Designing easier access to mechanical components in solids-conveying systems reduces maintenance costs and improves safety
Virtually every vehicle on the road today is designed with an engine hood that can be easily opened for access to the engine, so mechanics can perform routine service and diagnose and address problems that arise during its lifespan. Without that access, cars and trucks would be nearly impossible to maintain, and service life would be short. Bulk-solids conveyor systems should be designed in much the same way, with convenient points along the length of the belt to allow technicians to inspect its condition, perform service as needed and help prevent catastrophic failure.
After nearly a century of working with bulk handlers all over the world, experts have discovered that “maintenance access” is a common element for both safety and productivity across all industries (Figure 1). By adding safe, easy access and monitoring in the design phase, equipment can be better maintained using less labor, leading to reduced downtime. This is reflected in the cost of operation, offering a better overall return on investment.

FIGURE 1. Bulk handlers must be set up so that maintenance work can freely take place as needed
Unfortunately, this type of access is often overlooked when engineering conveyor systems — until a pressing need arises. The failure to recognize the importance of access on mechanical conveying systems increases the difficulty of ongoing inspection that could have allowed technicians to observe and service critical components before a crisis develops. As a result, lifecycle costs of the conveying system increase while productivity goes down. This is particularly true in a company culture that emphasizes a low-bid process, which encourages bidders to follow a belt-conveyor design methodology based on maximizing the load on the conveyor belt, while meeting the minimum regulatory compliance goals, often using the lowest price materials, components and manufacturing processes available.
This article describes best practices and design tips for maintenance access on mechanical conveying systems.
Lifecycle costs
Often when companies make purchasing decisions based primarily on price, the benefits are short-lived, and costs actually increase, resulting in a net loss over time. In contrast, when purchases are made based on lowest longterm cost (lifecycle cost), benefits usually continue to accrue and costs go down, delivering a net savings over the life of the system. In order to win the bid on price, suppliers only have to meet minimum quality and safety requirements, when a little additional investment for safer and more reliable equipment will usually result in an operation that is safer and more sustainable: easier to service, longer life, with lower costs to maintain.
Conveyor technology manufacturers have responded to the need for increased accessibility to system components by engineering accessories specially designed to reduce labor time while improving safety during service by maintenance staff. Innovative equipment designs, such as slide-out cradle frames, belt cleaner assemblies, idler assemblies — as well as sealed heavy-duty inspection doors — offer better access for safer and more efficient maintenance, resulting in fewer injuries, less labor for service and a lower overall cost of operation.
Conveyor maintenance access
Access doors should be sized as large as the available space will allow, and placed in locations likely to require regular inspection and service. A small access portal may allow inspection, but whenever possible, a larger door will also permit service to be performed, and it should be designed with a minimal ledge on the inside lip, to prevent the buildup of potentially explosive dust. When an access door has a large internal lip, dust can accumulate to depths of an inch or more. By nature, the inside of a transfer chute is a pressurized area, so when the access door is opened, air movement will carry the dust directly into the face of the person performing an inspection or service, providing an unwanted and unpleasant demonstration of what the bulk material tastes like.
To assist engineers when designing conveyor systems, the seventh edition of the CEMA (Conveyor Equipment Manufacturers Association; Naples, Fla.; www.cemanet.org) handbook Belt Conveyors for Bulk Materials [1] provides recommended clearances for servicing components, such as belt cleaners and impact cradles, based on minimum requirements and belt width.
Maintenance access is a cascading issue: improper access leads to poor maintenance practices, resulting in emergency outages and diminishing the operation’s productivity and safety. From an ownership and management perspective, downtime and injuries affect profitability through loss of production, capital expenditures for new equipment and ongoing insurance implications.
In the past, managers often decided against the expense of adding safer and easier access points to a conveyor system beyond what is required by code. However, over the system’s lifetime, conveyor maintenance professionals estimate that poor access increases maintenance and cleaning costs by 65%.
