The distinctive properties of ionic liquids enable versatility and efficiency across many industrial applications
Ionic liquids — salts in a liquid state at ambient conditions — make up a fascinating family of materials whose unique physical properties have made them highly sought after for many challenging applications. Nearly all ionic liquids (ILs) exhibit extremely low vapor pressure, but the diversity of ILs give way to countless combinations of anions and cations that can provide desirable properties for a vast array of uses.
IL-based technologies are still rather new commercially. BASF SE (Ludwigshafen, Germany; www.basf.com) became the first company to apply ILs at an industrial scale when a unit operating its BASIL (biphasic acid-scavenging utilizing ionic liquids) process technology went onstream in 2004 at BASF’s Ludwigshafen site. Since then, industrial applications for ILs have greatly expanded. ILs are now used as industrial solvents, lubricants, additives and more. This article details some recent industrial applications of ILs where they promote efficiency and sustainability.
Alternative fuels applications
The pretreatment of lignocellulosic biomass, a challenging step in the preparation of biofuels, is an area where ILs have proven advantageous. Biomass of all types must be pretreated in order to isolate the most useful part — the polysaccharides that are converted into the sugars used in industrial fermentation processes. Conventional pretreatment processes can be expensive and energy-intensive, and in some cases, may actually have damaging effects on downstream microbes, enzymes and sugars. This is where ionic liquids become an attractive alternative.
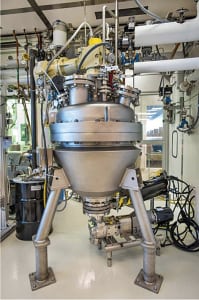
FIGURE 1. JBEI has scaled up biomass pretreatment technologies that utilize ionic liquids from the bench scale to the 100-L scale using a reactor located at the Advanced Biofuels Process Demonstration Unit (ABPDU)
The Joint BioEnergy Institute (JBEI; Emeryville, Calif.; www.jbei.org), in collaboration with the Advanced Biofuels Process Demonstration Unit (ABPDU; Emeryville, Calif.; www.abpdu.lbl.gov), has been working extensively to develop biomass-conversion processes that effectively utilize ionic liquids ( Chem. Eng., Sept. 2013, p. 15), with an emphasis on process optimization and unit-operation consolidation. JBEI has previously reported the creation of a single-vessel process that combines pretreatment and saccharification into one step, decreasing water input and waste generation. Now, in collaboration with the ABPDU, JBEI has turned its focus to scaleup, demonstrating IL-based pretreatment at the 100-L scale (Figure 1). Furthermore, according to the group, in a separate activity, a company has demonstrated IL pretreatment at a scale capable of processing one ton per day of biomass.
With these progressively larger demonstrations, Blake Simmons, JBEI’s chief science and technology officer, is optimistic about the prospects of positioning this technology as an economical alternative to other commercial pretreatment methods. “We are very confident that in the near-term, say two to three years, we will be able to generate an IL conversion technology that can compete on a cost basis and outperform current technologies,” says Simmons. The industry has taken notice of this work, as Simmons cites several companies that are funding collaborative projects across many applications, including fuels, chemicals and materials.
One key to optimizing the process is narrowing down the best ionic liquid for the job. According to JBEI, among the thousands of known ionic liquids, less than 50 have been shown to be effective for biomass pretreatment. “The selection of the anion and cation dictates how they interact with the principal components in biomass: lignin, cellulose, and hemicellulose,” explains Simmons. ILs can be tailored for specific process requirements to selectively interact with biomass components, resulting in the perturbation of the plant cell-wall structure. JBEI has found that imidazolium-based ILs are particularly suitable for disrupting the plant wall and interacting with the various biomass components, making them an effective choice for treating a large variety of biomass feedstocks. “You can equate this to how other solvents can selectively solubilize a wide range of polymers,” says Simmons, “after all, lignin, cellulose and hemicellulose are simply polymers that are produced by nature.”
In investigating numerous varieties of ILs for pretreatment purposes, JBEI also began to look into some novel ways to synthesize ionic liquids, specifically from bio-based materials, especially since the costs to procure and recycle ILs are among the major challenges the group faces for industrial scaleup. The group has developed two renewable ionic liquids (“bionic liquids”); one derived from hemicellulose, and one derived from lignin. Lignin, typically viewed as a waste stream, is an especially attractive raw material for the production of bionic liquids.
