To improve sustainability, materials manufacturers are welcoming new digital technologies and process innovations into their global supply chains
From palm oil to plastics, the global supply chains of many critical raw materials are evolving as consumers and manufacturers increasingly seek sustainable and renewable options. Digital technologies, including blockchain, Internet of Things (IoT) sensors and modeling tools, are facilitating these supply-chain transitions by enabling unprecedented data visibility and analyses. At the same time, chemical manufacturers are turning toward process and chemistry innovations to improve the sustainability of their raw materials.
Blockchain delivers accountability
Blockchain, in particular, provides many specific capabilities that are helping manufacturers realize more sustainable sourcing practices. In the plastics sector, for instance, DOMO Chemicals (Ghent-Zwijnaarde, Belgium; www.domochemicals.com) and Covestro AG (Leverkusen, Germany; www.covestro.com), along with the Circularise initiative (www.circularise.com/plastics), are partnering to implement blockchain technology to improve traceability and transparency in plastics manufacturing. “Blockchain can be applied to many challenges in the plastics value chain, such as complex record keeping and tracking of products. Blockchain serves as a less corruptible and better automated alternative to centralized databases,” says Jordi de Vos, founder of Circularise. Blockchain provides encoded information storage on a network-to-network chain, which validates data to protect business dealings and prevents the theft or manipulation of documents — a unique combination of transparency and security.
The Circularise platform (Figure 1) creates a digital twin of a material, component or product to build end-to-end traceability by integrating audit reports, certifications, material parameters and more. In addition to making materials traceable, Circularise aims to protect stakeholders’ privacy — the protocol is specifically developed to enable the disclosure of relevant supply-chain information without having to share sensitive data. One facet of the Circularise Plastics program is the creation of “material passports,” which contain all the verified information attached to a particular material, including batch number, certificates of analysis and more. “For example, when a material is being recycled, the recycler, and subsequently the customer, would know exactly where the material originates and exactly what it is made from,” explains Burkhard Zimmermann, head of strategy, sustainability and digital at Covestro’s Polycarbonates business unit.
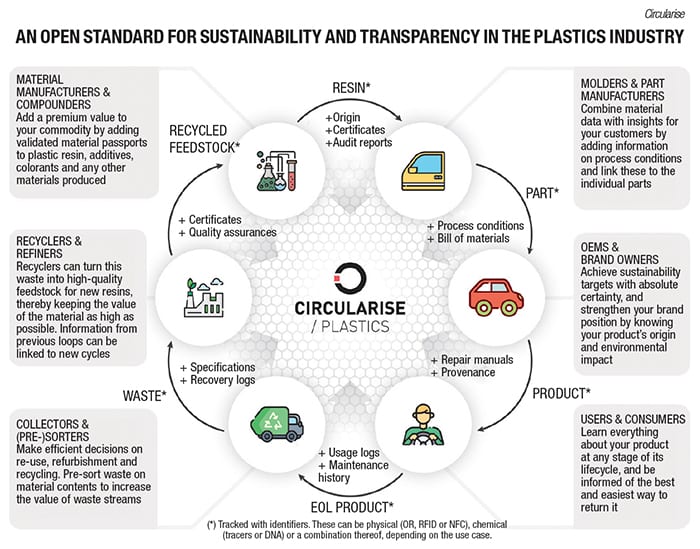
FIGURE 1. Circularise Plastics is a comprehensive, blockchain-based platform aimed at improving supplychain visibility for new resins, end-of-life (EOL) products, finished parts and more
The Circularise initiative aims to advance sustainability concepts — beyond just looking at plastics recyclability — and enable a communication protocol to facilitate their implementation. “This project can give us a sustainable feedstock of recycled plastics over time, yet also acknowledge additional benefits throughout the value chain and support customers in their search for sustainable materials,” emphasizes Thomas Nuyts, global product director of Domo’s Engineering Plastics segments.
