Higher-volume production of battery-powered vehicles is driving the development of high-performance polymers with improved properties to meet the needs of electric propulsion
The market for battery-powered electric vehicles (BEVs) has grown rapidly over the past five years. According to a recent analysis by market research firm IDtechEX (Cambridge, U.K.; www.idtechex.com), global sales of BEVs in 2020 were 5.5 times larger than in 2015, and BEV sales remained strong in 2020, despite the pandemic. As sales continue to increase, BEV technology is advancing in parallel, with battery capacity and energy density growing while vehicles become more connected and more autonomous.
Expansion of electric vehicles and vehicle-battery manufacturing has driven higher demand for high-performance polymers and polymer composites that exhibit specific properties required for safe and effective operation. The American Chemistry Council (ACC; Washington, D.C.; www.americanchemistry.com) states that hybridization and electrification will increase demands for efficiency, battery longevity, weight and space savings, as well as safety enhancements. Among the key properties for plastics used in BEV applications are high dielectric strength, high strength-to-weight ratio, flame retardance, impact resistance and others. Chemical manufacturers are continuing to develop new polymer grades, new additives and processing methods to meet the requirements of electric vehicles.
E-mobility requirements
Electromobility (e-mobility; referring to the use of technologies that allow electric propulsion of vehicles) has introduced new demands on the polymers used to make vehicle components. “There is a new set of requirements for materials in e-mobility,” says Brian Vargo, BASF E&E & eMobility segment manager at BASF Performance Materials (Wyandotte, Mich.; www.basf.com), “including electrical conductance, electromagnetic interference [EMI] shielding, flame retardance, dielectric strength (ability of insulating materials to withstand high electric fields without losing insulating properties) and others, and this creates opportunities for plastics to be introduced into EVs [electric vehicles].”
Dirk Heinrich, vice president of automotive and e-mobility at Evonik High Performance Polymers GmbH (Darmstadt, Germany; www.evonik.com) agrees that EVs have been a big driver for performance plastics because of their unique needs, including handling new types of fluids, improved electric isolation, specific coloring and more. “There are many small and sometimes subtle differences between EVs and conventional automobiles that lead to more plastics being required for EVs. One small example of this is that the fluid cooling lines for BEVs need to have larger diameters and wall thicknesses, as well as be longer, than those in conventional engines.” The sum of many similar examples at higher sales volumes leads to marked increases in plastics demand.
Darpan Parikh, a global product management leader in SABIC’s (Al-Jubail, Saudi Arabia; www.sabic.com) specialties business, summarizes by saying “EV batteries bring additional safety requirements for chassis and structural members, and the need for lightweighting for long-range drive capability without compromising on crash performance.”
At the same time, both BEVs and internal combustion engine (ICE) automobiles are adding a range of driver-assistance technologies, such as lane-centering, automatic braking and autonomous driving, that require specialized sensors, connectors and camera, adding new potential applications for performance polymers. Further, compounds and materials that address issues of noise, vibration and harshness (NVH) in the cars’ interior are important.
A significant and ongoing transition that has been occurring in recent years is the shift to designing EVs from scratch, rather than trying to introduce electric-propulsion components into vehicles that were originally designed as ICE vehicles, explains Chris Korson, chassis and structural market segment manager at BASF Performance Materials. “The initial generations of commercial EVs were just trying to put batteries into the existing vehicle bodies. Newer EVs have changing architectures that are designed to be battery-powered from the beginning.”
This design flexibility has led to new opportunities for polymer composites, including glass-reinforced polyurethanes as lighter weight replacements for metal parts. “Electric vehicle designs actually use more straight parts in their architecture,” says BASF’s Vargo, “which lend themselves to the use of polymer composites, such as glass-reinforced polyurethanes.”
The fundamental shift from propulsion by fuel combustion to propulsion by battery has also placed an emphasis on balancing cost and performance, and has highlighted the importance of plastic materials (Figure 1). Dhanendra Nagwanshi, global automotive leader, EV Batteries & Electrical segment, SABIC’s Petrochemicals business explains: “The battery pack is the most expensive assembly ever fitted to a vehicle. At the same time, mass [of the car] is an important variable — more mass means more energy required. All of a sudden, you need more battery storage, bigger brakes and so on.”
