Following the devastating explosion at the Imperial Sugar Co.’s Georgia factory that killed 14 people, injured many more employees and leveled the facility in February 2008, it was determined by the U.S. Occupational Safety and Health Admin. (OSHA; www.osha.gov) officials and the U.S. Chemical Safety Board (CSB; both Washington, D.C.; www.csb.gov) that the catastrophe could have been prevented had the manufacturer taken available steps to reduce the presence of sugar dust in its facility.
As a result of these findings, the U.S. regulatory climate turned a watchful eye toward combustible dust in the workplace, culminating in the announcement by new OSHA Chairman George Miller that a new standard on combustible dust is to be expected in the near future as part of the agency’s Reissued Combustible Dust National Emphasis Program (see box below). This announcement, combined with the current increase in OSHA inspections with regard to combustible dust in targeted industries, has spurred a lot of interest in explosion prevention and protection equipment in the chemical manufacturing industry, which is third behind the wood and food industries on OSHA’s list of targets.
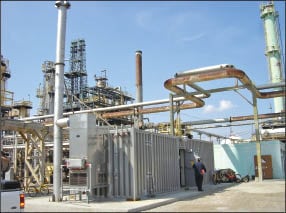
Currently OSHA is using applicable NFPA Standards 68, 69 (which define how to protect) and 654 (which defines where to protect) to inspect high-priority industries until their own standard is issued. “Basically any facility that is working with powders, drying materials from a wet to dry state, using dust collectors or air material separators or anywhere there is a process risk for a dust combustion event to take place needs to start thinking about proper protection,” says Bob Korn, director of sales, Fike Corp. (Blue Springs, Mo.; www.fike.com).
While it is difficult for processors to decide how to go about meeting a standard that doesn’t yet exist, explosion prevention experts say that now is the time to start making decisions. “Most people believe that using equipment that meets the current NFPA codes is going to be an acceptable way to meet the OSHA standards,” says Geof Brazier, director of product and market development, BS&B Safety Systems (Tulsa, Okla.; www.bsbsystems.com). However, he notes that there will be at least one major difference. According to current NFPA standards, if the facility met previous versions of the code, it is still in compliance with NFPA. OSHA, however, will likely rule that all facilities be up to date with the most recent version of NFPA if this is the chosen path to meet worker safety expectations. The current OSHA National Emphasis Program references all of the current NFPA standards for this purpose.
This change in grandfathering means that existing facilities will be scrutinized as closely as new construction, so all facilities with a risk for dust explosions need to start planning and working now in an organized, systematic manner to implement a risk protection plan.
“Now is the time to get your risk analysis and risk management plans in place and start looking at prevention and protection equipment,” says Brazier. “Starting now will allow processors to implement their plans and equipment on a budget and make informed decisions about which type of equipment is right for their facility and their needs.”
And, there are several choices to be made when it comes to dust explosion prevention, starting with the choice between active and passive systems. Passive systems include explosion vents that function completely based upon the design and construction of the item. There is no circuitry or logic for making decisions. Included in this group are explosion vents and flameless explosion vents. Active systems include explosion suppression systems, which use sensing detectors to identify that an explosion has started. There’s a logic decision in the controller that activates the rapid release of an agent into the offending equipment to prevent a full explosion from developing.
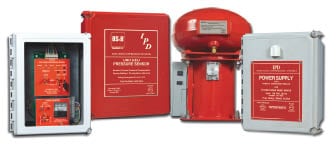
Venting versus suppression
There are pros and cons to each type of system. “We see many advantages of venting over suppression systems,” says Gerd Mayer, president of Rembe, Inc. (Charlotte, N.C.; www.rembe.us), which offers both types of equipment. “Suppression systems are subject to a lot of faults and if you don’t actually have an explosion situation and the suppression system is emptied, a facility can be knocked out of production for several days because everything, not just the dust collector, will have to be cleaned as the agent spreads all over the processing line. If you’re in a food, chemical or pharmaceutical plant, you don’t want suppression agents in your product.”
