As renewable energy becomes increasingly available (and less expensive), Europeans are looking to Power-to-X as a way to couple the energy, CPI and transportation sectors
Germany’s energy transition (Energiewende) from fossil-based fuels to renewables, such as solar and wind, is sparking a revolution that may change the way companies in the chemical process industries (CPI) operate in the not-to-distant future. With more than 33% of its power already supplied by renewables, and a goal to be virtually greenhouse-gas (GHG) neutral by 2050 (as outlined in the Climate Action Plan 2050, adopted November 2016), Germany is leading the charge, with many European countries joining the effort to meet the E.U.’s GHG targets set out in the Paris Agreement.
With the increased emphasis on carbon-free electricity from solar and wind power generation, many different technologies are being investigated to make this fluctuating electricity source more reliable, which is essential for industrial processes. Some of the options being actively investigated are power-to-x (PTX) technologies, which are ways to store and utilize excess renewable electricity in the form of a gas or liquid (X) that can be easily transported for use in transportation and heating, and as feedstock for producing bulk chemicals (Figure 1).
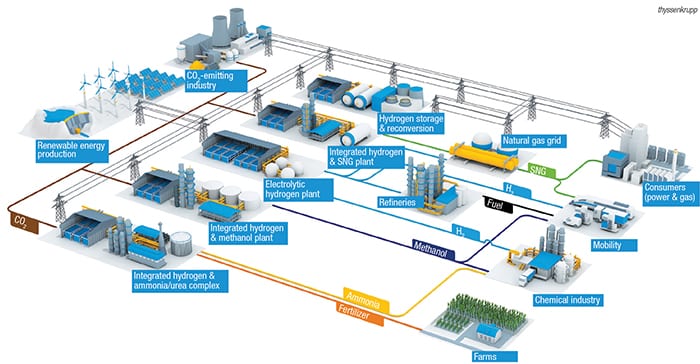
Figure 1. Hydrogen — produced by the electrolysis of water using carbon-free electricity from solar and wind generators — is the key for all power-to-x technologies
In 2016, the Federal Ministry of Education and Research (BMBF; Bonn, Germany; www.bmbf.de) introduced four “Kopernikus Projects for the Energy Transition.” One of the projects selected was PTX, which is coordinated by RWTH Aachen University, Forschungszentrum Jülich, and Dechema e.V. (Frankfurt am Main; www.dechema.de). The major project focuses on the storage of excess power into other energy carriers, with €30 million in funding from the BMBF for the first of three development phases.
Today, there are about 35 PTX projects in Germany, according to the German Energy Agency (dena; Berlin; www.dena.de), which maintains a database of the projects as part of its Power-to-Gas (PTG) Strategy Platform (www.powertogas.info). Dena established the PTG Strategy Platform in 2011 in order for partners from industry, associations and science to pool their diverse expertise and experience. The core objective is to establish PTG as a reliable, cost-efficient and large-scale multi-purpose option at least by the beginning of the years 2020–2025, with at least 1,000 MW of electrolysis power installed in Germany.
Power-to-gas: hydrogen is key
Splitting water into hydrogen and oxygen is a key step in almost all PTX schemes. Although the technology has been around for decades, water electrolysis only accounts for about 5% of the world’s H2 production, with the remaining bulk supplied from fossil feedstock, according to Manfred Baldauf, head of research group Electrochemistry, Siemens AG (Erlangen, Germany; www.siemens.com). Speaking at Dechema’s PraxisForum “Electrolysis in Industry” (22–23 November; Dechema Haus, Frankfurt), Baldauf presented the advances being made by Siemens to develop new, industrial-scale electrolyzers in order to decarbonize the production of H2 by taking advantage of the falling prices and increasing availability of renewable electricity — especially that produced from wind and solar energy. Siemens has focused on proton-exchange membrane (PEM) electrolysis — in principle, a fuel cell operating in reverse — for H2 production. Compared to acid or alkaline electrolysis, PEM offers good dynamic operation, which is especially important for fluctuating electricity, explained Baldauf, as well as producing higher purity (>99.9%) H2, and no chemicals are added. “We believe electrolysis is the chief technology for sector coupling,” said Baldauf, referring to the coupling of the power, process and transportation sectors.
Siemens first introduced its PEM technology in 2011, with the Silyzer 100, followed by the Silyzer 200 in 2015 — a 1.25-MW system with a 65% efficiency. Since 2015, three Silyzer 200 PEM systems have been operating at the Energiepark Mainz, converting wind energy into H2, which is then stored and fed into the local gas grid or delivered to surrounding industry and H2 -filling stations via tank trailers. This facility, a joint project of Stadtwerke Mainz AG, the Linde Group and Siemens, was, at the time, the world’s largest PEM electrolyzer facility.