Investment activities are further highlighting the economic importance of sustainable sourcing. In September, blockchain-based product-tracking platform OpenSC (Sydney, Australia; www.opensc.org) — co-founded by the World Wide Fund for Nature and BCG Digital Ventures — received $4 million in seed funding to further develop its technology to trace, verify and share supply-chain data (Figure 2). OpenSC assigns a digital identity to a product and uses IoT technologies to trace its supply chain from origin to consumer. Collected data are stored in a decentralized, tamperproof blockchain. “The benefit of blockchain is twofold. Firstly, it’s an immutable ledger, which means that once the data are recorded, it cannot be changed. The second benefit is that public blockchains are accessible and decentralized, so data can be made open and visible to consumers and other interested parties,” explains Markus Mutz, CEO of OpenSC. OpenSC utilizes machine learning to synthesize meaningful insights and verify ethical production claims by processing large amounts of previously underutilized data from disparate sources — including satellite images, GPS information, weather patterns and more.
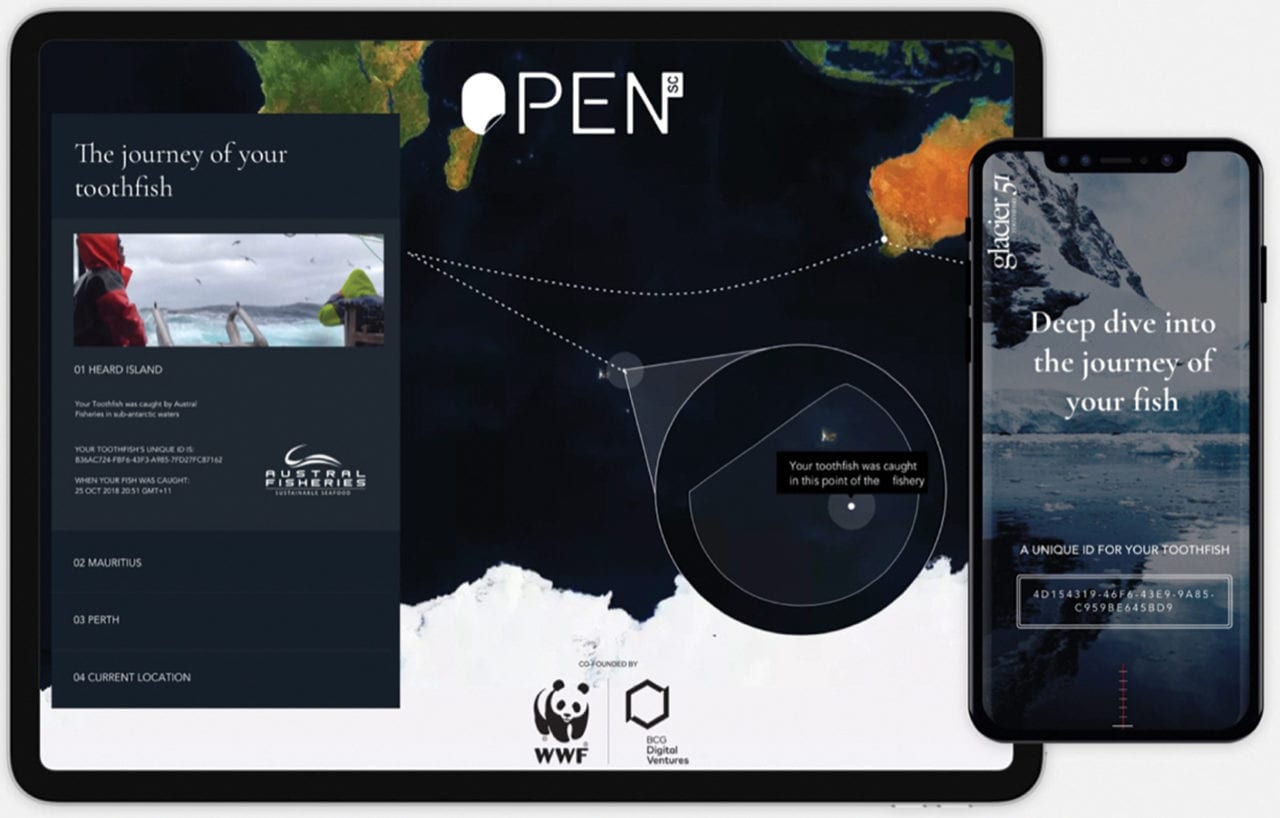
FIGURE 2. OpenSC depends on blockchain technology to bring together data from disparate sources, creating a holistic view of a material’s provenance OpenSC
OpenSC recently announced a pilot project with global food manufacturer Nestlé S.A. (Vevey, Switzerland; www.nestle.com) to trace milk products from New Zealand to the Middle East, and plans are in place to expand this partnership to trace palm oil sourced in Mexico. Palm oil is a ubiquitous ingredient in numerous food and personal-care products, but its procurement is currently fraught with environmental risks related to deforestation, making it an area where innovative supply-chain strategies are necessary. “OpenSC can use technology to verify that a palm-oil product was farmed on deforestation-free land by analyzing satellite imagery over time. This can be overlaid with plantation boundary coordinates and a unique product identification, tracing the product back to a particular property, verifying that it was produced without deforestation,” says Mutz. Palm oil is just one example of a product chain that can benefit from the data transparency provided by the customizable blockchain platform. Moving forward, Mutz believes that new levels of openness enabled by blockchain and other IoT technologies will drive consumers to increasingly demand sustainably sourced goods and encourage manufacturers to manage their supply chains to mitigate waste, fraud and other risks.
