Follow this guidance to improve results on capital projects
The opportunities for modularizing industrial and chemical projects are growing at an amazing pace. Once considered a mitigation strategy only for projects in remote areas with harsh climatic conditions or a shortage of skilled labor, modular execution is now prevalent across the chemical process industries (CPI). Even developing countries that have ample local labor, good site access and have previously executed “stick-built” execution are moving toward modular execution. Why? Because of the opportunity to yield improved overall project results.
Modularization, which involves the pre-assembly of structures away from the primary construction site (Figure 1), has been popular since the 1970s. Modules come in various sizes and shapes, from very large modules that are transported by barge, to smaller, truckable modules that may fit in a sea freight container. Modular execution provides many benefits, including improved labor productivity and quality, due to better controlled working conditions, and reduced health, safety and environmental (HSE) risks that arise when the need to work at elevation is reduced.
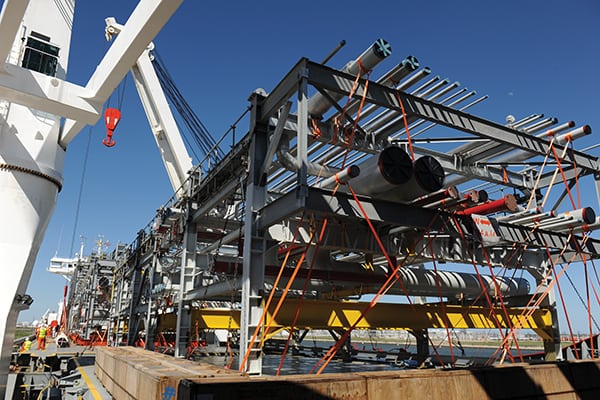
FIGURE 1. Modularization, the pre-assembly of structures away from the primary construction site, has many benefits, including improved labor productivity and reduced HSE risks
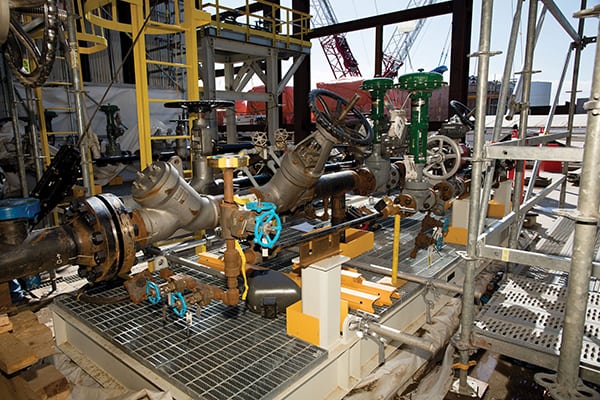
FIGURE 2. Input from operations and maintenance teams is required early on in the design process to ensure that modularized facilities can be easily maintained
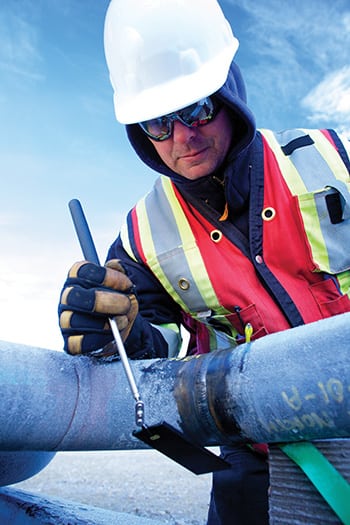
FIGURE 3. Projects should have a quality presence,
as well as a advanced
quality program, in the
fabrication yards
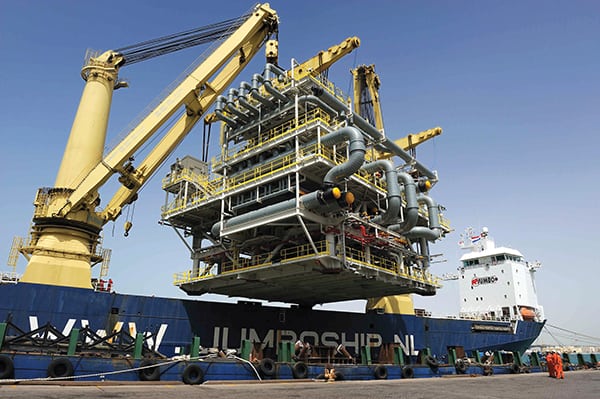
FIGURE 4. Transport of modules by ocean or barge requires different design considerations than modules that will be transported via truck
Modular projects, executed appropriately, can save time and money. A well-developed modular-execution strategy should create an integrated solution — as opposed to a hodgepodge of project scopes that are broadly planned but broken into separate engineering, procurement, fabrication and construction packages. Often, project managers do not consider that the additional interfaces are required between various organizations raise the potential for more disconnects, with no single organization having overall end-to-end accountability for the project. Integrated, innovative solutions are key for a modular execution outcome to be sucessful.
