New electrochemical processes are being developed to help CPI companies reduce their carbon footprint
For over a century, electrochemistry has played a crucial role in the chemical process industries (CPI), and many chemicals are still produced using traditional electrochemical processes, such as chlorine and caustic (chlor-alkali process), aluminum metal (Hall-Hérout process) and more (Chem. Eng., December 2014, pp. 17–22 www.chemengonline.com/electrolyzer-technologies-green-hydrogen). More recently, there has been a renewed interest in water electrolysis for producing “green” hydrogen (Chem. Eng., September 2020; pp. 26–30) and in large-scale batteries for storing renewable energy, including redox flow technology (Chem. Eng., September 2016, pp. 14–20). Now, with the goal of achieving carbon neutrality by 2050 or sooner, many producers are active in a number of projects to use electrochemistry with renewable energy and renewable feedstocks to make chemicals. Some of these new processes are now being tested at pilot scale (Figure 1).
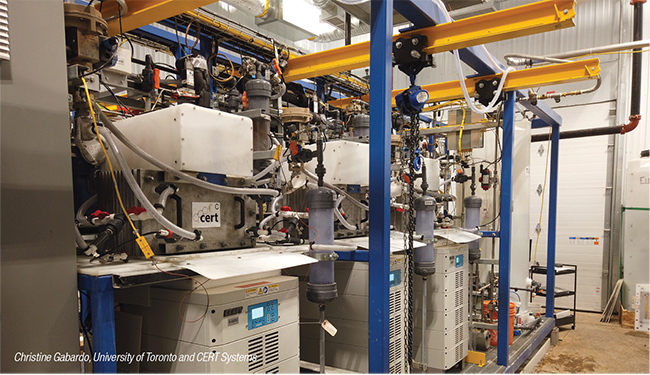
Figure 1. This pilot plant uses a membrane electrode assembly (MEA) for the production of ethane from CO2. It is said to be the world’s largest electrolyzer for producing C2 compounds
CO2-free aluminum
Before looking at the electrochemical production of chemicals, it is worth noting that major breakthroughs are still possible for traditional processes. One of the oldest industrial-electrochemical processes is still the conventional route for making aluminum — the 19th-centrury Hall-Héroult process. In this process, alumina (Al2O3) is dissolved in molten salts at temperatures up to 2,000°C and is electrolyzed in a smelter. The high temperature and large electrical currents used in the smelter make the process very energy intensive. Moreover, today’s aluminum smelters also use carbon-based anodes (graphite or petroleum coke), which are consumed in the reduction process. This not only requires costly anode replacement every 25 days or so of operation, but the consumed carbon-based anode is released as CO2 — a greenhouse gas — and other pollutants.
To reduce the carbon footprint, a breakthrough technology that has the potential to transform the aluminum industry is now being developed by Elysis (Montreal, Queb., Canada; www.elysis.com) — a joint venture (JV), formed in 2018 and led by Alcoa (Pittsburgh, Pa.; www.alcoa.com) and Rio Tinto plc (London, U.K.; www.riotinto.com). At the end of June, Elysis started construction on the first commercial-scale prototype of its inert anode technology at Rio Tinto’s Alma smelter in Saguenay-Lac-Saint-Jean, Quebec. The prototype will operate on a scale typical for large aluminum smelters, using an electric current of 450 kA.
The new anode is made of a proprietary material instead of carbon, and the only byproduct of the process is oxygen. Not only are CO2 emissions eliminated, but also other byproducts formed by traditional anodes, such as perfluorocarbons, CO, SO2, NOx, carbonyl sulfide, polycyclic hydrocarbons and benzol(a)pyrene. When powered by hydro-electricity, the overall process produces CO2 -free aluminum metal.
The new anode is said to be stable and unreactive, and has an expected lifetime of several years. In addition to the proprietary electrode material, the new process also uses a vertical anode/cathode geometry, which is said to increase productivity for the same surface area.
The technology was first demonstrated at the Alcoa Technical Center near Pittsburgh in 2009. In Q2 2020, Elysis opened a research and development center in Saguenay, Quebec.
The Elysis technology was developed with support from the Canadian Government and Quebec Government, each investing CAN$60 million (about $48 million). The first commercial-scale unit is planned for 2024, and the technology will be commercialized globally.
