With the right technology, chemical processors can obtain precise particle size and consistent material while improving throughput and quality
Particle sizing is an essential task in the chemical process industries (CPI) where achieving high-quality product efficiently and at a low cost is the name of the game. For this reason, appropriate size-reduction equipment is critical to overcoming process challenges that impede throughput, as well as acing new applications that require smaller, purer particles. Measurement and monitoring of particle size is also necessary to ensure that particles remain properly sized and distributed, as process changes can wreak havoc on particle size. For this reason, size reduction and analysis equipment providers are introducing solutions that help chemical processors achieve target particle sizes in a consistent manner with higher yields.
Many CPI companies receive, process and produce materials as powders and granules. Often, the particle size of these materials plays a crucial role in how well they may be stored, handled and processed and can greatly impact productivity, as well as quality of the product, says Brian Pittenger, vice president, Jenike & Johanson (Tyngsboro, Mass.; www.jenike.com). “However, it is not yet common for processors to have a well understood and controlled nature of the particle size distribution,” he continues. “When I visit chemical producers, it is rare that they have mass balances through their process on a particle-size-distribution basis. In fact, it is very common for this aspect of their process to be out of control, as it is rarely monitored or measured.”
And, this can be a problem, because many chemical conversion steps require control of surface-area-to-volume ratios of materials being processed or the reaction may not proceed as expected. “For nearly every unit operation — milling, blending, drying, centrifuging, compacting, agglomeration, as well as storage, feeding and conveying steps — a well-controlled particle-size distribution will nearly always result in more consistent product, higher throughput and less loss and waste, as well as fewer process upsets and unplanned shutdowns,” explains Pittenger.
Pittenger reports that his firm is routinely asked to troubleshoot the process and find, as a root cause, the uncontrolled variations of the particle size distribution. “It may come from unplanned attrition or agglomeration of materials as they move through the process or, more frequently, as a result of particle segregation since little attention was given during design or operation to particle flow,” he says. “Furthermore, once a process is in place, it is commonplace for it to be pushed well past its original design basis for either greater throughput or as a result of changing product expectations in the market. These increases are often made with little regard to the impact on particle size distribution. Processes are run faster, hotter and with shorter residence times and these changes almost always result in substantial unplanned changes to the particle size and distribution.”
For this reason, properly considering the particle size and distribution throughout the lifecycle — from design through planned changes — greatly benefits a range of processes. However, this requires the ability to measure and understand particle-size distribution as part of the process just as well as any other critical process variable, says Pittenger.
Size reduction solutions
Because every process is unique, there is no “one size fits all” when it comes to size reduction. Many size-reduction equipment providers, as well as engineering firms like Jenike, offer experience and laboratory testing and trials to help select the correct equipment for the application and to troubleshoot size-reduction processes that have gone out of specification. Most are familiar with the challenges faced in the CPI, and while those vary as widely as the applications, there are a few common issues.
The need for higher throughput is one of the most frequently heard challenges. Often when a processor seeks higher throughput, they assume that it is necessary to go with a larger or additional size reduction machine; however, advances in sieving and screening may allow them to achieve more throughput and yield without additional sieving processes, says Jeff Hochadel, president, HK Technologies (Salem, Ohio; www.clevelandvibrator.com). “Bigger is not always better when it comes to getting material through a screen,” he says. “We can apply ultrasonic technology to the screen or other high-frequency sieving devices that can give them additional yield without going to a larger machine.”
For example, the HK Ultrasonic Screen Deblinding System can convert existing gyratory screeners, sieves or sifters to an ultrasonic screener. The system is designed using an ultrasonic transducer attached to a frame or ring, preserving the integrity of the mesh screen and extending life in the field. The frame delivers a high-frequency, low-amplitude ultrasonic vibration that excites the screen and eliminates blinding of materials, such as ceramics, powdered metals, pharmaceuticals, powder coatings or additives on the screen deck.
However, just tweaking the machine itself is not always enough to improve throughput. Other glitches include issues with premixing, says Paul Trefny, laboratory manager and applications process advisor with Netzsch (Exton, Pa.; www.netzsch.com). “Proper premix is often a challenge,” says Trefny. “A customer may be using high-shear dispersing and a blade diameter is incorrect or something else is happening that leads to ineffective premixing. When the material is not properly premixed, it can be difficult to reach the target size and can also lead to problems with the mill, such as pressure, temperature, pumping and processing issues. However, they can get 15 to 25% better efficiency out of their mill if the pre-mix is effective.”
