It is clear that burning fossil fuels is no longer a viable proposition in terms of meeting the world’s energy needs. The move to renewable sources is underway and will only accelerate over the coming years. Hydropower, solar and wind are well established technologies, and investment in areas such as bio, geothermal and wave/tidal energy continues to grow.
Advanced batteries and fuel cells are another area in which technological advances are being made. The challenge, however, is to develop these technologies in such a way that initial R&D and prototyping is economically viable, but production can then be scaled up to industrial levels.
The matter is made all the more complex by the fact that no single technology will serve all needs: EVs, ESS (Energy Storage Systems) and fuel cells will all require different chemistries. Solid state, dry process Li-Ion, wet process Li-Ion, lithium iron phosphate (LFP), and air batteries are just some of the areas where significant progress has already been made in terms of research and development work. Other combinations of materials may offer even greater potential in terms of power density and efficiency.
Whatever these next-generation technologies prove to be, the principle of power production and storage via the movement of electrons through an electrolyte material is unlikely to change in the foreseeable future. And this is going to require the use of electrodes and separators.
The processes involved in electrode production can vary as much as the technologies themselves. Multi-layer dry process Li-Ion electrodes for instance, can involve scattering systems and calendaring equipment. Solid state batteries could use coating or scattering equipment ahead of a double belt press, with a calendaring roll for final lamination. Most will also make use of unwinders and winders with associated roll handling.