Electro-organic synthesis
Although some commodity and fine chemicals are already being produced using electrochemistry at the industrial scale, there has been a renewed interest in electro-organic synthesis more recently, due to the increasing availability of low-cost electricity, but also the urgent need to reduce CO2 emissions and to develop more sustainable production routes for a cyclic economy.
Electrosynthesis has several advantages over conventional chemical synthesis, says Sigfried Waldvogel, professor at the Johannes Gutenberg University of Mainz (JGU; Germany; www.ini-mainz.de). Electrosynthesis is inherently safe; saves on precious and rare elements; has no reagent waste; is reactive power adjustable; introduces new synthetic approaches; and has green advantages, he says. “This is a disruptive game changer,” he says.
For now, electrosynthesis is probably not suitable for synthetic fuels, because too much electricity would be needed and the volumes of products required are too large, says Waldvogel. Although there are possibilities for using electrosynthesis to make some commodity chemicals, for fine chemicals, there are already scenarios being realized, he says.
Waldvogel and colleagues have been working on electrosynthesis for many years using a simple undivided cell — two electrodes dipped into an electrolyte containing the reactant. When a voltage is applied, the reagent is either oxidized or reduced by donating or gaining an electron at the surface of one of the electrodes. Such an arrangement, he explains, can use an inert electrode, such as graphite, platinum or boron-doped diamond; or an electrode with a catalyst on the surface; or by using a moderator in the reaction. Because there are many parameters that need to be determined in developing such a process (such as electrode material, electrolyte, voltage, current and so on), Waldvogel developed a screening system for conducting multiple experiments at the same time. When combined with design-of-experiments (DoE) and machine learning (ML), the number of experiments needed to determine process conditions is greatly reduced, he says.
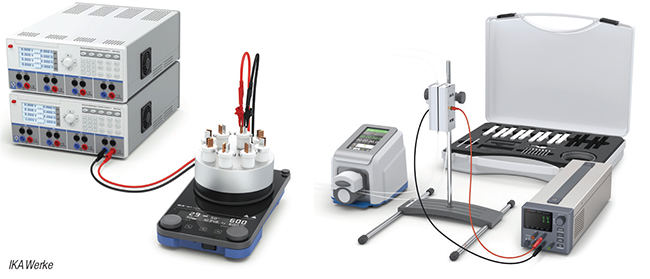
Figure 2. For developing a new electrochemical process, IKA-Werke offers a screening system for performing multiple reactions in parallel (left) and a small-scale flow system (right)
The screening system has since been further developed and commercialized by IKA-Werke GmbH & Co. KG (IKA; Staufen, Germany; www.ika.com), which offers two variations: one with six divided cells and another with eight undivided cells (Figure 2, left). The system includes the power and heating supplies, as well as the control system used for parallel processing of multi-batch electrochemical reactions. A large number of different electrode materials are also available.
After the process has been developed at the laboratory scale, then scaleup is usually performed using continuous flow systems. IKA also offers ElectraSyn Flow (Figure 2, right), a small-scale reactor system for performing continuous-flow electrochemical reactions.
However, the electrochemical process itself is not the only consideration, because the product has to be purified. “Downstream processing is usually the killer of all processes, because it is more expensive than the electrolysis itself,” says Waldvogel.
Nevertheless, electrosynthesis has been shown to be advantageous for a number of reactions. In a recent example, Waldvogel’s group reported an electrochemical route to sulfonamides, which are used in many drugs (Chem. Eng., April 2021, p. 8–9). The new route requires only one synthesis step, compared to three required by conventional routes, which also require corrosive chemicals, high temperatures and expensive metal catalysts.
JGU is also involved in a €10-million project under the E.U.’s Horizon program, which began in 2018 with the aim to produce chemicals from wood-based lignin. The Liberate project (Lignin Biorefinery Approach Using Electrochemical Flow) involves 16 partners, including chemical producers Evonik Operations GmbH (Essen, Germany; www.evonik.com), Perstorp AB (Malmo, Sweden; www.perstorp.com) and Oxiris Chemicals S.A. (Barcelona, Spain; www.oxirischemicals.com), as well as small-to-medium sized companies and universities and research institutes.
