Combining process analytical technology (PAT) and the cloud for next-level productivity
Process analytical technology (PAT) enables manufacturing and processing companies to continuously enhance their competitiveness in an increasingly fast-paced and demanding market (see part 1, “Process Analytical Technology Advances,” pp. 24–31). The latest advances in data technology — particularly cloud computing — can help create an advanced PAT framework and new opportunities for manufacturers. As a result, companies can improve flexibility, responsiveness, efficiency and quality across an entire enterprise.
PAT is among the key solutions that forward-looking businesses should implement when developing smart manufacturing strategies (Figure 1). It is a realtime, data-driven framework that aims to improve process efficiency, resilience and quality by controlling critical process parameters (CPPs) within a pre-defined design space to optimize a product’s critical quality attributes (CQAs) in a timely manner. At the core of this setup is an in-depth, science-based understanding of how CPPs influence CQAs that allows businesses to implement quality-by-design (QbD) practices, where quality is built into products from the early design phases.
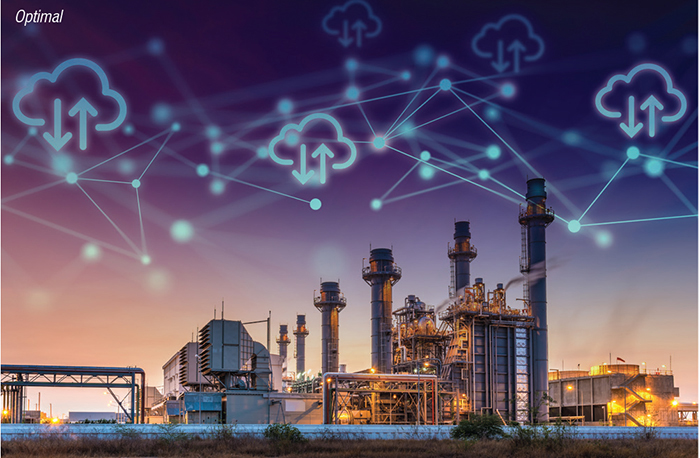
Figure 1. An advanced PAT framework, such as this commercial system that utilizes cloud computing, can help to create new opportunities for manufacturers
Future CPI production is PAT-driven
This knowledge supports the implementation of statistical process control and the creation of models for quality predictions. As a result, it is possible to make sure that all manufacturing activities are operating according to the most effective processing conditions at all times, enabling companies to consistently deliver high-quality products and reduce variability while optimizing a plant’s operations.
In addition, by supporting realtime monitoring either in-, on-, or at-line, PAT allows chemical manufacturers to move away from off-line laboratory analysis and adopt more comprehensive, as well as faster, process analytics. This transition results in a considerably improved process understanding and enhanced root-cause strategies, while also minimizing the downtime associated with quality control. For example, it is estimated that the downtime associated with quality control/assurance can be halved and the cost of quality (CoQ) can be reduced by 15% [1].
Furthermore, a PAT system can help ensure regulatory compliance as well as lay the groundwork for the implementation of lean-manufacturing and six-sigma strategies. By reducing off-specification materials via realtime quality-assurance practices, chemical processing facilities can substantially reduce waste and reworks, minimize raw material and energy utilization, as well as shorten production times. Consequently, it is possible to reduce time-to-market and support just-in-time manufacturing.
Live process control can also help to reduce overprocessing and achieve homogeneous product quality, for example, by obtaining a narrow particle-size distribution during granulation phases, further streamlining manufacturing activities [2].
Considerable savings in operational expenses (OPEX) are therefore achievable. Similarly, it is possible to optimize existing assets, reducing the need for significant new investments to increase capacity. For instance, biologics manufacturers that have adopted PAT-driven strategies have reported a threefold increase in titers (capacity) from their fed-batch units [3]. This shows that capital expenditure (CAPEX) can be optimized using the insight provided by PAT to support continuous improvement strategies.
PAT is also key to enabling the adoption of continuous processing strategies, which can further streamline production and processing operations, reducing running costs, cycle times, energy and resource utilization. In particular, a study examining the fractional cost differences between operating continuous flow and batch reactors in chemical manufacturing plants concluded that operating costs are between 15 and 40% lower when continuous processes are used [4]. More precisely, a fourth of costs for catalysts were required in hydrogenation stages while 35% could be saved in expenses associated with energy usage during nitration [4].
PAT & ‘smart’ are interconnected
To provide successful, data-driven insight into processing activities with PAT, a highly interconnected infrastructure needs to be created that can transfer, store, process, analyze and subsequently visualize the large volumes of information continuously generated. To implement an effective industrial internet of things (IIoT) system, manufacturers need to move away from conventional, centralized high-performance computing strategies that focus on supercomputers or clusters of collaborative computers. Instead, they should favor high-throughput computing, which relies on distributed data sharing and content delivery applications. As a result of this paradigm shift, it is necessary to develop suitable data fusion strategies that can facilitate the integration of readings from different instruments to create optimized quality predictions and a comprehensive process overview.
