Ongoing advances in both adsorbent materials and system engineering allow today’s pressure swing adsorption (PSA) systems to produce nitrogen of varying purities and volumes at relatively low cost compared to cryogenic air separation
Nitrogen production that is carried out using pressure swing adsorption (PSA) technology over a carbon molecular sieve (CMS) is considered to be a mature, cost-effective and highly efficient method to produce nitrogen to meet a wide range of purity and flow requirements. Ongoing increases in efficiency in PSA-based nitrogen-generation facilities are being driven by enhanced CMS materials (Figure 1) and process improvements. This article provides an overview of the fundamentals of PSA-based nitrogen generation, while focusing specifically on innovative practices and improved CMS materials. Together, these advances contribute to continuous improvement in PSA system performance, giving chemical process industries (CPI) plant operators a proven way to produce a reliable and low-cost supply of high-purity dry nitrogen onsite.
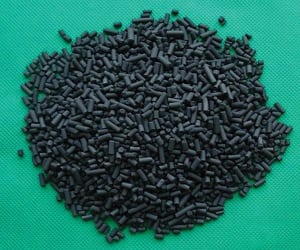
FIGURE 1. Carbon molecular sieve (CMS) pellets, typically manufactured from coconut shells, provide the surface area and pore structure needed to separate oxygen and nitrogen from a compressed air inlet stream (Credit: Comelt S.p.A.)
Introduction
Thanks to its inertness and low reactivity, nitrogen — in both the gaseous and liquid state — is used in a wide range of applications in many industrial sectors. These include the production of foods and beverages, chemicals and pharmaceuticals; petroleum processing; the thermal treatment of metals; the manufacture of flat glass, semiconductors and electronics; and many more. Industrial facilities that require large volumes of nitrogen always look for efficient methods of onsite nitrogen production to meet all of the specifications related to purity, flow requirements, power consumption, footprint and portability [ 1 ].
Nitrogen gas is produced by separating air into its primary component molecules (nitrogen and oxygen), using one of two methods: 1. Traditional cryogenic fractionation of air that has been liquefied; or 2. Separation of gaseous air using pressure swing adsorption (PSA) or membrane-based separation systems. If large volumes of nitrogen with extremely high purity (99.998%) are required, cryogenic fractionation of air remains the most efficient and economical technology option [ 2 ]. This is the oldest method of nitrogen production, and it has the ability to produce both gaseous and liquid nitrogen (for daily use and as a backup supply). Cryogenic fractionation of air is typically carried out in large-scale commercial plants that then deliver the produced nitrogen to users.
However, at many CPI facilities, enriched nitrogen is produced onsite using smaller-scale PSA separation or membrane-based separation systems. PSA systems operate on the principle of physical adsorption of the oxygen in air by carbon molecular sieve materials (such as those shown in Figure 1), leaving an enriched nitrogen stream as the product; the process is illustrated in Figure 2. Today’s PSA systems can economically produce nitrogen from compressed air at a variety of volumes. For instance, today’s systems can handle an inlet air stream of less than 5,000 to more than 60,000 std. ft3/h, reliably producing N2 that meets purity requirements from 95 to 99.9995% [ 1 ].
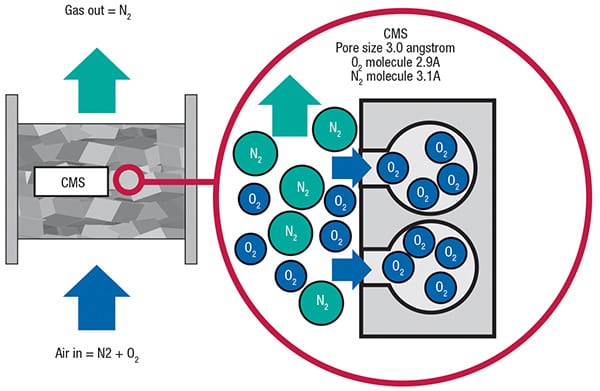
FIGURE 2. Within the CMS pellets, oxygen is preferentially adsorbed, allowing a nitrogen-rich product stream to be captured for use onsite (Credit: SHL)
However, the capital and operating costs of a PSA system are directly correlated with the purity of the nitrogen produced, and these costs climb rapidly once nitrogen with purity greater than 99.5% is required. In some cases, it can be cost-effective to produce higher-purity nitrogen by first producing 99.5%-purity nitrogen using a PSA system, and then using a palladium or copper unit to remove residual levels of oxygen in the nitrogen product. Such systems can bring down residual oxygen to 1–3 ppm.
