After a rough past year, petroleum refineries are seeking profit opportunities through the use of renewable feedstocks, such as vegetable oils and waste fats, as well as with new alkylation technologies and by increasing “crude-to-chemicals” (C2C) approaches
The past 18 months have generally been extraordinarily challenging for the world’s petroleum refineries, as pandemic-related restrictions dramatically reduced demand for refinery products and cut refinery utilization rates. Even with demand for transportation fuels returning as the world economy begins to emerge from the pandemic, long-term growth in gasoline and diesel fuel demand is not expected. Flat fuel demand growth, coupled with a broader trend toward decarbonizing the energy sector and increasing investment tied to environmental, social and governance (ESG), is driving petroleum refiners to seek profit opportunities through changes in the products they make and the methods they use to make them.
One area seeing a tremendous amount of activity is the production of renewable diesel fuel (see sidebar below). Driven by potentially lucrative subsidies for renewable fuels and other government policies — including the trading of RIN credits [renewable identification numbers; the currency of the U.S. Enviromental Protection Agency’s (EPA) Renewable Fuel Standard (RFS) program], the recently renewed biodiesel tax credit, along with state-level programs, such as Low-Carbon Fuel Standards in California, Oregon and British Columbia — many refiners are looking to expand production of renewable diesel by repurposing underutilized refining assets. The current incentives, coupled with new technologies for renewable fuels, are justifying revamps and new builds for renewable diesel projects.
SIDEBAR: Renewable diesel production on the rise: Ongoing Projects
Currently, production of renewable diesel fuel is relatively small compared to petroleum-based diesel, but there are a number of projects in the U.S. and abroad — some under construction and others proposed — that will dramatically increase the volume of renewable diesel available. According to forecasts from the International Energy Agency (Paris, France; www.iea.org), production of renewable diesel in the U.S. will increase from 9 billion L in 2020 to an average of 17 billion L annually from 2023-2025.
Renewable diesel differs from biodiesel in that renewable diesel consists of hydrocarbons produced by hydrotreating non-petroleum vegetable oils, such as refined soybean oil, distiller’s corn oil or waste animal fats from poultry and beef production, while biodiesel is a mono-alkyl ester (fatty acid methyl ester) formed by transesterification of bio-derived oils. Biodiesel is typically used to blend with conventional petroleum-derived diesel, while renewable diesel is a drop-in replacement for petroleum-derived diesel. Typical vegetable oils and animal fats used in renewable diesel production are triglycerides with C16 and C18 chains that undergo a hydrotreating process.
The following is a selection of ongoing projects in the area of renewable diesel:
•Honeywell recently announced that Brazil-based ECB Group (Sao Paulo; www.ecbgroup.com.br) will use the UOP Ecofining process to convert vegetable oils and inedible animal fats into renewable diesel and jet fuel at the Omega Green production facility in Villeta, near Asuncion, Paraguay. Honeywell UOP has designed the Omega Green project to minimize fossil CO2 emissions at the site by using the renewable LPG and naphtha produced in the UOP Ecofining unit to self-sustain the process in energy and hydrogen. In partnership with the engineering firm Wood PLC (Aberdeen, U.K.; www.woodplc.com), Honeywell UOP will integrate Wood’s hydrogen plant technology with the Ecofining unit design to produce hydrogen from renewable feedstocks to further reduce carbon intensity. When it enters operation, Omega Green will produce up to 20,000 barrels per day (bbl/d) of renewable diesel and jet fuel
• Marathon Petroleum Corp. (Findlay, Ohio; www.marathonpetroleum.com) is now producing 12,000 bbl/d of renewable diesel at its plant in Dickinson, N.D. The plant began production in the first quarter of this year and expects to hit full rates soon. Marathon plans to transport the renewable diesel by rail to the California market to benefit from that state’s Low-Carbon Fuel Standard. The company has also announced plans earlier this year to convert its Martinez, Calif. refinery into a renewable-fuels production facility. The Martinez facility is expected to start producing renewable diesel in 2022 and build to full capacity in 2023
• Diamond Green Diesel (Norco, La.; www.diamondgreendiesel.com), the largest renewable diesel facility in the U.S., is the result of a joint venture between Valero Corp. and Darling Ingredients Inc. Diamond Green Diesel is expanding capacity for renewable diesel at its Norco, La. site using Honeywell UOP’s Ecofining process. Diamond Green Diesel plans to build another renewable diesel plant in Port Arthur, Texas
• Revamp work is underway at CVR Energy Inc.’s (Sugar Land, Tex.; www.cvrenergy.com) Wynnewood Refinery in Oklahoma to convert an existing hydrocracker to produce renewable diesel from soybean oil. The project has selected Haldor Topsoe’s (Lyngby, Denmark; www.topsoe.com) HydroFlex technology for the production. HydroFlex is commercially proven technology that can be deployed in both grassroots units and revamps for co-processing or stand-alone applications.