Integrating these technologies into one efficient process line can be technically challenging but the recent acquisition by IPCO of US-based New Era Converting has created a team capable of delivering integrated, end-to-end process solutions for the development and production of next-generation separators, barriers, membranes, and multi-layer electrodes.
IPCO is a leading manufacturer of advanced industrial process systems, with scalable production solutions for applications including thin film casting, scattering, and pressing/laminating. New Era’s portfolio complements this with the addition of calendaring equipment, coaters and web handling equipment
Thin film casting for separators, ceramic tape and membranes
IPCO’s continuous film casting system enables the production of thin film and tape products to exceptionally narrow tolerances. A slot die coater delivers a uniform casting of the product onto a continuously moving, steel belt. The thin film is carried to the IPCO Venturi dryer, a technology that eliminates any risk of skin and wave formation on the product.
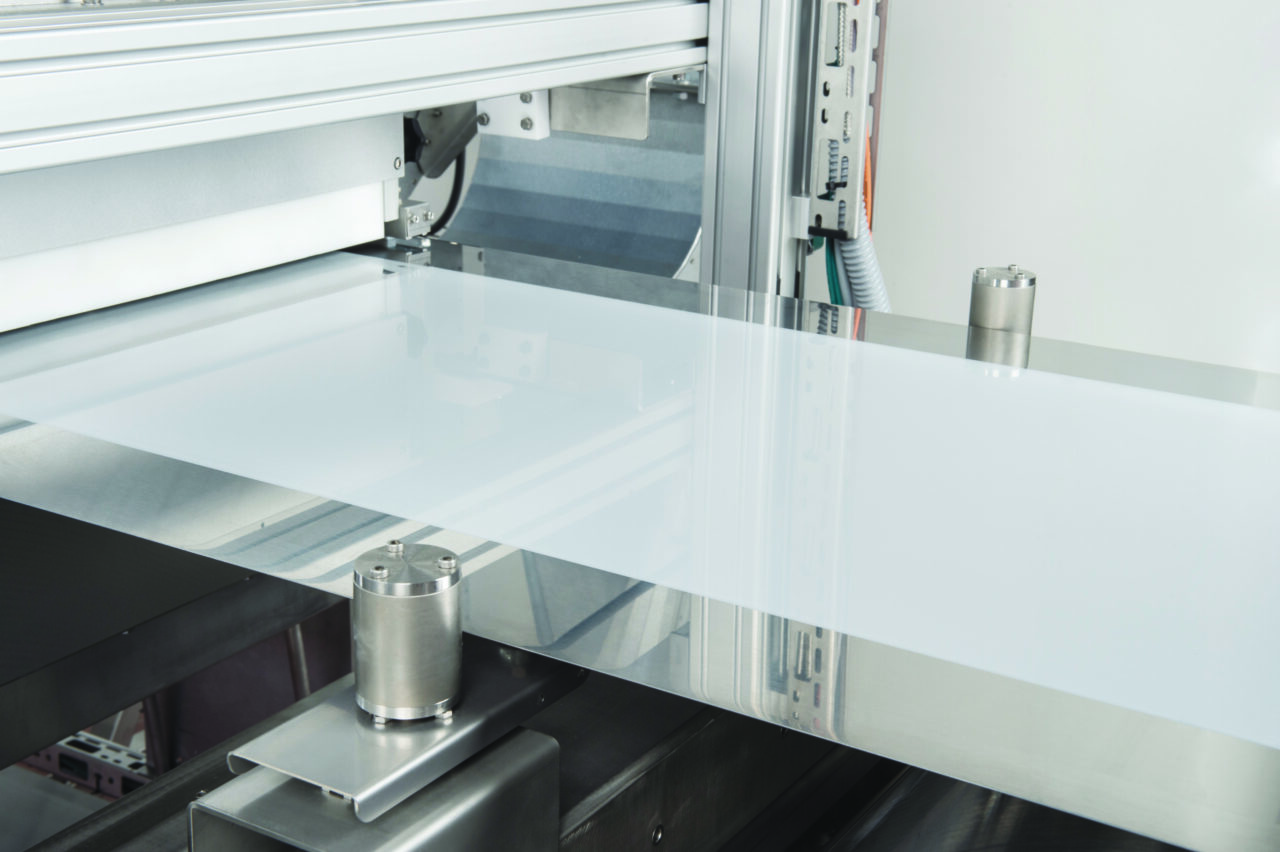
IPCO Thin film casting system – thin film on steel belt
The result is an end product of exceptionally high quality, with low stress and virtually no risk of fault and imperfections. Films can be produced in thicknesses from 5-300 µm, depending on the end application.
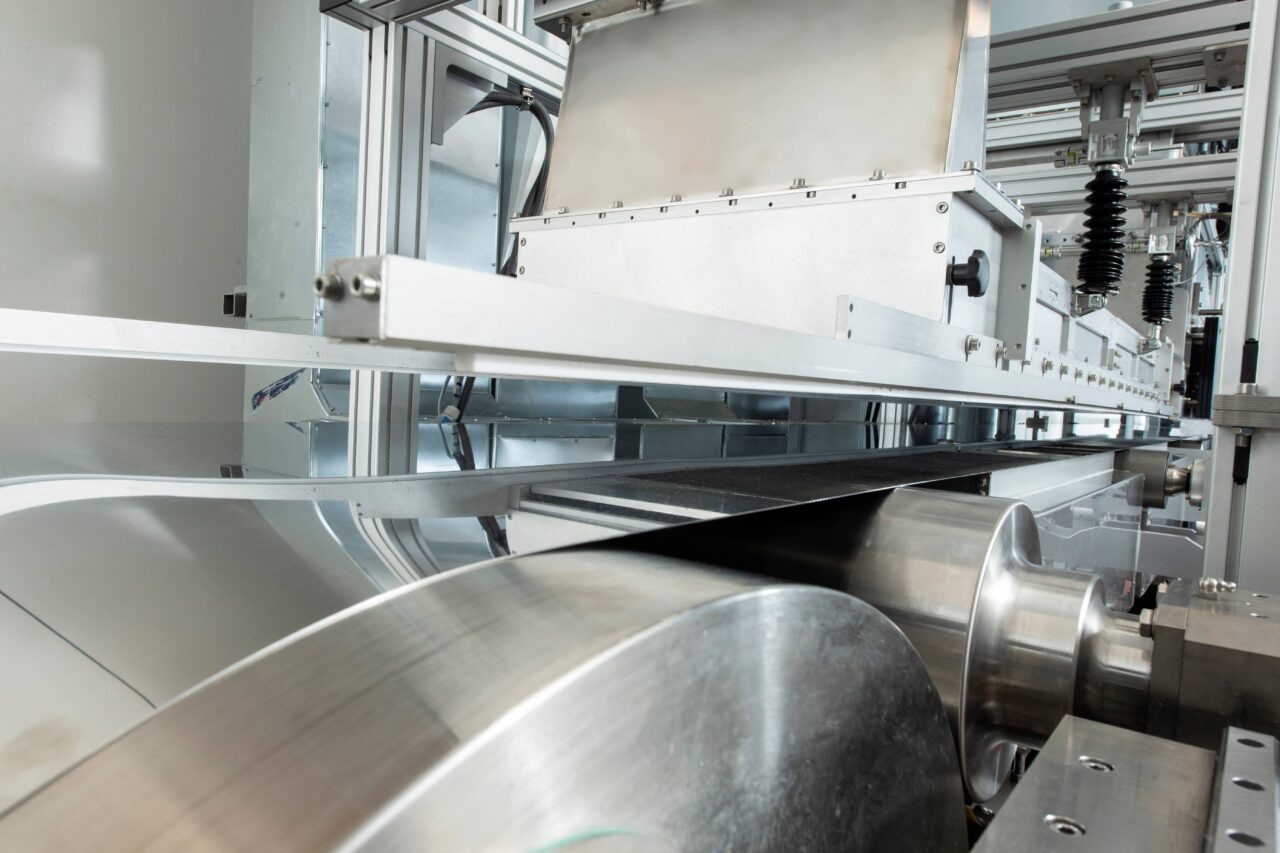
IPCO Film casting system
Precision scattering for dry process electrodes
IPCO recently announced the launch of the ScatterPro BX, a system developed specifically to enable the precision scattering of powders used in dry process production of thin electrode layers. Innovative geometries and component design allow this unique system to distribute agglomerating powders – often clay-like in consistency with a tendency to clumping – in preparation for calendaring and laminating with the current collector material.
