Enhancing data management using LIMS software provides enhanced product-development opportunities
Accurate and efficient data management is key to productive and collaborative working practices, yet recording, storing and analyzing large quantities of laboratory data can be challenging. With many laboratories using disconnected systems and data often stored in siloed locations, numerous organizations face inefficiencies in their processes, a lack of collaboration and manual data transcription, increasing the risk of errors.
Implementing laboratory information-management system (LIMS) software, as part of a digital transformation strategy, can overcome data management challenges and bring many other benefits. Data output from instruments can be recorded directly, improving accuracy and increasing process automation (Figure 1). These high-quality data are stored centrally allowing easier collaboration between stakeholders. And the availability of data for further analysis means crucial insights can be more readily identified. Potential benefits include increasing productivity, reducing costs and driving optimization and research through improved connectivity and collaboration.
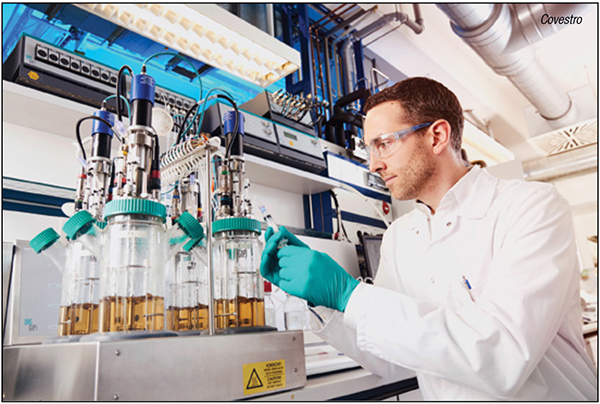
FIGURE 1. With a laboratory information management system, data outputs from instruments can be recorded directly, improving process automation
Covestro AG (Leverkusen, Germany; www.covestro.com), a global producer of high-performance materials, has successfully introduced Thermo Scientific SampleManager LIMS software (Thermo Fisher Scientific; Waltham Mass.; www.thermofisher.com) in 21 laboratories over 10 sites, involving around 1,700 people. We examine how their data management approach has changed, their experience of implementing SampleManager LIMS and the benefits they have observed.
Data management challenges
Collection of data is important across both Covestro’s research and development (R&D) and production environments, and data need to be shared between these groups. Before the implementation of a LIMS, data were input manually, often into shared spreadsheets, an error-prone, labor-intensive process that resulted in data siloes. Information was then communicated by phone from the laboratory to the production line. Subsequent analysis occurred only on a small scale, and data for an entire process were not considered holistically or retrospectively, so trends and potential opportunities for optimization could be missed.
The potential of a LIMS
After much consideration, Covestro identified a LIMS to streamline data management as a crucial part of their digitalization strategy. By integrating instruments with the software, data entry and storage would be automated, bringing improvements in efficiency and accuracy.
LIMS allow data to be standardized and harmonized. No matter what its source, the underlying database remains the same, so meaningful comparisons and extrapolations can be made. This enables easier collaboration and analysis, with the data able to be used and reused to inform current and future projects. For example, data can be used to monitor processes and identify trends to inform optimization, and act as feed for R&D projects. Ideas “hidden” in these data could be the key to the new products or processes of the future. As Frank Wahl, project manager R&D Solutions at Covestro, who was responsible for the implementation of SampleManager LIMS, says, “The data of today are the raw materials of tomorrow.”
Practical implementation
Introducing any new technology, including a LIMS, requires effective change management and company-wide participation to smooth the process. Wahl explains, “Involving different teams in discussions throughout the implementation process reduces the time taken for staff to go from opponents to proponents of the new system.”
Thermo Fisher’s professional services team was instrumental in guiding the process, working closely with stakeholders at Covestro to suggest the best path forward for the implementation. Taking a consultative approach, the team looked at all processes within the scope of the project to determine the best way to configure the LIMS to fit Covestro’s laboratory workflows. Their focus was on configuration over customization to achieve a more future-proofed solution that would be easier and less costly to support and maintain.
Wahl explains, “The significant experience of Thermo Fisher’s team with interfaces to SAP’s Enterprise Resource Planning and other third-party systems helped us integrate SampleManager LIMS tightly into the existing Covestro infrastructure, easing the transformation process and ensuring that existing best practice was maintained. We were able to incorporate the specific requirements of individual laboratories with relatively low effort.”