To synthesize ILs from lignin, first, the lignin must be depolymerized into monomers. The monomers are then functionalized via standard chemical routes to generate aldehydes and alcohols, representing the cation portion of the resultant IL. The anion portion comes from phosphoric acid used in the process. These renewable ILs, says Simmons, are “comparable to the top-performing conventional ILs.” Since lignin and residual amounts of hemicellulose are both byproducts of biomass pretreatment, a potentially closed-loop pretreatment process is possible. The bionic liquids not used for pretreatment can be sold to other markets, providing another source of revenue. The development of a renewable, efficient biomass-pretreatment process will help to bridge the gap between bio-based chemicals and fuels and their petroleum-derived counterparts.
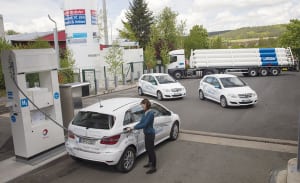
FIGURE 2. Linde is employing its ionic compressors at hydrogen fueling stations in several locations, including this Geiselwind, Germany site, opened in May 2015
Like biomass, hydrogen gas is poised to become an alternative fuel source, specifically in the automotive sector. The Linde Group (Munich, Germany; www.linde.com) is at the forefront of this movement, opening hydrogen-fueling stations in California, Austria and Germany (Figure 2) in the past year. One very distinctive component of these modular stations is the company’s ionic compressor, where ILs behave like mechanical pistons. Non-volatile and nearly incompressible, the ionic liquids used in these compressors provide corrosion inhibition and lubrication, and do not contaminate the hydrogen gas. Linde specially designed the IL for the compressors, seeking out a material that would not mix with hydrogen gas. This renders seals and gaskets unnecessary while providing efficient compression.
Acting as reciprocating pistons, the motion of the IL columns within the five-stage compressor serves to compress the hydrogen gas nearly isothermally, with almost no mechanical wear. According to the company, energy savings of around 40% are achieved with the use of ionic compressors versus those containing traditional pistons. Hydrogen can be compressed from a minimum of 5 bars inlet pressure to a maximum of 1,000 bars outlet pressure, says Linde. A coalescer on the outlet of the compressor allows for the ILs to be recovered and recycled. With construction underway on many new hydrogen-fueling stations, Linde will continue to commercially deploy ionic compressors as hydrogen becomes a more widely used fuel source.
Longterm solar-power supply
ILs are also becoming prevalent in the solar-energy sector. Merck KGaA (Darmstadt, Germany; www.merckgroup.com; www.emdgroup.com) has been developing electrolyte mixtures for dye-sensitized solar cells (DSSC), where ILs dissolve the electrolyte redox system (consisting of iodine, iodides and additives). DSSC systems employ electrolyte mixtures to facilitate efficient charge transport between the cell’s electrodes. Merck commends ILs’ “special properties” for instilling stability and longterm service life into DSSCs. “One reason for the long lifetime is the negligible vapor pressure of ionic liquids. Hence, there is no mechanical stress on the sealing or electrolyte evaporation when the cells heat up in the sun,” says Hannah Bürckstümmer, strategic marketing manager, Photovoltaics within Merck’s Performance Materials business sector. Low viscosity was also extremely important in creating the company’s proprietary IL, as conventional electrolyte systems are usually quite low in viscosity. However, a solvent-based DSSC system, while highly efficient, is very volatile and has a shorter lifetime than electrolytes based on ILs. “Evaporation of the electrolyte is a key failure mode. For products with lifetime requirements of several years, experts see electrolytes based on ionic liquids as the best alternative,” explains Bürckstümmer.
According to Merck, there are several market sectors where DSSCs are ideal. DSSCs can be used in low-light or indoor environments to supply power for small, non-wired devices like sensors, since they work efficiently and provide very high power densities. They are an attractive option for architectural structures, as well, since they can be made semi-transparent and the color can be adjusted (Figure 3). Here, they can serve simultaneously as a power source and a design element, says Bürckstümmer.
