To lower their climate impact, petroleum refiners are increasingly assessing greenhouse-gas-emission intensities as they consider processing lower-carbon feedstocks. One area of particular activity is sustainable aviation fuels (SAF), where demand growth is accelerating
While the oil-and-gas industry has been on a profitable run since the economic recovery from the pandemic, 2022 has brought a host of complications for the industry, including the ongoing effects of the Russian invasion of Ukraine on fuel markets, and exacerbated supply-chain and labor-force disruptions. These issues are overlaid onto a landscape in which the pressure to transition to climate-sustainable energy and to achieve global net-zero carbon emissions by 2050 continues to grow.
The recently released 6th assessment report from the U.N. Intergovernmental Panel on Climate Change (IPCC; Geneva, Switzerland; www.ipcc.ch) emphasizes the need for aggressive and comprehensive actions to achieve net-zero emissions by mid-century. Stéphane de la Rue du Can, a researcher from Lawrence Berkeley National Laboratory and lead author of the industry chapter, noted “Significant cuts in global greenhouse gas emissions … can be achieved by 2050, but it will require … transformational changes in energy and feedstock sourcing.”
The current environmental and geopolitical situation is prompting petroleum refiners across the globe to evaluate their assets and explore how to adapt to a carbon-constrained future, and one in which the negative climate effects of greenhouse-gas (GHG) emissions from fossil fuels will increasingly be priced into refinery products (see sidebox on carbon accounting, below).
One area that has seen a marked uptick in activity and an acceleration in production is sustainable aviation fuels (SAF).
Sidebox: Open-source carbon accounting models
Limiting climate-related problems by drastically lowering GHG emissions from fossil-fuel operations and transitioning to sustainable energy in the coming decades requires a nuanced and detailed assessment of how energy assets are operated and transferred, including petroleum refineries; an effort that depends on the ability to assess the lifecycle carbon intensity (CI) of different types of oil and gas, as well as other feedstocks, in a transparent and standardized way.
Deborah Gordon, former Chevron engineer and current climate policy researcher at RMI, a global energy non-governmental organization based in Boulder, Colo. (www.rmi.org), expresses some of difficulties of the energy transformation this way: “The industry is too opaque, too close to market pressures and too short-term-oriented to durably alter its own course. Uninterrupted operations, quarterly returns, annual dividends and stiff competition tend to take precedence over emissions reduction, clean-energy transformation and corporate climate alignment,” she says. At the same time, “policymakers and civil society sometimes fail to understand the complexities and inherent dynamics of oil-and-gas supply chains and their wide-ranging climate impacts. They do not have to worry about the economic viability of the industry or about pleasing stock-market investors.”
Carbon intensity (CI; measured in kilograms of GHG emissions per barrel of oil equivalent) is becoming more widely used as a metric for assessing the lifecycle emissions of a given fuel. CI is important whether the facility is producing conventional crude oil, associated gas, unconventional oil and gas, or is making biofuels. Since it will not be possible to immediately suspend production of fuels from crude oil, reducing overall GHG emissions will require a deep and broad understanding of the ways CI can be dialed down for different types of oils and gases.
This is a point made in a recently published book, titled “No Standard Oil: Managing Abundant Petroleum in a Warming World,” by RMI’s Gordon. “In fact, one [crude oil] barrel can have ten times the climate impact of a different barrel,” Gordon says. Currently, this environmental information is not available to inform consumers’, policymakers, investors’, and citizens’ decision-making. “And as a result, oil-and-gas markets are not able to effectively price in climate externalities,” Gordon points out.
The importance of assessing individual assets’ CI is underscored by industry efforts underway to price carbon. Gordon’s previous analyses while serving as the Energy and Climate Program Director at the Carnegie Endowment for International Peace recommends constructing a “smart” tax to price each barrel according to its individual CI, rather than mistakenly assuming all oil and gas have identical carbon footprints.