Membrane-based separation systems, which typically produce nitrogen at relatively low capacity (up to 40,000 std. ft3/h) with a purity of 95–99.5%, use several semi-permeable membrane modules. Each membrane module contains thousands of hollow-fiber membrane strands that remove oxygen, water vapor and carbon dioxide from the compressed-air inlet stream, via selective permeation. Membrane technology is the newest of the three nitrogen-production options (introduced more recently than cryogenic and adsorption processes). In recent years, ongoing improvements in membrane materials have helped to make membrane systems attractive for somewhat larger nitrogen flow requirements.
Selecting the right system
When selecting the most appropriate nitrogen-production process, several parameters should be considered. Purity and capacity are the most important factors that can affect the choice of production methodology, and hence, have a direct impact on the unit cost of the nitrogen produced. The use of a PSA nitrogen-generation system, which can be designed to meet all types and patterns of nitrogen flow — steady, periodic and erratic — has grown in popularity during the last several decades, thanks to the simplicity, performance, flexibility, reliability and relatively low capital and operating costs of this production route.
However, the optimal nitrogen-production rate using a PSA system based on CMS pellets is around 3,000 Nm3/h of N2 produced (>95% purity). Within that range, PSA is a more economical option than O2/N2-separation by air liquefaction and cryogenic separation, or by membrane-based separation. The principles of PSA-based nitrogen-generation technology using CMS and several important aspects of process engineering knowhow are discussed below.
Carbon molecular sieves
CMS is part of a special class of activated carbons that have non-crystalline (amorphous) structure with a relatively narrow pore-size distribution. This material provides molecular separations based on the rate of adsorption of nitrogen, rather than the differences in adsorption capacity between oxygen and nitrogen. Figure 2 shows the inner structure of a CMS material that is appropriate for the separation (removal) of O2 molecules from N2 molecules in the compressed-air inlet, to yield an enriched nitrogen stream (Note: Carbon molecular sieves are selective for oxygen, while zeolite molecular sieves are selective for nitrogen).
CMS that is used to separate nitrogen and oxygen from air in PSA systems is typically manufactured from coconut shells, in pellet form, with pellet diameter from 1.0 to 1.8 mm. Such pellets have the most suitable pore size and maximum surface area to allow for the separation of nitrogen and oxygen from air during the continuous, cyclical process of adsorption (pressurizing) and desorption (depressurizing).
Due to the presence of micropores in a very small size range, oxygen molecules are able to penetrate the CMS pellets relatively fast, whereas the slightly larger nitrogen molecules take more time to penetrate the CMS material and be adsorbed (Figure 2). Initially, oxygen preferentially enters the micropores. However, after a few hours, equilibrium is achieved and when that occurs, CMS adsorbs roughly equal amounts of nitrogen and oxygen.
Nitrogen production via PSA
The PSA process makes use of cyclic pressurization and depressurization steps, where more oxygen is adsorbed on the CMS during the high-pressure cycle, and then released when the pressure is reduced. Figure 3 shows a typical PSA nitrogen-generation system, consisting of two interconnected CMS (adsorber) columns that have automatic changeover valves. Through cyclic operation of the valves, the two columns alternate in function, so that compressed, dry air flows into one column (during the adsorption phase). Once the adsorption phase is complete and the pressure in that column is reduced (toward atmospheric pressure), depressurization takes place (desorption phase). Assuming that Column C1 is operating in adsorption mode, the CMS in that tank adsorbs oxygen from the inlet air and the product nitrogen stream leaves the adsorber and is fed to the end user via a receiver tank.
