Tighter enforcement requires up-to-date monitoring and control equipment
With stricter emissions regulations on the horizon and with the U.S. Environmental Protection Agency (EPA; Washington, D.C.; www.epa.gov) actively enforcing ones, the chemical process industries (CPI) can not sit back and relax. The EPA has been actively cracking down on the enforcement of existing regulations and is paying closer attention to reporting and quality assurance of the measurements and information being reported. So what does this mean for chemical processors? It necessitates the continued use of top-notch environmental monitoring and control technologies, as well as solutions that provide more accurate and timely reporting of data. This article examines the newest trends in monitoring, control, software and solutions designed to ensure compliance.
Monitoring instrumentation
When it comes to monitoring, processors tend to be moving away from traditional instruments toward newer, more accurate and reliable methods, including laser-based devices. “The real challenge with traditional methods of monitoring is in the sample conditioning system, which includes the probe, the probe filter, the pump and associated moving parts,” explains Warren Dean, senior strategic sales support with Siemens Corp. (Alpharetta, Ga.; www.usa.siemens.com). “And those parts become even less reliable when measuring reactive components.”
To overcome this obstacle, he says instrumentation providers have devised non-traditional ways, including laser technologies, to measure these components in situ. “Tunable-diode laser (TDL) analyzers are excellent at accurately, effectively and reliably measuring ammonia and other highly reactive gases thanks to the laser technology,” explains Dean.
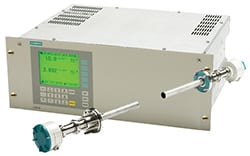
Figure 1. Siemens’ Sitrans LDS 6 TDL instrument is designed to measure the necessary components directly in the stack without any sample handling or conditioning system
Siemens Corp.
Siemens’ Sitrans LDS 6 TDL instrument (Figure 1) is designed to measure the necessary components directly in the stack, duct or process stream without any sample handling or conditioning system. The TDL measurement technique allows measurement of ammonia, hydrogen chloride, oxygen, carbon monoxide and carbon dioxide in extremely dirty, dusty or corrosive samples where an extractive sampling system would quickly fail or require constant maintenance. The LDS 6 has an internal reference cell for long-term stability and lifetime on-line, continuous, automatic calibration requiring no calibration gas. This technology ensures reliability and accuracy of the measurements.
The Rosemount Analytical division of Emerson Process Management (Irvine, Calif.; www.emersonprocess.com) is also turning to laser technologies in the form of quantum cascade lasers (QCL; Figure 2). The technology is based upon TDL absorption spectroscopy (TDLAS) and replaces other measurement techniques, such as paramagnetic detectors and chemiluminescence. QCL offers multi-element detection, high accuracy, wide dynamic range, low maintenance and a long lifecycle. Unlike TDLAS, QCL doesn’t require cryogenic cooling.
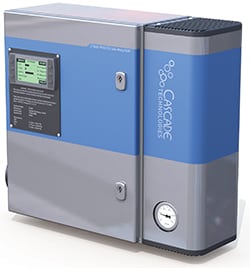
Figure 2. Emerson Process Management’s quantum-cascade laser instrument features multi-element detection, high accuracy, wide dynamic range, low maintenance and a long lifecycle
Emerson Process Management
QCL technology features a cascade of electrons down a series of quantum wells, which result from the growth of very thin layers of semiconductor material. Traditional single electron-hole recombination methods can only produce a single photon, whereas the quantum cascade laser can cascade down between 20 and 100 quantum wells, producing a photon at each step. This technology produces an electron “waterfall” that provides a step change in performance in terms of efficiency, enabling QCL to emit several Watts of peak power in pulsed operation and tens of milliwatts continuous wave. All this translates, according to Ruth Lindley, product manager, into the ability to collect up to a million measurements per second and measure up to 20 gases simultaneously.
“This means processors can use just one analyzer to reliably and accurately measure multiple gases,” says Lindley. “The advantage is that we can measure the majority of the components people must monitor, such as oxides of nitrogen (NOx), sulfur oxides (SOx), CO, CO2, ammonia and oxygen. Replacing multiple analyzers with a single solution is not only cost competitive, but it simplifies the measurement process.”
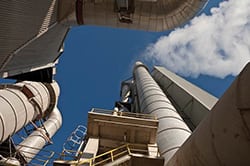
Figure 3. Chemical processors may begin to move away from point emissions monitoring to whole-site footprints via the use of remote sensing technologies like drones and lasers, according to experts at Golder Associates Golder Associates
And, lasers are expected to play a huge role in the very near future of measurement technology, as well. Sam Arnold, senior atmospheric scientist with Golder Associates (Nottingham, U.K.; www.golder.com) says, “Chemical processors may begin to move away from point emissions monitoring to whole-site footprints via the use of remote sensing technologies like drones and lasers (Figure 3). Monitoring the average emissions of a whole site with drones or lasers has the advantage over point monitoring in that it helps avoid having to take compliance actions based upon the measurements of single pieces of equipment that could be outliers.
“The industry is increasingly innovating in technology and turning to this type of monitoring to stay at the forefront of regulatory compliance on emissions controls,” says Arnold.
Emissions control technologies
Emissions control is one of the areas where EPA is most likely to crack down on existing regulations, which could result in the need to upgrade to one of today’s more efficient and certifiable options.
For example, Scott Bayon, director of sales with Anguil Environmental (Milwaukee, Wis.; www.anguil.com), says many processing facilities that had been flaring emissions are being forced to look at more-modern control technologies where it is possible to accurately measure what is coming into the system and what is coming out of the system to ensure destruction efficiency.
