Steam and condensate-return systems can be susceptible to unique forms of corrosion. This overview explains how to prevent or minimize such issues
Steam is utilized for process heating and other applications at thousands of industrial plants in the chemical process industries (CPI). Often, a significant portion of the steam condensate is recovered and returned to the boilers. Depending on the plant processes the steam serves, the condensate may contain any number of impurities that range from acidic compounds to organics to mineral salts. These impurities can cause corrosion and failure of condensate return piping and equipment, and they can potentially induce serious steam-generator corrosion and fouling. This article provides an overview of several critical issues in this regard and outlines techniques for chemically treating the steam/condensate and polishing the condensate return to reduce corrosion and scaling potential.
Potential boiler problems
The steam generator itself may be the source of a common condensate impurity: carbon dioxide. High-pressure utility boilers require high-purity makeup (contaminants not exceeding low parts-per-billion concentrations) as a result of the high temperatures and pressures in these units. However, the much lower heat fluxes and pressures in many industrial units allow less stringent makeup. Table 1 outlines some general guidelines, extracted from a well-known American Society of Mechanical Engineers (ASME) booklet [1] regarding impurity limits in low- to medium-pressure industrial water-tube boilers. The booklet contains additional details on these guidelines.
A popular makeup treatment for many boiler units, and especially those operating under 300 psi pressure, is basic sodium zeolite softening to exchange calcium and magnesium, the hardness ions, for sodium. This minimizes the potential for common scale deposit formation, with calcium carbonate (CaCO3) being the most prevalent.
Ca2+ + 2HCO3 – + heat → CaCO3 + CO2 + H2O (1)
However, sodium softening does not remove other impurities, including bicarbonate alkalinity (HCO3–). On reaching the boiler, this constituent is in large measure converted to carbon dioxide via the following reactions:
2HCO3 – + heat → CO32– + CO2 + H2O (2)
CO32– + heat → CO2 + OH– (3)
The total conversion of CO2 from the combined reactions may reach 90%. CO2 flashes off with the steam, and, when it re-dissolves in the condensate, can increase the acidity of the liquid.
CO2 + H2O ↔ H2CO3 ↔ H+ + CO32– (4)
Although the pH generated by this reaction has a relatively mild lower limit, the acidity is more than enough to cause significant carbon steel corrosion. For example, 3 parts per million (ppm) of CO2 in pure steam condensate will lower the pH to 5.26. If dissolved oxygen is present in the system, corrosion can be greatly magnified.
Several methods are available to counteract the influence of CO2 carryover with steam. One choice is to upgrade the makeup treatment system to capture or remove alkalinity. A scheme utilized in years past was split-stream dealkalization, with a sodium softener and strong acid cation exchanger placed in parallel, followed by a downstream forced-draft or vacuum decarbonator. Both sets of ion-exchange resins remove hardness, but the acid generated by the cation exchanger converts alkalinity to CO2, which is removed in the decarbonator. The process does not remove other impurities, including chloride, sulfate or silica, which then concentrate in the boiler and must be controlled by blowdown.
Another alkalinity removal method is dealkalization in the chloride mode. This ion-exchange process utilizes an anion exchanger directly after the softener. The anion unit removes total alkalinity and sulfate ions. If caustic is added, natural CO2 is removed along with some silica. However, for every part of alkalinity removed, one part of chloride is added. Nearly complete alkalinity removal can be attained, but this may require an increase in boiler blowdown because of the added chlorides.
A more modern approach comes from the maturation of water-treatment membrane technologies. Reverse osmosis (RO) is a core component of many makeup water treatment systems (Figure 1), and even a single-pass RO can remove over 99% of the impurities from the makeup.
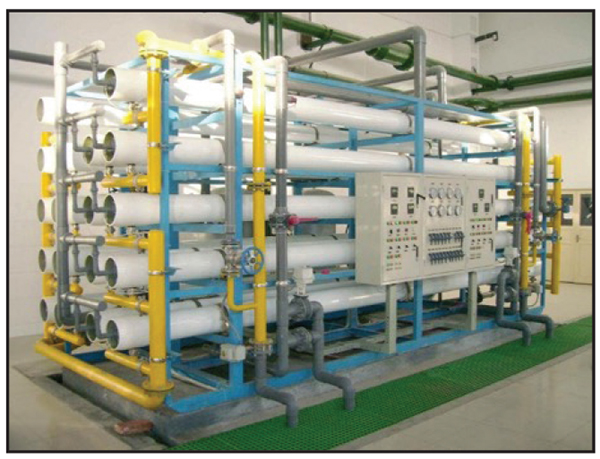
Figure 1. Shown here is a skid-mounted reverse osmosis (RO) unit
Such technology can often be the best choice for a new plant, where the steam-generation chemical-treatment program is selected for the higher-purity makeup. However, careful thought and planning is needed if such a change is made at an existing facility. The switchover from softened or dealkalized makeup water would most likely require other changes to the chemical-treatment program, especially the internal boiler water treatment.