PAT can address these needs using the latest innovations in sensor and network technologies, big data analytics and data mining. In effect, it can support the creation of a highly interconnected, comprehensive and intelligent system that enables industry 4.0 applications. This ultimately facilitates next-level realtime process control and quality assurance.
While big-data technologies are extremely important, it is also essential to create a suitable infrastructure that can support them. One of the most promising enabling technologies is cloud computing, as it offers near unlimited space for storage and data processing power on demand, as well as decentralized data availability (Figure 2). Hence, it is a key tool for chemical manufacturers interested in setting up big-data-driven process intelligence strategies aimed at enhancing their operations and end-product quality.
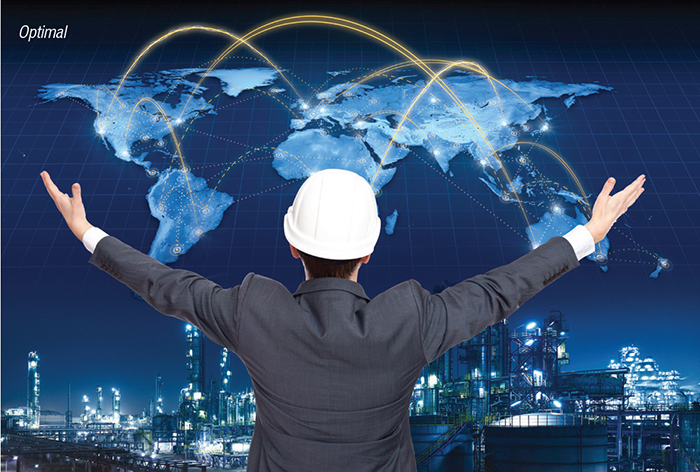
Figure 2. The cloud can enable the creation of an enterprise-wide PAT system, which is able to acquire and integrate key knowledge from multiple manufacturing facilities, regardless of their geographical location
Next-generation PAT
The next generation of PAT should support data transfer to the cloud. The cloud allows companies to truly leverage the power of big data by providing a flexible stack of massive computing, storage and software services in a scalable manner and at a low cost. It offers this without the need to build the required physical high-capacity computing infrastructures that need substantial CAPEX and OPEX as well as increase the manufacturing footprint.
A practical example can be found in (Fourier-transform) near-infrared (NIR) process spectrometers, which are able to generate multiple spectra per second. The volume of data produced by a single analyzer, let alone a network containing multiple analyzers, can quickly exceed the gigabyte range. Therefore, existing on-premises servers and data centers in chemical plants may not have the ability to store and analyze such large datasets from multiple devices and analytical instruments.
While edge computing is generally better suited to support time-critical process control, the cloud is well-equipped to address the needs of advanced process control during predictive model-building phases. In particular, cloud computing can support the creation of an extremely advanced PAT knowledge-management system that can perform complex functions and computing algorithms, which require more computing power than can be possibly provided by edge-computing devices. Time-critical model execution can then be delegated to realtime control systems, such as programmable logic controllers (PLCs) and distributed control systems (DCSs), which are acting on quality-driven setpoint changes from the cloud-based PAT system. These will then work together to automatically adjust CPPs, thus optimizing quality. Consequently, a PAT solution that can pump data to the cloud can help chemical manufacturers to set up advanced, automated operations that increase production flexibility and responsiveness.
An additional benefit of utilizing a framework that supports cloud connectivity is that companies can set up an enterprise-wide PAT system, which is able to acquire and integrate key knowledge from multiple manufacturing facilities, regardless of their geographical location. By doing so, chemical manufacturers can gather larger volumes of data, creating ever more accurate and precise predictive models. Furthermore, they can standardize processes across multiple plants, creating shared best practices. Such a system can also support multi-site collaborations and coordination. Ultimately, chemical manufacturers can optimize all aspects of their operations while increasing consistency across different factories.
Moreover, cloud-computing solutions are fully scalable, supporting expansions and upgrades within chemical manufacturing plants, even for limited periods of time. This is particularly beneficial for chemical manufacturers during model validation, as they can scale-up data processing capabilities temporarily and downsize when these activities are not required.
Data transparency and availability are also enhanced by the cloud, with multi-user access and remote monitoring supported. Also, if equipped with instant reporting capabilities, a PAT solution that supports cloud computing can facilitate and streamline the creation of suitable documentation for quality auditing or similar purposes.
Finding the ideal PAT system
To get the most out of cloud computing for process control and quality assurance, companies need to choose a PAT knowledge-management platform that can effectively pump data to the cloud. This will either utilize either “push” or “pull” methods for data transfer. In the former, data are periodically sent by each monitored system to a central data lake located in the cloud. Whereas in a “pull” architecture, a central collector periodically requests metrics from each monitored system.