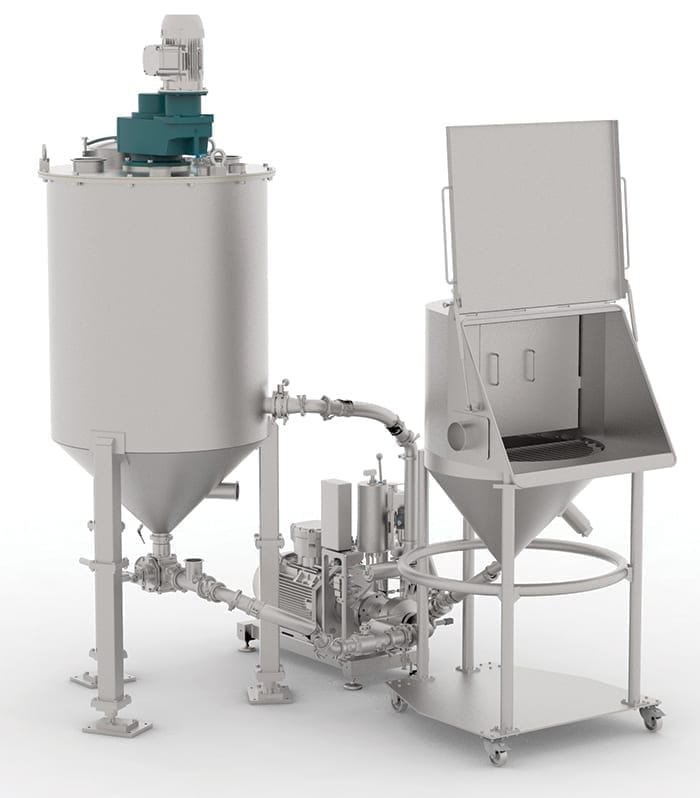
Figure 1. To assist with pre-mixing, Netzsch introduced the Epsilon, a compact solution for producing homogeneous dispersions with reproducible quality in an inline process. Netzsch
To assist with pre-mixing, Netzsch introduced the Epsilon (Figure 1), a compact solution for producing homogeneous dispersions with reproducible quality in an inline process. The dispersion process takes place in an atmospherically sealed processing chamber and is dust and emission free. The inline disperser is operated in circulation mode, whereby the powder can be fed from a bag via suction lance or bag feeding station. The machine operates similarly to a feed pump. Through optimal flow control, a negative pressure is created in the processing chamber during operation. This negative pressure is used to draw in the powder, where, in combination with appropriate powder delivery, introduction of external air is minimized.
Maintenance issues frequently impede throughput, as well, says Joe Bailey, sales manager with Midwestern Industries (Massillon, Ohio; www.midwesternind.com). “We get a lot of calls from customers who are having issues with the screen not performing as it should or that they aren’t getting the throughput they used to,” he says. “Sometimes the issue is blinding, which can be solved with anti-blinding technologies, but often it’s a matter of changing the screen. Screens in a screener are wearable items, and they can be difficult and time consuming to change.” To combat the problem, Midwestern developed the Electro-Lift (Figure 2) to assist with the lifting of separator frames, eliminating the need for two people to remove each frame. Also, the Electro-Lift helps reduce downtime and can be used to inspect the screens to ensure quality control. “The system can be used by one person who pushes a button and the screen lifts up, allowing them to easily slide it out and slide in another to save downtime and labor during screen changes.”
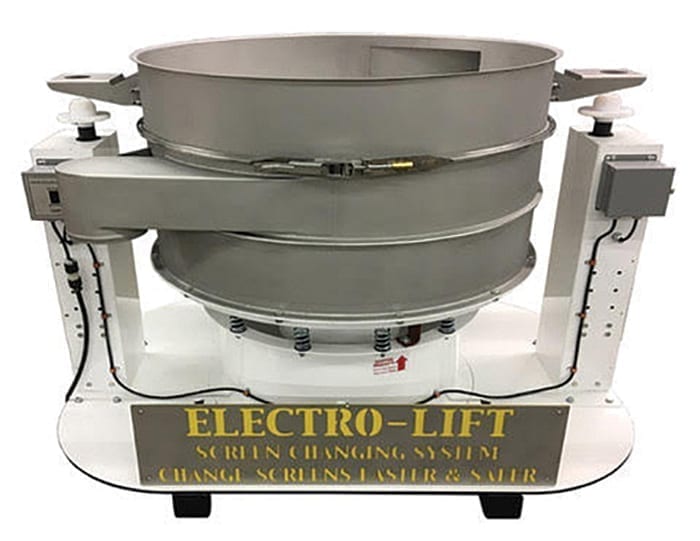
Figure 2. Midwestern developed the Electro-Lift to assist with the lifting of separator frames, eliminating the need for two people to remove each frame. Also, the Electro-Lift helps reduce downtime and can be used to inspect the screens to ensure quality control. Midwestern Industries
Tackling new applications
Many of today’s applications, such as those in pharmaceuticals, life sciences, battery and electronics and solar cells, require smaller, purer particles. Fortunately, size reduction equipment is rising to the challenge. “Surface area reactivity is the main reason processors want to get to finer particle sizes, sometimes in the 1 to 3 micron range or smaller,” explains Jeffrey Hoffman, vice president, with Paul O. Abbe (Wood Dale, Ill.; www.pauloabbe.com). “And in many of these applications, such as those for solar-cell materials, advanced ceramics and glass and cobalt used in porcelain coatings, they require very consistent particles with a narrow particle distribution range so that, at the end of the day, the processor has an end product that is consistent.”