In the Liberate project, a highly efficient and selective anodic electrochemical oxidation is being used to depolymerize lignin and produce chemicals. Three types of lignin are being studied: Kraft, organosolv and Fabiola (three different pulping processes). The depolymerization process developed at JGU takes place at 160°C in a caustic solution using nickel electrodes. Three different product trains are being developed: one for making vanillin; another for converting cyclohexanols into 3-propyl adipic acid, a precursor for making polyamides and unsaturated polyester resins; and mixed phenolic derivatives, which can be used for making antioxidants, phenol-formaldehyde resins and other chemicals.
A pilot plant is being constructed at Liberate-partner Sintef AS’s site in Trondheim, Norway. “The reactor system (a plug-flow reactor) has now been implemented into the pilot plant, and we are working on commissioning,” says Bernd Wittgens, senior advisor at Sintef. He expects continuous operation to begin in Q3 2021. The project runs through December 2022.
PowerPlatform (Perform) is another project of the E.U.’s Horizon 2020 program that is aimed at establishing a platform infrastructure for highly selective electrochemical conversions with the goal of the electrification of the chemical industry. This 4-year, €1.7-million project is led by the Netherlands Organization for Applied Scientific Research (TNO; The Hague, the Netherlands; www.tno.nl) with 11 other partners, including industrial participants Avantium Chemicals B.V. (Amsterdam, the Netherlands; www.avantium.com), Perstorp, AVA Biochem BSL AG (Muttenz, Switzerland; www.ava-biochem.com), Novamont S.p.A. (Novara, Italy; www.novamont.com) and Radici Chimica S.p.A. (Bergamo, Italy; www.radicigroup.com). The engineering company Hystech S.r.l. (Turin, Italy; www.hysytech.com) will design and manufacture the platform.
Two different lines are being developed in the platform, which involve the use of biomass-derived C5-C6 feedstock. “Sugar is the new oil,” says Bart van den Bosch, an R&D chemist at Avantium.
In Line 1, a paired electrochemical process is used, whereby furfural is oxidized at the anode to maleic acid, and levulinic acid is reduced at the cathode into valeric acid. Both of these value-added products are industrially relevant, and producing them simultaneously in the same cell has obvious economic advantages. In Line 2, paired tandem electrosynthesis is used to oxidize glucose to glucaric acid, which is then hydrodeoxygenated into adipic acid, another important commodity chemical. The core of the process is the catalyst, which is said to have a selectivity of over 80%.
Currently, the project, which began in January 2019, is in phase 2 with scaleup to a 1,000-cm2 cell capable of producing 25 g/h of product, with integrated downstream processing (electrodialysis, nanofiltration, extraction and distillation, crystallization). Although the location is not yet decided, the pilot plant will be constructed in 2022 and the demonstration finished in 2023. After that, the platform will be available for others to develop electrochemical processes.
CO2 utilization
For the last five years, TotalEnergies SE (Paris, France; www.totalenergies.com) and the research groups of David Sinton, professor of mechanical and industrial engineering and Ted Sargent, professor of electrical and computer engineering at the University of Toronto (Canada; www.utoronto.ca) have been developing an electrochemical process, based on a membrane electrode assembly (MEA), to convert CO2 into C2 compounds, such as ethylene (an important petrochemical) and ethanol (for biofuels). In the initial stages of the research, considerable work was done to improve the electrochemical conversion. First, nanocatalysts were developed, followed by microstructured electrodes “that made sure the reactants get to where they need to be,” explains Sinton. The researchers were then able to increase ethylene productivity by extending the active area of the electrode. This was done by using a metal:ionomer hybrid catalyst, which decouples gas, ion and electron transport, and enables the CO2 to be carried into the catalyst.
In partnership with Total Energies and the University of Toronto, a pilot plant was constructed (Figure 1), which has been running 24 h/d for months. The pilot plant uses a MEA with area of 40,000 cm2 — a considerable scale up from the 5–100-cm2 units used in laboratory studies. Sinton says, to his knowledge, this is the largest C2-producing electrolyzer in the world. The pilot is being used to learn more about the process and for making improvements.