“If detailed information about the highly varying climate intensities of oils and gases were part of market calculations, producers, refiners, and shippers would compete on a level playing field, and actors with high-emitting resources could be made to pay their fair share to mitigate climate change,” she says.
Most international oil companies have come out in support of the government placing a price on carbon, Gordon says, but carbon pricing is an extremely difficult political sell. “Interestingly,” Gordon continues, many companies already use “shadow pricing” to place an internal cost on GHG emissions that informs their investment and operating decisions. “This is motivating corporate changes,” she says. “Many larger oil-and-gas companies are starting to unload their high-climate-intensity production and refining assets.” However, shifting climate-intensive assets onto smaller, lesser-known companies’ books may exacerbate global warming, she warns.
A key aspect of the book is the OCI+ (Oil Climate Index plus Gas), a new model developed by Gordon and a team of other researchers that is designed as a publicly available web tool that assesses and compares the lifecycle GHG emissions from any barrel of oil (or gas) from extraction through end use. The OCI+ employs the Petroleum Refinery Life Cycle Inventory Model (PRELIM) — developed by Joule Bergerson and her colleagues at the University of Calgary — to calculate emissions from refining crude oil and crude-oil blends.
“The OCI+ is a first-of-its-kind tool that can be used by novices and experts to explore oil-and-gas climate impacts and mitigation strategies,” Gordon notes.
“The OCI+’s greatest effect in the refining space is that it can both guide the industry’s operations and policymakers’ actions in the quest to change feedstock purchasing decisions, and design, retrofit and ultimately decarbonize refining. The OCI+ can also be used to illuminate how future changes in product slates (such as biojet fuel) will alter overall emissions from end use consumption,” explains Gordon.
Among the OCI+ conclusions is that lifecycle GHG emissions are not correlated with API gravity and sulfur content. Instead, emissions vary greatly depending on overall crude composition, equipment used, fuels used for extraction and processing, hydrogen generation, maintenance regimes, leakage rates and system failures. In accounting for all these variables, the OCI+ estimates GHG emissions more accurately than using API gravity, sulfur or other simple emission factors.
RMI’s “go-live” day for the OCI+ web tool is scheduled for summer 2022. The release of the newly expanded OCI+ web tool will be accompanied by a major report, titled Know Your Oil and Gas, co-authored by the OCI+ researchers at RMI, Stanford University, the University of Calgary, and Koomey Analytics. This updated model version assesses over 100 global oil-and-gas resources — representing 50% of current global production. Anyone can use the web tool to view public data inputs and quantify and compare oil-and-gas GHG emissions. Interested parties can also download the OCI+’s underlying models, Gordon says.
The OCI+ web tool has numerous functions. Maps locate oil-and-gas resources and overlay them with flaring and methane maps. Total lifecycle emissions can be parsed and compared by region, resource type, and other sorts, Gordon explains. “Users can view supply chain emissions breakouts for CO2 equivalent and methane-only emissions,” she says, and “The analysis tab depicts scatter plots for user-defined variables, including resource age, API gravity, sulfur content and industry versus consumer emissions’ responsibility.” The OCI+ has a “new scenarios” tab that allows users to explore numerous climate solutions and estimate the reduction potential of different technologies and practices. In addition, the OCI+ includes a full methodology, demonstration videos, peer-reviewed journal articles and other resources.
To further make emissions visible using data analytics to develop climate policies and activate climate markets, RMI plans to use the OCI+ and the expanded open-source climate data it provides to chart decarbonization pathways for the oil-and-gas sector, Gordon says. “One avenue we are pursuing that pertains directly to the global refining sector is green hydrogen, as a full-scale renewable replacement for steam-methane reforming,” she points out. “We are also researching petrochemicals and their different processes and emissions that could expand as gasoline demand wanes . . . In sum, we are laser-focused on 1.5°C [global average temperature rise] climate alignment in the oil-and-gas industry during this decisive decade,” Gordon says. ❑
Sidebox 2: Investor influence
Both individual and institutional investors are becoming increasingly concerned with environmental, social and governance (ESG) criteria when making financing decisions, and are demanding more information about climate risks to which companies may be exposed.
