As the global energy transition accelerates, the need for scalable, resilient and ethically sourced battery-storage solutions has become critical. Lithium-ion batteries (LIBs), though central to electric vehicles (EVs) and grid-scale storage (Figure 1), face long-term limitations due to their reliance on critical raw materials and susceptibility to interfacial degradation. Emerging research has focused on developing cobalt-free chemistries and advanced interface treatments to deliver robust, cost-effective and sustainable energy storage systems suitable for grid deployment.
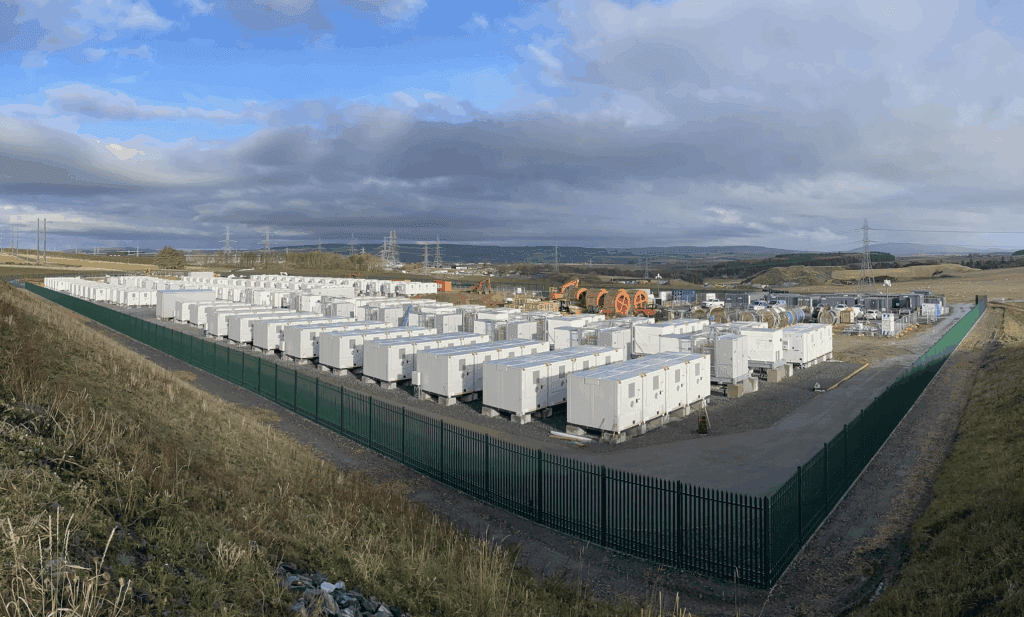
FIGURE 1. Grid-scale energy storage systems depend on critical raw minerals and complex interfacial interactions that can limit their longevity, making resilient battery materials a key consideration in design (Shutterstock)
This article outlines recent innovations in cathode design and surface engineering that address these challenges and lead to more resilient battery materials. Key developments include the use of earth-abundant transition metals in cathode materials, precise atomic-scale surface treatments to stabilize electrode interfaces and manufacturing-compatible techniques to scale these advances.
Rethinking cathode chemistry with cobalt-free alternatives
Many commercial cathode materials, such as LiCoO2 and nickel-rich layered oxides (NMC), rely on cobalt, a metal with limited availability, high cost and ethical sourcing concerns. Substituting cobalt with more abundant elements like manganese, iron, nickel and titanium offers a promising path forward, with many projects focusing on new reactions and formulations. Transition metal-doped spinels and layered oxides, including LiNi0.5Mn1.5O4 and LiMn2O4, exhibit favorable redox behavior and structural stability when doped or substituted appropriately.
Nickel doping, in particular, has demonstrated the ability to maintain redox balance and reduce oxygen release at high states of charge. These improvements are achieved without compromising energy density or rate capability. By adjusting synthesis parameters, such as annealing time [1], precursor ratios and doping concentration, cathode performance can be tailored for both EV and stationary applications. X-ray diffraction (XRD) analysis of doped metal oxide (Ni doped TiO2) has been used to observe and validate the clear phase segregation of NiO based on post-synthesis annealing conditions [1].
While LiFePO₄ (LFP) has already become a staple in EV and stationary storage markets due to its safety and stability, its lower energy density compared to NMC chemistries has prompted further interest in high-voltage spinels like LiNi0.5Mn1.5O4 [2]. These cobalt-free cathodes are particularly attractive for grid storage, where long cycle life and thermal tolerance are prioritized over gravimetric capacity. Advances in hydrothermal synthesis, microwave-assisted calcination and dopant engineering are making these materials more accessible for commercial production.