During the initial phase of implementation, there were some hurdles and, according to Wahl, “It took time for this ‘activation energy’ to be overcome.” However, as staff learned about the new system, they could see how it positively impacted their roles and confidence grew. For example, the removal of manual data input and transfer reduced their administrative workload, allowing more time for scientific tasks. Any concerns disappeared within a few months, and they began sharing and discussing suggestions for optimizations. Later, the broader benefits to the company, including increased productivity, were also clearly recognized and their contribution to this reinforced the team’s positive experience.
By the end of the implementation process, Wahl noted, “You have a great product placed in the laboratory and our scientists now rely on it.” At Covestro, there is now full confidence in the system and staff consider SampleManager LIMS to be integral to their work.
Benefits of LIMS for Covestro
After the implementation, Covestro realized a number of benefits, including time and cost savings. As a direct result of integrating the LIMS with instrumentation, skilled laboratory staff no longer spend time inputting and sharing data (Figure 2). Instead, data collation is automated in a central database that is readily accessible to all who need it. And when decision-making is required, this is better informed by all the available data.
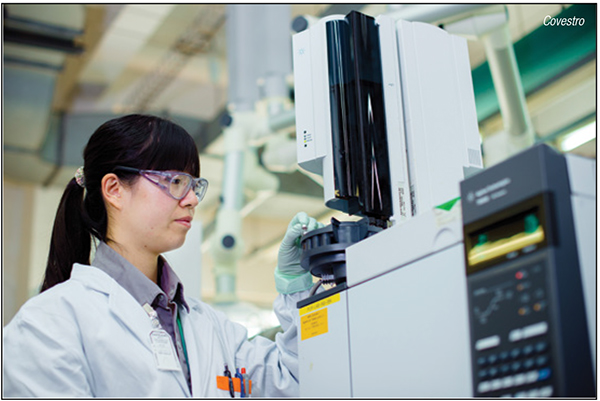
FIGURE 2. After integrating the LIMS with instrumentation, skilled laboratory staff no longer spend time inputting and sharing data
When data are needed for a project or to develop an idea or process, this may already exist and be stored in the system so time and effort is not spent on duplication. As researchers can see all available data, they can focus on areas where there are gaps, meaning research efforts are better focused. The availability of high-quality “big data” alongside advanced analytics allows trends to be studied — for example, the effect of weather on processes. The synergy between different parts of the business, such as R&D and production, is maximized.
The benefits of the SampleManager LIMS introduction have been felt throughout the company. Wahl comments, “Thermo Fisher’s configuration-over-customization approach has allowed us to standardize and harmonize our LIMS landscape, as SampleManager LIMS is introduced into more laboratories.” And those without SampleManager software are now requesting it, with implementation in more sites scheduled to begin in 2022–2023.
Concluding remarks
The implementation of an integrated LIMS is pivotal to any digital-transformation strategy. With vendor support and stakeholder involvement, the best configuration of the LIMS can be built to standardize and streamline processes, reduce manual interactions and connect instruments to provide a complete flow of information from research through to production.
This automated digital data management saves time and improves accuracy, which benefits laboratory staff and drives process optimization while increasing productivity. What’s more, due to the standardized format of the data, maximum value benefits can be obtained through its analysis, across the company. Scientists can now use existing data in new projects rather than collecting it again, avoiding redundancy. Further study using advanced analytics can help generate new ideas or uncover potential product development routes that before might have stayed “hidden” in existing data. The introduction of LIMS software has led to long-term gains for Covestro and demonstrates how LIMS can be implemented to bring company-wide benefits.
Authors
Frank Wahl started his career working as a laboratory technician for almost 17 years at Bayer AG, which later transformed into Covestro AG (Kaiser-Wilhelm-Allee 60, Leverkusen, Germany, 51373; Email: [email protected]). Following his interests, Wahl moved into a position as R&D IT project manager, taking over as project lead of several local and global IT projects. One of these projects was the first Thermo Scientific SampleManager LIMS implementation for Bayer in 2008, which then developed into a companywide implementation program, including the implementation of more than 20 instances of SampleManager LIMS globally. In his current role as R&D Solutions Manager, Frank continues to manage the LIMS as well as other digitalization projects within Covestro.
Christian Mueller joined Thermo Fisher Scientific Inc. (168 Third Avenue, Waltham, MA 02451; Email: [email protected]) in 1998 and has since held various responsibilities within the Digital Science business unit as a project manager and a services manager for the Germany region. In 2020, Mueller was promoted to the director, Service and Support, for the EMEA (Europe, the Middle East and Africa) region. Prior to joining Thermo Fisher Scientific, Mueller worked as a laboratory lead for an environmental laboratory. Mueller is a chemist with a doctorate from the University of Essen, Germany.