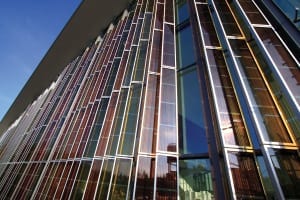
FIGURE 3. Dye-sensitized solar cells are highly efficient energy sources that can be implemented into glass units on architectural structures. Merck’s work in introducing ionic liquids into DSSC systems has helped to increase the possible service lifetime of these devices
Natural-gas purification
ILs are also being positioned as a valuable material for natural-gas purification processes, including carbon-capture. In a project funded by Petronas (Kuala Lumpur, Malaysia; www.petronas.com.my), researchers from the Queen’s University Ionic Liquids Laboratories (QUILL; Belfast, Northern Ireland; www.quill.qub.ac.uk) have investigated the use of various ILs for the capture of carbon dioxide (CO2) from natural gas (Figure 4). Typically, CO2 removal involves the use of corrosive and volatile amines, but the alluring physical properties of ILs offer many advantages. For instance, ILs boast very high stability, and they exhibit negligible vapor pressure under typical process conditions. Also, unlike amines, there is little risk of corrosion occurring due to the presence of ILs.
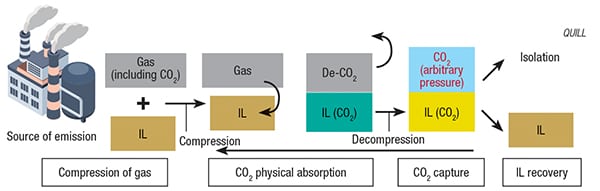
FIGURE 4. A proposed IL-based carbon-capture system has many benefits over conventional absorption processes
QUILL’s research investigated various IL formulations, some containing water, for their CO2-capture capabilities at the CO2 partial pressures typically found in submarine natural-gas sources. As in other applications utilizing ILs, selection of the proper cation and anion was of utmost importance. Focusing on ILs with carboxylate anions, QUILL sought to maximize CO2 absorption on the basis of solvent volume and weight. IL basicity was another key design factor. The team also found that formulating the IL solvent with a nearly equimolar volume of water enhanced the CO2 solubility, as water participates in the chemical mechanism of the process and slightly decreases the viscosity of the IL-water formulation.
After examining numerous IL formulations, QUILL’s studies indicated that tributylmethylphosphonium propanoate was the most viable IL candidate for CO2-capture processes. The team worked with the U.K. branch of engineering consultancy company WorleyParsons Ltd. (North Sydney, Australia; www. worleyparsons.com) for an in-depth analysis of the IL-based CO2-capture process, and their findings indicated that, when compared with one of the most effective conventional CO2 absorption processes (containing activated methyl diethanolamine), the IL-based process (utilizing tributylmethylphosphonium propanoate), actually had lower operating costs. Added bonuses were reduced heat input, the absence of corrosion and equivalent selectivity and stability. According to QUILL’s Natalia Plechkova, the process has been demonstrated at both laboratory and semi-pilot scale, and two patents have been filed as a result of the research. The next steps for scaleup, says Plechkova, will be to reduce the viscosity of the system and to change existing equipment to adapt to the new ionic liquid technologies. These findings are especially significant to the natural-gas industry, due to the restrictive regulations surrounding amines in some parts of the world.
Scientists from QUILL were also involved in the development of HycaPure Hg, a now commercialized technology that applies ILs to remove mercury from natural gas streams. The HycaPure process was developed in partnership with Petronas, which has been operating the technology at commercial scale in its own facilities in Malaysia since 2011. In 2014, Clariant (Muttenz, Switzerland; www.clariant.com) signed a marketing license agreement for the technology to expand its reach internationally.
Naturally occurring in many hydrocarbon streams, mercury is a toxic contaminant that can cause corrosion and embrittlement in process equipment, and can generally degrade the quality of the product. Its presence also poses considerable exposure risks to workers. HycaPure Hg technology is said to capture all mercury species (organic, inorganic and elemental) that are present in natural gas streams, with a capacity three times higher than competing commercial mercury-removal methods, such as those containing activated-carbon materials, sulfides or silver. The HycaPure Hg process benefits from its kinetics — reportedly 10–20 times faster than other mercury-removal technologies — enabling it to handle fluctuating mercury content, particularly the large spikes in mercury concentration that could be damaging to downstream processes if not properly mitigated. Furthermore, the non-volatile nature of ILs proves valuable here, as there is no risk for inherent contamination of the gas during the mercury- removal process.