“Investors are putting growing pressure on oil-and-gas companies to report their ‘Scope 3’ (end-use) emissions that come from burning the wide array of petroleum products refiners sell to consumers,” RMI’s Gordon says. “Publicly accounting for end-use emissions is the first step to factoring in their negative externalities — and rethinking their business model,” she argues. “Moreover, as demand wanes for certain petroleum products (such as gasoline as electric vehicles replace internal combustion engines) and various renewable feedstocks are converted into bio-based fuels, refiners will be compelled to redesign their processes. Factoring decarbonization into these renovations will offer refiners a competitive edge in the global marketplace,” Gordon says.
In March 2022, the U.S. Securities and Exchange Commission (SEC; Washington, D.C.; www.sec.gov) proposed rule changes (which are now open for comment) that would require registrants to include certain climate-related disclosures in their registration statements and periodic reports, including information about climate-related risks that are reasonably likely to have a material impact on their business, results of operations, or financial condition, and certain climate-related financial statement metrics in a note to their audited financial statements. The required information about climate-related risks also would include disclosure of a registrant’s GHG emissions, which have become a commonly used metric to assess a registrant’s exposure to such risks.
The proposed SEC rules would include a phase-in period for all registrants, with the compliance date dependent on the registrant’s filer status, and an additional phase-in period for Scope-3 emissions disclosure, according to SEC. ❑
SAF pathways
The International Civil Aviation Organization (ICAO) defines SAF as alternative aviation fuels that achieve net GHG emissions reduction on a lifecycle basis, while respecting conservation of ecosystems and biodiversity, and that contribute to local social and economic development without competing with food and water.
Because commercial aircraft are likely to continue to require high-energy-density liquid fuels for propulsion, reducing the GHG emissions associated with commercial air travel and air shipping thus depends heavily on SAF. The aviation industry is expressing its desire for low-carbon SAF through purchasing agreements and collaborations.
In order for the aviation industry as a whole to achieve net-zero carbon emissions by 2050, a massive increase in production of SAF will be required (Figure 1). The International Air Transport Association (IATA) estimates that SAF production would need to reach 449 billion L/yr by 2050 in order to mitigate the majority of global emissions by the aviation industry. Several SAF pathways are currently under development and scaleup, but all face questions of high feedstock and production costs, which are currently substantially higher than conventional jet fuel.
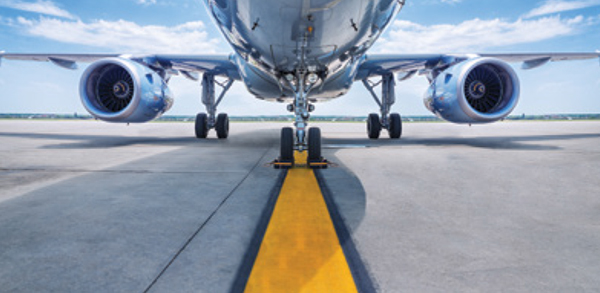
FIGURE 1. Demand for sustainable aviation fuel (SAF) is growing, driven by the commercial aviation industry
From a processing perspective, SAF production pathways can be grouped into at least four categories, each of which have multiple variations: alcohol-to-jet (ATJ) processes; hydroprocessing of waste fats and oils, and plant-based oils to jet fuel (similar to the hydroprocessed esters and fatty acids (HEFA) process for renewable diesel); gas fermentation with Fischer-Tropsch (F-T) synthesis; and converting sugars to jet fuel.
Perhaps the most straightforward pathway for producing SAF is by hydrotreating triglycerides, such as plant oils, used cooking oils and waste animal tallow (HEFA route). The most technologically mature technologies for achieving this are Topsoe A/S’ (Lyngby, Denmark; www.topsoe.com) HydroFlex technology and Honeywell UOP’s (Des Plaines, Ill.; uop.honeywell.com) Ecofining technology, co-developed by Eni S.p.A. Others are Axens’ (Reuil-Malmaison, France; www.axens.com) Vegan and Sulzer ChemTech’s (Winterthur, Switzerland; www.sulzer.com) BioFlux technologies.