• Holly Frontier Corp. (Dallas, Tex.; www.hollyfrontier.com) is building a renewable diesel unit at its Artesia, New Mexico. facility that will use Haldor Topsoe’s HydroFlex technology. The project is expected to begin producing renewable diesel in the first quarter of 2022. Along with its N.M. project, HollyFrontier intends to repurpose its Cheyenne, Wyoming, refinery to produce 90 million gal/yr of renewable diesel. The company expects the project to be completed in early 2022
• Last year, Global Clean Energy Holdings Inc. (Long Beach, Calif.; www.gceholdings.com) acquired the Alon Bakersfield Refinery and is now retrofitting the facility to produce renewable diesel, liquid propane from a variety of feedstocks including waste fats, used cooking oil, soybean oil and distillers corn oil—as well as GCEH’s proprietary camelina oil. The project will use HydroFlex technology.
• In 2020, Ryze Renewables LLC (Sparks, Nev.; www.ryzerenewables.com) developed, then sold its interest in, a 3,500-bbl/d renewable diesel facility near Reno, Nev. The company is now working on building a larger-scale renewable diesel facility near Las Vegas, Nevada.
• World Energy LLC (Boston, Mass.; www.worldenergy.net) is expanding its Paramount, Calif. refinery to produce renewable diesel, as well as sustainable aviation fuel and propane from inedible agricultural waste. The project is reported to be completed in 2023
• Renewable Energy Group Inc. (Ames, Iowa; www.regi.com) is currently expanding capacity to produce lower-carbon renewable diesel at its Geismar, La. refinery from 90 million gal/yr to 340 million gal/yr. Construction is expected to be completed in 2023.
• Last year, Phillips 66 (Houston; www.phillips66.com) announced plans to convert its San Francisco Refinery in Rodeo, Calif., from a crude-oil-processing facility to one that produces renewable fuels. The plant would convert used cooking oil, fats, greases and soybean oils into 680 million gal/yr of renewable diesel, renewable gasoline and sustainable jet fuel. Production of renewable fuels is expected to begin in 2024
• Next Renewable Fuels Inc. (Houston; www.nextrenewables.com) is building a renewable diesel production facility in Port Westward, Oregon. The site will eventually produce 50,000 bbl/d and is expected to open in 2024
• Grön Fuels, LLC (www.fidelisinfra.com) has proposed building a 60,000 bbl/d renewable diesel production facility in Baton, Rouge, La. The project is expected to break ground in 2021 and will use Haldor Topsoe’s Hydroflex technology ❑
Renewable diesel
An example of a tool that can help refiners take advantage of opportunities in this area is a new, simplified version of Honeywell UOP LLC’s (Des Plaines, Ill.; www.uop.com) “Ecofining” process for the production of renewable diesel fuel. UOP launched the new version earlier this year as a single-stage technology designed to be a fast-to-market, low-capital-cost technology option that can be ideal for repurposing an underutilized hydrotreating or hydrocracking unit.