![]() |
Figure 3. The Q-Rohr-3 guarantees
indoor venting without any flames or dust propagation, allowing protection for equipment that is hard to access or free standing in the process area Rembe
|
Also, there are high maintenance costs associated with suppression systems, says Mayer. NFPA 69 explains that a suppression system should be checked a minimum of four times a year because the agent-containing bottles can lose pressure, which would result in faulty or no activation during an event.
“In many cases vents are chosen because they are an inexpensive and readily available way to retrofit an installation to meet standards,” explains Christopher Driesel, engineering manager with Oseco (Broken Arrow, Okla.; www.oseco.com). “Active systems are more expensive over the longterm cost of ownership because of the necessary inspections and maintenance involved.”
However, it is important to remember that venting systems are not “fit and forget.” Brazier says that the latest generation of NFPA standards is very clear that even passive systems do have a requirement for periodic inspection. “This is something that the end user community is very weak in embracing,” he says.
Inspection here is necessary because several factors could affect the operation. For instance, process material can build up inside the vent, causing it to become heavy, which may result in an inability to open fast enough, or at all, during an event. Another example is when a process changes, which can have significant consequences to the protection equipment if the material being processed was changed to one with higher combustion characteristics and previously employed safety measures might not be enough to control the current hazard. “A good guideline is that having partial protection might be the same as having no protection,” points out Brazier.
Providers of both kinds of systems are working hard to improve upon the faults of their equipment. Oseco, for example, now offers the MV explosion vent with an all-metal (no fluoropolymer) design using a stainless-steel membrane. No holes or slits are visible, which makes the MV suitable for applications where product buildup may be a concern.
And as flameless venting continues to be favored where a fireball can’t be released, many equipment providers are coming up with new models. Rembe’s Q-Rohr-3 guarantees indoor venting without any flames or dust propagation. Therefore appliances that are hard to access or standing free in production areas can be protected without reconstruction work to walls or buildings. The company says the vent is maintenance free, making it a very economical comparison to similar active quenching systems.
Fike offers Flamquench flameless venting solutions that extinguish flames from vented explosions — not allowing flames to leave the device where secondary explosions could be ignited — without ducting, limitations on location of the process equipment or the use of other explosion protection systems.
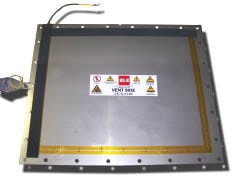
Also to help make sure vents are working properly, BS&B offers the Type VIS vent integrity sensor, which brings continuous monitoring capability to explosion vents. VIS technology comprises an electrically isolated supervisory circuit placed beneath the explosion-vent gasket arrangement. The circuit passes over each of the controlled points of weakness that determine the vent relief pressure. The VIS circuit runs along the three opening sides of the vent. The sensor provides a signal when any one burst control member (present in all BS&B explosion vent types) is compromised, allowing personnel to take immediate action when normal operating conditions threaten vent integrity.
In the suppression system arena, BS&B also provides the Type IPD Explosion Suppression System for protection where dust suspended in air represents an explosion hazard. The early stages of the pressure rise associated with a dust explosion are detected by the unitized sensor, which is mounted to the equipment to be protected.
When at least two of the three individual pressure sensors respond, an electrical signal activates the explosion suppression cannons installed on the equipment, causing the pulverized suppression agent (food-compatible sodium bicarbonate) to be energized and discharged into the equipment, extinguishing the early stages of combustion before it builds into a deflagration, which can generate a pressure exceeding the strength of the process equipment.
Making the choice between these or any other passive and active protection systems rests with the processor. “It’s all about looking at the unique attributes of each individual application, considering the concerns of each application and the way they want to conduct their business when it comes to identifying which of these many options is the right choice for a specific scenario,” says Brazier. “There needs to be a good fit between the business intentions and the technology selection in order to get the job done safely.”
Click here for full pdf version of this article – includes all graphs, charts, tables, and author information