The ScatterPro BX can be supplied in widths from 200 mm to 2000 mm, enabling solutions for everything from research facilities to full scale production. Pilot plants are available for R&D and prototyping.
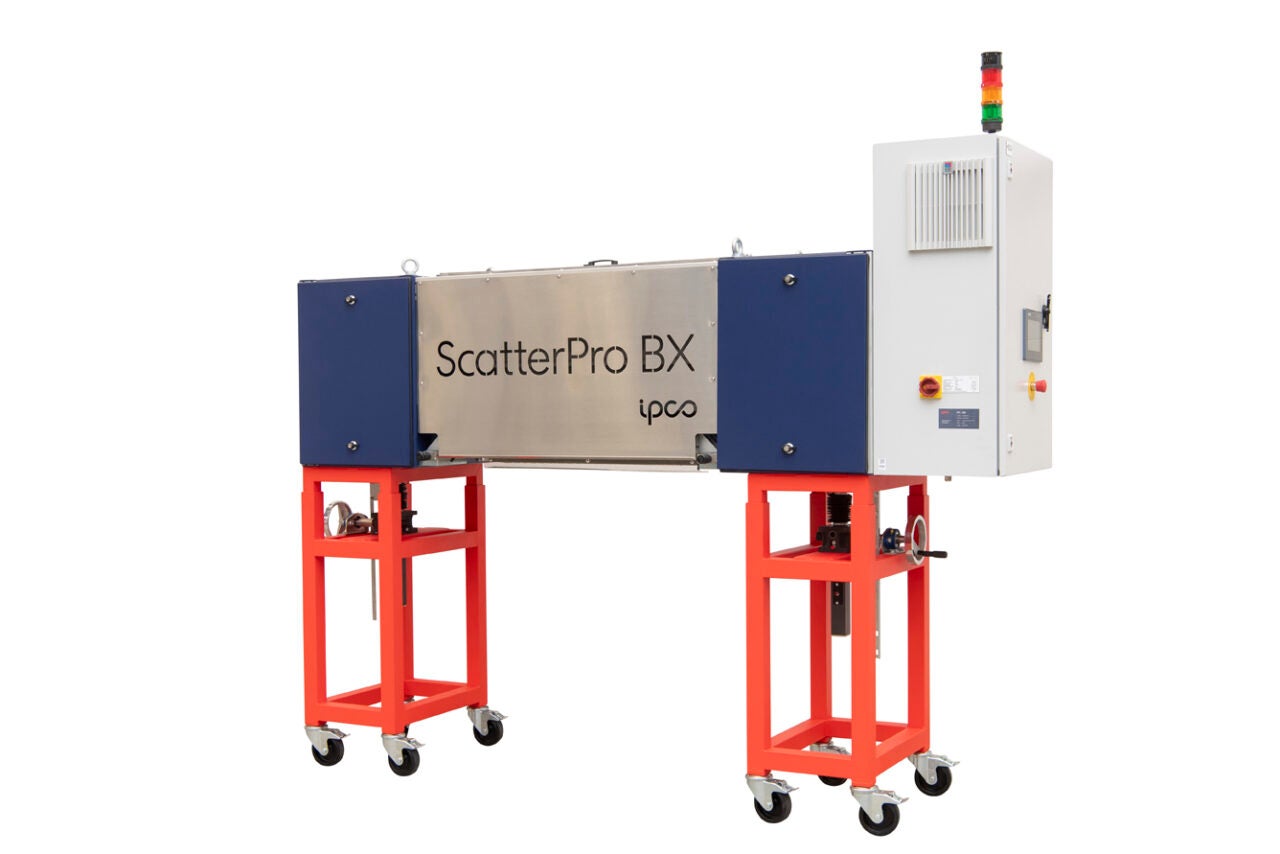
IPCO Scattering system ScatterPro BX
ThermoPress double belt press systems
IPCO is a leading manufacturer of double belt presses for the continuous production of advanced composite materials. The ThermoPress range is unique in that solutions can be based on steel belts, PTFE belts, or a combination of the two.