Ben Owens, vice president and general manager, Honeywell Sustainable Technology Solutions, says that over the past two years, two factors have combined to motivate the company toward developing the single-stage version of Ecofining. “There’s been a lot of movement on biodiesel as companies seek to meet sustainability goals and pay more attention to ESG reporting,” Owens points out, and “there are a lot of idled assets that refiners are trying to figure out how to use.” Owens specifically cites a tripling of the number of biofuels-related projects in development, and a sharp increase in refining revamps aimed at making renewable fuels.
Those factors drove the development of Single-Stage Ecofining, which Owens says is 50–70% less expensive than the original, two-stage Ecofining, because of a simplified design, and can reach production in 12 months, versus at least three years for a greenfield project (Figure 1).
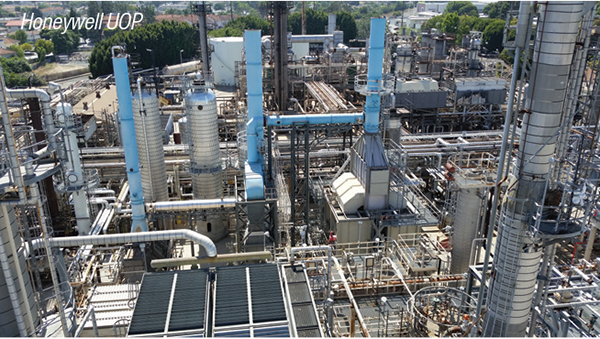
FIGURE 1. The single-stage version of the Ecofining process for renewable diesel is designed as a fast-to-market, low-capital-cost option
The single-stage Ecofining process produces Honeywell Green Diesel fuel from vegetable oils, used cooking oils, and inedible corn oil. Honeywell Green Diesel is chemically identical to petroleum-based diesel and can be used as a drop-in replacement in vehicles with no modifications. Green Diesel also features up to an 80% lifecycle reduction in greenhouse gas emissions compared with diesel made from petroleum, Honeywell says.
The faster speed to market of the single-stage unit requires a tradeoff in feedstock flexibility, however. With its greater feedstock flexibility, the two-stage Ecofining can make renewable jet fuel, while the single-stage Ecofining “is probably going to be focused more on making diesel from under-utilized refinery assets, depending on the refinery’s unique situation relative to feedstock logistics,” Owens says.
The new, single-stage process uses a combination of catalysts in a single unit to clean and remove oxygenates and other contaminants from the feedstock, and then isomerize the feed to improve its cold-flow properties. “We developed a new process design and catalysts that combine the hydrotreating and isomerization functions into a single reactor system operating in a sour environment with sulfur, nitrogen, water and carbon oxides,” Owens explains. “The new highly selective catalysts remove sulfur and nitrogen from the feeds and isomerize the oils to raise cetane values,” he says, “minimizing cracking and maximizing isomerization to deliver high yields of renewable diesel.”
A single-stage Ecofining system can subsequently expand into a full two-stage Ecofining process, if desired by the refinery, UOP says. Currently, single-stage Eco-fining setups are in the design phase at several petroleum refineries. UOP invented the original Ecofining jointly with Eni Sp.A. 10 years ago.
Co-processing
Another strategy related to renewable diesel is co-processing biologically derived feedstock alongside conventional petroleum-based feedstock. An example of this comes from MOL Group (Budapest, Hungary; www.molgroup.info), a petroleum refiner with facilities in Hungary, Slovakia and Croatia. MOL is moving into biofuels production as it looks to the future of vehicle fuels markets. In March, MOL announced an initiative to co-process vegetable oils along with crude oil to make diesel fuel with higher renewable content.
“Bio-feedstock will be co-processed together with fossil materials, increasing the renewable share of fuels and reducing up to 200,000 ton/yr CO2 emissions without negatively affecting fuel quality,” says MOL Group Executive Vice President of Downstream Gabriel Szabó. “This is in line with our ‘Shape Tomorrow’ strategy, where we plan to produce 100,000 ton/yr of advanced biofuels by 2030.” The co-processing unit has been operating successfully since last year (Figure 2).