Modular engineering
This approach entails clearly identifying and procuring the right materials to be delivered at the right time to the right location, and providing timely responses to all queries. This latter aspect is typically not emphasized, but is a prime opportunity to enhance and influence a project’s successful outcome.
One key aspect of successful modularization is to adhere to the concept that modularization drives layout — rather than layout driving modularization. Technically, this concept creates huge challenges and often dissuades clients and project managers from embracing modularization, but it can deliver significant project benefits.
Some of the radically different design approaches are not well known. These design approaches include plug-and-play technology (where modules go through significant pre-commissioning and testing at a fabrication yard and are then nearly ready for operations after being set into place) and elimination of pipe racks between process areas of a facility.
While some projects claim success with piperack modularization, they miss the recent step-change improvement in modularization where elimination of pipe racks is the goal (rather than just modularizing pipe racks). Such radical plot-plan reorganization by process blocks requires all engineering disciplines to be re-focused and aligned to support this goal. Some key considerations include the following:
- The establishment of a proper work-breakdown structure (WBS), which has all designs and materials coded for correct destination and installation scope. The WBS delineates the module assembly yard versus the jobsite. It avoids the use of the term “field,” which can be misleading or unclear as to whether work is taking place at a module-assembly yard or at the ultimate jobsite
- The use of an accurate, continuously updated and accessible module index and dashboard that provides realtime information on design status and material availability
- The ability to obtain early reliable vendor data, particularly with respect to instrumentation and controls
- Additional management of pre-packaged equipment and the detailed integration of those components into the overall project’s material-identification and numbering system
- Adherence by all engineering disciplines to an advanced (early) schedule
- Careful weight management to control module size and minimize any shipping and installation surprises
- Modular-fabrication plans that maximize installation, pre-commissioning and testing prior to shipment of completed modules to the jobsite (using a plug-and-play approach)
- A construction sequence that is defined early and does not change
Module designs
Important design aspects include efforts to ensure the following:
- Appropriate safety distances and spacing between equipment and process blocks
- Unobstructed emergency-escape routes
- Efforts to address permanent maintenance requirements (monorails, lifting beams and more)
- Efforts to incorporate ergonomic considerations for operation, with consistency and standardization in design
- Establishment of underground utility routings and pile and foundation locations
- Excavation and piling: 35% reduction is typical
- Concrete: 60% reduction
- Piping: 20% reduction
- Electrical: 30% reduction
These multiple work fronts enable labor to be shifted in case of a change in one area. In contrast, modular assembly is similar to assembly-line work in manufacturing, where progress halted in one part of the assembly line slows down the whole line.
Modularization can move a significantly high percentage of the total construction work to the module assembly yard. Modules for a project are assembled at a module-assembly yard, rather than at the jobsite, thus transferring work that would have taken place at the construction site to the module assembly site. Accordingly, engineering support at the yard needs to be greater in numbers than at the site. Answers to requests for information from the module assembler should be answered the same day, if possible, to prevent delays.
When it comes to modularization efforts, successful engineering is carried out with the end in mind. The construction department’s early, continuous and unchanging involvement in the design phase eliminates surprises when the time comes to build the modules and execute the remaining work at the site.
Construction and operations teams should provide input related to the ability to construct a design, as well as access and how construction will progress through the jobsite. These plans must be diligently followed through execution, as changes create untimely rework and yield unnecessary challenges. Items on modules that are not secured into place are often overlooked during engineering and planning. The items not physically secured to the module get tricky to manage and often get lost in the assembly, completion and shipment work process.
Many modularization projects also benefit from reduced material, equipment and fabrication costs through increased use of global sourcing. While some project teams have been hesitant to work with overseas vendors, the past decade of successes (and a few highly publicized failures) has fine-tuned the global supply chain and created numerous successes on projects. Critical to this success is engineering’s understanding of the fabricators’ local conditions to manage the fabrication and achieve a win-win solution.