Advantages of the HEFA route to SAF include a nominally better liquid yield than ATJ (80 vol.% versus 60 vol.%) and a higher level of technical maturity, explains Dave Collings, senior technical advisory consultant at 1898 & Co. (Kansas City, Mo.; 1898andco.burnsmcd.com). Also, HEFA lends itself better to petroleum refinery conversions, and has lower capital expenses per barrel of SAF product, he adds.
However, feedstock availability issues remain for potential SAF-producing sites. “A shortfall of [non-fossil] triglyceride feedstock afflicts both renewable diesel production and SAF production,” comments Collings, “and the prices for those feedstocks are currently very high.”
SAF pathways beginning from alcohols or sugars could increase available SAF feedstock and lower costs for SAF, which currently are much higher than conventional jet fuel. Collings says “although the yields for SAF from ethanol are not as high as those from triglycerides, the feedstock costs are much lower — ethanol is only one-third the price of the triglycerides.” Further, there is currently more capacity for making renewable ethanol for the ATJ pathway, he adds, and the ATJ route requires less hydrogen.
In places with readily available sugar, such as Brazil, sugar-based ethanol has an advantage over corn-derived ethanol because it’s a lower carbon-intensity pathway, explains Collings. In the longer term, processing corn starch into fuels could be competitive with the ATJ processes, he adds.
The corn-starch pathway is the route employed by Virent Inc. (Madison, Wis.; www.virent.com), a wholly owned subsidiary of Marathon Petroleum Corp. (Findlay, Ohio; www.marathonpetroleum.com). Virent is working to commercialize its BioForming process, which makes synthetic aromatic kerosene (SAK; equivalent to jet fuel). The ability to make aromatics-containing kerosene is significant because it allows the plant-based fuel to be used without blending with conventional jet fuel. “Most SAF — such as the fuel typically made from used cooking oil or vegetable oil — has to be blended with petroleum-derived products because it doesn’t contain aromatics, which are required to meet today’s jet-fuel specifications,” says a Marathon spokesperson. “Virent’s SAK … provides those aromatics.”
Virent upgraded its Madison, Wis., demonstration plant in 2019 to install the latest generation technology that was developed for scale-up and commercial production, Marathon says. Since then, the demonstration plant has run for over 17,000 hours, generating the process engineering data for a commercial plant design, testing the latest generation of catalysts that will be used in the process, and producing material for fuels testing and demonstration projects.
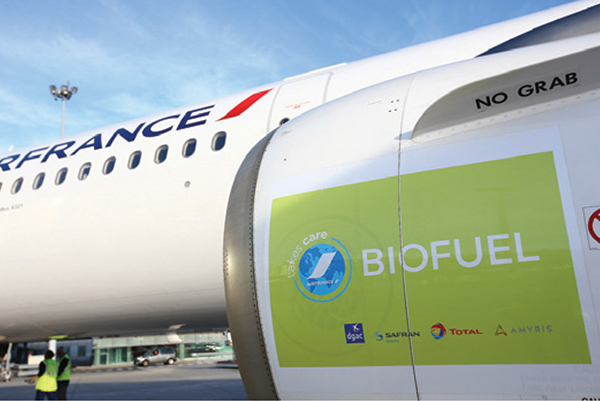
FIGURE 2. The aviation industry has been driving demand for SAF through partnerships and purchasing agreements
SAF from plant and waste oils
A number of projects for converting used cooking oils and animal fats to SAF are moving ahead using UOP and Topsoe technologies, including a project in China. In March 2022, Honeywell and Oriental Energy Company Ltd. jointly announced that a SAF production facility with an annual output capacity of 1 million tons will be built in Maoming, Guangdong Province, China.