Interface engineering: Extending lifetime with atomic precision
Interface degradation at the solid-electrolyte interphase (SEI) and cathode-electrolyte interphase (CEI) is a persistent issue in LIBs, especially under high-voltage or high-temperature conditions. Advanced coating techniques, including atomic layer deposition (ALD) and vapor-phase fluorination, provide atomic-scale control over interfacial chemistry.
In a 2021 study by Darapaneni and others [3], systematic X-ray photoelectron spectroscopy (XPS) analysis demonstrated that ALD coatings of Al2O3 and AlF3 applied to transition-metal oxide cathodes can alter the surface redox state, with trimethylamine (TMA) acting as a reducing agent and hydrogen fluoride-pyridine (HFPy) as an oxidizing agent. These treatments fine-tune the interface without damaging bulk structure.
ALD enables the deposition of ultrathin, conformal layers of metal oxides (for example, Al2O3 and TiO2) and fluorides (such as LiF) that passivate active material surfaces. These coatings mitigate transition-metal dissolution, suppress side reactions and improve electrolyte compatibility. A useful schematic showing the conformal ALD coating on cathode particles is shown in Figure 2.
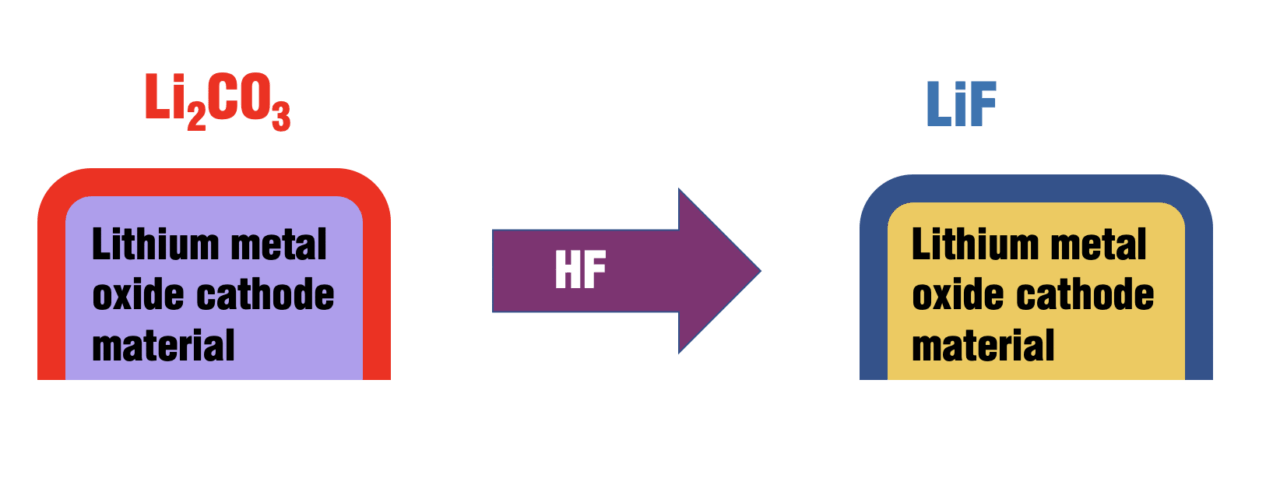
FIGURE 2. This schematic shows the conversion of surface carbonate on cathode active materials into lithium fluoride via single-step hydrogen fluoride pyridine (HFpy) precursor exposure. Figure adapted and re-created from Ref. 4
In addition to ALD, vapor-phase fluorination using reagents like HFPy removes surface carbonate contaminants and forms LiF-rich interphases. In another study by Darapaneni and others [4], vapor-phase fluorination effectively enhanced gas evolution behavior and cycling stability in Ni-rich systems. These treatments improve gas evolution behavior and cycling stability in high-voltage systems.
Alternative methods, such as sol-gel coatings or wet-chemical treatments, offer low-cost routes for interface protection, but often lack the conformality and atomic-level control of ALD. Comparatively, ALD’s layer-by-layer growth enables precise thickness tuning and uniformity on both flat and porous morphologies. These benefits are especially useful for powder-based cathodes used in industry.
Environmental and duty-cycle adaptability
Unlike EVs, grid-scale storage systems must operate across diverse environmental conditions, including extreme temperatures and irregular duty cycles (Figure 3). Material design must therefore account for thermal stability and ionic conductivity at low temperatures.