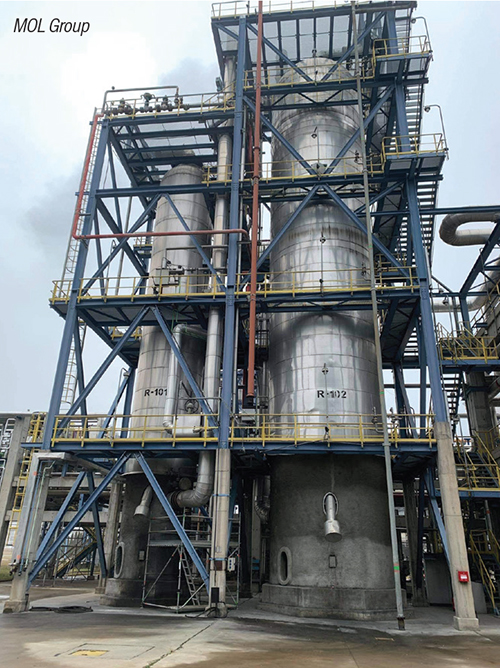
FIGURE 2. The photo shows the reactors for co-processing renewable feedstock for diesel production
MOL R&D over the past several years has overcome several challenges associated with co-processing bio-based materials. “The main problems are that the feed is non-homogeneous, so you need catalysts that won’t lose activity, and you need an efficient logistics system to get the bio-feedstock to the refining site,” Szabó says. “Also, the renewable components have added potential for corrosion.”
The site is now using vegetable oils as the bio-based component, but will expand in the future to accommodate used cooking oils, waste animal fats and other potential waste and advanced feedstock. Szabó says the company has also built logistics infrastructure to allow bio-based waste fats and oils to arrive by rail or by truck, as well as storage facilities.
The co-processing results in gasoil that is partly renewable, without any quality differences compared to diesel produced entirely from crude oil. “The main advantage of this innovative method is that the resultant diesel with bio-content can still be blended further with a maximum 7% biofuel, in line with diesel standards, allowing the bio-share of the gasoil to be higher,” MOL Group says.
The share of transportation fuels that must be renewable is increasing in the European Union, and it has been met so far by blending gasoline with bio-based ethanol and blending diesel with biodiesel. The co-processing arrangement allows for a higher share of bio-based content because the co-processed diesel already has bio content, but since it is identical to petroleum-derived diesel, it can still be blended further with biodiesel.
MOL plans to invest $1 billion on new projects focused on sustainability and decarbonization over the next five years.
Another example where co-processing renewable feedstock is at play appears in the sustainable aviation fuel sector. Earlier this year, Spanish fuel manufacturer Repsol S.A. (Madrid; www.repsol.com) announced the industrial-scale manufacture of aviation fuel with biologically derived content at its complex in Tarragona, Spain. The company developed a proprietary co-processing route where its “biojet” fuel is produced in parallel with kerosene production. The biological component of the fuel is made via a hydrogenated esters and fatty acids (HEFA) process, starting with vegetable-derived materials.
The first batch of biojet fuel totaled 10,000 tons and had renewable content of 5%, which complies with the quality requirements established in international specifications.
Repsol plans to extend the production of biojet fuel to its other sites, and to introduce a continuous process (the two initial runs were batch processes).
Refinery-petrochem integration
Over the past year, “Integrated refinery and petrochemical sites significantly outperformed their fuels-only peers,” according to industry analyst Wood Mackenzie (Edinburgh, U.K.; www.woodmac.com). “This switch in demand away from gasoline to petrochemicals promotes the adoption of refinery and petrochemical integration, particularly for new facilities in Asia and the Middle East.
