Taking a modular approach to capital projects offers a pathway for companies to be proactive, rather than reactive, as they manage project risk in the time of COVID and potential similar disruptions in the future
It has been more than a year since the COVID-19 global pandemic took center stage, and the uncertainty engendered by it has impacted every person on the planet. The disruption of the pandemic precipitated a cascading series of changes observed across nearly every industry. It was no longer business as usual. Although the chemical process industries (CPI) are familiar with the cyclical nature of the markets into which they sell, for the first time, the CPI faced a paradox: how to continue to execute projects on time and on budget, while keeping contractors, employees and operators safe in the midst of a public health crisis. The need to address this issue applies not only to current projects in the time of COVID-19, but also to future projects, which may face unknown and unanticipated risks from forthcoming health crises, natural disasters or other widespread disruptions. This article provides information on how modularization can help manage project risks in the new environment in which CPI companies now find themselves.
COVID-19 response
In a matter of weeks after COVID-19 was first identified, both plant owners and engineering, procurement and construction (EPC) firms alike were implementing stay-at-home orders and sending employees home to work virtually to ensure their safety and help slow the spread of disease. Even prior to the pandemic, many in the CPI were already familiar with virtual team environments, simply from having to manage project teams across various geographic regions to facilitate work sharing. So in some ways, companies were well positioned remotely and virtually executed design- and engineering-related work. Even as the percentage of remote workers rose and strained the information technology (IT) infrastructure, the CPI answered the call successfully.
However, neither “greenfield” nor “brownfield” projects can be physically constructed in a virtual environment. The same challenges brought on by the procedures designed to ensure that workers remained safe also began to materially impact construction projects, particularly those employing traditional stick-building construction strategies. Addressing these challenges directly impacted the CPI’s collective ability to deliver projects safely. As a result, schedules and budgets started to slip.
Health and safety risks became the primary constraint on continuing project execution and field operations. Fairly abruptly, companies’ focus shifted from reducing workplace hazards to managing workforce COVID-19 exposure and infection rates. There was a widespread feeling of community and social responsibility to prevent community spread of the virus. A number of health and safety preventative measures are now common practice, and many have become normalized, including social distancing, additional personal protective equipment (PPE), pre-work measurement of body temperatures and staggering lunch breaks and work shifts to reduce gatherings and exposure.
Incorporating these new policies and procedures impacts the engineering and planning components of project delivery in several ways, including the following:
- Construction challenges
- Completion date slippages
- Critical work activities extended
- Deferred startups and commissioning activities
- Extension of project schedule
- Flattening of expenditures across the project duration
- Lower levels of project productivity
In addition to the onsite challenges, few anticipated the extent to which global supply chains were disrupted in the wake of the pandemic. Supply chain disruptions, in turn, had cascading effects that led to the following:
- Schedules and project scopes requiring rework
- Shifting priority to projects that could deliver immediate return on investment (ROI)
- Shifts in the pipeline of planned projects
- Delayed final investment decisions
- Projects being revisited and re-evaluated
- Reductions in capital expense (CAPEX) budgets
- Delays in project approvals
In light of these new challenges, realization took shape that the advantages and benefits inherent to modular construction strategies could help mitigate many of the project-delivery risks that arose with COVID-19. While it is true that, even with modular construction approaches, physical projects cannot be accomplished virtually, it is also the case that modularization could help companies adapt to many of the supply-chain, project-scheduling and health-safety issues associated with the pandemic. In fact, modular construction has always provided some of these benefits.
Modular construction defined
Modular construction of process systems can be defined as complete process units that are prefabricated at an offsite, specialized, indoor, modular assembly shop to the maximum extent possible.
Truckable modular systems, as an example, are built in such a way that they can be transported across states and countries by trailer truck (Figure 1). The modules are supported by a structural steel frame, which serves not only as the support system for the equipment during shipment, but once installed, allows for a safe passageway via access platforms to operate.