The need for responsible sourcing in the mining and minerals sector has been amplified by the tremendous growth in demand for battery materials, such as cobalt, graphite, lithium, lead, nickel and manganese. “The circumstances under which battery materials are produced, traded and transformed in certain geographies is fraught with risks,” explains Nicholas Garrett, CEO of RCS Global Group (Berlin, Germany; www.rcsglobal.com). RCS Global has collaborated with IBM (Armonk, N.Y.; www.ibm.com) and a consortium of large-scale mining companies, automotive manufacturers and intermediate suppliers to develop the Responsible Sourcing Blockchain Network (RSBN), said to be the mining industry’s first blockchain-based endeavor to tackle supply-chain sustainability. The RSBN includes an integrated assurance mechanism incorporating RSC Global’s audits, which consider standards and guidance from the Organisation for Economic Cooperation and Development (OECD; Paris, France; www.oecd.org), including verification against human rights abuses. “For each tier of the supply chain, additional criteria can be applied, including, but not limited to, social, environmental or operational health and safety conditions,” adds Garrett. The RSBN platform also aims to promote the socioeconomic advancement of small-scale miners through a tokenization model. Furthermore, the platform is designed so that it can be expanded to include additional conflict minerals and precious metals, with the goal of making it the industry standard for fully assured material traceability and provenance.
In addition to the RSBN, RCS has developed a smartphone application for data collection from remote mining sites.
“We use handheld devices for onsite monitoring of responsible practices and to scan tagged material shipments to enable traceability. Both data flows are captured in our central database, where algorithm-based analytics help us to analyze the data, design on-the-ground risk reports and direct and verify corrective actions,” explains Garrett.
However, he emphasizes, even with the abundant capabilities of digital technologies, a “boots on the ground” approach remains key in high-risk supply chains to ensure data integrity and for downstream companies to gain full visibility into their supply chain. “Our global supplier audit program helps clients map their entire raw-material-specific supplier ecosystem and verify that this ecosystem adheres to responsible sourcing practices, including industry policy frameworks, corporate codes of conduct and legislative requirements,” adds Garrett.
Another key element in assuaging supply-chain concerns is the collaborative management of relationships between suppliers and customers. “Enterprise contract management provides supply-chain visibility by tracking what a firm’s worldwide obligation, entitlements and business relationships truly are. It gives a firm grasp on the supply chain, key suppliers, the composition of the products purchased and the locales in which they operate,” says Neal Singh, chief operating officer at Icertis (Bellevue, Wash.; www.icertis.com). Icertis offers blockchain and artificial intelligence (AI) technologies to help companies improve transparency, execution speed and compliance with regard to measuring supplier diversity and product provenance. In the pharmaceutical sector, for instance, the complexities surrounding global supply chains, regulatory programs and drug trials introduce unique issues rooted in contract management and data visibility. “We’re seeing more customers with the need to enforce regulatory compliance across multiple geographies and optimize their relationships with material suppliers,” adds Singh.
Beyond blockchain, Icertis also uses artificial intelligence (AI) in its supply-chain monitoring and contract management platforms. “For the first time in history, contracts are being digitized. The ability to apply AI to this new pool of digitized data enables the transformation from static document to live contract,” says Singh.