Other materials may require even smaller particles, says Frank Tabellion, director of global sales and marketing, grinding and dispersing technologies, with Bühler Group (Uzwil, Switzerland; www.buhlergroup.com). “There is also a need for particles between 100 and 200 nm in the fields of inks, raw materials for batteries and other industries,” he says. “For instance, for ink jet printing, they require particle sizes between 100 and 200 nm to prevent clogging of the printing nozzles, and in lithium ion batteries, they require finer particles to improve battery performance. This trend toward finer and nanosize particles requires fine grinding and a lot of energy.”
For fine-grinding applications, ball and bead mills are often the go-to technology. “The size reduction equipment needs to be able to handle very small beads in order to achieve nanodispersions,” says Tabellion. “An additional benefit is that the smaller beads you are using, the more efficient the whole grinding process becomes, regarding energy efficiency.”
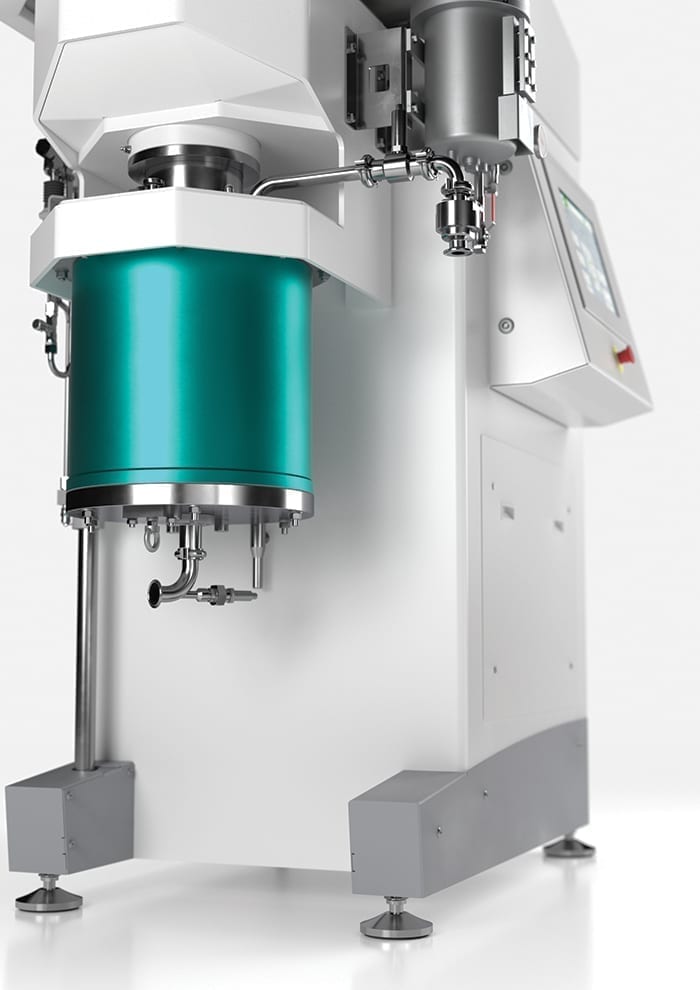
Figure 3. The MicroMedia Invicta is the latest version of Bühler’s bead mill, which features a new process-chamber design and bead-separator system that delivers a 25% increase in efficiency and a 50% uplift in productivity in wet grinding applications. Bühler
Bühler recently introduced the MicroMedia Invicta (Figure 3), the latest version of its bead mill with a new process chamber design and bead separator system that is said to deliver a 25% increase in efficiency and a 50% uplift in productivity in wet grinding applications. The remodeled bead separation system and screen design reduce blockages and pressure buildup. This allows recirculation to be driven faster, speeding up overall flowrates by an average of 100%. In addition to helping achieve target particle size faster, this also improves process safety and reliability.