In addition, many of the oxidizer technologies installed 20 years ago are reaching the end of their useful life, he says. This means that when attempting to amend air permits, many processors are finding that they need to replace lower-efficiency existing equipment with today’s more efficient models, says Bayon. “The 95% destruction efficiency achieved by older technology might have been the gold standard when it was installed 20 years ago, but today 99-plus percent efficiency is easily achievable and is what regulatory agencies require.”
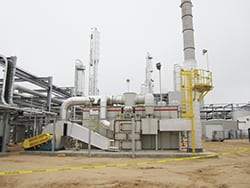
Figure 4. Regenerative thermal oxidizers provide a cost-effective-emission control solution as they achieve 99% destruction efficiency
Anguil Enviornmental
For this reason, many processors are moving away from catalytic oxidizers toward thermal oxidizers. Bayon says regenerative thermal oxidizers (RTOs; Figure 4) provide a cost-effective solution as they achieve 99% destruction efficiency of hazardous air pollutants (HAPs), volatile organic compounds (VOCs) and odorous emissions without the use of a catalyst. RTOs achieve emission destruction using a mix of temperature, residence time, turbulence and oxygen to convert pollutants into carbon dioxide and water vapor.
Vipul Patel, project manager and environmental specialist with Epcon Industrial Systems (The Woodlands, Tex.; www.epconlp.com) says that direct-fired oxidizers (Figure 5) may be the preferred solution when there is a very high VOC or hydrocarbon load, as well as fluctuating operating conditions. In this technology, flame arrestors are installed between the vapor source and the thermal oxidizer. Burner capacities in the combustion chamber varies based on the size of the system and the VOC loading. Operating temperatures range from 1,400 to 1,800°F, and gas residence times are typically 1 s, or more. The conditions cause the process stream’s molecular structure to break down into simple CO2 and water vapor.
Patel acknowledges that this technology may use a lot of fuel, but says the solution is often offered as part of a package that features heat recovery equipment intended to reduce overall fuel consumption of the plant by using the waste heat to provide steam, hot water or hot air to other areas of the plant to alleviate the cost of additional equipment and overall fuel consumption.
Automation and software
When it comes to compliance, automation and software can provide much needed assistance to processors looking to ensure tighter control and faster, more accurate reporting.
“One of the factors that has driven the growth of automation is that it can help with environmental compliance and reporting,” explains Lee Swindler, program manager with Maverick Technologies (Columbia, Ohio; www.mavtechglobal.com). “Automating the process instead of relying on human operators not only makes the plant run more profitably and reliably, but it also allows it to run with fewer emissions. It can also be used to help document and prove that the plant is in compliance and can measure actual emission levels and make a record, which can be used to provide regulatory agencies with the necessary information in a very timely manner.”
One of the most important areas automation expertise can help is in the timely detection and reporting of emissions events, notes Swindler. “A lot of the compliance requirements involve being disciplined around how you monitor and report an event in which an emission limit has been exceeded. Typically this is a very lengthy manual process for many plants, which is problematic because there are often time limits associated with how quickly such events are acted upon and reported. A more automated reporting process can help alleviate this challenge, and is one of the areas where we see a lot of potential and promise.”
Philip Black, environmental practice lead, with Wood Group Mustang (Houston; www.mustangeng.com) agrees that time is of the essence. Penalties, he adds, can become costly if a problem goes unnoticed for a significant period. “If you’re required to maintain compliance on an hourly basis, but your environmental management system only processes data once a day, you may not have known there was an event until the next day. This means that you could have been out of compliance for 24 h, which could result in significant fines, says Black.
In addition, as technology increased and regulations tightened, processors began using continuous monitoring systems to analyze samples in realtime and provide values at a very high frequency. “Not only do the environmental agencies require processors to report all these data, but they often require a tremendous amount of quality assurance on the instruments themselves,” he says. This means, according to Black, that processors must certify that not only are their emissions below a certain limit, but also that the many instruments monitoring the emissions are operating correctly nearly 100% of the time. “These data and associated quality assurance documentation must be reported together, in a timely manner,” notes Black. He says that over the years, many processors have developed spreadsheets or other tools that require time-consuming manual work to handle this arduous reporting task.
“However,” he continues. “There are software solutions that handle all the environmental calculations, quality assurance and validations in realtime, so that operators always know the current status and can be assured that the process is in compliance at any given time.”
To this end, Wood Group Mustang offers ENVision, a software suite that provides a realtime flow of information and notifications of potential issues, allowing proactive responses to prevent non-compliance. The system brings transparency to the calculation process and lowers the cost of compliance by automating the data gathering and reporting. The software integrates with enterprise resource planning (ERP) software and environmental management information systems (EMIS) to automate additional reporting requirements, as well.
Software may also be used to help processors reach compliance earlier in the design process. For example, aspenONE from AspenTech (Bedford, Mass.; www.aspentech.com) can be used to model, track and reduce emissions more effectively and earlier on in the design process. “Companies could achieve emissions reductions of up to 40% through improvements in operations and maintenance, investments in energy-efficiency measures at the equipment and process levels and the use of software tools to model and manage their operations,” says a spokesperson for AspenTech.
The simulation modeling functionality in aspenONE Engineering helps process manufacturers by making it easier to comply with global health, safety and environment policies and regulations. The greenhouse-gas (GHG) calculation capabilities within AspenHYSYS and Aspen Plus give processors an automated solution that accurately determines GHG emissions for simulated processes. The new functionality calculates equivalent greenhouse-gas emissions (GHG) from direct and indirect sources, such as energy consumption and chemical processes, and reports on those emissions to support GHG reporting and compliance. n