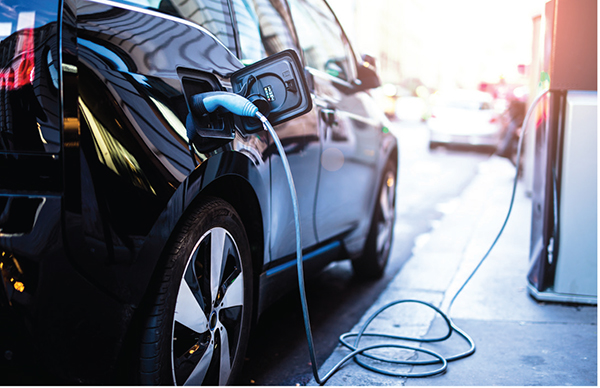
FIGURE 1. The shift from propulsion by liquid fuels to propulsion by battery has highlighted the importance of plastic materials with specific properties
“Despite the industry’s best efforts,” Nagwanshi says, “the addition of new technology and content continues to increase the overall curb weight of vehicles. The good thing about thermoplastic materials is their powerful combination of structural strength and low density. When you can remove mass and weight by, for example, replacing aluminum in battery packs with plastic, you can theoretically reach a point where battery cells can be removed because you no longer need as much energy for the same amount of range.”
In addition, Nagwanshi points out, thermoplastics can contribute to additional cost savings by eliminating the need for adhesives and fasteners, and for die casting, welding and other processes.
Generally, the polymer types that are used for automotive applications have been known for quite awhile, says Bert Havenith, market intelligence and sustainability director at DSM N.V. (Geleen, the Netherlands; www.dsm.com). “But there has been significant innovation in ways to functionalize the materials through compounding processes so that they are able to exhibit improved properties for a wide variety of parameters. DSM, among others, has been working on improving specific properties so the polymers can be used in new applications,” Havenith explains.
In an example of the increased demand for compounding of engineered plastics, Celanese Corp. (Irving, Tex.; www.celanese.com), announced a three-year plan to expand engineered materials compounding capacities at the company’s Asia facilities, including the locations of Nanjing, China; Suzhou, China; and Silvassa, India. The initiative will add approximately 52,000 tons of compounding and long-fiber thermoplastics (LFT) capacity at the company’s Nanjing chemical complex by the second half of 2023, as well as nylon compounding capacity at the Suzhou facility in 2022.
Glass-reinforced plastics
For making metal-replacement structural components in BEVs, where strength and stiffness at light weights is a premium, glass fibers are among the most common materials found in plastics. Significant focus has been leveled at processing glass-reinforced plastics, with the automobile market a major emphasis. BASF’s Korson points out the impact of one kind of processing technique, known as pultrusion, on EVs. “New EV architectures lend themselves to pultrusion-made parts,” he says, “and BASF has done a lot of work on pultrusion processing for composite materials, and have pushed pultrusion to achieve higher throughputs.”
Pultrusion is a processing technique in which glass fibers are pulled through a bath of polymer resin.
Earlier this year, BASF introduced serial production of glass-fiber polyurethane parts made in a pultrusion process. “There are lots of opportunities in the future for pultrusion materials in EVs,” Korson says. Another important factor in the adoption of pultrusion in the automotive market is the ability to model pultruded components in computer simulation to accurately predict the behavior in the full vehicle system. This is important for original equipment manufacturers (OEMs) and Tier 1 suppliers to design pultruded parts early in the vehicle development. Engineers are also working on ways to modify the glass fibers before they are introduced into the resin bath for different properties based on the applications needs.
Evonik recently introduced a number of products that will be used in the BEV market, including a new polyamide-12 polymer of the group’s Vestamid L grades, a glass-reinforced, electrically conductive PA12 molding compound that was developed in particular for the injection molding of connecting elements for fuel line systems (such as quick connectors). The electrical conductivity of the new Vestamid L changes only slightly on contact with fuels, even if they contain alcohol. This is of great importance for use in fuel-conducting systems, Evonik says.