For those plants where sodium softening remains the preferred choice, chemical control of CO2 is possible. Such control ties in with an important aspect of feedwater chemistry outlined in Table 1: maintaining the feedwater pH in a mildly alkaline range. In fact, operating results over the years indicate that feedwater pH should typically be maintained closer to the upper limit of the 8.3–10.0 range shown in the table to minimize feedwater piping iron corrosion. This is particularly true in the power industry, where flow-accelerated corrosion (FAC) has been a serious problem [2].
The common feedwater pH-conditioning chemical for power plants is ammonia, which raises the pH via the following reaction:
NH3 + H2O ↔ NH4+ + OH– (5)
This is an equilibrium reaction, and, thus, the alkalinity increase is limited, which usually minimizes excessive steel corrosion in the event of a chemical feed upset. (Copper alloy corrosion is a completely different story.) But ammonia is very volatile, and the compound significantly partitions with steam in low-pressure boilers. For industrial units, neutralizing amines are a common alternative for feedwater pH conditioning (Table 2). These are small-chain organic molecules with an ammonia group attached to, or embedded within, the compound.
Two important properties of these compounds are the distribution ratio and basicity. Some of the amines have a higher basicity than ammonia and can raise the pH to higher levels if necessary. Another important property for systems with condensate return is the distribution ratio, that is, the amount of amine that carries over with steam versus the amount that remains in the water. The ratios vary with boiler temperature and pressure, but some products tend to remain in the boiler water while others significantly partition with the steam. Careful selection of a blended product can provide comprehensive pH conditioning to the boilers and condensate return system.
A critical aspect in developing chemical-treatment programs for condensate system protection is an understanding of all system metallurgy. Typically, the piping is carbon steel, in which the most corrosive agents are dissolved oxygen and acids. For copper-alloy heat-exchanger-tube materials, combining ammonia with dissolved oxygen can be quite harmful. Stainless steels perform best in oxygenated environments, but some mineral salt anions, most notably chloride, can cause localized pitting and stress corrosion cracking (SCC), the latter mechanism being greatly influenced by temperature. Sulfide is deleterious to many metals. So, no evaluation of a chemical-treatment program is valid without knowledge of all materials within the condensate return system and the conditions to which the metals are subjected.
Before moving to the next section, two additional points should be noted. First, when representatives of the authors’ employer audit a new system, they frequently see boilers with overheating or corrosion (or both) problems. Further research often reveals previous upsets or failures of the sodium softening system. The resultant hardness in-leakage to the boilers generates the reaction shown in Equation (1), among others. As these incidents and the case study in the next section suggest, the focus at industrial plants is often concentrated on process chemistry and engineering, and the water/steam systems take a backseat in terms of attention and funding, at least until a major problem arises.
Second, much work continues in the development of film-forming products, either amine-based or other compounds with alternative active groups, for steam-system metals protection. Much of the effort so far has been concentrated in the power industry. Film-forming chemistry is not new, but improved products are now available to make this technology more attractive. However, questions remain about the efficiency of these products and whether they can provide complete protection to all metal surfaces. Space limitations prevent a discussion of this chemistry now, but we hope to provide details in a future article. In the meantime, please contact the authors for additional information.
Condensate return system
This section begins with a case study. A number of years ago, one of the authors and a colleague were asked to visit an organic chemicals plant with four 550-psig package boilers with superheaters. Much of the steam utilized for energy in the plant heat exchangers was returned as condensate to the boilers. Each of the boiler superheaters would fail every 1.5–2 years on average because of deposition and subsequent overheating within the tubes. An inspection of an extracted superheater tube bundle in a laydown area revealed deposits of approximately 1/8–1/4 in. in depth. Additional inspection revealed foam issuing from the saturated steam sample line of each boiler. Among the items evident from water/steam analyses previously performed by an outside vendor were total organic carbon (TOC) levels of up to 200 ppm in the condensate return. Contrast that with the <0.05 feedwater TOC recommendation in Table 1. No processes or equipment were in place to remove these organics upstream of the boilers. Based on that evidence alone, it was easily understandable why foam was issuing from the steam sample lines, and why the superheaters rapidly accumulated deposits and failed from overheating.