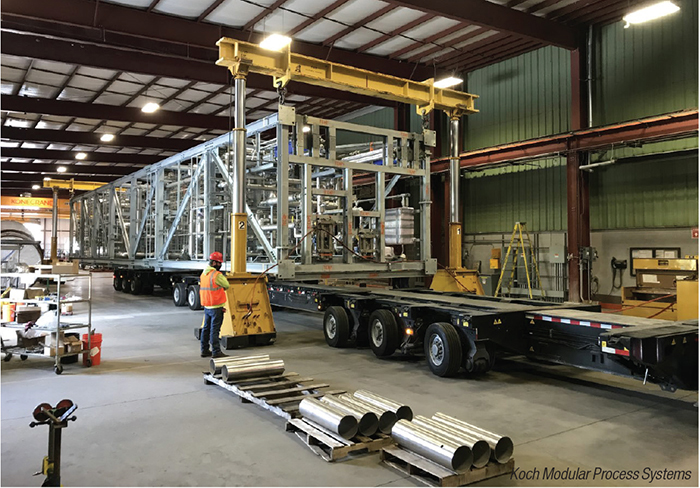
FIGURE 1. The truckable process module shown here is being readied for transport to a project site
In general, building systems under controlled indoor environments minimizes field construction labor by up to 90%, and mitigates the inherent risks associated with field construction.These legacy benefits of modular construction align well with addressing concerns surrounding project execution during COVID-19 or another similar disruption in the future.
Delivery, installation and startup
Given that many truckable modular-process-unit providers are experienced in the delivery of their modules to owners’ sites — both domestic and globally — delivery is included in the overall scope of modular construction, in most cases. In preparation to receive modules onsite, the facility owner’s onsite construction contractor will prepare the foundations where the modular systems will be set upon arrival. The foundations are prepared based on foundation load drawings provided soon after the purchase order for the modules is prepared (Figure 2).
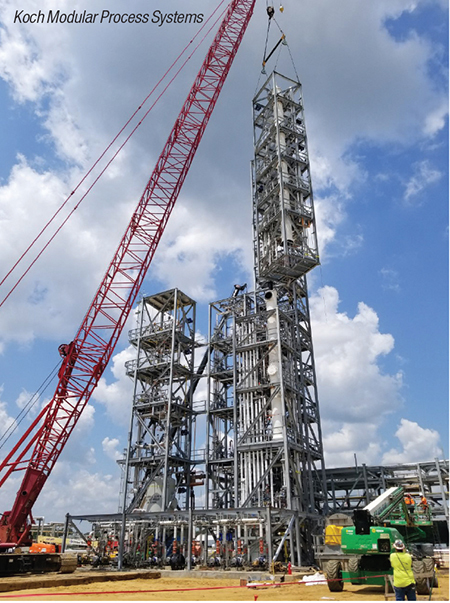
FIGURE 2. Once delivered to a project site, truckable modules are set on pre-made foundations
Depending on the number of process modules comprising the overall project and the overall onsite project construction completion status, modules can either be received onsite all at once, by staggered shipment or received and set on temporary supports in the laydown yard. Typically, smaller projects comprised of one, two or just a few modules can be received and set in a single day. Larger projects comprised of a series of modular systems will have delivery staggered over the period of a few weeks.
Once the modules are in place and all interconnecting spools have been installed, the process units are connected to the outside battery limits (OSBL) utilities, feed piping and product pipelines. After the completion of a field-readiness checklist, a mock startup is performed using water. It is important to do a water startup prior to introducing chemicals into the process units to ensure all instrumentation and equipment is working properly. This reduces potential exposure to hazardous chemicals. Once the system has been validated using water and controls have been adjusted in the control room, the plant is ready for full commissioning and startup with the process chemicals. Depending on the size of the plant, typically one or two engineers, plus an operator, are required during startup. This allows for operator training, while also ensuring that the unit reaches steady-state operation in a smooth matter.
With approximately 90% of the overall construction activities transferred to the modular assembly contractor, onsite installation, startup and commissioning activities are typically shortened from months to weeks, and onsite construction personnel required to support project scope is drastically reduced. Furthermore, associated costs related to onsite cranes and other rental equipment can be minimized, because they can be planned for use on site only when modules are being received and installed upon their foundations.
Modularization benefits
The benefits of modular construction that were recognized even before the global pandemic have only become amplified in the years 2020–2021. These benefits can be divided into three main categories: completion; contractual and commercial; and project risk mitigation. Included here is a list of benefits, some general and others more specific to COVID.
