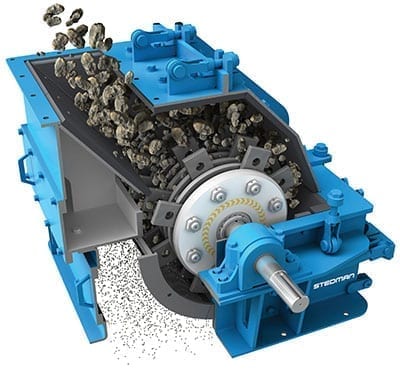
Stedman Machine Company
Hammer mills for reducing soft to medium-hard materials
The ideal hammer mill is determined by feed size, feed rate, operating conditions and desired product output. This company offers many configurations of industrial hammer mill grinders (photo) that transform the consistency of soft and rough materials by using the pulverizing technique of a hammer mill grinder to produce a finished particle. Capacities from 1 to 300 ton/h are offered with 30- to 250-hp models. Capacities vary depending on feed size, feedrate, operating conditions, desired product output, characteristics of feed material, and equipment configuration. Perforated screens or grate bars are used for reducing soft to medium hard materials with multiple size-reduction stages. Fibrous materials are easily handled due to the high concentration of shearing actions by the grate bars or screen within the unit. Specially designed heavy reversible hammers, working in conjunction with the company’s adjustable breaker plate, enables the hammer mill to produce a uniform product with the lowest possible maintenance. — Stedman Machine Co., Aurora, Ind.
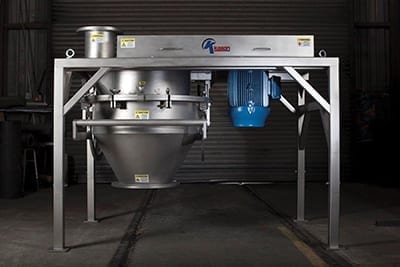
Kason
High-capacity cone mill for sticky, moist fragile materials
A new 29.5-in.-dia. (750 mm) cone mill, CGM 750 (photo), gently grinds fatty, heat-sensitive, sticky, moist or fragile materials into uniform particle sizes with minimal fines at rates up to 35 ton/h (32 m.t./h). Vertical material flow and low-energy grinding action with short residence times yield close particle-size distribution from 125 to 250 microns, without the noise, dust, product build-up or heat generation associated with traditional mills, says the manufacturer. Ideal for bulk pharmaceuticals, foods and contamination-sensitive chemicals, the sanitary unit is suitable for wet and dry milling, pre-conditioning and de-agglomerating of a wide range of bulk products. Material is fed by gravity or vacuum-conveying system into a central milling chamber, in which a rotating impeller accelerates it centrifugally against and through apertures in a conical screen, and then into a receptacle below the milling chamber. A pneumatic, swing-down conical discharge chute with quick-release clamps allows easy lowering of the 250-lb (114-kg) cone housing and full access to the housing interior, beater and perforated conical screen for cleaning and sanitizing. The unit can be cleaned wet or dry, and is available configured for clean in place (CIP), steam in place (SIP) or filling with liquid during cleaning. Provision is included for optional air purging of bearings and seals. Conical screens with round, square or raised-lip (cheese grater) perforations can be changed rapidly and are offered with apertures from 150 micron for fine/dry de-agglomeration, and up to 25 mm for wet granulation. Constructed of 304 or 316 stainless steel to sanitary or industrial standards, the mill is top-driven by a belt drive and equipped with fully interlocked moving components with time-delay function for operator safety. Explosion-containment versions are also available. — Kason Corp., Millburn, N.J.