In many of these sensitive applications, says Abbe’s Hoffman, contamination can be an issue. “In applications for solar cells and electronics, as well as many others, it is essential that there is no contamination coming from the mill,” he says. “In any application where the end product has to be super conductive, insulating or pure, contamination is a huge concern. It’s the equivalent to being in the medical industry and saying I have the correct drug for you, but the needle isn’t sterile.” For this reason, Abbe makes its ball mills in a range of materials that are compatible with what is being processed (Figure 4). “For instance, if the material is ceramic, we make the ball mill from compatible ceramic materials so that there is no chance of contamination.”
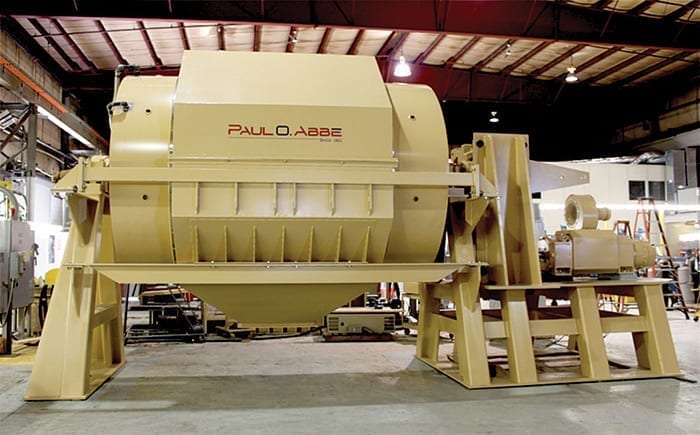
Figure 4. Paul O. Abbe makes its ball mills in a range of materials that are compatible with what is being processed. For instance, if the material is ceramic, the company makes the ball mill from compatible ceramic materials so that there is no chance of contamination. Paul O. Abbe
Up-to-the-task instruments
When it comes to ensuring product quality, monitoring and measuring particle size and distribution is as important as getting the sizing right. “Processors need to know, with precision and accuracy, good information about particle size and distribution of sizes because not everything is going to be perfect,” says Jeffrey Kenvin, technical director with Micromeritics (Norcross, Ga.; www.micromeritics.com). “Detecting when there’s a problem, such as there being too many big particles, and trying to understand what is causing the problem when you’re manufacturing something is essential because particle size issues can slow down the process, create problems with speed of the process, harm processing equipment and affect performance and quality of the final product. When there’s a mistake or a problem, there is often a severe economic penalty for the processor.”
Because processors must make consistent product, they need assurance that their particle sizes are within specifications, so their test methods have to be robust, dependable and representative of the product, explains Kenvin. “Digital control has dramatically improved the quality of laboratory instruments as it allows not only the measurement to be more accurate and repeatable, but also the device itself,” he says. “If I buy one device to use in California and another for New York, they should both provide the same answer. Thanks to digital controls, the performance of the instruments has really leveled out and devices are very accurate and repeatable because they employ the same control algorithms and control devices.”
However, accurate and repeatable results aren’t the only thing processors are looking for. “Speed of analysis is also important for many processors, especially when they are monitoring and measuring particle size in order to make decisions about operating the process or quality control,” says Maik Paluga, sales consultant, particle sizing, with Fritsch GmbH (Idar-Oberstein, Germany; www.fritsch.de). Fritsch introduced the Dynamic Image Sizer, which can be fed with dry powders or granules (between 20µm and 2 cm) that are transported by a vibrating feeder and fall into the measuring zone. There, they pass between a camera and a flashing light source. Images are taken with a rate of up to 72 frames per second and transferred to the software that determines the outer perimeter of each particle. This provides information not only about particle size, but also about particle shape. “The results they need can be achieved within minutes using this equipment versus spending hours waiting for the results of one traditional analysis.”
And, the trend toward smaller particles requires instruments that provide a better understanding of smaller sizes, says Kenvin. “We are moving into a range where the smaller the particles get, the more challenging it is to rapidly determine size, which is critical when the technology is used in the process industries and they need results in a timely manner,” he says. “So the challenge becomes the ability to provide a better understanding of smaller particle sizes, more precisely and in a timelier fashion.”
He says dynamic light-scattering technology is a good solution for this type of monitoring. “For some time, progress in laser light-scattering technology led to faster analyses, but the quality of the measurement was limited. Recognizing the need for better detection capability, Micromeritics developed the Saturn DigiSizer, an instrument that employed a laser diode and modern charge-coupled device (CCD) detector to improve the sensitivity, resolution, reproducibility and repeatability of the laser light scattering particle sizing technique,” he says.