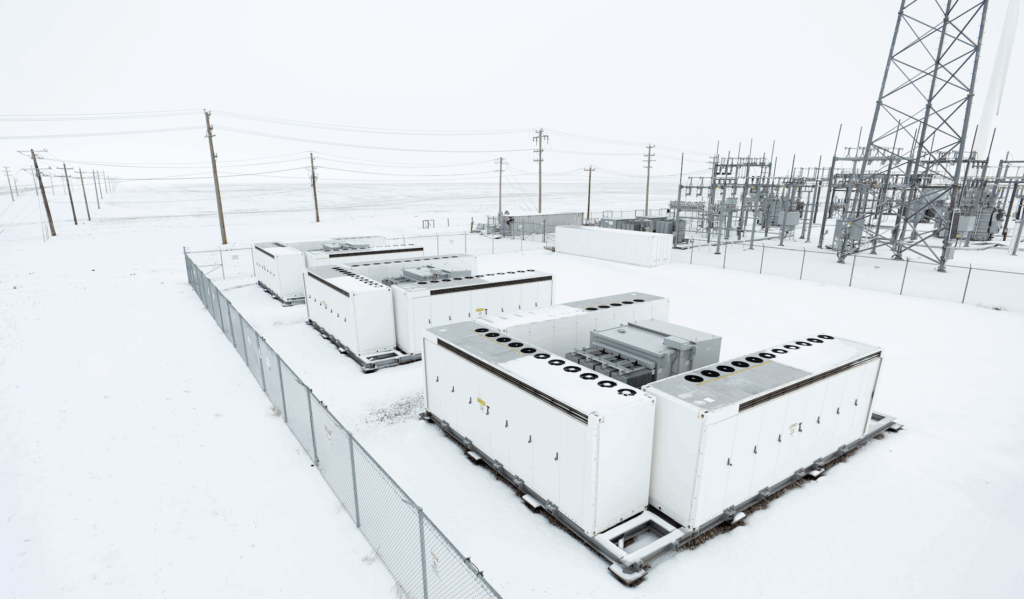
FIGURE 3. Materials used in grid-scale energy-storage systems are exposed to extreme outdoor conditions and must be designed for high performance at a wide range of temperatures (Shutterstock)
By engineering oxygen-vacancy concentrations and lattice defects in spinel or layered-oxide structures, researchers have achieved improved conductivity and redox kinetics across broad temperature ranges. These modifications are complemented using flexible electrolytes and thermally stable separators, which collectively enhance performance under grid-relevant conditions.
ALD coatings can reduce HF attack, preserving structure even in fluctuating temperature environments, as shown in test data from coated versus uncoated cathodes [5]. For residential solar and storage systems deployed in hot deserts or cold northern climates, such robustness ensures reliability without added cost for HVAC management. Recent research shows that batteries with Al2O3 coatings can retain over 85% capacity after 1,000 cycles at –10 to 45°C cycling conditions.
Scalable manufacturing and localized production
The transition from laboratory research to commercial deployment hinges on manufacturing compatibility. ALD coatings and vapor-phase treatments can be implemented using scalable tools such as roll-to-roll reactors and fluidized-bed systems. Process conditions, such as precursor pulse duration, substrate temperature and gas flowrates, can be optimized for high-throughput operation.
These methods are being integrated into pilot production lines under various industry initiatives. For powder-based coatings, spatial ALD and atmospheric-pressure ALD are under investigation to reduce process times and enable continuous coating of cathode powders. Advances in precursor development, such as safer fluorinated ligands or room-temperature processes, are also being explored to minimize handling risks and reduce energy input.
Global research adoption and industrial relevance
Research on interface engineering has seen widespread uptake across international institutions and national laboratories. ALD-based coatings and fluorination techniques have been incorporated into cathode optimization studies in potassium-ion and sodium-ion batteries as well. This cross-platform adaptability underscores the broader applicability of the strategies described here.
Key institutions applying these methods include Curtin University (Australia), Academia Sinica (Taiwan), and Brookhaven and Los Alamos National Laboratories (U.S.). These groups have extended redox-modulating ALD processes to next-generation electrode systems, confirming the reproducibility and value of interface engineering in real-world applications.
The broader battery community is also exploring these coatings in non-LIB chemistries, including zinc-ion and dual-ion batteries. The electrochemical stability and chemical inertness of LiF and Al2O3 make them universal protective agents across multiple electrolyte systems.
Catalyst parallels and dopant-controlled redox behavior
Interestingly, the concepts of dopant control and subsurface engineering in battery cathodes mirror strategies used in redox catalysts. In a separate study led by Darapaneni and others [6], subsurface Ni-doped CexZr1-xO2 catalysts were shown to enhance methane dry reforming by stabilizing redox cycles through Ni-O interactions. Similar principles of redox-tuned functionality can be applied to doped battery electrodes for reversible lithium cycling.