The Oriental Energy SAF project, which will be built in two phases, is expected to be among the world’s largest SAF production facilities using used cooking oils and animal fats as feedstocks when completed. Using these feedstocks reduces lifecycle GHG emissions by approximately 80% compared with traditional fuel, Honeywell says.
UOP technology was also selected in February 2022 for a proposed bp plc (London, U.K.; www.bp.com) diesel and SAF project in Kwinana, Western Australia. bp plans to convert hydroprocessing equipment at its former refinery site to produce approximately 10,000 bbl/d of diesel and SAF from renewable feeds, integrating with its existing terminal operations.
Honeywell’s Ecofining will be used in the first commercial-scale aviation fuel project in Japan, a facility owned and operated by JGC Holdings and Cosmo Oil. Scheduled to start up in 2025, the project will convert locally collected cooking oil into renewable jet fuel that meets ASTM D7566 standards for jet fuel.
Ecofining also figures in a project looking to expand SAF feedstock options to microalgae. In November 2021, Ecofining was used to generate SAF from oils produced by microalgae. The algae-based SAF was incorporated into a fuel blend that was used to power two commercial flights in Japan.
In September 2021, Honeywell announced a joint multimillion-dollar investment, along with United Airlines, in Alder Fuels LLC (Washington, D.C.; www.alderfuels.com) — a company developing technologies for converting biomass, such as forest and crop waste, into sustainable low-carbon, drop-in replacement crude oil that can be used to produce SAF. Alder technologies, combined with Honeywell’s Ecofining process, have the potential to produce a carbon-negative fuel with specifications matching traditional jet fuel, the companies say. The goal of the technologies is to produce fuel that is a 100% drop-in replacement for petroleum jet fuel.
The Alder technology pathway originates with solid biomass converted to a biocrude through fast pyrolysis, then upgraded using the Alder Energy process, the company says. It is then sent to an Ecofining unit or other refinery hydroprocessing unit for conversion to SAF or other transportation fuel (for more information on UOP’s Ecofining, see Chem. Eng., May 2021, pp. 12–16).
Meanwhile, in January 2022, Topsoe and Indaba Renewable Fuels announced plans to build two greenfield refineries in California and Missouri to produce SAF with Topsoe’s HydroFlex technology. The facilities are expected to begin SAF production in 2024. The capacity of the plants is 6,500 bbl/d at each location. Topsoe will also provide its H2bridge hydrogen technology for both facilities that further replaces fossil fuels with renewable liquids, like LPG or naphtha, to lower the carbon intensity of the products.
HydroFlex was also used in test production runs for SAF and renewable diesel at the Marathon Petroleum facilities in Dickenson, N.D. and Martinez, Calif.
Sulzer’s BioFlux technology will be used to make SAF (along with renewable diesel) at the Sabah Maju Jaya Renewable Energy Industrial Complex in Kota Kinabalu, Malaysia. The planned plant, which was announced in February 2022, will use a BioFlux technology package to convert locally sourced plant-based oils into SAF. BioFlux was developed by Duke Technologies Inc. (Fayetteville, Ark.; www.dukebiofuels.com) in the U.S. and licensed by Sulzer Chemtech. The technology is said to be the only licensed technology with a liquid-phase full reactor design that maximizes hydrogen availability and eliminates the vapor recycle loop. This significantly reduces the capital and operational costs while improving yield and catalyst life, according to Sulzer Chemtech. The new 10,000-m2 processing complex is slated to deliver an annual production capacity of 250,000 tons.
Axens Vegan technology was selected by TotalEnergies SE (Paris, France; www.totalenergies.com) for its first biorefinery, located in La Mède, France. The plant will produce 500,000 ton/yr of high-quality paraffinic biodiesel, treating primarily used oils, as well as other renewable feedstocks. The Axens technology was originally developed by IFP Energies nouvelles in the mid-2000s.