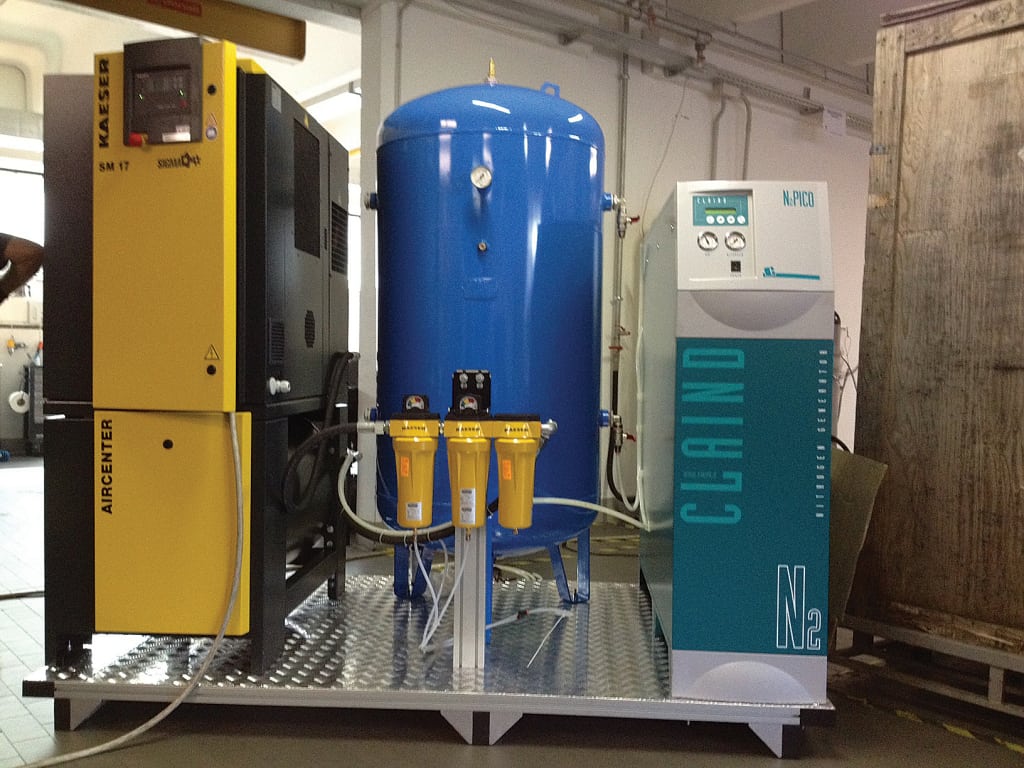
FIGURE 3. A typical onsite PSA system uses two vessels, both filled with CMS pellets. They operate in an alternating mode, so that at any time, one is in pressurization mode to enable air separation (to allow the nitrogen product stream to be collected), while the other tank is in depressurization mode, to allow the adsorbed oxygen to be released to the atmosphere (Credit: Claind S.r.l.)
At the same time, the second column (C2) is operating in its desorption phase. As C2 is depressurized toward atmospheric pressure, the oxygen that was adsorbed by the CMS media is released, creating an oxygen-enriched gas (off-gas) that is vented to the atmosphere as an inert exhaust stream.
Once the operation cycle is complete, the valves are activated in such a way that C1 again operates in desorption mode, while C2 operates in adsorption mode. This cyclic pressure-swing operation allows for continuous nitrogen production.
Short cycles between adsorption and desorption are typically adopted, in order to obtain the higest possible oxygen load by the CMS media (to allow the target nitrogen stream to be quickly and efficiently separated from the inlet compressed-air stream). In a typical PSA system, the usual adsorption-desorption cycle time lasts just 45 to 90 seconds. At the end of the desorption cycle, pressure is equalized between the two adsorbers (for a few seconds), and another cycle begins.
For the sake of process optimization, the pressure release into the atmosphere can be cut off shortly before the end of the cycle by closing the waste-gas valve. This so-called “cutting technique” leads to higher nitrogen purities (<1 vol.% residual oxygen in the product nitrogen stream), because toward the end of each desorption cycle, a major proportion of nitrogen still remains in the pore structure of the CMS substrate. This provides a slight initial pressure of pure nitrogen at the start of the next adsorption cycle, which benefits the overall adsorption sequence.
The cutting time (to achieve oxygen content in the product nitrogen of <1%) is typically set according to the following procedure:
Measurement of O2 concentrations in the exhaust gasObservation of the (declining) O2 concentrations in the exhaust gasDetermination of the time taken up to the moment when the dropping O2 concentration has gone down to 21 vol.%.
The time measured (in seconds), plus the cutting time to which the closing times of exhaust valves, is typically set via a controller.
PSA plant configuration
A standard PSA nitrogen-generation plant typically includes four major sections:
Air compressor for the inlet airAir pretreatment (which typically involves the use of a mist eliminator to remove water droplets and very small amounts of entrained oil, plus a carbon filter to remove residual oil vapors prior before the inlet stream enters the buffer tank)Adsorption-desorption columnsProduct-delivery system (typically a nitrogen receiver/buffer tank plus an oxygen analyzer ahead of delivery to the customer)
Similarly, PSA nitrogen-generation plants are usually operated with an upstream refrigeration dryer (Note: The use of refrigerated dryers eliminates the requirement for purge air, resulting in a capital-cost reduction, but this design introduces more water vapor into the CMS columns [ 1 ]). As an alternative, the PSA system can also be operated with a desiccant layer arranged in the bottom part of the PSA adsorbers to remove moisture from the inlet air stream.