An example of new technology supporting the trend toward production of chemical building blocks from crude oil comes from a research partnership between the King Abdullah University of Science and Technology (KAUST; Thuwal, Saudi Arabia; www.kaust.edu.sa) and Saudi Aramco (Dhahran, Saudi Arabia; www.aramco.com). A research team led by KAUST professor Jorge Gascon has developed a new multi-zone fluidized-bed reactor and a new catalyst material that is capable of performing several refinery upgrading steps, resulting in the stable conversion of crude oil to light olefins in a single reactor with minimal byproduct production.
The one-step C2C transformation could prove to be a critical process approach as demand for gasoline and diesel decreases and demand for petrochemicals rises. The technology could also help conserve energy as less energy-intensive steps are required.
Currently, the researchers point out, most C2C processes combine technologically mature units (high-severity fluid catalytic cracking (FCC) units and naphtha crackers) to maximize the production of ethylene, propylene and aromatics. “Although economically attractive, this approach still requires the use of oil pre-treatment processes [hydrotreating], energy-intensive distillation units for separating different fractions and the primary products of FCC, and the use of other energy-intensive units, such as steam crackers,” the team writes in a recent study in Nature Catalysis.
The multi-zone configuration of the reactor allows for in-situ catalyst stripping and regeneration, the KAUST team says, where catalyst particles undergo cycles of deactivation, stripping and regeneration in separate zones of the same fluidized-bed vessel (Figure 3). Meanwhile, the incorporation of silicon carbide (SiC) into the catalyst improves its physical, mechanical and heat-transport properties. As a result, this reactor-catalyst combination has shown stable conversion of untreated Arabian Light crude oil into light olefins with per-pass yields of over 30 wt.% with a minimum production of dry gas, the researchers say.
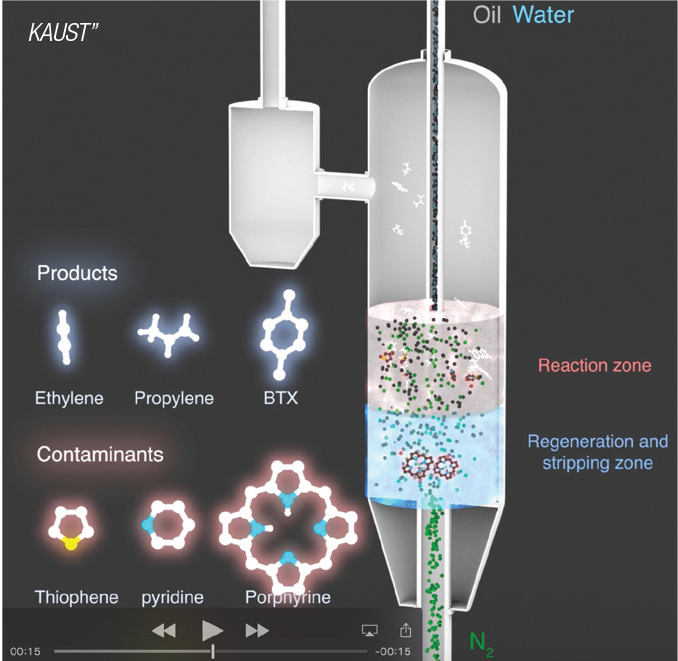
FIGURE 3. This new multi-zone fluidized-bed reactor can support production of petrochemical feedstocks from crude oil
The untreated crude oil is fed into the reactor at the middle of the vessel, which has the cracking zone at the top section and the stripping zone and catalyst regeneration at the bottom, Gascon explains. “Different reaction zones in the reactor vessel can be fine-tuned to achieve different environments and residence times with continuous operation of the catalyst,” he says.
“Carrying out cracking and stripping in the same reactor obviates the need for several units in the process,” Gascon says, and “you can utilize the energy from coke burning to run the cracking reaction, while maintaining the activity of the catalyst.”