Lightweighting
Automotive engineers have long known the relationship between lowering vehicle weight and raising fuel economy. A rule of thumb in the auto industry has been that for a 10% reduction in weight, the fuel efficiency of the vehicle improves by 6–8%. In BEVs, vehicle lightweighting allows longer ranges for a given battery size or achieving the same range with a smaller (and therefore less costly) battery.
“Lightweighting by replacing metal parts with plastics is a priority across the board for vehicles, but most of the ‘low-hanging fruit’ in this area has been realized already,” says Mark Jablonka, application technology leader for transportation at Dow Packaging and Specialty Plastics (Lake Jackson, Tex.; www.dow.com). Among the implications for this is that BEV makers are looking at every existing component for ways to cut weight. “The use of TPO [thermoplastic olefin; polypropylene (PP)-based composites containing PP, elastomers and reinforcements] in automobiles has expanded greatly over the past 25 years, but further expansion into new applications, including those in BEVs, has required more innovation,” Jablonka remarks.
Of the 25 products in Dow’s Engage portfolio of TPO impact modifiers, Engage 11000 is the newest. Dow recently introduced the 11000 series of its Engage polymer product portfolio as a way to expand the usage space for PP and TPO in automotive applications. Engage is an ethylene-octene copolymer produced using Dow’s single-site catalyst technology that is blended with PP and reinforcement materials. The concept behind the Engage 11000 series development was to arrange the co-monomers on the polymer chain in a specialized way to decrease the glass-transition temperature of the polymer, Jablonka explains. “The objective is to move the glass transition temperature lower to improve low temperature toughness while moving the melting temperature outside the normal operating range of the material to reduce thermal expansion,” he says.
PP has a relatively large coefficient of linear thermal expansion (CLTE), so to be used for automotive parts with acceptable design appeal, such as body panels, it needs to be modified to minimize CLTE so that the small gaps between the panels, can be small, for example. Lower CLTE also avoids fatigue issues and cracking when TPOs are welded to other lower CLTE materials.
Another advantage of the Engage 11000 series is the superior melt flow properties it enables during processing due to its high impact efficiency, Jablonka says, which allows more complex geometries in the components to be made from it. The material has been launched commercially and is currently being incorporated into BEV and ICE vehicles. “Expanding the usage space of TPOs for lightweighting means there will be continued demand growth for plastics in vehicles,” Jablonka says.
According to Dow’s Jablonka, among the goals is more efficient impact modifiers with resins that flow well for processing, and have low-temperature toughness without embrittlement. Other plastics have potentially poor melt flow, but TPO can be used for more applications. “There’s going to be continued growth in plastics due to lightweighting expanding usage space of the PP and TPO,” Jablonka says.
Safety and flame retardance
The growing electrification of vehicles has made vehicle safety a particular concern, especially with the potential for battery fires and thermal runaway, many experts agree (Figure 2). “Vehicle safety can be particularly important when you look at the need to protect the battery system during a crash, including side impacts,” SABIC’s Parikh says.
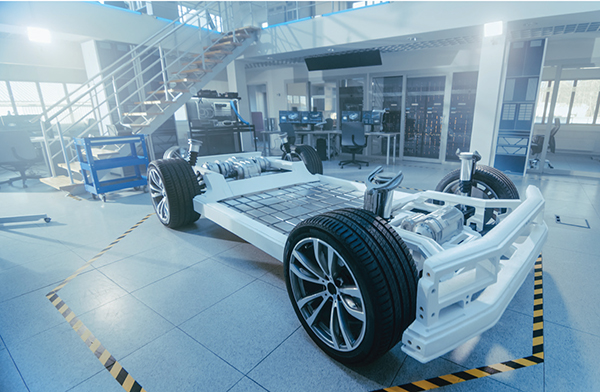
FIGURE 2. The possibility of battery fires has made flame retardance a critical property for vehicle safety in EVs
“The possibility of battery fires has pushed plastics makers to view flame retardance as a critical feature for EV components,” says Sandra Reemers, vice president of R&D at Evonik High Performance Polymers.