Delivering a carefully controlled pressure/temperature profile, these presses can be used for consolidating, compressing, laminating and densifying, making them ideal for processing continuous tapes or scattered powders for the production of multi-layer electrodes.
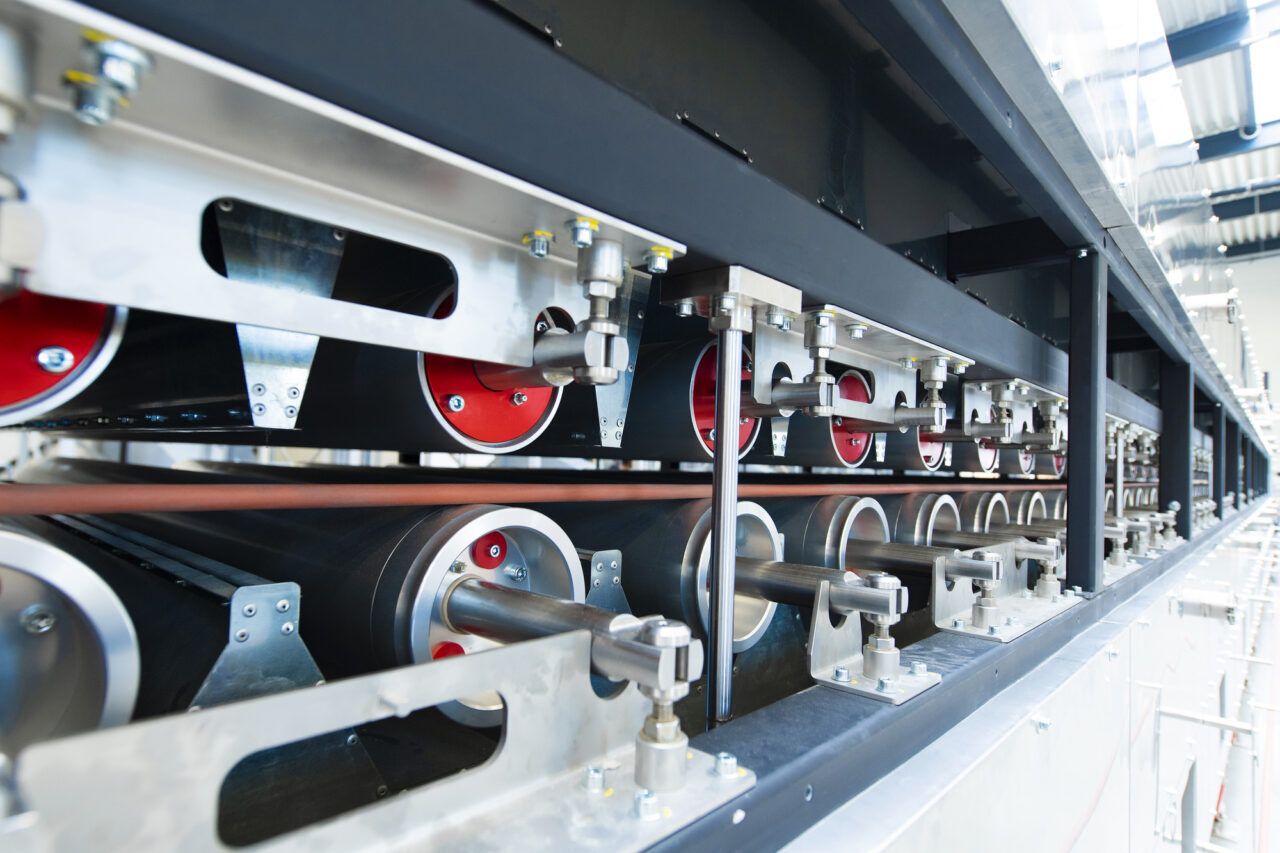
IPCO ThermoPress double belt press
Calendering systems
New Era’s calendering equipment is custom engineered to precise specifications to meet specific requirements including process temperature, pressure and width. Systems can incorporate features such as load cells for nip pressure readout and a number of different methods to counteract deflection, such as crowned rolls, roll skewing and roll bending. Other options include a downstream thickness gauge system for automatic, closed loop control of line speeds, gap settings and pressures.