In 2016, the Silyzer 200 was used in Germany’s first PTG plant at Windgas Haßfurt GmbH & Co. KG, which is owned by partners Greenpeace Energy eG and Städttische Betrieb Haßfurt GmbH. The 1.25-MW unit is used to stabilize the total power network by drawing excess electricity from wind and solar plants.
Last year, Siemens launched the Silyzer 300, consisting of up to 24 PEM modules for a total capacity of 20 MW, and an efficiency of 75% (without H2 compression). The first commercial application of the Silyzer 300 — a 6-MW pilot unit with only 12 modules — was commissioned at the end of 2018 in Linz, Austria, where it is featured in the E.U.-funded (€18-million) flagship project H2Future. The plant is scheduled to be fully operational this spring, producing 1,200 m3/h of H2 that will be used for steel-making processes at voestalpine AG (Linz, Austria; www.voestalpine.com), using hydroelectric power supplied by Verbund — Austria’s largest electricity company, which operates 128 hydropower plants.
Also scaling up to industrial scale is thyssenkrupp AG (Essen, Germany; www.thyssenkrupp.com), which commercially launched its advanced water electrolysis technology last year (Chem. Eng., August 2018, p. 6; www.chemengonline.com/advanced-water-electrolysis-launched). To make deployment of large H2 projects as easy as possible, the thyssenkrupp technology is available in pre-fabricated, skid-mounted standard modules (5, 10 and 20 MW each). The pre-mounted skid modules allow easy transport and quick installation with minimum effort. By simply adding them up, desired project sizes can easily be realized, up into the range of several hundred megawatts, explained Gergor Polcyn, head of Product Management & Technology Dept, Energy Storge & Hydrogen at thyssenkrupp Uhde Chlorine Engineers GmbH (Dortmund, Germany). More than 200,000 elements have already been manufactured, said Polcyn at the Dechema forum. The first demonstration unit — a 2-MW electrolyzer producing 440 Nm3/h of H2 with 99.95% purity, started up last summer in Duisburg, Germany as part of the Carbon2Chem project (www.thyssenkrupp.com/en/carbon2chem). That project aims to develop technology for converting the emissions from steel mills — composed of about 44% N2, 23% CO2, 21% CO 10% H2 and 2% CH4 — to make chemicals, such as ammonia and methanol.
Power-to-gas: methane
Although there is a large market for H2, its use as a fuel is still limited, due to a lack of infrastructure, says Marc Grünewald, head of Business Development and New Energies, Power Unit, MAN Energy Solutions SE (MAN ES; Augsburg, Germany; www.man-es.com). Therefore, MAN ES aims to build large-scale PTG plants as a way to utilize surplus electricity to make methane, or synthetic natural gas (SNG). SNG has the advantage over H2 in that it can be directly injected into existing infrastructure, where it can be pipelined for use for power generation, heating in households and as a transportation fuel, including for ships (Figure 2). “This is not simply energy storage, but rather the production of green fuels,” Grünewald says. About 50% of energy used for industry today is consumed by transportation vessels — “vessels do not want batteries, but green fuels,” he says. To reduce CO2 emissions and achieve more stringent emission targets, ships can shift from oil or diesel fuel to liquefied natural gas (LNG) or SNG, Grünewald explains. “We envision having a 50-MW power-to-gas plant in all the major harbors to supply ships.”
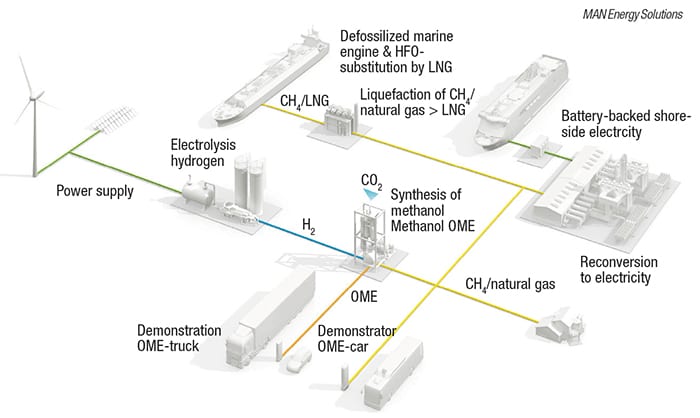
Figure 2. MAN Energy Solutions envisions having large (50 MW), complete power-to-gas plants in every major harbor to produce substitute natural gas as fuel for ships and vehicles
Since 2012, MAN ES has been operating a pilot methanation plant at an Audi site in Werlte, Germany for the production of SNG directly from CO2 and H2. The process takes place in a tubular fixed-bed reactor operating at about 260°C and 6–8 bars pressure. CO2 and H2 (mole ratio of 1-to-4) are fed into the reactor and react over a nickel catalyst to form CH4 and H2O. The water can easily be removed.