Axens Vegan technology fundamentally consists in hydroprocessing any kind/mixture of renewable lipids into ultra-clean iso-paraffins. The resulting high quality mixture of bio-paraffins exhibits a high cetane number, tunable cold-flow properties, contains virtually no sulfur neither aromatic compounds and is easily blended into regular diesel or jet fuel, the company says.
Axens also signed a license agreement for the Vegan technology with biofuels company Aemetis Inc. (Cupertino, Calif.; www.aemetis.com) last year.
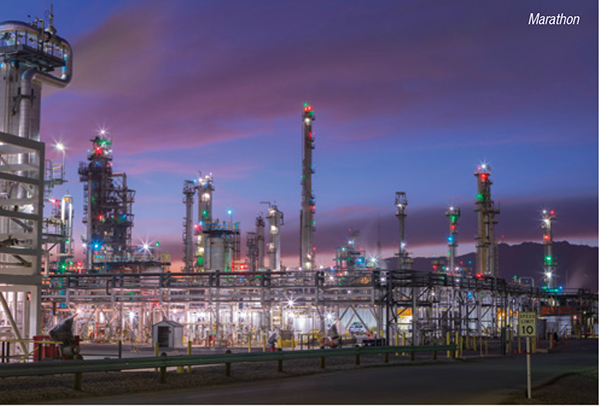
FIGURE 3. SAF and renewable diesel production has been tested at refineries such as this Marathon Petroleum facility
SAF from ATJ process
The past year has also seen significant activity around the ATJ process, whereby biomass-derived ethanol is dehydrated to ethylene, which is then oligomerized into C12–C15 olefins. The olefins are then saturated to make fuel of the correct composition to meet jet fuel standards.
In March 2022, biofuel maker Gevo Inc. (Englewood, Colo.; www.gevo.com) announced an agreement with Delta Air Lines to supply 75 million gal/yr of SAF for seven years to the air carrier. Also in March, Gevo announced that the Oneworld Alliance, a network of seven airlines, will utilize Gevo’s SAF for their operations in California, including San Diego, San Francisco, San Jose and Los Angeles International Airports.
Meanwhile, LanzaJet, a fuel-making company spun off from LanzaTech Inc. (Chicago, Ill.; www.lanzatech.com), announced a partnership with Marquis Sustainable Aviation Fuel in February 2022 to construct a 120-million gal/yr integrated sustainable fuels plant at Hennepin, Ill. Using the LanzaJet ATJ process, the plant will employ on-site carbon capture and sequestration and renewable energy to produce SAF, resulting in a lifecycle greenhouse gas reduction of more than 70% compared to conventional jet fuel.
And in January, LanzaJet announced a $50-million investment from the Microsoft Climate Innovation Fund to support construction of its Freedom Pines Fuels plant in Soperton, Ga. The ATJ SAF production plant is expected to achieve mechanical completion in 2022 and begin producing 10 million gal/yr of SAF and renewable diesel from sustainable ethanol, including from waste-based feedstocks, in 2023.
Another ATJ technology is that of Vertimass LLC (Irvine, Calif.; www.vertimass.com), which originated at Oak Ridge National Laboratory as a way to lower the cost of converting alcohols to hydrocarbons by utilizing a single reactor. In February 2022, Vertimass announced a collaboration with U.S. biofuels maker World Energy for the development of Vertimass technologies for SAF and other renewable fuels.
F-T synthesis
Still other SAF projects are looking to utilize CO2 as a carbon-negative feedstock for liquid fuels. Several concepts reduce CO2 to CO, which is then combined with hydrogen to make synthesis gas (syngas). The syngas can then be converted into longer-chain alkanes using F-T synthesis, and refined further into SAF or other products.
A new development related to this SAF pathway occurred in January 2022, when Johnson Matthey (JM; London, U.K.; www.matthey.com) launched HyCOgen, a process designed to enable the production of SAF from CO2. A new proprietary catalyst, developed by JM engineers, catalyzes the reverse water-gas shift reaction, in which CO2 and H2 are combined to generate CO and water.