To ensure reliable operation of the PSA plant, moisture in the inlet air should be maintained at rate lower than the rate corresponding to the pressure dewpoint +2°C (<5.57 g H2O/m³ of air at 8 bars). Excessive levels of moisture will contaminate the CMS columns and reduce the efficiency of the nitrogen generation process.
Long-term practical experience with PSA plants has shown that, as long as the specified conditions are strictly observed, the entire CMS bed can expect a lifespan of five years or more. The CMS material must be filled homogeneously into adsorbers, and these vessels should be equipped with a bottom gas-inlet system. The recommended procedure is to fill the CMS pellets homogeneously into adsorbers using the snow-storm-filling device, which distributes the desiccant and CMS evenly over the entire adsorber cross-section as it enters the column. This procedure ensures the highest bed densities in one filling step (higher than that produced using vibration or other commonly used methods), and leads to optimal system performance.
Regular maintenance is key
To meet longterm performance objectives, the CMS media must be replaced regularly, according to system-specific revamp requirements. If the performance of an existing PSA facility begins to decline, the CMS should be replaced. Such a revamp provides a good opportunity to adjust the existing design concept to ensure that the nitrogen requirements of the user are still being met. Upgrading to the most modern CMS materials allow operators to optimize the existing plant toward higher production rates and better gas quality. Along with a safety inspection and replacement of worn parts, such a periodic inspection, upgrade and retrofit allows operators to stay abreast of the most state-of the-art technology.
The inherent flexibility and reliability of today’s PSA systems provides many advantages, allowing CPI operators to produce nitrogen in the required purities and volumes, to meet a diverse range of chemical process applications. Ongoing advances in both the CMS adsorbent materials and the overall process design and engineering have led to continuous improvements and advancements of such systems for air separation, allowing them to be used as a cost-effective alternative to more costly cryogenic air separation in many applications. n
Edited by Suzanne Shelley
References
1. Ivanova, S., and Lewis, R., Producing Nitrogen via Pressure Swing Adsorption, Chem. Eng. Prog., June 2012, pp. 38–42.
2. Smith, A.R., and Klosek, J., A Review of Air Separation Technologies and Their Integration with Energy Conversion Processes, Fuel Processing Technology, Vol. 70, 115–134, 2001.
Recommended reading
1. Billiet, C., Advanced Energy Saving Pressure Swing Nitrogen Generators, Nano-porous Solutions Ltd., UK, March 2013.
2. Crittenden, B., and Thomas, W.J., “Adsorption Technology & Design,” Elsevier, USA, April 1988.
3. GasTec, An Introduction to Pressure Swing Adsorption (PSA) Nitrogen Generation System, Rev.1, GasTec, Malaysia, Nov. 30, 2012.
5. Mayekawa Mfg. Co., Ltd., PSA Nitrogen Generating System, Mayekawa Mfg. Co., Ltd., Japan, 2012.
6. Moreiraa, R.F.P.M., Jose, H.J., and Rodriguesb, A.E., Modification of Pore Size in Activated Carbon by Polymer Deposition and Its Effects on Molecular Sieve Selectivity, Carbon, Vol. 39, 2269–2276, 2001.
7. Schroter, H.J., Gahlen, R.N., and Knoblauch, K., “Nitrogen-PSA Plants Know-How Handbook,” Bergwerksverband GmbH, Germany 1991.
Authors
Saeid Mokhatab is an internationally recognized gas-processing consultant (Dartmouth, NS, Canada; Email: [email protected]) who is actively involved in supporting adsorption projects in the hydrocarbon processing industry, from conception to operation. Mokhatab has developed innovative solutions and process configurations for difficult-to-treat feed streams, to help maximize the use and life of adsorbents, and also provides customized training programs to optimize adsorption systems based on the specific needs of operation personnel.
Stefano Corso is an area sales manager of Comelt S.p.A. (Via Sondrio, 4, 20063, Cernusco sul Naviglio, Italy; Email: [email protected]), in the activated carbon and adsorbents field. He started his professional experience with a multinational petrochemical and chemical company operating in the optimization of industrial processing plants through chemical treatments. For 15 years, Corso developed his chemical and sales experiences in the adsorbents field (molecular sieve and silica gel) at Grace Davison, and after that as a specialist on carbon molecular sieves with CarboTech AC GmbH, Germany.