When designing proper access into a conveyor system, there are three objectives:
- Make components easy to see. If equipment cannot be seen, neither can problem
- Make components easy to reach. Equipment maintenance is likely to be postponed if it is awkward or dangerous to access
- Make components easy to replace. Failing equipment can remain without service for a long period if it is complicated and time-consuming to access
Loading-zone innovations
Across virtually all industries that handle bulk solids, conveyors are increasingly being required to handle higher loads at greater speeds, often rendering original system designs inadequate. Many conveyor transfer points still have an outdated roller system tasked with absorbing impact and centering the material being carried. As a result, components can break and seize, causing friction and creating a potential fire hazard. To replace them, workers must remove the skirtboard and break the plane of the conveyor as they reach across the stringer with heavy tools to assess and repair equipment. Further, traditional skirtboards and wear liners can limit access, with some designs welded to the inside of the chute structure, involving confined space entry with a grinder or blow torch to perform maintenance, repair or replacement. To avoid these complications, specifiers would be well served to consider external wear liners, skirtboards and seals that can be safely serviced from outside the structure, reducing service time and risks.
To reduce maintenance time and labor, improve safety and extend equipment life, operators should consider track-mounted impact cradles and belt support cradles (Figure 2). Located under the skirtboard and mounted with rugged steel assemblies, the cradles feature large impact-absorbing UHMW (ultrahigh molecular weight) polymer “box bars” engineered with smooth surfaces across which the belt can slide with little friction or belt wear. These assemblies can be pulled out by a single worker, working safely from outside the conveyor. In some cases, box bars can be simply removed and flipped over to double the service life.
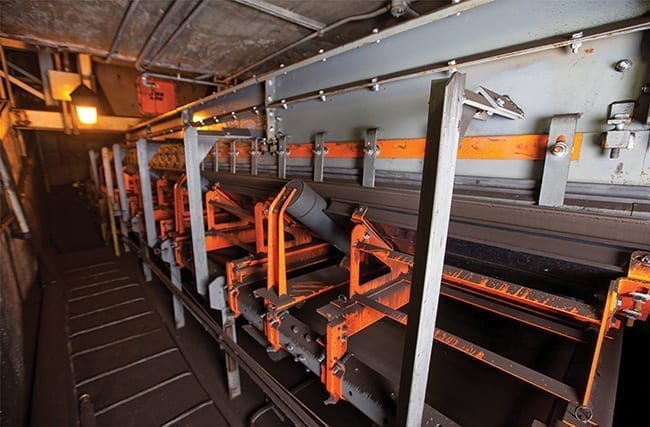
Figure 2. Track-mounted components and inspection doors facilitate maintenance for extended equipment life. Photo: Martin Engineering
Along the cargo path in the settling zone and beyond, slide-out/slide-in idlers support the belt and maintain the trough angle. Exposed to the punishing environment, gritty dust and extreme weather, rollers can easily seize. Often set close together in the loading zone to avoid belt sag, easy-to-service roller frames permit workers to perform idler service outside of the belt plane without the need to raise the belt or remove adjacent idlers (Figure 3).
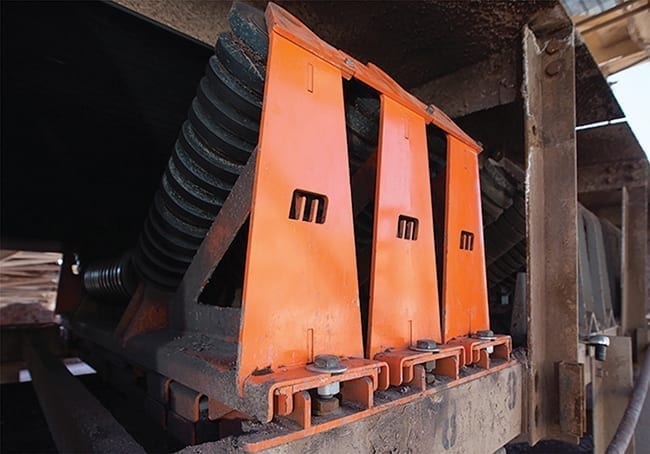
Figure 3. Track-mounted idlers allow service technicians to quickly swap out failed rollers. Photo: Martin Engineering
Discharge zone maintenance
Parts that wear, such as belt cleaner blades, need to be monitored, serviced or changed regularly to prevent carryback from causing dust and spillage along the belt path. However, blade maintenance and changes with existing designs can require several hours of downtime.