The KAUST team is currently building a mini-pilot plant (capable of processing 10 L of crude oil per day) in order to conduct material and energy balances and economic analyses for the process, as well as evaluating its performance on other types of crude.
New alkylation technologies
Alkylate, formed by the reaction of light olefins (such as butylene) with isobutane, is the most sought-after blendstock for gasoline because of its high research octane number (RON) values and low (or no) sulfur content. Two new technologies launched this year can improve alkylation operations at refineries.
In April 2021, Chevron Corp. (San Ramon, Calif.; www.chevron.com) and Honeywell announced the commissioning and startup of the world’s first commercial-scale IsoAlky process unit at Chevron’s Salt Lake City refinery. IsoAlky technology utilizes ionic liquids to produce alkylate, and is designed to offer a cost-effective and safer alternative to conventional liquid-acid systems. Using a non-aqueous liquid salt, or ionic liquid as a catalyst (rather than hydrofluoric or sulfuric acid), the new process requires only standard personal protective equipment and produces a valuable high-octane blending component. IsoAlky technology was pioneered by Chevron USA Inc. and licensed to Honeywell UOP to offer the technology to the wider entire industry.
Bryan Glover, president and CEO of Honeywell UOP says “Ionic liquids have strong acid properties that enable them to produce alkylate without the volatility of conventional acids, allowing for simpler handling procedures.” He adds that the newly commercialized technology canpromote cleaner-burning fuels at a lower cost while simplifying complex handling requirements.”
IsoAlky can be used in new refineries, as well as existing facilities undergoing capital expansion or retrofits. The technology has wider and improved feed flexibility relative to conventional alkylation technologies, Glover says, and the ionic-liquid catalyst material is regenerated onsite, eliminating the need to transport it offsite for regeneration and polymer byproduct handling.
In another alkylation-related development, Lummus Technology (Houston; www.lummustechnology.com) recently announced the startup of its first C5 CDAlky unit at Valero Energy Corp.’s (San Antonio, Tex.; www.valero.com) St. Charles Refinery in Norco, La. C5 CDAlky is a new version of the company’s CDAlky technology, a low-temperature sulfuric acid alkylation process.
The St. Charles installation is the first C5 CDAlky alkylation unit in the world, and Lummus’ first CDAlky unit in the U.S. Lummus developed this new version of the alkylation platform to process low-value C5 feedstock at its pilot plant facility in Pasadena, Texas. A depentanizer column is used to recover C5 olefins from light cat naphtha and to remove impurities from feedstocks. The CDAlky unit converts C5 olefins into a superior alkylate product with minimum acid consumption. The capacity of the new C5 CDAlky alkylation complex is 17,000 bbl/d of alkylate product.
The C5 CDAlky version employs the same core technology as the original technology, but couples the CDAlky with a CDHydro depentanizer, a specific pretreatment system for fractionating and hydrogenating C5 impurities, such as cyclopentene and pentadienes.
“In the past, refiners would need a depentanizer plus a hydrogenation step to deal with the C5 stream, but through process intensification the CDHydro uses the principles of catalytic distillation to separate the C5 feedstock and to remove impurities in the same unit,” explains Todd Vogt, head of refining at Lummus.
“With this system, refiners can take the C5 stream and turn it into high-value gasoline blendstock,” adds Jackeline Medina, Lummus technology manager for alkylation technologies (Lummus was previously owned by McDermott International, but was recently spun off as a standalone company).
Online-only content:
The following includes additional online-only content about fuel manufacturing.
New process configuration for premium gasoline. In April, Honeywell announced a new refinery configuration developed by Honeywell UOP to produce a cleaner-burning gasoline product that meets increasingly stringent fuel regulations, including the Euro V standard, which limits sulfur content and restricts carbon emissions from gasoline and diesel vehicles.
The UOP Premium Gasoline Complex (PGC) employs a combination of technologies to convert 100% of naphtha into 95 RON Euro-V gasoline — without the addition of traditional octane boosters such as alkylate, MTBE, ETBE, and ethanol — to meet these regulations.
