PVP a step further, Clariant has introduced the EcoTain concept, which the company applies to products and solutions that are deemed to have best-in-class attributes and sustainability advantages for customers. “Our approach not only considers the footprint of our products,” explains Joachim Krueger, senior vice president for corporate sustainability and regulatory affairs, “but also the benefits as well.” Based on the PVP screening, EcoTain products must demonstrate benefits in multiple lifecycle phases and not pose adverse effects to the environment or public health. Currently, around 120 products are classified as EcoTain labeled. Products that fall short in the portfolio screening are placed on an improvement roadmap and opportunities for enhancement, substitution or even discontinuation are evaluated, says Krueger. “I am convinced,” he added, “that when you are really committed to becoming a sustainable company, you cannot exclude the option of eventually discontinuing a specific product or process because of its sustainability profile.” In these cases, using the PVP, the company sees an opportunity to develop a more sustainable alternative product. “One thing is clear,” notes Krueger, “sustainability fuels innovation.”
Industry collaboration
Collaboration among the many parties involved in the CPI value chain is crucial for ensuring sustainability. Processors, vendors, suppliers and customers must all work in tandem to bring about change. Collaboration among competitive companies on large-scale projects, such as the ongoing Solar Impulse aircraft project, further represents an underlying commitment to sustainability. “What a fantastic example of chemistry overcoming issues,” said Covestro’s Richard Northcote of Solar Impulse. Covestro has teamed up with industry partners like Solvay S.A. (Brussels, Belgium; www.solvay.com) to provide advanced materials for Solar Impulse’s lightweight solar-powered aircraft. Northcote emphasizes the importance of industrial collaboration to sustainability, noting: “The more we can work together as an industry, the more we can generate the huge impact society expects. Solar Impulse is a great example of what we can do if we work together. I have every confidence in our industry being a huge part of the solution.”
Another example of a cross-industry collaboration tackling a challenging issue is Clariant’s work with the SPOTS (Sustainable Palm Oil and Traceability with Sabah Small Producers) initiative, which brings Clariant together with agribusiness company Wilmar International Ltd., cosmetics giant L’Oreal and Malaysian social enterprise Wild Asia. The aim of the SPOTS collaboration is to encourage certification and supply-chain traceability among palm-oil producers in the Sabah region of Malaysia, while also increasing productivity by 20% by 2020. Palm oil, Clariant’s most widely used renewable raw material, is a topic of public debate due to the adverse social and environmental impacts of its cultivation from palm tree fruits (Figure 2). Along with ensuring that Clariant’s palm-oil supply chain is certified by the Roundtable on Sustainable Palm Oil (RSPO), the project will also benefit small-scale palm-oil producers by giving them access to global markets and introducing more sustainable cultivation practices. The use of sustainably sourced raw materials is one of the criteria required for a product to meet Clariant’s EcoTain label. In July 2014, Clariant’s Gendorf, Germany production site was successfully certified according to the RSPO Mass Balance supply-chain standard. The company plans to have all relevant production sites RSPO certified by December 2016.
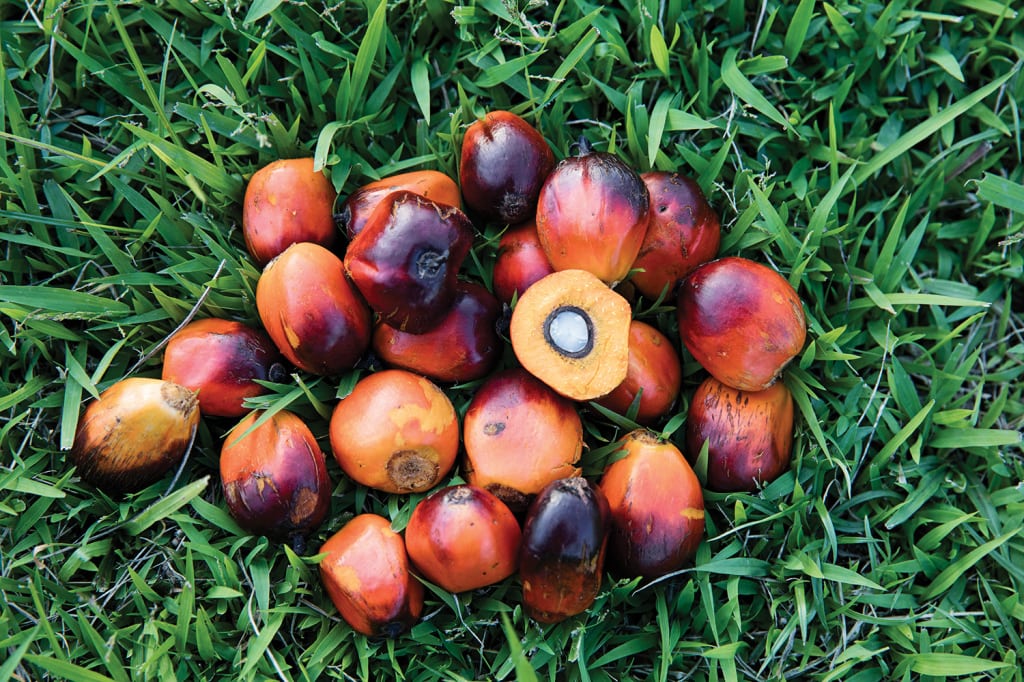
Figure 2. Palm oil is a major raw material in the specialty-chemical supply chain, and global efforts are underway to encourage its sustainble cultivation
Workforce sustainability
On a smaller scale, organizations are also recognizing the importance of individuals to sustainability goals, particularly in the areas of safety and workplace development. “Companies should be focused on people as a core component of sustainability,” says Suresh Sundaram, senior vice president of product and market strategy at Aspen Technology (Bedford, Mass.; www.aspentech.com). “Over the next few years, the industry is expected to see a turnover of the workforce with a newer generation of engineers, as the more seasoned employees retire.” The key to longterm workforce sustainability, explains Sundaram, is balancing operational strategy with market demand and reliance on employees. “Companies need to ensure that their strategies include investment in cutting-edge technologies, brain power and skills to give their businesses a clear advantage in a turbulent marketplace,” Sundaram continues.