Lenzing AG (Lenzing, Austria; www.lenzing.com), in collaboration with TextileGenesis, has launched a pilot project to use blockchain technology for tracking and tracing materials in the textile industry. Currently, there is no established system or commonly applied traceability language in the textile industry providing the transparency that consumers desire, explains Filip Miermans of Lenzing. As part of its ongoing sustainability efforts, Lenzing has invested considerably in its environmentally friendly fiber brands, which has made these products targets for counterfeiting in recent years. Blockchain technology helps to protect and identify the materials, providing full protection against fraud. The TextileGenesis platform creates a digital twin that represents and identifies each kilogram of fiber. “Digital tokens are passed along the supply chain and can be tracked from fiber to brand, all the way to retail stores, where customers can scan a garment using a mobile app, allowing them to view relevant information, such as origin, material and producers,” says Miermans. The first garments that are identifiable with TextileGenesis are already on the market, and the company expects to roll out this technology at progressively larger scales throughout 2020.
Innovations in materials use
The major drivers for responsible sourcing in the plastics supply chain are twofold — manufacturers must consider the sustainability of their raw materials while also minimizing the carbon footprint of producing plastic products. Dow (Midland, Mich.; www.dow.com) has advanced its sustainability strategy with technology partnerships focused on recycled and renewable raw materials, as well as by making their products more readily recyclable. Dow has begun work with Fuenix Ecogy (Weert, the Netherlands; www.fuenix.com) based around feedstock recycling. Fuenix operates a plant that processes post-consumer wastes, such as multilayer films and food packaging, into a pyrolysis oil that Dow then uses in its crackers in place of traditional fossil-fuel feedstock for plastics manufacturing (Figure 3). A key benefit, points out Carsten Larsen, Dow’s commercial director, Recycling EMEA & APAC, is that the “virgin” plastics produced using Fuenix recycled feedstock can be used in food-contact applications, whereas many other products that use recycled materials cannot, since the process using Fuenix feedstock is identical to typical plastics manufacturing. Through its partnership with Dow, Fuenix is working to scale up this technology. “This could be a very significant circular economy success story,” says Larsen. Another partnership finds Dow producing plastics from a renewable naphtha fraction provided by UPM Biofuels (Helsinki, Finland; www.upmbiofuels.com). UPM produces its renewable naphtha from tall oil, a residue from pulp-and-paper processing. Like the Fuenix partnership, UPM pulp-based naphtha gives Dow a renewable source to make plastics that can then be deployed into higher-value products, including in food-contact applications. Using UPM feedstock, Dow has already produced thousands of tons of renewable polymers. Now, says Larsen, the company is looking to expand the use of these renewable polymers into new high-value application areas, including footwear. Larsen emphasizes the importance of using plastics only where they are the most sustainable choice of material. “We should be able to enjoy the benefits of plastics — decreasing food waste, safer transportation or sterile medical instruments — without the negative environmental impact. We must collaborate with waste-management and technology partners to make sure we can maintain plastic as a sustainable material.”
On the recycling front, Dow is executing its Design for Recyclability initiative, aimed at making packaging materials more sustainable, and recently launched a new LDPE resin made with 70% post-consumer recycled materials. “We can look at a complex multilayer packaging structure and take out the layers that are not recyclable, or make them compatible with polymers or additives that can be integrated into packages so that when they are recycled, they can be used in higher-value applications,” explains Larsen
Digital technologies are also playing a role in Dow’s recycling initiatives. The company is employing advanced modeling tools for application testing of recyclable and renewable materials to prove that they can meet the performance requirements demanded by brand owners, such as Procter & Gamble or Unilever. For instance, Dow’s modeling tool can examine a 100% recyclable package and see the impact of removing a layer of PET when that package falls from a certain height — such as a shelf in a store. Then, the tool helps to simulate the effects of the impact and which kinds of materials can be added to strengthen it, explains Larsen. “When you start incorporating post-consumer recycled materials into your product, there is a worry about if the materials are good enough quality to bring into packaging structures. If you can manage those concerns quickly, that is an area where you can really advance quickly and come up with recyclable structures. This is driven by brand owners and consumers,” he continues.