Completion. The benefits of modular in the area of construction completion include the following:
- Increased productivity, quality, and safety at the indoor modular assembly shop. The step-by-step, assembly-line method of construction allows for predictable procedures, reduces the risk of injury to personnel and improves overall product quality
- Minimized interruption to the owner’s site operation resulting from offsite fabrication and assembly, along with short times onsite for installation, startup and commissioning activities
- Significant schedule improvements over traditional stick-built projects
- Better labor availability. Assembly shops have a more stable workforce and do not experience the typical personnel turnaround that is seen with pulling stick-built construction crews together for each project
- Continued off-site fabrication during site-permitting activities
- Smaller workforce equates to less non-productive time spent performing the newly necessary pre-work health screening
- Controlled work environment contributes to higher productivity in inclement weather
- The ability to shift fabrication to multiple assembly shops in locations with low COVID-incidence rates. Modular construction allows you to change the fabrication site to areas with lower case rates, something that could not be accomplished with a stick-built approach
- Mitigated labor availability disruption by minimizing workforce exposure and infection in these controlled environments
- Maintained productivity during a pandemic mitigates schedule extension
The owner of the plant is able to see significant improvement in overall project execution when activities are performed in a parallel fashion, versus when performed sequentially. Modularization allows the end-user to focus on activities such as acquiring necessary permit approvals from local municipalities, without causing delay in the design and construction of the process units, normally ongoing in the modular shops already. This is one example of how schedules are shortened, with the modules ready for shipment within 10 months of kicking off the project. This is, and has always been, very difficult to accomplish with stick-built construction.
Contractual and commercial benefits. Modular construction has always delivered contractual benefits and risk mitigation. This has not changed during the pandemic, but the approach is being looked at with fresh eyes. A third-party modular systems provider will assume fabrication and delivery risk of the completed modular system, taking on much of the project delivery risk. This transfers some risk from the facility owner to the contractor. There is also a definitive estimate, and fixed price scenarios, which can provide overall cost savings.
Additionally, maintaining contract performance requirements is paramount for the successful execution of a project. By minimizing workforce exposure, infection rates and supply chain disruptions, plus maintaining labor availability, modular approaches enable a smooth process for execution and fabrication.
On the contract side, there is a risk reduction on force majeure, suspension of work, and stop work order. On the commercial side, the risk of increased project costs related to extended performance and legal costs and contract penalties are reduced.
Project risk mitigation. When considering a modular execution model over stick-built construction, various project delivery risks can be mitigated through modularization. This has always been the case, but when viewed through a pandemic lens, it highlights certain aspects even more clearly.
While a typical stick-built construction site workforce could require hundreds or thousands of individual workers, an indoor modular assembly shop may average under 100 workers in one location. This allows for the following:
Assembly line fabrication methodology that equates to smaller workforce density (Figure 3)
- Overall smaller shop workforce population
- Smaller field size population
- Controlled environment, which offers greater PPE comfort and higher compliance
- Shorter exposure duration
- Local and consistent workforce that minimizes potential community spread
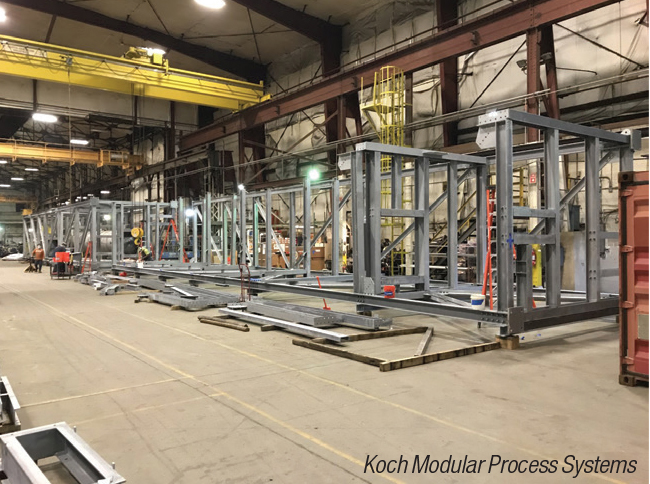
FIGURE 3. Modular process equipment can be put together in an assembly-line fashion, which allows lower workforce density
Preparedness for project risk
Preparation is key to helping minimize project risks as the industry continues to adapt to this ever-changing landscape. The pandemic highlighted some weaknesses in the marketplace that can now be addressed in cases where similar circumstances develop in the future. For example, there are some steps that owners can take early on during the planning of a project that allows for a more proactive execution.