This convergence of catalysis and battery science highlights the fundamental role of defect chemistry [7] and dopant positioning in determining performance [8]. Taken together, the work in Refs. 7 and 8 could present a comparative schematic or electrochemical profile that illustrates similar redox cycles in battery and catalytic systems.
Defect engineering in catalysis often leverages oxygen mobility and metal-oxide support interactions, which translate directly to cathode-electrolyte compatibility in batteries. These parallels offer promising frameworks for cross-disciplinary innovation.
Future directions and emerging trends
Looking forward, emerging directions in grid storage include the development of solid-state electrolytes, lithium-metal anodes, and hybrid chemistries that combine the energy density of LIBs with the safety of aqueous systems. Interface engineering remains central to these efforts.
New ALD processes using plasma enhancement or molecular layer deposition (MLD) are being tested to grow organic-inorganic hybrid films that can interface with sulfide or polymer electrolytes. Meanwhile, AI-driven material design tools are accelerating the discovery of dopant-composition-performance maps, reducing trial-and-error in cathode optimization.
High-throughput experimentation combined with machine learning (ML) is expected to speed up interface formulation, reduce cost and identify new redox-active dopants. These tools will be crucial for meeting U.S. Dept. of Energy targets for cost ($50/kWh), energy density (>400 Wh/kg) and cycle life (10,000+ cycles).
Summary and outlook
The future of battery storage lies in materials systems that are not only high-performing, but also sustainable, cost-effective and manufacturable at scale. Innovations in cobalt-free cathodes and atomic-scale interface treatments address many of the current barriers to grid-scale deployment.
By leveraging transition metal chemistry and precision surface engineering, researchers have enabled batteries that can operate across wide temperature ranges, deliver long cycle life, and reduce reliance on fragile global supply chains. Ongoing collaborations between academia, government labs, and industry are accelerating the commercialization of these solutions, supporting both national energy goals and global decarbonization efforts. ♦
Edited by Mary Page Bailey
References
- Darapaneni, P. and others, Effect of Moisture on Dopant Segregation in Solid Hosts, The Journal of Physical Chemistry C, Vol. 123, Iss. 19, May 2019.
- Nayak, P.K., others, Review on challenges and recent advances in the electrochemical performance of high capacity Li‐and Mn‐rich cathode materials for Li‐ion batteries, Advanced Energy Materials, Vol. 8, Iss. 8, March 2018.
- Darapaneni, P. and others, Elucidating the Redox Behavior during Atomic Layer Deposition on Lithium-Ion Battery Cathode Materials, Chemistry of Materials, Vol. 33, Iss. 20, October 2021.
- Darapaneni, P. and others, Removal of Surface Carbonate from Lithium-Ion Battery Cathode Materials via Vapor-Phase Fluorination, ACS Applied Energy Materials, Vol. 5, Iss. 8, August 2022.
- Chen, L. and others, Novel ALD Chemistry Enabled Low-Temperature Synthesis of Lithium Fluoride Coatings for Durable Lithium Anodes, ACS Applied Materials & Interfaces, Vol. 10, Iss. 32, July 2018.
- Safavinia, B. and others, Enhancing CexZr1–xO2 Activity for Methane Dry Reforming Using Subsurface Ni Dopants, ACS Catalysis, Vol. 10, Iss. 7, March 2020.
- Ofoegbuna, T. and others, Modifying Metastable Sr1–xBO3−δ (B = Nb, Ta, and Mo) Perovskites for Electrode Materials, ACS Applied Materials & Interfaces, Vol. 13, Iss. 25, June 2021.
- Ofoegbuna, T. and others, Stabilizing the B-site oxidation state in ABO3 perovskite nanoparticles, Nanoscale, Iss. 30, August 2019.
Author
Pragathi Darapaneni (linkedin.com/in/pragathi-darapaneni) is a senior materials scientist with over a decade of interdisciplinary research experience spanning lithium-ion batteries, advanced thin-film coatings and redox interface engineering. She holds a Ph.D. in chemical engineering from Louisiana State University and currently works at the forefront of battery materials development, having held research and technical leadership roles at Argonne National Laboratory, Schaeffler Group USA and Martinrea International, Inc. Darapaneni’s expertise lies in the design and modification of cathode materials using techniques such as atomic layer deposition (ALD), vapor-phase fluorination and dopant-controlled defect engineering. She has co-authored 13 peer-reviewed publications, holds 4 U.S. patents and has presented her work at top scientific conferences including AIChE, MRS, and the Electrochemical Society. Her research has informed industry practices in lithium-metal anode development, graphene-based electrode coatings, and all-solid-state battery interface design. She is also an active reviewer for journals such as Inorganic Chemistry, Langmuir, and ACS Applied Nanomaterials, and is a member of professional societies including ECS, MRS, and AIChE.