BASF SE (Ludwigshafen, Germany; www.basf.com) is looking to the next generation of engineers to help instill sustainability into the workforce through its investment in the BASF Sustainable Living Laboratory at Louisiana State University (LSU; Baton Rouge, La.; www.lsu.edu). In May, BASF selected the lab’s first researcher-in-residence, Kevin McPeak, assistant professor in LSU’s chemical engineering department, who will lead a research group in developing a visible-light-powered water-disinfection system. “The lab advances science and engineering education in the region while engaging creative minds to innovate sustainable solutions,” says BASF. The project is part of BASF’s ongoing workforce-development activities in the U.S. Gulf Coast region.
McPeak’s work at the Sustainable Living Laboratory involves visible-light-driven advanced oxidation processes (AOPs) for environmental remediation. “Ultimately, he will develop a visible-light-driven water disinfection system using plasmonic-assisted-photo-Fenton catalysis,” explains BASF. These AOPs are set apart from other solar-driven water-purification technologies that rely on ultraviolet light (representing just 5% of the spectrum) because they will utilize the much larger visible range of sunlight (over 40%). The technology will provide a low-cost, efficient method for photo-inactivation of waterborne pathogens, says BASF.
Sustainability in all stages
Many companies cite innovation as a core value with regard to both economics and sustainability. In May, SABIC inaugurated a research center in Geleen, the Netherlands that is focused on sustainability projects for the architectural and mass-transportation sectors, including weight reduction, energy efficiency and the integration of photovoltaic panels. For all new initiatives at the company, a sustainability assessment is conducted in the early stages and remains ongoing throughout the development phase (Figure 3). “The entire lifecycle is thoroughly considered and carefully examined. Passing a quantitative threshold is a prerequisite in order to proceed,” explains a SABIC representative.
Aspen’s Suresh Sundaram reiterates the importance of innovation and technology development over the lifetime of assets: “For an asset to remain viable over the term of its useful lifespan, it must be continually improved over time.” He suggests that data management is a crucial pillar for sustainability, since it can introduce significant efficiencies into operational decision-making, requiring fewer resources and less time to complete tasks. With proper data management and analysis, he says, “Sustainability is enhanced through more efficient use of energy and less raw-material waste, which overall improves quality.”
Evaluating sustainability through the lens of data management and process development means that some degree of standardization is necessary. In May, under a work item within ASTM International, the National Institute of Standards and Technology (NIST; Gaithersburg, Md.; www.nist.gov) announced the creation of a new international standard for characterizing the environmental aspects of manufacturing processes. ASTM E3012-16 provides guidance to help manufacturers consider their processes one by one, capturing the environmental impacts and identifying opportunities to be more sustainable. “While previous standards are a useful first step and help in developing a management approach to sustainability, they fall short of providing specific guidance for manufacturers to really dive deeply into their processes and find opportunities for improvement at that level,” explains K.C. Morris, leader of the Information Modeling and Testing Group in NIST’s engineering laboratory. The standard, which was co-developed by manufacturers, breaks processes into unit manufacturing process models and promotes development that can link manufacturing information and analytics for calculating desired environmental performance measures. “The standard format defined in ASTM E3012-16 provides a basis for ensuring that a consistent set of details are covered and that they are covered consistently. This consistency will allow for better comparison, more reuse, and, in the end, more reliable results,” says Morris.
For the CPI, ASTM E3012-16 will help to provide value in the form of facilitating communication among stakeholders and expediting decision-making processes. NIST believes the standard may be of particular interest to software providers in the CPI. Morris emphasizes that the standard’s purpose is not to dictate sustainability goals, but rather to highlight the need for such goals to be defined specifically for an individual process. “By establishing that rigor, one should see opportunities for improvement and have a basis for understanding the implication of using a particular process in the future.”
It is clear that constant innovation and evaluation are crucial to ensure sustainability in the CPI, whether with regard to environmental and social concerns, resource efficiency, business practices or safety. Eastman’s Cathy Combs sums it up thusly: “The bottom line is that sustainability is a continuous journey, and we are constantly re-evaluating our current business practices to determine how we can improve.” ■