With the wide variety of intermediate and final products generated by industrial plants, the possibilities for contaminant leakage into condensate return are enormous. Besides the examples noted above, other impurities may include strongly acidic or basic compounds, mineral salts, complex organics, and many additional contaminants, including oxygen from air in-leakage, which can cause intense carbon-steel corrosion and corrosion-product transport (Figure 2).
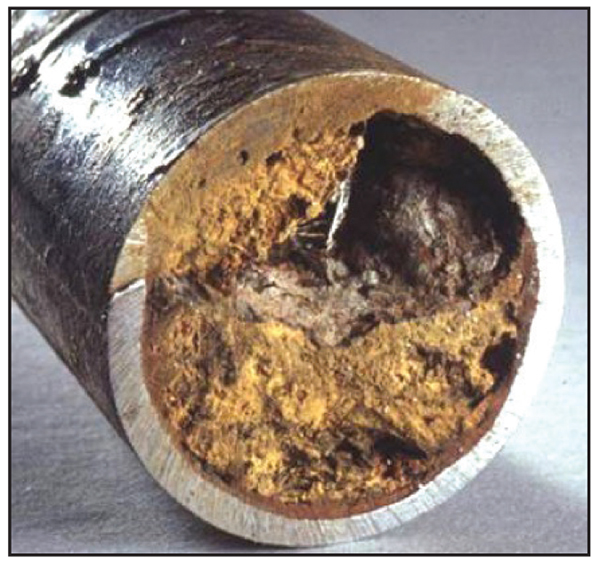
Figure 2. The pipe shown here is nearly blocked with iron oxide corrosion products
As we have noted, products that might not cause corrosion or scaling in the condensate return system can still travel to the boilers to induce major problems.
So, what are some useful methods to protect return condensate and minimize impurity ingress to boilers? One method is to establish and maintain heat exchanger integrity so impurities do not enter the condensate. A common argument is that systems are so complex or have so many components that keeping track of all the heat exchangers is a nearly impossible task. However, we believe such an effort should be part of the plant’s overall safety program. Too many examples are available where an old, corroded component failed and triggered a major accident.
One possibility for steam-generator protection is to equip the condensate return system with a dump line so an excursion in some instrument reading, say, specific conductivity, will open a valve and allow the condensate to be drained rather than returned to the steam generators. Some plants use TOC analyzers to monitor return condensate. If neutralizing amines are utilized for pH adjustment, the contributing TOC from the amine is taken into consideration, and a target TOC is selected for dumping. Dumping can involve a large loss of water and may require special makeup water system design to handle periodic high makeup requirements. An alternative idea, albeit one that requires additional funding and staffing, is to place a condensate polisher on the return line to the boilers. The choice of equipment and polishing process will depend on the impurities to be removed and mechanical conditions such as flowrate, temperature, and pressure; but a number of options are available, including the following:
- Ion-exchange resins, with some flexibility of selection for particular contaminants
- Particulate-matter removal by fabric or mechanical filters
Ion-exchange resins can be specifically designed to remove a variety of dissolved ions, ranging from primary cations and anions to other trace constituents. A difficulty with resins is that, depending on the resin type, they may be more or less limited by temperature. Some anion resins begin to break down at temperatures not much higher than 100°F, while others may be stable at substantially higher temperatures.
Direct filtration with a fabric medium is a common technique, particularly if system corrosion generates a significant amount of iron oxide or other metal particulate matter. A prime example comes from the power industry, where air-cooled condensers (ACC) have become somewhat popular as an alternative to cooling towers as a method to conserve water. ACC units require a huge amount of carbon-steel piping to effectively cool turbine exhaust steam, and even with the best chemical treatment programs, the process still introduces a large amount of iron oxide particulates to the condensate. These particles must be removed before entering the steam generator, as they can deposit on boiler tubes to reduce heat transfer and potentially establish locations for under-deposit corrosion.
Monitoring condensate
The recommended online water/steam chemistry analyses for high-pressure steam generators is described in Ref. 3. Prompt detection of chemistry upsets can save a plant huge sums by preventing steam generator corrosion and failure. The data are also important for helping plant personnel maintain day-to-day chemistry within proper ranges.