For example, one of the problems associated with MEA is that when CO2 is introduced to the electrolyte, it is quickly converted to carbonate. To avoid this loss, the researchers recently showed that this loss can be avoided by using a tandem system. First CO2 is converted to CO in a solid-oxide electrochemical cell (SOEC), then the CO is converted to ethylene in a MEA. This study, published in the February 15 issue of Joule, found that the tandem configuration had an overall efficiency of 140 GJ/ton of ethylene — a 50% reduction from the direct route.
Meanwhile, a flagship project involving industrial partners Royal DSM N.V. (Heerlen, the Netherlands; www.dsm.com) and Avantium, together with TNO and VoltaChem (Delft, the Netherlands; www.voltachem.com), aims to reduce the CO2 emissions from fermentation processes that are used for making higher value products. These fermentation processes use sugars as a renewable feedstock, but only a fraction of the sugar is used as a carbon source for the product; the rest of the sugar is used as an energy source for the microbes, which release CO2 as a waste product. The partners are working on a process that captures the released CO2, reduces it to formic acid electrochemically, and then feeding the formic acid back to the fermenter as an energy source. This not only eliminates the net CO2 emission, but reduces the amount of sugar needed for making the product.
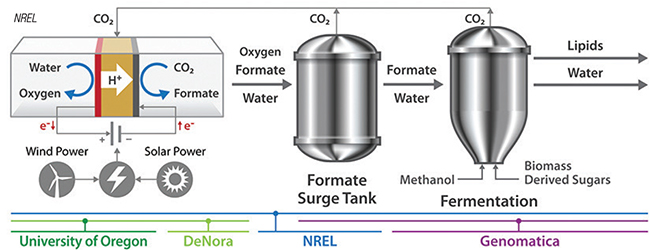
Figure 3. Formate can both stimulate the conversion into lipids and serve as an anchor for recycling carbon dioxide from the fermentation
A similar project is now underway in the U.S. In May, researchers at the National Renewable Energy Laboratory (NREL; Golden, Colo.; www.nrel.gov) were awarded nearly $3 million from the U.S. Dept. of Energy’s Advanced Research Projects Agency-Energy (ARPA-E) to lead a project to develop CO2 -free fermentation technology. Together with partners from the University of Oregon and industrial partners Genomatica (San Diego, Calif; www.genomatica.com) and De Nora Tech, LLC (Plainseville, Ohio; www.denora.com), NREL plans to integrate electrochemistry with sugar fermentation to produce fatty acid methyl esters (FAME), which are used to make biofuels. Like the Dutch project, the process (Figure 3) captures the CO2 from a fermentation process, and the CO2 is reduced to formate ions and O2 in an electrochemical cell powered by renewable electricity. The formate is then used as an energy carrier for the fermentation process, thereby reducing the demand for sugar and reducing CO2 emissions.
Meanwhile, researchers from the Fraunhofer Institute for Interfacial Engineering and Biotechnology (IGB; Stuttgart, Germany; www.igb.fraunhofer.de) are working in two E.U. projects (EVOBIO and ShaPID) to develop ways to utilize CO2 using both biotechnology and electrochemistry. The research team works with native methylotrophic bacteria, which metabolize methanol, and yeasts that cannot metabolize methanol. Using metabolic engineering, genes are introduced into the microbes that provide the blueprint for certain enzymes, which are subsequently produced in the microorganism to catalyze the production of a specific product.

Figure 4. This bioreactor setup is used for growing large amounts of biomass of M. extorquens AM1
Methanol and formic acid are used to feed these engineered microorganisms, which are grown in bioreactors (Figure 4). Both feedstocks are made from CO2 — methanol is made from a heterogeneous catalytic reaction of CO2, and formic acid is made by the electrochemical reduction of CO2. The CO2 generated by the fermentation can also be recovered and used for making more methanol or formic acid.
Products being investigated include organic acids, which are building blocks for polymers, and amino acids as food supplements or animal feed.