To address the issue, newly developed automated tensioners have been designed that continuously monitor belt cleaner pressure and wear, automatically adjusting for optimum cleaning performance and service life. An automated tensioner can be run off the existing electrical service or paired with a local power generator, which uses the kinetic energy of the moving belt to generate electricity. Powered auto-tensioners are considered “smart” devices that can deliver realtime performance data from a remote location.
On most existing belt-cleaner designs, primary cleaners — located just under the material flow path on the head pulley — are mounted on rotating assemblies that maintain the proper tension between the blade and the belt. Secondary cleaners are typically located under the belt and behind the head pulley. Both need regular inspection and adjustment to obtain maximum cleaning performance and service life. One way to improve maintenance access and safety while reducing service time is with track-mounted blades that can slide in and out by simply pulling a lever and releasing a pin. This allows maintenance to be performed outside of the system by a single worker — typically in less than one hour (Figure 4).
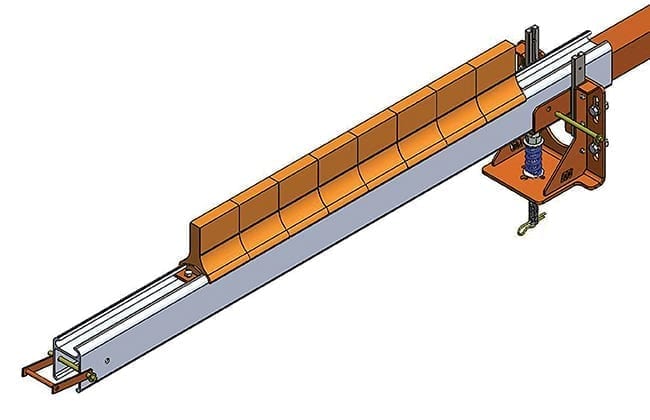
Figure 4. Track-mounted components allow fast replacement by a single worker. Diagram: Martin Engineering
Inspection doors
A tight seal is the key to preventing fugitive dust from escaping the transfer chute. Many current setups require workers to crouch or crawl under the system or even enter a confined space to inspect the chute or perform maintenance, which can increase the risk of serious injuries. Inspection of the system needs to be fast, easy and safe. Inspection doors — either solid or grated — can allow several observation points. Larger doors can offer access points with ample space for maintenance of specific parts that experience wear.
Real-world examples
The following examples of actual solids-handling operations show the difficulties that can arise with the maintenance of mechanical conveyors, and subsequent solutions to the problems.
Example 1: Dust issues. A west coast coal-handling operation was experiencing dust issues at one of its transfer points, so operators requested an inspection by outside experts. Starting at the top of the transfer zone, technicians initially saw no fugitive material. In fact, they found several access doors that had been cut into the chute by the company’s maintenance staff to allow inspection at various points. Then they noticed that the doors were all sealed with duct tape in an apparent attempt to avoid the cost of installing properly-engineered doors with tight-fitting seals (Figure 5).
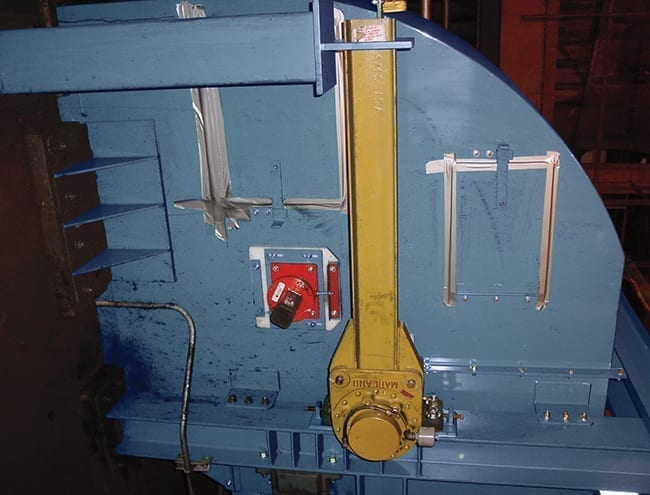
Figure 5. Duct tape can have drawbacks when used to seal access doors. Photo: Martin Engineering
Duct tape is a versatile tool, but it has some drawbacks when used to seal access points, a fact that was about to become readily apparent. The technicians had to see the material stream to evaluate the dust issue below, and while they were impressed by the ingenuity with which the access points were cut and sealed, that tape had to come off. The maintenance supervisor commented that he’d never had to do that, which was an indication that trouble might lie ahead.
