In any given chemical processing facility, there may be literally hundreds of operational environments that require protection from excessive pressure. Both rupture disks and pressure relief valves, or the two used in combination, help protect against damage to equipment and injury to personnel. While the basic technology for either type of mechanism has not changed much in recent years, tweaking the manufacturing process has resulted in pressure relief devices that last longer and perform better.
Rupture disk trends
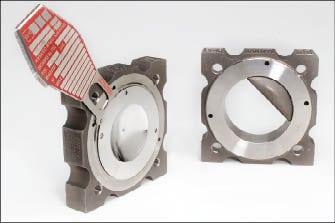
A significant change in the rupture disk industry is the rise of reverse buckling disks over forward acting disks. While reverse buckling disks are not new, per se, over the last few years manufacturers and users of overpressure products are seeing the benefits of reverse buckling products materialize.
“With forward acting disks, the pressure is on the concave side, but when you flip the disk over as with a reverse buckling disk, the pressure pushes against the dome,” explains Mark Holt, vice president of engineering with Oseco (Broken Arrow, Okla.). “The benefit is that you change the stresses and start acting on a compressive load for the materials. In applications where there is a lot of cycling, it provides a longer life for the rupture disk and the ability to control burst pressure through the material itself.”
He says each manufacturer may put different score patterns on the material to make the disk open in different ways, but the real benefit comes from the higher cycle life due to the reverse action.
Another distinct improvement is increased operating ratios (how closely to the disk’s set burst pressure a user can operate the system). “What we’ve had over the history of rupture disks is an increase in this value because it benefits disk users to be able to run their system as close to the failure point as is possible so they may get the maximum process or product through their system,” says Holt.
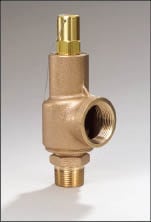
The upper limit used to be around 90%, but recently it has climbed to 95%, which is a result of increased manufacturing capabilities and variations in the processes used to make the disks.
Many of the newer disks combine the benefits and offer both higher cycling and higher operating ratios. Oseco offers the Opti-Gard, which is peripherally scored on the vent side for accurate burst control. With a 95% operating-to-burst pressure ratio and a performance tolerance of three percent, Opti-Gard has been tested to more than 100,000 cycles. And its architecturally engineered burst pressures allow the device to provide these advanced performance characteristics in liquid, gas or vapor applications.
![]() |
Figure 2. With a 95% operating- to-burst pressure ratio and a performance tolerance of 3%, Opti-Gard has been tested to more than 100,000 cycles Oseco
|
Similarly, Fike’s (Blue Springs, Mo.) Axius rupture disk is also high cycling and offers a high operating ratio. Designed for use in aggressive chemical and pharmaceutical applications, this reverse-acting rupture disk is available in corrosion-resistant materials and has very tight tolerances. It operates at up to 95% of its marked burst pressure for burst pressures over 40 psig and up to 95% of the minimum of the burst tolerance at 40 psig and below. Also, the device is capable of cycling from full vacuum to 95% operating ratio in excess of 100,000 times, even at the lowest burst pressures that are available.
“One-hundred-thousand cycles is more than any disk would see in a lifetime, and even after 100,000 cycles, it showed no fatigue of any kind,” says Michael Zitariuk, global product manager for pressure relief with Fike.
Some manufacturers are also developing new disk-holder combinations with significant benefits. One such case is BS&B’s (Tulsa, Okla.) Sure-SAF System, which includes the CSI rupture disk combined with the CSR-7RS Safety Head to provide accuracy and reliability. The partnership of disk and holder ensures that the CSI disk bursts at or below its certified burst pressure even if the disk is installed in the wrong direction or becomes damaged.
The CSI rupture disk uses SAF (structural apex forming) technology, the central feature on the disk dome, to enhance the accuracy of burst pressure. At its burst pressure, the CSI rupture-disk dome reverses and opens by shearing around a circular score line located at the perimeter of the dome. The CSR-7RS Safety Head outlet contains an energy absorbing hinge that aligns with an unscored portion of the CSI rupture-disk perimeter that retains the CSI disk upon opening, avoiding fragmentation.
Should the disk in its holder be accidentally installed the wrong way, it will burst at or typically below its burst pressure. This “fail-safe” design feature is called the reversal safety ratio. If the CSI rupture disk is accidentally damaged, it will reverse at a reduced pressure and interact along its circular score line with stress raising features in the CSR-7RS Safety Head to open at a reduced burst pressure.
Relief valve improvements
In general, the design of pressure relief valves is not much different today than it was when the first spring-loaded models were invented in the 1800s, says Bert Lowden, president of Aquatrol, Inc. (Elburn, Ill.). “However, manufacturing technologies have improved over the years allowing valve makers to hold closer manufacturing tolerances, which have resulted in improved operation of the valves,” he says. “Manufacturers have also changed the internal structure of the valves to maximize valve relieving capacities.”
However, Rupture Pin Technology (Oklahoma City, Okla.), offers the Rupture Pin valve that Julian Taylor, president of the company, says is superior to rupture disks, spring-loaded conventional valves and pilot-operated valves. These valves consist of a piston on seat, restrained from movement by a slender round pin known as the buckling pin. The piston and seat have a bubble-tight seal while under pressure. The pin will buckle at set point from an axial force applied by the system pressure acting on the piston. Each valve is self-contained and self-acting. When the pin is buckled, the valve is full open in a matter of milliseconds, says Taylor. The pin is external to the system being protected and is tightly held in place at both pin ends.
Taylor says the benefits of Rupture Pin technology include the inability of the pins to fatigue, maximum operating pressures to 95% of set point, zero leakage to set point and nearly foolproof pin installation.
Joy LePree