The PGC configuration operates through four main processes, beginning with full range naphtha that is fed to a naphtha hydrotreating unit, and a naphtha splitter separates the product into an overhead stream of C5/C6 components. From there, the product moves to a Penex unit, then to a sidecut stream primarily of C7s to an IsomEx isomerization unit, and finally to a bottom stream rich in C8+ components to a CCR Platforming™ unit. By integrating the three processes, the configuration can convert 100% of a naphtha feed into 95 RON (research octane number) gasoline that meets all Euro-V specifications such as aromatics, olefins and Reed Vapor Pressure, Honeywell says.
Bio-based alcohol pilot plant. OMV (Vienna, Austria; www.omv.com) plans to build a pilot plant at its Schwechat Refinery which will produce second-generation biofuels starting in 2023 using a patented process developed in-house. The plant involves advanced biofuels that are not in competition with food materials.
The plant will use a catalyst, or reaction accelerator, developed inhouse by OMV, to produce propanol (an alcohol) from glycerin. Glycerin is a byproduct or waste product from the production of biodiesel, as well as the manufacture of detergents and soaps, but it is also considered an advanced feedstock under the European Union’s RED II (Renewable Energy Directive). The propanol produced in this way will then be used as a bio-additive for gasoline. Its other applications include as a sustainable feedstock for the chemicals market as a replacement for fossil-based propanol.
OMV is set to invest around 30 million euros. Of this, 6.9 million euros will come from the Austrian Research Promotion Agency (FFG).
Sustainable aviation fuel. To enable decarbonization efforts in the aviation industry, LanzaJet, Inc., a spinoff of LanzaTech (Chicago, Ill.; www.lanzatech.com), announced today that it has awarded a fixed-price engineering, procurement and construction (“EPC”) contract to Zeton for the fabrication and construction of the first Alcohol-to-Jet (AtJ) facility of its kind in Soperton, Georgia. LanzaJet is deploying a scalable modular construction approach whereby Zeton will construct the majority of the modules along with a smaller number that will be built by Chemical Design, Inc. Fabrication of the modules is already underway, and construction at the site along with existing utility integration will begin in summer 2021, with the plant starting up in 2022 and beginning to produce 10 million gal/yr of sustainable fuels. LanzaJet’s technology is uniquely able to produce up to 90% of its fuels as SAF, with the remaining 10% as renewable diesel. The SAF will be blended with conventional fossil jet fuel and be supplied to airports through existing supply routes. The technology can flex to produce more diesel and less SAF, as desired. LanzaJet’s SAF is approved to be blended up to 50% with fossil jet fuel, the maximum allowed by ASTM, and when blended, is a drop-in fuel that requires no modifications to engines, aircraft, and infrastructure. Additionally, LanzaJet’s SAF can deliver more than a 70% reduction in greenhouse gas emissions on a lifecycle basis, compared to conventional fossil jet fuel.
LanzaJet was launched in June 2020 following nearly a decade of technology development and commercial scale-up through a partnership by LanzaJet’s founder, LanzaTech, with the U.S Department of Energy’s Pacific Northwest National Laboratory (PNNL). The LanzaJet process can use any source of sustainable ethanol for jet fuel production, including, but not limited to, ethanol made from recycled pollution, the core application of LanzaTech’s carbon recycling platform.
Another renewable aviation fuel project is Net-Zero 1, which uses proprietary technology from Gevo (Englewood, Colo.; www.gevo.com) to produce sustainable aviation fuel and other products. Announced in early 2021, Net-Zero 1, the first in a series of “Net-Zero” projects, is expected to be built in Lake Preston, South Dakota. Gevo expects that each Net-Zero Project will have the capability to produce approximately 45 million gal/yr of liquid hydrocarbons (jet fuel and renewable gasoline) and are also expected to produce at least 350,000,000 lbs/yr of high protein animal feed.
Scott Jenkins