Printing better reactors
Improving the performance of electrochemical reactors is a goal of everyone working in this field, and a step in this direction is being developed at the Lawrence Livermore National Laboratory (LLNL; Livermore, Calif.; www.llnl.gov). In two recent publications, LLNL researchers and its team describe how 3D printing can be used to rapidly enhance electrochemical reactors for CO2 conversion. In an article published last month in the Proceedings of the National Academy of Sciences ( PNAS), the LLNL engineers describe how it is possible to use 3D printing to make carbon flow-through electrodes (FTEs) from graphene aerogels. Using this technology, the researchers demonstrated that they could “tailor” the flow in FTEs, “dramatically” improving mass transfer of liquids or gas reactants through the electrodes and onto the reactive surfaces. Conventional materials, such as carbon-fiber-based foams or felts, have a randomly ordered microstructure, which leads to uneven flow and mass-transport distribution. In contrast, the flow channel geometry could be controlled using 3D printing, so that electrochemical reactions can be optimized (Figure 5). “By 3D printing advanced materials, such as carbon aerogels, it is possible to engineer microporous networks in these materials without compromising the physical properties, such as electrical conductivity and surface area,” says LLNL researcher and co-author of the PNAS paper.
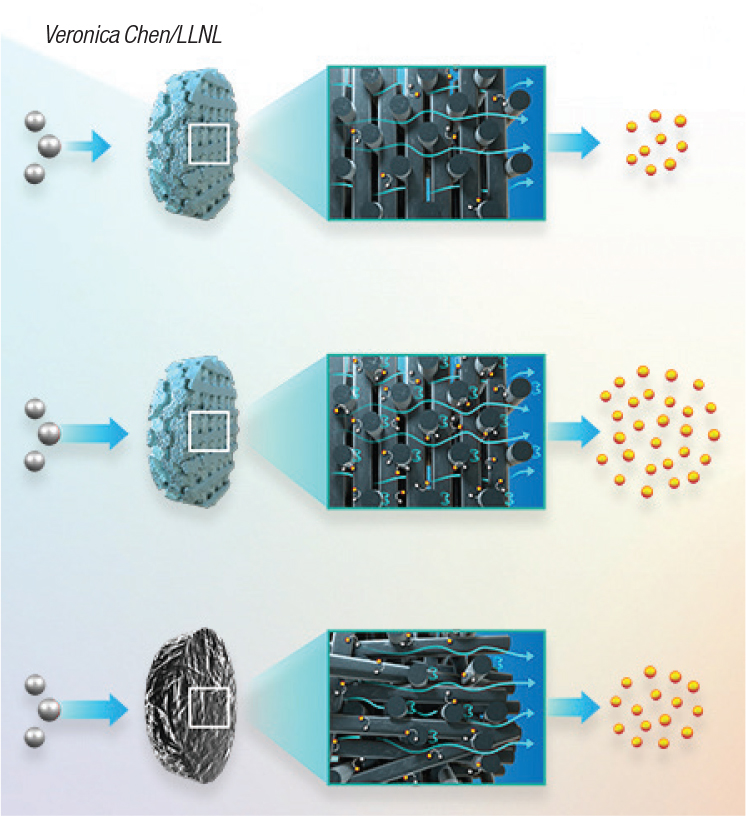
Figure 5. Carbon-based flow-through electrodes can be 3D printed with optimized flow and mass transfer characteristics
LLNL scientists and engineers are exploring the use of electrochemical reactors for a number of applications, including the conversion of CO2 into fuels and polymers, as well as applications in electrochemical energy storage.
The researchers are working to produce more robust electrodes and reactor components at higher resolutions through light-based 3D polymer-printing techniques, such as projection micro-stereolithography, followed by metallization.
The use of 3D printing not only helps to optimize the flow in FTEs, but it also makes it possible to quickly build and test new reactor designs. “The real advantage for using 3D printing is that we can literally have an idea, design a new reactor, print it and test it within 24 hours,” says LLNL scientist Jeremy Feaster, who co-authored a report published in the May 2021 issue of Energy & Environmental Science, with partners Stanford University (Calif.; www.stanford.edu) and Total American Services, Inc. (Houston). “What we’ve been able to show is that you can quickly iterate on the design and cut not only the time it takes, but also the cost to make these reactors by several orders of magnitude,” he says.
For this study, the researchers used 3D printing for the reactor housings and rapidly iterated to find the optimal geometry, which improved the overall mass transport of reactant to the catalyst, and products from the catalyst. Benchmarking studies performed at Stanford demonstrated high yields for ethylene (3.36%) and record levels of ethanol (3.66%), compared to literature values.