“The 6-MW power-to-gas plant in Werlte is still the world’s largest PTG plant today, and continues to run quite well,” says Grünewald. “Since it started up in 2012, we have made a number of improvements,” he explains: “The methane content has been improved from 92% to 95% today, the footprint has been reduced by 30%, and the costs have fallen by 20–30%. We can say that the methanation technology is now industrially ready,” he says. With MAN ES’s new corporate strategy, the company is targeting to have 50% renewable-energy business by 2030, with a billion or more in sales in new business, Grünewald says.
Meanwhile, others are also working to develop more efficient PTG technology. In Switzerland, for example, the Institute for Energy Technology (IET) at the HSR Hochschule für Technik (Rapperswil, Switzerland; www.iet.hsr.ch) is working on two E.U. PTG projects, says Sandra Moebus, manager, Power-to-Gas. Implemented in the E.U. project Pentagon of the framework program Horizon 2020, the project High Efficiency Power-to-Methane Pilot (HEPP) aims to boost the PTG efficiency from 55% to 70% for an industrial scale of megawatts. To achieve this efficiency boost, the researchers are using a high-temperature electrolyzer (around 600°C) to make H2, which will then be used in a methanation reactor to produce CH4. Improvements in efficiency will be achieved by tight heat integration — using the heat from the exothermic methanation reaction to heat up water for the steam electrolyzer, Moebus says. Also, a new methanation catalyst is being tested that absorbs water, a product of the equilibrium reaction, to boost the product yield. A membrane-separation process is also being used for gas purification. The 10-kW pilot plant, located in Rapperswil, was inaugurated last October, and the first production of methane is expected this month, with operation to run through 2019.
In a second E.U.-funded project, dubbed STORE&GO, three different PTG technologies will be investigated, with pilot units located in Germany, Italy and Switzerland. The first two units started last year, and the third will start up this month in Switzerland, says Moebus. These units use conventional electrolyzers, and the goal is to compare the performance and economics of the different technologies, she says.
Meanwhile, last February, 75% efficiency was first achieved in a PTG project coordinated by the Karlsruhe Institute of Technology (KIT; Germany; www.kit.edu). The four-year, €3.8-million Helmeth project, funded under the E.U.’s 7th Framework Program, achieved this milestone by optimal use of process heat from the methanation for heating the water used in the high-temperature (about 800°C) solid-oxide cell (SOC) electrolyzer of Sunfire GmbH (Dresden, Germany: www.sunfire.com). The goal of the project is to achieve 80% efficiency on the industrial scale.
Taking a completely different PTG approach is Viessmann Werke GmbH & Co, KG (Allendorf, Germany; www.viessmann.com). Its subsidiary MicrobEnergy GmbH (Schwandorf, Germany; www.microbenergy.com) has been developing and implementing various PTG projects involving its biological methanation process known as BION, in which archaea microorganisms produce CH4 from H2 and CO2. Since 2015, the first PTG plant with biological methanation, located in Allendorf (Figure 3), has been producing methane that is directly fed into the gas grid for storage and distribution, says marketing manager Eva Sonnleitner. The company is currently involved in a number of PTX projects all over Europe. “The storage of renewable electricity, the production green gases and the upgrading of CO2-rich sources are our main scopes,” says Sonnleitner. “In these projects, we expect a planning and realization period, from initial contact until commissioning, of two to three years. These are plants in the megawatt range. For individual projects, we are close to the official announcement now,” she says.