Procurement and fabrication
End-to-end materials management has become a complex, international endeavor. Low-cost global supply and fabrication create a capital efficiency that allows many projects to be sanctioned that otherwise would not have been able to move forward. If global supply and fabrication are implemented as part of a project’s execution plan, several key items should be addressed.
To mitigate quality concerns, projects should have appropriate quality personnel and resources in the module-assembly yard and at the global supplier locations. While this is a good first step, an additional valuable step is to implement an advanced quality program at the fabricators, as materials, such as pipe, steel and vessels, are also sourced from other global suppliers. Aspects of such a program include training the supplier’s workers in the quality requirements and providing a physical sample of pieces of work, such as welded pipe, to clearly demonstrate the level of quality expected.
Modular fabrication and assembly facilities often have space limitations that can impact the material-delivery aspects of the procurement plan. With the “module-in-a-box” delivery concept, all materials necessary to fabricate a module are shipped to the module-fabrication yard at the same time.
This approach is widely considered mandatory when delivering materials and equipment to a module-assembly yard. Driven by the assembly-line manufacturing concept, having 100% of the materials on hand prior to starting a module’s assembly is the norm. If a module is taking up yard space and cannot be finished on time, it potentially prevents another module from having the space available to be started. This sequencing is a key factor in the procurement, logistics and fabrication planning effort.
Material delivery to a module assembler can either be direct from vendors or via an intermediary marshalling yard that is set up to receive and stage materials and equipment. If a module assembler has a robust receiving and warehousing program, a project can consider having deliveries come directly from vendors. However, it is more likely that module assemblers are more focused on fabrication and thus allocate the majority of their yard to standing and building modules, instead of storing and staging materials.
Delivery using the module-in-a-box scenario requires an intermediate marshalling yard be set up to receive, separate, organize and report upcoming deliveries. This clear line-of-sight to the project team enables proper decisions to be made on when module assembly starts, and allows a project to change sequencing when one module is trending late. It serves as a risk-mitigation technique, allowing work to easily be moved from one module assembler to another, in case of schedule slippage.
If a module’s material has already been delivered to one module assembler, it is very difficult to retrieve it to give it to someone else. A marshalling yard also allows for the segregation of bulk materials by module, since many vendors are not set up for (and typically charge extra for) sorting and separating items prior to shipment.
A typical oversight is the integration of pre-packaged equipment into the overall module-execution program. Careful cross-referencing of equipment tags and material commodity codes from the pre-packaged equipment vendor, as well as proper identification of interfaces with the rest of the design, is imperative.
Some module assemblers may use poor integration of pre-packaged vendors into the overall project as an excuse for delays and schedule extension requests. Rather than forcing the pre-packaged equipment vendor to comply with a project’s WBS or numbering system, instead focus on building a concise and comprehensive cross-referencing system and interface matrix to give the module assembler the information needed to install the equipment package in the various modules.
Finally, a module-fabrication program requires a robust material-management software tool and work processes that will ensure that data are kept up to date and the information accessible. Many hours can be wasted trying to resolve data inconsistencies between systems that report different material-availability and forecast-delivery dates. There are significant advantages to using a program-wide system that an integrated solution provider can bring to the table.
Logistics
One of the most critical early decisions to be made on the project is the maximum size of the modules. Often this task is left entirely to the engineering group to plan, without due consideration to finished module shipping envelopes and potential road, rail and sea transport weight limitations.
Developing a route survey from the module assembler to the final installation location is critical at the very early stages of the project. There have been cases where the importance of these decisions has not been properly understood, and this has led to unwanted surprises that require drastic changes to modules far too late in the project.
Ocean-going transport should use the services of a qualified and experienced marine surveyor early in the project. Specifically, this input is required at the initial engineering stages to help design temporary (removable) shipment-related bracing and supports.
Even land-based module transportation requires careful coordination. For example, ensuring that a module is assembled at a proper height above grade for ease of loading may be overlooked. It is best to integrate the shipping beams into the module design, instead of utilizing third-party rented shipping beams and trying to recycle them in time for the next module shipment.
Global sourcing also brings considerations related to import and export compliance and anti-dumping laws. Special expertise is needed in this area to avoid surprises related to the disposition of surplus materials and moving materials in and out of special economic-exemption zones. An entire article can be written just about this one area, but the best strategy to avoid surprises is to use a person with proven expertise.