BASF’s Korson adds, “Many of the applications for performance plastics appear in the batteries, where thermal runaway protection is key.”
Thermal management of the battery and improved flame-retardant properties are partly related to higher voltages observed in EVs. Bert Havenith, from DSM, says, the voltages experienced in modern electric vehicles are orders of magnitude higher than those seen in conventional vehicles, so there is a huge need for improved electrical properties, such as higher dielectric strength, higher comparative tracking index (CTI), a measure of the amount of voltage an insulator can withstand with 50 drops of water without tracking (electrical breakdown) values, as well as better flame-retardant properties.
SABIC’s Nagwanshi says “We have developed and tailored specific resins from our polymer portfolio that we have modeled using computer-aided engineering (CAE) tools to ensure they comply with safety requirements and regulations, whether these apply to a crash scenario or some sort of system failure leading to a fire in the battery pack.”
China’s new GB 38031-2020 standard requires a battery cell that has caught fire to delay propagating to other cells or battery modules for up to five minutes so occupants have time to exit the vehicle, Nagwanshi says, and “SABIC’s polymer materials can be key in meeting this requirement and upcoming safety regulations in other countries.”
SABIC has also developed a process for adding flame retardancy to resins. “The process features exceptional dispersion of the additive within the resin,” says SABIC’s Nagwanshi, “and that ensures uniform flame-retardant protection across the entire part.”
An example of this resin technology for EV battery pack applications is SABIC’s introduction of non-halogenated flame retardant Stamax resins for various electrification components. Because of its unique character, Stamax FR resin delivers a higher level of fire shielding protection, SABIC says. The exceptional dispersion and distribution of the FR additive within the polymer matrix, even at high loadings, helps maintain structural integrity of EV battery components. “This is not possible with competitive technologies, which would require halogenated FR chemistry to produce the same results,” Nagwanshi says.
Temperature resistance is also a key property for new grades of SABIC’s Noryl GTX resin family. SABIC’s Parikh says, “The expanded temperature range of Noryl GTX resin has the potential to provide value to the OEMs at both ends of the temperature spectrum. The high-temperature resistance of the material allows for plastic components to be assembled to the frame of a vehicle prior to eCoat or along with the body of a vehicle for on-line painting. The low-temperature ductile performance of the material enables more predictable and repeatable energy absorption at low-temperature impacts. This predictability can help engineers optimize their designs and contribute to improved vehicle and occupant safety.”
SABIC’s Parikh continues, “In addition to temperature and impact resistance, our non-halogenated Noryl resins offers flame retardancy for battery covers, modules, electrical enclosure and other EV battery components. Noryl GTX resin can also be used for energy absorbers to aid in crash protection.”
Flame retardancy in plastics also has implications for rapid charging, which is a key aspect of successful electromobility. New standards allow for charging up to 350 kW, which reduces charging time to minutes, but it also requires different materials for the equipment. In these applications, Evonik’s flame-resistant Vestamid PA12 and Vestakeep polyether ether ketone (PEEK) are suitable for use as insulation for cables or busbars in the battery module or electric motor, and as plug components for high-voltage charging.
Sustainability
“The transition toward a circular economy for industrial goods will require the automotive industry and its suppliers to rethink the ways that vehicles and their materials are designed, constructed, used, and handled at end of life,” says ACC.
Dow’s Mark Jablonka agrees that the final big topic is circularity. “How do you make sure, at end of life, that your materials are not ending up in landfill?” he says. Designing for circularity is a tough challenge for the industry overall, and a priority for Dow. “We want to make sure all of the materials on the vehicle end up being recycled, either mechanically, or by using advanced recycling techniques like pyrolysis and gasification with the lowest carbon footprint.”
DSM has also focused heavily on sustainability, including reducing carbon footprints of products and deriving monomers from recycled waste or from bio-sources. DSM has pledged to offer bio-based or recycled versions of all of its products by 2030.
Scott Jenkins