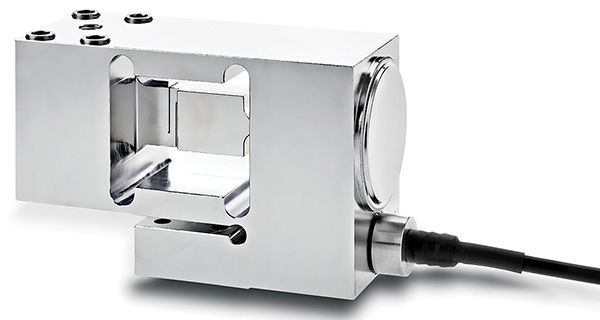
Alfa Laval
This load cell is robust and hygienic
The UltraPure single-point load cell (photo) is a comprehensive solution for hygienic process weighing and measurement of liquid level, mix ratios, dosage or batching, and is suitable for weighing on small hoppers and vessels, scales or conveyor belts. With its patented technology, mounting kits are unnecessary and setup is quick and easy. A complete laser-welded construction makes the weighing system an ideal choice in processes where the production environment is hosed down on a daily basis. The pre-calibration of the load cells eliminates the need for onsite calibration in many applications. Mechanical protection devices are not necessary when installing these digital load cells. This is not only an important cost and maintenance saver, but also allows for a hygienic installation. Two standard accuracy ranges ( 0.05% and 0.025%) are available that cover a total measurement range up to 150 kg. — Alfa Laval AB, Lund, Sweden