The same logic applies to monitoring condensate return chemistry. Valuable analyses, depending on process conditions, may include the following:
- pH
- Specific and cation conductivity
- TOC
- Sodium (a common and easily measurable impurity in cooling water)
- Iron or Millipore testing (or both)
Improved grab-sampling techniques for iron monitoring can (Figure 3), with proper sample treatment, measure total iron concentrations down to 1 part per billion (ppb). This method can provide nearly realtime corrosion rate data, although on a “snapshot” basis.
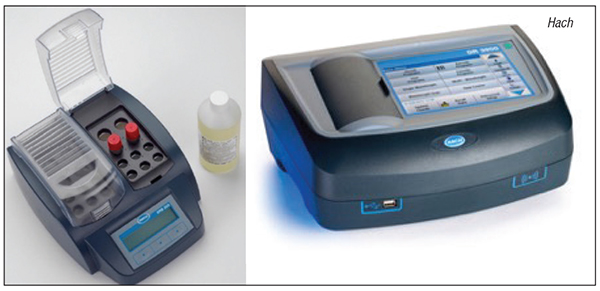
Figure 3. Shown here is an iron-digestion unit / spectrophotometer for grab samples
Millipore testing (passing a fixed volume of condensate through a 0.45-micron Millipore filter pad and comparing the coloration to standard charts) and trending of the return condensate will show whether the corrosion products are reddish (hematite) or darker gray-black (magnetite), and if condensate conditions are changing. Table 3 is a rough guide to carbon-steel corrosion in the condensate system.
The importance of iron monitoring has become very well recognized in the power industry, but it can be equally valuable at many other facilities as well.
Disclaimer
This discussion represents good engineering practice developed over many years. However, it is the responsibility of plant owners, operators, and technical personnel to set up reliable chemical feed, control and monitoring systems based on consultations with industry experts. Many additional details go into the design and subsequent operation of these technologies than can be outlined in this article. Each system is different, and we encourage you to contact experts for a consultation.
References
1. “Consensus on Operating Practices for the Control of Feedwater and Boiler Water Chemistry in Modern Industrial Boilers,” The American Society of Mechanical Engineers, New York, NY, 1994.
2. Buecker, B., Shulder, S., and A. Sieben, Fossil Power Plant Cycle Chemistry; pre-conference seminar to the 39th Annual Electric Utility Chemistry Workshop, Champaign, Illinois, June 4, 2019.
3. Buecker, Brad, Monitoring of Water and Steam Chemistry for Steam Generation, Chem. Eng., September 2019, pp. 33–42.
Authors
Brad Buecker is senior technical publicist with ChemTreat, Inc. (5460 Cox Road, Glen Allen, VA 23060; Phone: 804-935-2000; Email: bradley.buecker@chemtreat.com). He has many years of experience in or supporting the power industry, much of it in steam generation chemistry, water treatment, air quality control, and results engineering positions with City Water, Light & Power (Springfield, Illinois) and Evergy’s (Kansas City Power & Light) La Cygne, Kansas station. He also spent two years as acting water/wastewater supervisor at a chemical plant. Buecker has a B.S. in chemistry from Iowa State University with additional coursework in fluid mechanics, energy and materials balances and advanced inorganic chemistry. He is a member of the ACS, AIChE, AIST, ASME, CTI, NACE, the Electric Utility Chemistry Workshop planning committee, the International Water Conference Advisory Council, and the Power-Gen International planning committee. Buecker has authored many articles and three books on power plant and water/steam chemistry topics.
Ed Sylvester is director of Filtration, Ion Exchange & Membrane Technologies at ChemTreat (same address as above), and has over 40 years experience in the water treatment market. He has been involved in product development of membrane antiscalants, alkaline and acidic membrane cleaners and filtration and ion-exchange cleaners. In addition to his consulting and troubleshooting work, Sylvester is also involved in presentations and training. He is the presenter at Texas A&M semiannual Water & Wastewater Short Course at the Global Petroleum Research Institute every April, as well as giving presentations at the Phosphoric/Sulfuric Acid AICHE meeting in Florida; the Southwest Chemistry Workshop; and the AEP Corporate Technical Conference.
Kevin Boudreaux is director of Boiler Technologies at ChemTreat (same address as above) with 18 years experience in the water treatment market. He has been involved in product development of products for boiler chemistry, software for modeling boiler chemistry and models for exchanger/condenser performance. He has also been involved in consulting and troubleshooting of boiler systems, and has given a number of presentations for many different industries. Boudreaux also gives corporate presentations for the company’s seminars and conferences as well as training.