These include the following items:
- Performing risk assessments on future projects to include likelihood of an epidemic or pandemic
- Understanding local permitting timeframes
- Close collaboration between the engineering firm and module supplier to identify bottlenecks early in the planning phase of the project
- Identifying site workforce availability to minimize bringing workers from outside the local geographic area
- Soil testing and subsequent foundation preparation and construction
- Identifying potential lay-down areas if required
- Securing supply chain early in the project to minimize impact of a heated market premium
Old problems; more challenges
CPI companies have overcome many obstacles in the last few decades, such as the financial crisis of 2008, and the global recession of 2014. Many could say that the problems faced during the pandemic were simply old problems in a new global landscape, but the numbers tell a different story. This single event is still causing unique challenges in the industry. According to Industrial Information Resources (Sugar Land, Tex.; www.industrialinfo.com), the pandemic has directly impacted more than 7,000 projects globally worth $556 billion. Specific actions were announced throughout the industry. For example, Fluor Corp., one of the largest EPC players in the industry, announced its exit from competitive EPC lump-sum bidding in 2020 on its full-year 2019 press release. Key reasons driving this decision were the increased project risk, the transactional marketplace, and ultimately, the market uncertainty driven by the COVID-19 pandemic.
And although many of the challenges are common in the industry, such as extension of project schedules, lower levels of project productivity, CAPEX budget cuts and so on, the reality is that these current challenges “feel” different. It is the first time in over 100 years that the industry is fighting with a new and possibly fatal pathogen on such a widespread basis. EPC activities will continue to be impacted, but companies will continue to adjust. Perhaps the best lesson is better preparation.
The positive news is that owners can take steps early on during the planning of a project that allows for a more proactive execution. Preparation is key to help minimize project risks as the industry continues to adapt to this ever-changing landscape. The pandemic highlighted some weaknesses in the marketplace that can now be addressed in case similar circumstances develop in the future.
As mentioned earlier, there are some key steps that owners can take early on during the planning phase of a project. These steps range from performing risk assessments on future projects to include the likelihood of an epidemic or pandemic, to securing the supply chain early to minimize the impact of a heated market premium. Also, understanding local permitting timeframes highlight the importance of strong contractor relationships. Taken together, these steps allow for a more proactive and risk-mitigated project execution.
The path forward
The reality is that nobody can predict when the pandemic will be over, if it will be the last one our industry will face or what the new steady state will be five years or even ten years from now. What is clear is that the industry needs a project-execution model that enables projects to continue to be delivered successfully and safely in challenging environments. Modular construction can help level the playing field due to its adaptive nature.
Modular assembly shops also continue to mitigate the impact of the pandemic. Executing a project in this fashion allows for continuous operation at the owner’s facility with minimum interruption, which is possible while maintaining the proper health and safety measures.
Ultimately, modularization can serve as a potential risk-mitigation approach as the industry adapts to what will be the new normal. While it would be simplistic to say that modularization is the silver bullet to the COVID-19 pandemic’s ongoing challenges to the delivery of projects, modular construction, together with other project-risk-mitigation measures, can and has played a significant role in enabling projects to continue safely and effectively. It should be considered as a viable alternative, both in the current situation and into the future.
The pandemic highlighted weaknesses in the marketplace that can now be addressed in anticipation of similar circumstances in the future, which in light of history and public health research, will very likely occur.
Impact of COVID-19 during Fabrication: An Ammonia Recovery System Case Study Example
This case study concerns a modular construction project that had kicked-off six months prior to the quarantine mandate in the northeastern U.S.
The project involved an ammonia recovery system that included three truckable process modules and one stair tower (Figure 4). The project schedule was 49 weeks, including process development, detailed engineering, procurement, fabrication and shipping to the client’s site. When COVID-19 hit, the project was at the beginning stages of the modular assembly phase: process design and detailed engineering was complete; structural steel nearing galvanizing; equipment and instruments were approaching readiness for shipment to the modular assembly shop; and the modular assembly contract was already awarded.