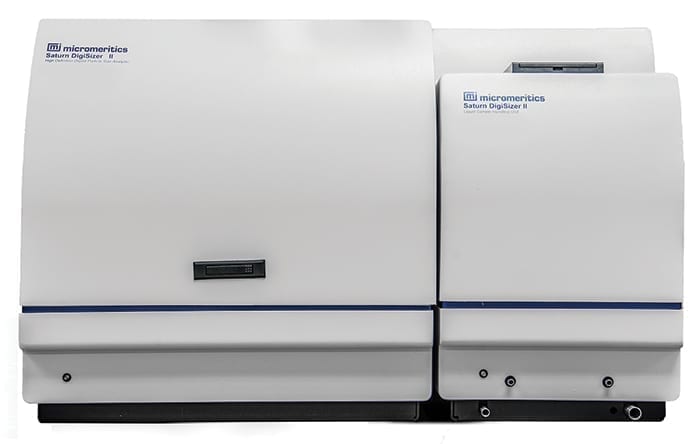
Figure 5. The Saturn DigiSizer II uses a state-of-the-art CCD detector containing over three million detector elements and unique design and data-reduction features to provide users with an extremely high level of resolution and sensitivity. Micromeritics
Improving further, Micromeritics introduced the Saturn DigiSizer II (Figure 5). Using state-of-the-art CCD detector containing over three million detector elements and unique design and data reduction features, the latest version provides users with an extremely high level of resolution and sensitivity. The level of detail, accuracy and resolution enables the extraction of all available information from the static light scattering pattern. Users can now measure the same material on multiple instruments located at different locations around the world and obtain the same, highly detailed size distribution measurement on each instrument.
And, for applications with more advanced formulations that included mixed particle sizes, all of which are submicron, Horiba Instruments Inc. (Irvine, Calif.; www.horiba.com) introduced an instrument for nanoparticle tracking analysis, says Jeffrey Bodycomb, product line manager, particles characterization, with Horiba. “The latest technology in particle sizing is the advent of multi-laser nanoparticle-tracking analysis. This is a big improvement over the older, single laser systems that did not work well with the size distributions commonly encountered in proteins, nanoparticle synthesis, vaccines or viruses. Nanoparticle tracking lets users determine detailed size distribution of submicron particles with much better accuracy than traditional dynamic-light-scattering instruments. With appropriate choice of scattering volume, it is also a suitable tool for determining submicron particle concentration.”
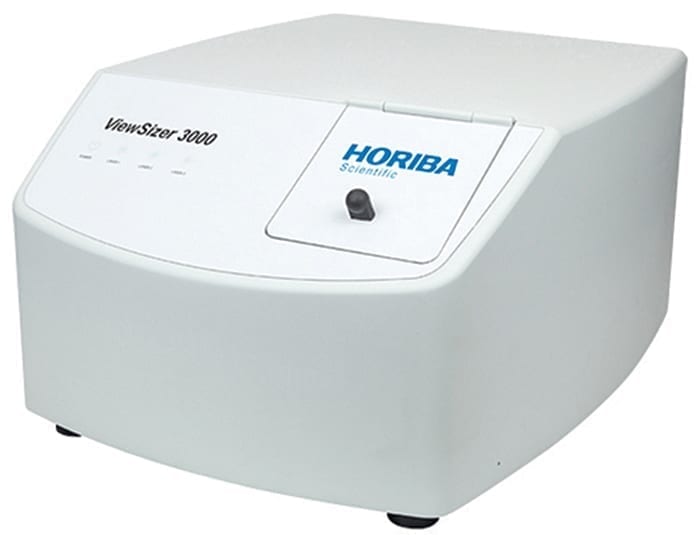
Figure 6. The ViewSizer 3000 incorporates three variable light sources, allowing the instrument to select the optimum conditions for any sample analysis, overcoming limitations of conventional nanoparticle-tracking analysis when analyzing polydisperse samples and enabling a much larger range of particle sizes to be visualized. Horiba Instruments
The company’s ViewSizer 3000 (Figure 6) incorporates three variable light sources (blue, green and red), allowing the instrument to select the optimum conditions for any sample analysis, overcoming limitations of conventional nanoparticle tracking analysis when analyzing polydisperse samples and enabling a much larger range of particle sizes to be visualized. Furthermore, by introducing the sample in an easy-to-use (and clean) cuvetter, the ViewSizer 3000 is able to repeatedly “analyze and stir,” giving more reproducible results. And, since the sample is viewed in a vertical orientation, it is suitable for visualizing processes such as protein aggregation or crystal dissolution.