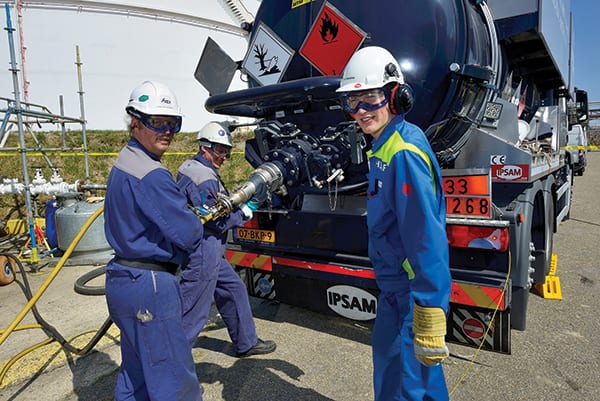
FIGURE 3. Dow has received its first delivery of Fuenix renewable feedstock at its manufacturing site in Ternuezen, the Netherlands Dow
Dow’s renewable-plastics supply chain has been verified by the International Sustainability & Carbon Certification (ISCC; www.iscc-system.org), a rigorous auditing process that examines a product’s entire lifecycle, from the raw material supplier to the production and post-processing facilities. “ISCC requires that you document and prove the amount of renewable feedstock or waste-plastic feedstock you bring into your operation and how much of that is turned into final product. It’s quite a thorough certification process,” says Larsen.
In the interest of making the supply chain for polyvinyl chloride (PVC) more sustainable, Perstorp AB (Perstorp, Sweden; www.perstorp.com) has become the first chemical manufacturer to gain certification from ISCC for renewable polyols, including the plasticizer Pevalen Pro. “The ISCC system has over 3,700 certificates in more than 100 countries. For Perstorp, reliability and transparency were essential when developing pro-environmental polyols, and we wanted to use a globally recognized third-party certification system,” explains Anna Berggren, business development director at Perstorp. By employing bio-based alternatives to traditional raw materials, Perstorp makes Pevalen Pro in three different grades, ranging from 8 to 40% renewable content. “Pevalen is a pentaerythritol tetravalerate (PETV), which is formed by combining one pentaerythritol molecule with four valeric acid molecules. In the production of the raw material valeraldehyde, we can use biogas instead of natural gas; and for pentaerythritol, we can change acetaldehyde to bio-acetaldehyde and the methanol to bio-methanol,” explains Jenny Klevås, Perstorp market segment manager, plasticizers. She points out that while it is not currently possible to make Pevalen Pro with 100% renewable content, it is the company’s ambition to secure additional supply of renewable raw materials to make completely bio-based products. Beyond its renewable polyols, Perstorp has several other sustainability-focused projects in the works. “Besides our non-phthalate plasticizers, Perstorp is also developing new fertilizers that are based on formate chemistry, as well as a new polyester that can replace glass, styrene or polycarbonate in disposable and reusable packaging,” mentions Perstorp innovation director Linda Zellner.
Another recent project aims to improve the supply chain for acrylic acid (AA), a commodity chemical used in numerous products, from diapers to paints. Nearly all AA is made from petroleum-based materials, but Archer Daniels Midland Co. (ADM; www.adm.com) and LG Chem (Seoul, South Korea; www.lgchem.com) are developing a technology to manufacture 100% bio-based AA using ingredients from corn processing. “We plan to leverage experience in feedstocks and process from both parties to advance the project to commercialization,” says Paul Bloom, ADM’s vice president for process and chemical research. At this point, portions of the technology have been demonstrated from laboratory- to full-scale operation. As part of the project, LG Chem is exploring the construction of a bio-based AA production plant in the U.S., and also evaluating additional opportunities in bio-plastics production. Bloom believes that the project is an excellent example of the type of cross-industry collaboration that is essential in advancing sustainable manufacturing processes. “Both parties bring unique processing experience. Between the companies, the team possesses the key capabilities to develop not only the technology, but the supply-chain integration needed to commercialize this new route,” he adds. ■
For additional coverage of recent blockchain activities in the materials supply-chain space, read New Blockchain Projects Target Renewable Energy, Battery Materials.