Supporting the project from home offices, rather than a company office setting, became the first challenge. During this time, most individuals had to continue their work activities from home. One of the first advantages of modular construction that came to light is that the construction staff did not change, and the relationship of the project manager with the selected assembly shop had been established for years prior to the pandemic. This would have been a very different situation for a stick-built project, where workforces are mobilized from different parts of the country.
Using technology resources to connect with and manage resources, such as video conferencing, email, and phone calls, allowed for a smooth transition and efficient, effective communication.
A vendor responsible for delivering three vessels that would go into the modules confirmed that the vessels had been completed and were ready for the final hydrotest, as well as for the installation of the internals. However, when the inspector and engineer arrived, they were notified that one of the vessels was not yet complete. The inspector and engineer extended their trip long enough to see that vessel through hydrotest, but had to return before the internals in the third one could be installed, because COVID case numbers were quickly increasing at the time, and new protocols (including restaurant closures) were quickly going into place. Because of the fear of not being able to safely return to the vessel shop, the three vessels (along with the uninstalled packing for the third column) were sent to the assembly shop with plans to install the packing in the third one at the assembly shop, which had the full set of equipment needed to do this work under roof (Figure 5). To ensure the safety of the assembly shop employees as the virus case rate continued to increase, a detailed procedure was drawn up and the engineers worked remotely with the assembly shop using a video camera and sequential pictures to support this work.
Another important focus during the modular assembly phase was to keep the assembly shop employees healthy. Modular construction is performed with an assembly line approach, which requires low workforce density. The modules are built along a horizontal orientation, allowing for reduced personnel hazards and other risks. Social distancing was possible with this type of arrangement. This is in contrast to the situation at a stick-built facility, where workers perform activities simultaneously, often in close quarters in multiple areas around the construction site.
The assembly shop also added additional measures of its own to ensure the project would be successful. Weekly staff meetings were scheduled to set the tone to keep the facility open and the importance of collaboration with the employees to stay healthy. Discussions about the impact of decisions made outside of the assembly shop, not only by the employees themselves, but also by their families, became routine. An emphasis was placed on the importance of individual behaviors.
It was key to understand the new risks and efficiently communicate with the various teams during assembly. The decision to shift the schedule to push for inspections and walkthrough toward the tail end of the project was made. This helped reduce exposure with outside personnel during construction.
The client was able to visit the assembly shop once the modules were near completion and was extremely satisfied with the way the team had handled the challenges brought by the global pandemic.
Recognizing all the challenges in a timely matter while also looking for proactive solutions resulted in zero cases of illness and the seamless, continuous production.
While the modularization part of the project allowed many challenges to be overcome, the client still faced other challenges that could not be avoided. For example, significant delays in permitting resulted from the local permitting office had closed due to the health concerns and with reduced staff returning to work, the timeframes were significantly extended to get approval of the permits.
This ammonia recovery system was completed on schedule, but the client shared that unfortunately, as a result of COVID-related delays, the foundation work had not yet been completed.
At time of modular readiness to ship, client requested that the modules be stored off-site at a laydown yard until all on-site work could resume and be finalized. Subsequently, hydraulic lift trucks were used for the modular transit and there was no need for cranes for unloading. ❑
Edited by Scott Jenkins
Authors
Mauricio Villegas is the manager of business development at Koch Modular Process Systems LLC (45 Eisenhower Drive, Suite 350, Paramus, NJ 07652; Phone: 832-859-0416; Email: mauricio.villegas@kochmodular.com). Villegas has more than 25 years of experience in the engineering and construction industry, delivering projects across industries ranging from small brownfield projects to greenfield mega-projects. Prior to joining Koch Modular, he held various management roles at WorleyParsons, Technip, IHI E&C and Arcadis. Villegas earned a B.S. in business administration and management from Northeastern University.
Chris Loftus is a project manager at Koch Modular Process Systems LLC (same address as above; Phone: 201-739-8697; Email: chris.loftus@kochmodular.com) and has over 25 years of experience in the chemical process industries. Prior to joining KMPS, he held positions as engineering manager at Genecor, a DuPont biotechnology subsidiary, and field service and product management for Veeco, in the semiconductor industry. Loftus holds a B.S.Ch.E. from Clarkson University.