Roll-to-roll coating equipment
New Era designs and manufactures pilot and production equipment for roll-to-roll anode and cathode coating, separator coating and specialty coatings for vibration dampening/thermal materials. The company has implemented simultaneous dual side coating for both horizontal and vertical drying applications, all driven by customer needs, substrates and coating rheology.
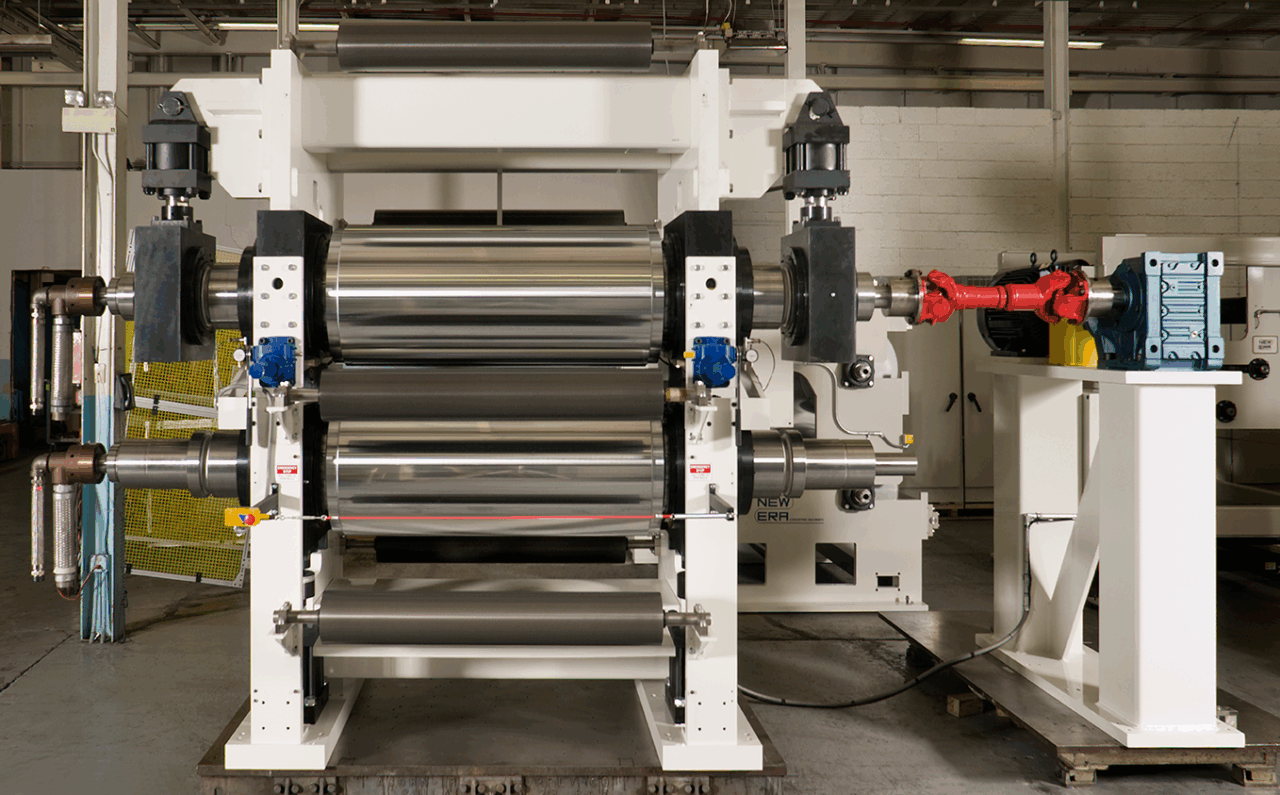
Calendering Equipment
Customer prototyping at advanced test facilities
IPCO also supports customers through its productivity centers. These advanced R&D facilities are available for process assessment and product testing, with technicians and engineers available to provide full support. All IPCO systems – film casting, scattering, pressing and calendaring lines – are available for product development and customer R&D, with feasibility studies and prototyping to support the move to the next step.
Take the opportunity to discuss with our IPCO experts — together with the newly acquired New Era Converting team — our comprehensive range of solutions for developing and producing next-generation separators, barriers, membranes, and multi-layer electrodes at The Battery Show in Stuttgart, Hall 6, Stand D76. Visit our website to learn more.