The access door provided a good view of the material flow, but the opening allowed huge volumes of dust to billow out, forcing the technicians to quickly re-close the opening. In doing so, they were reminded why duct tape should never be used to seal an inspection door. When it was closed, the door latched properly, but a small gap remained around the edges, which undoubtedly prompted the use of the tape seal in the first place. The air that was now being forced out from that gap travelled at high speed, and carried with it a cloud of airborne dust particles. Unfortunately, the tape that had been removed was no longer sticky and could not be used to re-seal the gap. So the technicians were faced with a dense stream of black, flammable coal dust that essentially sand-blasted the team. It took only a few minutes for the supervisor to run downstairs and grab a new roll of tape, but they were some of the longest, most unpleasant minutes the men had ever experienced.
By the time he returned and re-sealed the breach, every square inch of the transfer house was covered in a 1/16-in. film of black powder. It looked like every surface had been painted black. To make matters worse, the air in the room was filled with a cloud of dust so thick that it was difficult to see, much less breathe. Coal particles covered ears, noses, hair, safety glasses and clothes, as well as tools and electronics. The group quickly made an exit, but they knew they would be tasting coal dust for days afterward.
Given the physical properties of the dust, the technicians also knew that they had just a day or two before it would begin to self-ignite. The supervisor was so concerned that he didn’t even order a cleanup crew to address the problem. Instead, the transfer house was evacuated, and he turned on the fire sprinklers. The entire mess was gone in about ten minutes, avoiding a potential fire or explosion.
A simple cost-saving decision made years ago to save a few dollars resulted in a series of events that could have resulted in a catastrophe.
What could have been done instead? There are well-engineered access doors designed for exactly this scenario, which would have allowed a quick inspection and immediate re-sealing of the opening simply by closing and latching the door. Even this modestly priced solution couldn’t compete with a dollar’s worth of duct tape, but reviewing the events revealed that the cost savings were an illusion. There were five people on the inspection team, including the supervisor, all of whom lost productive time dealing with the mess. When they realized that the situation had gone beyond any hope of manual cleanup, the transfer house had to cease operation for half an hour while the sprinklers washed down the area, forcing three more workers to evacuate until the dust was gone. That doesn’t include the cost of the washdown. That dollar’s worth of duct tape turned out to be an expensive “solution” after all.
Example 2: Equipment failures. A coal plant in Eastern China had belt damage, spillage and dust issues at two conveyor transfer points with outdated and inadequate equipment in the loading zones. Raw coal ore was loaded onto the 40 in.- (1,000 mm) wide belts traveling 500 ft/min (2.56 m/s). The first chute had a 16.5-ft (5-m) high drop chute that loaded into a 40-ft (12-m) long loading/stilling zone. The second chute had a similar drop, discharging into an 85-ft (26-m) long loading/stilling zone.
Like many facilities, new demands began to exceed the system’s design capabilities, which were originally intended for less tonnage and slower speeds. The belts were supported by impact idlers and a troughed roller system, neither of which were equipped to cope with new production demands. Equipment failures happened regularly, and without proper accessibility for routine maintenance, long periods of downtime were common. Belt sag created gaps between the belt and rollers, causing fugitive dust emissions throughout the facility. Inadequate impact control led to spillage becoming entrapped between the belt and tail pulley, damaging them both. Excessive downtime, costs for cleanup and equipment replacement seriously impacted plant production. Managers sought a solution that better protected the belt, sealed the chute from dust and spillage, and offered easier inspection and ongoing maintenance.
Technicians from an international service provider were invited to perform an on-site assessment and suggest an affordable solution. After offering a detailed proposal, the team installed modern equipment that addressed the issues on both conveyors even though they were of different lengths. The first chute was equipped with a track-mounted impact cradle to improve loading and protect the belt and tail pulley (Figures 6 and 8).