Paul Ticehurst, JM senior business development manager, says the new catalyst has been integrated into a process that provides a route to SAF that consumes CO2 in a circular way.
The HyCOgen process is integrated with the FT-CANs process, co-developed by JM and bp plc, in ways that maximize efficiencies to make synthetic crude (F-T liquids), which could then be upgraded by refiners into SAF.
“JM has a deep and detailed understanding of the water-gas shift reaction, so we approached the challenge of reversing the reaction as a syngas-generating technology using that foundational knowledge and applying it to the new process,” Ticehurst says.
Because the process is endothermic and requires high temperatures, JM engineered the metallurgy of the process equipment to handle the elevated temperatures reliably over time, Ticehurst notes.
Ninety percent of the carbon in the initial CO2 leaves the process in FT liquids. “I think of HyCOgen as borrowing molecules that we don’t want in the atmosphere and converting them to a form that has an established supply chain,” says Ticehurst. “They are converted, used as fuel and returned to the atmosphere, so it’s circular, and we get the power.” The circular aspects of the technology are maximized when the H2 used results from water electrolysis powered by renewable energy.
Ticehurst reports “immense interest” in the technology since the January launch, and notes that JM sold its first license for HyCOgen in March. The deal will be announced in the coming months.
F-T synthesis is also a key part of solar fuels. Synhelion (Lugano, Switzerland; www.synhelion.com) has developed a proprietary process that converts solar heat into syngas. This syngas is then fed into a modular synthesis plant and converted into liquid fuels via Fischer-Tropsch.
Synhelion is currently implementing an industrial-scale plant to produce sustainable kerosene from solar energy in Jülich in North Rhine-Westphalia, Germany, and has chosen Ineratec GmbH (Karlsruhe, Germany; www.ineratec.de) as its partner for the fuel production from the solar syngas.
The partners plan to rapidly scale their fuel production with support from industry partners such as Swiss International Air Lines and Lufthansa.
The F-T route also figures in a power-to-fuels project in Germany, directed by the carbon offset not-for-profit organization Atmosfair (fairfuel.atmosfair.de). Atmosfair is building an e-kerosene plant in Emsland, Germany that is capable of producing carbon-neutral SAF.
Conversion projects
A number of large biofuels projects moved ahead over the past year with the involvement of traditional petroleum refiners converting conventional petroleum operations into renewable-fuel production sites.
For example, in September 2021, Shell plc (London, U.K.; www.shell.com) announced a final investment decision to build an 820,000-ton/yr biofuels facility at the Shell Energy and Chemicals Park Rotterdam, the Netherlands (formerly known as the Pernis refinery). Once built, the facility will be among the largest in Europe to produce SAF and renewable diesel from waste. Advanced production methods will be used to make the fuels, Shell says.
As part of its “Powering Progress” strategy, Shell is transforming its refineries (which numbered 14 in October 2020) into five energy and chemicals parks. Shell aims to reduce the production of traditional fuels by 55% by 2030 and provide more low-carbon fuels, such as biofuels for road transport and aviation, and hydrogen. The Rotterdam facility is the second to be announced, following the launch in July of the Energy and Chemicals Park Rheinland, in Germany.
The Rotterdam biofuels facility is expected to start production in 2024. A range of certified sustainable vegetable oils, such as rapeseed, will supplement the waste feedstocks until even more sustainable advanced feedstocks are widely available. The facility will not use virgin palm oil as feedstock. SAF could make up more than half of the capacity, with the rest being renewable diesel, Shell says. Shell can adjust this mix to meet user demand.
In France, the TotalEnergies (Paris, France; www.totalenergies.com) Normandy platform started production of SAF in March 2022. This new site complements the company’s existing biojet-fuel production capacity. This move enables TotalEnergies to meet demand from its customers and respond to French legislation, which calls for aircraft to use at least 1% SAF effective January 1, 2022. In April 2022, Airbus powered two flights on its A380 aircraft using SAF that was made by TotalEnergies.