Each data-transfer method benefits different applications and the specific requirements of an enterprise. For example, if advanced cybersecurity is a top priority, a PAT data pump system based on “push” methods is likely to offer the best solution, as it can support controlled access. Setting up such a system is therefore extremely important for producers supplying highly regulated industries, such as the pharmaceutical sector. More precisely, a “push” cloud-data pump prevents a network opening to a secure good-manufacturing practice (GMP) area containing the PAT’s comprehensive data. In either case, populating a cloud-data lake provides companies with the ability to expand their data-driven science using their best, established tools without accessing secure systems directly.
In addition, it can prove extremely beneficial for chemical processing and manufacturing facilities to adopt a PAT system that is able to transfer and store data in the cloud that complies with current good-manufacturing practices (cGMPs) and directives for food and pharmaceutical producers. In this case, companies need a PAT solution with cloud-data-pump capabilities that can meet regulations on electronic signatures and records (ERES), such as the European Union’s GMP Annex 11 or the U.S. Food and Drug Administration’s (FDA) 21 CFR part 11, or both. Examples of products that support data “push” to the cloud, while addressing governing standards of the pharmaceutical industry, are available.
Act now for a competitive edge
A PAT system can already offer a major advantage to chemical manufacturing facilities by interfacing with analyzers. The importance of PAT will continue to increase as companies need to create data-driven applications and highly interconnected infrastructures to realize smart manufacturing strategies. The opportunities and innovations offered by industry 4.0 technologies are also able to enhance the capabilities of PAT and increase the benefits of this framework (Figure 3).
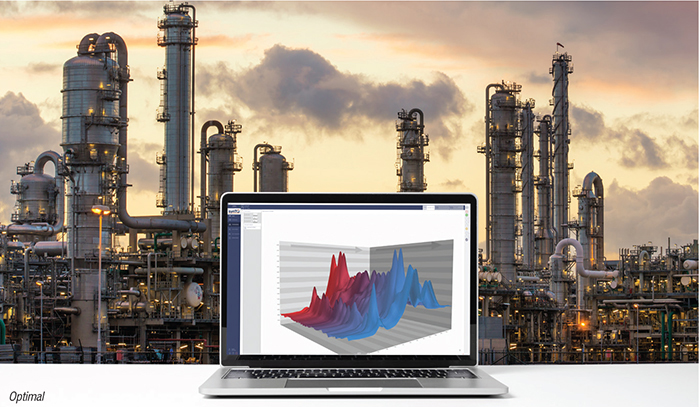
Figure 3. A data driven PAT framework, such as the commercial system shown here, can help manufacturers to greatly improve flexibility, responsiveness and product quality
In particular, a PAT framework that supports cloud computing for data analysis, storage and reporting can greatly improve flexibility, responsiveness and product quality while reducing waste, costs, energy and resource utilization. In order to fully reap the benefits of this technology, it is important for chemical manufacturers to identify a solution that can meet the needs of their enterprise and is secure, regulatory compliant and easy to access. By selecting the right system, chemical manufacturers can leverage a unique competitive advantage while future-proofing their operations.
References
1. Cogdill, R. P., Knight, T. P., Anderson, C. A., and Drennen, J. K., The Financial Returns on Investments in Process Analytical Technology and Lean Manufacturing: Benchmarks and Case Study, J. of Pharmaceutical Innovation, 2(1–2), 38–50, 2007.
2. Lee, W. B., Widjaja, E., Heng, P. W. S., and Chan, L. W., De-Risking Excipient Particle Size Distribution Variability with Automated Robust Mixing: Integrating Quality by Design and Process Analytical Technology, European J. of Pharmaceutics and Biopharmaceutics, 157, 9–24, 2020.
3. Steinhof, O., Next Generation Manufacturing at Biogen. Presentation, 2020. Available at: www.brighttalk.com/webcast/10519/450488 (accessed: November 30, 2020).
4. Calabrese, G. S., and Pissavini, S., From Batch to Continuous Flow Processing in Chemicals Manufacturing, AIChE Journal, 57(4), 828–834, 2011.
Author
Martin Gadsby is owner and director of Optimal Industrial Technologies Ltd. (5 Monarch Court, Emersons Green, Bristol BS16 7FH, U.K.; Phone: +44-1454-333222; Fax: +44-1454-322240; Email: [email protected]). He has over 30 years of experience in process automation and PAT. Before founding Optimal, he worked as R&D European Group Leader for Kraft Foods. Optimal Industrial Technologies is a market leader in the field of PAT and has developed the PAT knowledge-management system, synTQ (www.syntq.com). Gadsby graduated in engineering with an honors degree from the University of Bath in the 1970s.