Assembly and installation
Business and project drivers, risks and constraints influence the decision to incorporate modular execution into a project plan. The decision to incorporate modular execution can stem from possible adverse jobsite attributes in the following areas:
- Site safety
- Site conditions, weather and remoteness
- Availability and cost of labor
- Site location, transportation and other indirect costs to support site labor
- Efficiency and productivity at the site
- Overall quality
Similarly, modularization benefits from the use of a more consistent work environment. The benefits of transferring construction and labor costs from a congested jobsite to a controlled assembly environment at the module yard can be significant. The reduction in jobsite labor hours also helps to mitigate the risks associated with skilled or limited local (jobsite) labor required to support the project schedule. It also reduces peak manpower, which reduces the overall jobsite indirect requirements, such as support staff and tool rooms, and can reduce the dependency on the adverse qualities of the jobsite.
The controlled environment that is typical of a fabrication and modular assembly yard also enables improved quality control and inspection. Teams should focus on detecting design, equipment and fit-up issues at the shop with adequate time to carry out repairs before a module transfers to the construction site. Sending incomplete modules to the site will have follow-on impacts, resulting in late project completion.
Specific consideration must be accounted for in the schedule to integrate module delivery and the sequence of placing modules at the jobsite. Construction should plan for some staging of modules prior to setting, but avoid excessive storage durations in order to minimize the required extra space for modules to be stored at the jobsite prior to being set into their final places. An integrated module and equipment setting plan requires that all teams proactively communicate, as modularization is heavily dependent on proper schedule and logistics management, and thus deviations can easily appear. It is critical to identify risks related to possible scenarios in advance and be prepared to implement contingency measures, as needed.
As the modules are set into place at the jobsite, multiple work fronts start to open, including the completion of all module interconnections and terminations, and commencement of construction testing and pre-commissioning. Advances in module lifting and setting technology have enabled the use of advanced rigging systems that can be adjusted rapidly to accommodate various module sizes and configurations. Use of these systems increases the setting pace of modules, thus increasing work-front availability. Work fronts encompass available space for construction and work. For example, only after a module is set into place can further work take place to finish it, connect it and test and energize it. With advances in module lifting and technology, modules can be set faster and work fronts opened more quickly. This provides the onsite construction workforce with more available areas for work and the ability to finish the project faster. Investments in this new technology can benefit the schedule immensely.
The construction group will be the recipient of the modules and the modular design. The continued interface with the construction group during all stages of the project will enable a successful module-delivery plan.
Pre- and site commissioning
This input must continue to be an iterative process through formal reviews, or by identifying and addressing issues during design development.
As module walkdowns are completed, areas such as pressure testing, electrical and equipment testing and pre-commissioning can be incorporated into the turnover strategy from the fabrication or assembly company to the jobsite. By incorporating these activities into the turnover strategy, testing and pre-commissioning can be completed in the controlled environment of the module-assembly yard.
The quality assurance of the work is monitored to ensure all modules are fabricated in accordance with specifications and standards prior to loading for transportation to the site. The systems-turnover documentation must also be completed for immediate retrieval at the site.
Transporting a tested and pre-commissioned component of an overall site minimizes startup timing after module delivery, as well as site installation and commissioning costs and schedule.
Closing thoughts
The design of a module provides additional complexities that need to be effectively addressed. This approach will challenge many traditional design and execution methods. Overcoming these challenges will help all stakeholders to deliver success and overall improved project results.
Edited by Suzanne Shelley
Susan Halford is in project management at Fluor Corp. (55 Sunpark Plaza SE, Calgary, Alberta, Canada, T2X 3R4; Email: [email protected]). A certified project management professional, she has been with Fluor for 10 years, and has 18 years of experience with engineering, procurement and construction (EPC) and construction companies within the oil-and-gas and mining industries. Halford’s professional experience focuses on project management, module coordination, offshore fabrication management, engineering coordination, project controls, materials management, IT project management and infrastructure design, with a keen focus on project team environments to manage projects and lead teams effectively to achieve project objectives.
Tony Kretzschmar is a project director at Fluor Corp. (55 Sunpark Plaza SE, Calgary, Alberta, Canada, T2X 3R4; Email: [email protected]). A registered professional engineer, he has been with Fluor for more than 28 years, with experience in engineering, operations, materials management and project management across Fluor’s business lines. For much of his career, Kretzschmar has led and supported projects implementing modular execution. This work has taken him from his native Canada to working overseas in India, China and Mongolia for more than half of his career. He is also a member of Fluor’s Business Transformation & Innovation team leading various innovation initiatives.