Neste Oyj (Espoo, Finland; www.neste.com) will modify its existing renewables production capacity in Rotterdam, the Netherlands, to enable production of SAF. Currently the refinery produces mainly Neste MY Renewable Diesel. The modifications to the refinery, an investment of approximately €190 million, will enable Neste to optionally produce up to 500,000 ton/yr of SAF as part of the existing capacity.
Neste expects the project to be completed in the second half of 2023. Together with the company’s ongoing Singapore refinery expansion, Neste will have the capacity to produce 1.5 million ton/yr of SAF by the end of 2023. Currently, Neste’s sustainable annual SAF production capacity is 100,000 tons. Neste MY SAF, in its neat form, reduces greenhouse gas emissions up to 80% compared to fossil jet fuel takling into account the full lifecycle, Neste says.
In February 2022, bp, which created a specialized international aviation fuel products and services division known as Air bp, began producing SAF from used cooking oil. The bp plant in Lingen is the first industrial production facility in Germany to use co-processing to produce SAF from waste and residues, bp says.
The Lingen refinery processes the used cooking oil together with crude oil in its existing facilities, with SAF as the end product. Thanks to co-processing, bp can continue to operate the existing plant with some modifications and extensions while also making a direct contribution to decarbonization.
Meanwhile, Marathon is currently in the permitting process for the conversion of its Martinez, California, facility to renewable fuels production. The permitting process includes discussion of possible future uses, and SAF is part of that discussion, a Marathon spokesperson says.
SAF offtake agreements
The expanded interest in using SAF over the past several years has been driven in large part by major players in the aviation industry, including airlines, aircraft manufacturers, gas-turbine engine makers, international shipping companies and others. According to the International Air Transport Association (IATA; Montreal, Que., Canada; www.iata.org), approximately 100 million liters of SAF were produced in 2021, and about 5 billion liters of SAF production annually are projected by 2025. Twenty new fuel offtake agreements were made during 2021 alone, and 61 forward-purchase agreements totaling 25.8 billion liters currently exist as of April 2022, according to ICAO. Virtually all major airlines have SAF purchasing agreements in place, including United, American, Delta, Southwest, Jet Blue, Alaska Airlines, FedEx, DHL, Luftansa, Qantas, KLM and others.
As one example, bp is to supply DHL Express with sustainable aviation fuel until 2026 as part of a new strategic collaboration with the global logistics company. The bp agreement is one of two deals comprising the largest SAF deals in aviation to date, with a combined volume of more than 800 million liters of SAF. The other supplier, entering in to separate agreement with DHL and making up the total volume, is Neste.
In its Sustainability Roadmap, Deutsche Post DHL Group has committed to using 30% of SAF blending for all air transport by 2030. bp will provide SAF produced from waste oils. Such SAF from wastes and residues can provide greenhouse gas emission reductions of up to 80% over its lifecycle compared with the conventional jet fuel it replaces, thereby reducing DHL’s carbon footprint, DHL says. DHL Express transports more than 480 million documents and packages annually across its global network of 220 countries and territories.
Another example of a prominent offtake agreement came as part of the investment agreement between Honeywell and Alder Fuels. United is committing to purchase 1.5 billion gallons of SAF from Alder when produced according to its requirements. United’s purchase agreement is said to be the largest publicly announced SAF agreement in aviation history.
In December 2021, Austrian fuel maker OMV and Austrian Airlines (AUA) announced the production and use of regional SAF in Austria. The two companies agreed on the production and fueling of 1,500 metric tons of SAF in 2022.
The sustainable fuel is produced at the OMV Schwechat Refinery by co-processing Austrian used cooking oil in the fuel production process. This approach makes the entire production chain as regional as possible and keeps transport routes to a minimum. Compared to conventional kerosene, SAF makes for a CO2 reduction of more than 80% over the entire lifecycle. With the direct pipeline connection to the Vienna International Airport, SAF was slated to be available for fueling Austrian Airlines aircraft as of March 2022.
Scott Jenkins