Figure 6. Track-mounted components deliver safe, easy access. Photo: Martin Engineering
In addition, slider cradles for smoother centering were installed, along with a full-length apron seal to prevent dust and spillage from escaping. A comparable solution was installed in the longer chute, with added cradle support down the entire length. Both chutes featured non-powered dust bag systems to collect emissions (Figure 7).
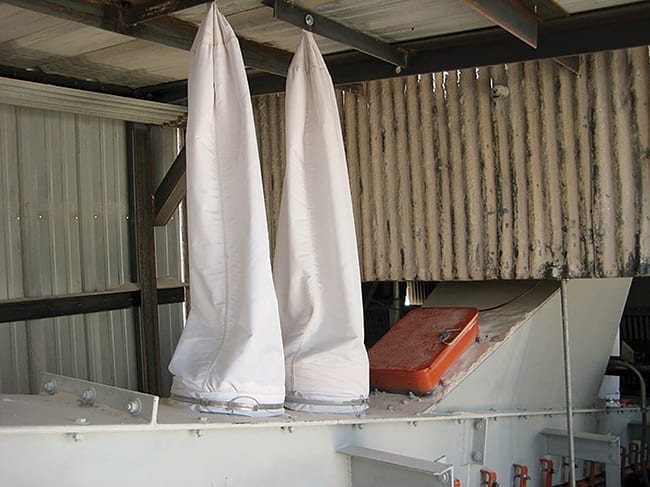
Figure 7. When the conveyor is running, the dust bags inflate, and a stoppage releases the dust back to the belt. Martin Engineering
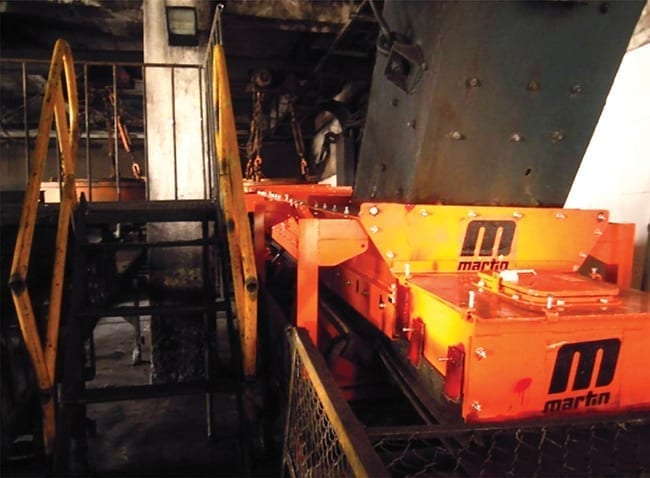
Figure 8. A hatch over the tail pulley allows plant staff to easily detect entrapped material. Photo: Martin Engineering
Since installation, spillage around the loading zones is under control. Dust emissions have been drastically reduced at the facility, measured at less than 3.5 mg/m3 within the immediate area surrounding the transfer points, and total dust is down to 10 mg/m3 throughout the facility. Operators report that a considerable drop in equipment failure rates has resulted in a substantial increase in plant productivity. Contributing to the success was workers’ ability to easily inspect and service components by sliding them out and servicing them outside of the conveyor. Managers say that workplace safety and the overall work environment have improved significantly.
Edited by Scott Jenkins
Reference
1. Conveyor Equipment Manufacturers Association, Belt Conveyors for Bulk Materials, 7th ed., CEMA, 2014, pp. 43–46.
Author
Daniel Marshall is a product engineer at Martin Engineering (One Martin Place, Neponset, IL 61345; Phone: 309-852-2384; Email: [email protected]; Website: www.martin-eng.com). Marshall has been working in the bulk solids industry for his entire career. A self-described “numbers guy,” Marshall joined Martin Engineering in 2000 as a research and development engineer, and has since moved into a product engineering role specializing in conveyor components and finally to a quality assurance position. Marshall has been instrumental in the design and development of transfer point accessories, conveyor components and safety products. He now ensures that Martin products are manufactured to the rigorous standards required by the demanding applications in bulk solids handling. Marshall has authored 36 published articles, presented at 17 different industry conferences and contributed to more than 100 press releases. He holds a B.S.M.E. from Northern Arizona University.