In laboratory tests examining the solubility of mercury in ILs — in this case, a chlorocuprate-based IL — QUILL observed that ILs in their fluid form could be applied to a mercury scrubber. However, the viscosity of the IL system would render it impractical for industrial scaleup. Therefore, a supported-ionic-liquid-phase (SILP) structure, wherein thin IL films are incorporated on a porous solid media, was proposed for use in a fixed-bed scrubber. The SILP format provides adequate contact between the IL and the gas stream, and also imparts mechanical strength.
Petronas took this technology from the laboratory to a gas-processing plant in Malaysia, and demonstrated that, even at commercial scales, the process resulted in natural gas streams that were significantly lower in mercury content than required sales specifications. According to QUILL, HycaPure Hg systems can be directly retrofitted into commercial plants, and the increased mercury-removal capacity can result in lower operating costs. QUILL emphasizes the remarkable nature of HycaPure’s rapid commercial implementation, transitioning to commercial operations in less than four years.
Saving energy in catalysis
A notable feature of ILs is their ability to alter the behavior of other materials in their presence. Evonik Industries AG (Essen, Germany; www.evonik.com) has been taking advantage of this trait in the development of advanced SILP catalysts. In June of this year, Evonik announced an industry-first achievement, demonstrating that SILP catalysts can run reliably in a pilot plant for over 2,000 h, proving commercial viability.
Essentially, this SILP catalyst technology can make homogeneous catalysts — which are highly active and very selective, but can require energy-intensive downstream separation and recovery — behave more like their easier-to-handle heterogeneous counterparts. In a SILP system, the homogeneous catalyst can be dissolved into a solution. This allows the catalyst to be applied to solid materials, eliminating downstream separation requirements.
For the development and application of SILP catalysts, Evonik has been focusing on the hydroformylation reaction, a common industrial reaction that converts olefins and syngas into aldehydes. Hydroformylation reactions traditionally employ a homogeneous cobalt or rhodium catalyst that becomes dissolved in the reaction mixture, necessitating costly separation and recycling steps. According to Evonik, since there is no known heterogeneous alternative for hydroformylation catalysts, this process is a prime candidate for SILP catalysis technology.
As in other IL-based applications, the ability to manipulate the cation and anion of the IL provides the flexibility to optimize the IL for the specific application. Evonik, along with researchers from the University of Erlangen-Nuremburg (Erlangen, Germany; www.fau.eu), began seeking out different IL anion-cation combinations to best adapt the SILP catalyst for hydroformylation. Also crucial was determining the most appropriate ligand for the catalyst. Many compounds were screened as the team targeted the optimal IL solubility, which, says Evonik, had to be high for the catalyst and low for the end product (so that no separation would be required to recover the catalyst materials).
From this work, the best candidate SILP catalyst consisted of a rhodium complex and a ligand based on polycyclic anthracene triol. The IL had an imidazolium cation and a binary amine anion. This was the SILP system that was used in the milestone 2,000-h demonstration. In addition to the intrinsic benefits of making the homogeneous catalyst easier to manage, Evonik also reports that in pilot-plant demonstrations, SILP operations resulted in a greater than 2% reduction in CO2 emissions when compared with conventional hydroformylation processes, and that the metallic portion of the catalyst could be recycled.
Looking forward
Even as the use of ILs in industrial applications becomes much more widespread, there are still some challenges, mainly stemming from the cost in procuring some ILs in large-enough volumes for commercial-scale operations, and also in the sheer number of ILs that can be synthesized. As reiterated in this article, the ability to “tailor” ILs with the optimal cations and anions for a particular application instills great flexibility in process development. It also introduces some daunting challenges in process development, as it is infeasible for researchers to test literally thousands of anion-cation combinations. This is where predictive modeling tools will increasingly become important to narrow down the field of potential ILs for a particular process. As these tools become more robust and mainstream, it will certainly aid in expediting the development of future IL-based technologies. ■ Mary Page Bailey