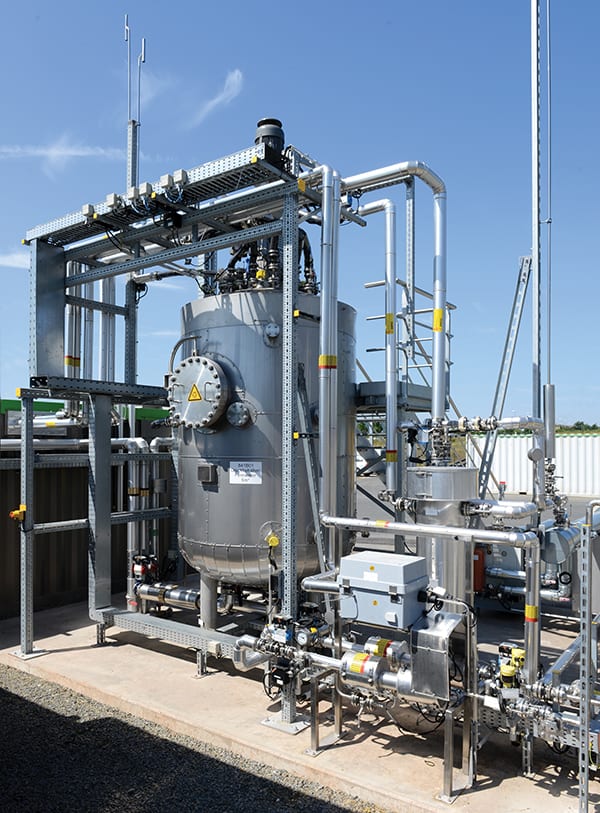
Figure 3. This biomethanation unit in Allendorf, Germany, uses microbes to convert hydrogen and CO2 into methane
Source: microbEnergy
Power-to-liquids
“Many recent studies predict an ongoing dependency on carbon-based fuels,” says Tim Böltken, managing director, Ineratec GmbH (Karlsruhe, Germany; https://ineratec.de). “In this context, we are absolutely convinced that power-to-fuels, such as gaseous energy carriers (PTG, especially power-to-methane), as well as liquid energy carriers, such as gasoline, kerosene and diesel (power-to-liquids via Fischer-Tropsch (F-T) synthesis) will be one of the foundations for the coupling of the sectors transport, energy and industry,” says Böltken.
Ineratec — a spinoff company from KIT — has developed chemical microstructured reactors that are suitable for integration into containerized plants. Because they are modular, the plants can be integrated into various energy related sectors. The core of the synthesis reactors is microstructured, which provides a large surface area for heat and mass transfer. Reactors are available for methanation, F-T synthesis and methanol synthesis.
The company is participating in numerous public and industrial PTX projects with various foci, both on the national and international level, Böltken continues. “Objectives of these projects are, for example, the scaleup of the technology in the megawatt class and the industrial production of liquid fuels for transportation and aviation. In the future we will standardize our modules in order to accelerate the realization of the PTX plants and focus on the energy-efficient integration of our synthesis technology in industrial sites.”
“We have successfully delivered a PTX plant with a 250-kW electrolyzer capacity,” Böltken continues. “Now we are building the first plant in megawatt class and we are currently taking the step from manufacturing to serial production. The interest of the industry, especially the energy and the gas industry, is very high: we just received [last November] the innovation award of the German gas industry.”
Ineratec is already commercializing its technology, having installed plants in Spain and Switzerland. A large megawatt facility will be realized in 2019, with even larger capacities to come soon. By 2021, it is very likely the company will have sold more than 50 plants worldwide, says Böltken.
Meanwhile, EDL Anlagenbau GmbH (Leipzig, Germany; www.edl.poerner.de) is involved in several PTX projects, mainly for the production of fuels and chemicals, with capacities ranging from 65 to 8,000 tons. These PTX projects use the CO2 direct air-capture technology from Climeworks (Hinwill/Zurich, Switzerland; www.climeworks.com) for the CO2 source. One key technology driver for PTX, on the production side of synthesis gas (syngas) from CO2 and H2O, is the combination of the steam electrolysis with the CO2 conversion to CO in a single electrolysis cell. Sunfire’s solid-oxide electrolysis cell (SOEC) technology will be used in EDL’s upcoming projects for the first time for syngas production. The syngas is converted to paraffinic hydrocarbons (e-crude) using a F-T process. For smaller capacities, EDL will rely on the F-T technology from Ineratec. The e-crude is converted to finished products, such as fuels or waxes, by a combination of catalytic process steps.
One PTX project for which EDL has recently completed the conceptual design phase, together with its strategic partners Climeworks and Sunfire, is the Norwegian Nordic Blue Crude (NBC) PTL project to be implemented in Norway, in the industrial park of Heroya, located 140 km southeast of Oslo. The PTL plant will produce 8,000 ton/yr of raw e-fuels and e-waxes from renewable hydropower (Figure 4). It is planned to start up in 2022.
Three other PTX projects cover the production of e-Jet A1 aviation fuel in modular plants, with capacities of 65, 130 and 260 ton/yr. These plants are installed in close vicinity to local airports. The engineering for all three projects will start in 2019, says EDL.
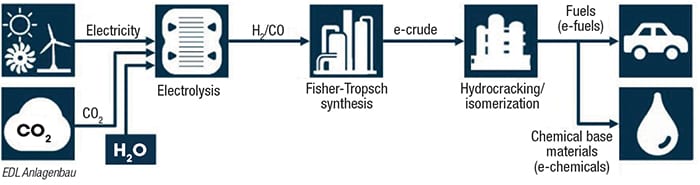
Figure 4. Scheduled to start up in 2020, the power-to-liquids plant in Norway will use hydroelectric power to make H2 from water, the water-shift reaction to make CO from CO2, and F-T synthesis to make liquid fuels and waxes