As environmental awareness receives renewed focus in the government, the public and industry, it appears that higher standards will be applied to processors to achieve even higher oxides-of-nitrogen (NOx) removal than in the past. And since selective catalytic reduction (SCR) has been proven to be one of the most efficient systems for NOx removal from high output sources, such as coal-fired power plants and generators used for back up power, it makes sense that the chemical process industries (CPI) are using this same technology to reduce harmful emissions from their plants.
The beauty of SCR is that it is an already proven technology, making it a reliable and trusted choice for processing facilities that need to reduce NOx emissions. And, since SCR has existed and been in mainstream use for more than 15 years, system and catalyst providers have been tweaking their technologies to make them even more efficient.
“New developments of SCR catalyst and in the design of the systems themselves make it possible to reach NOx conversions of about 95% without ammonia slip,” says Peter Lindenhoff, general manager of SCR/De-NOx Catalyst and Technology with Haldor Topsøe (Lyngby, Denmark). “This means it is now possible to install SCRs on the highest NOx producing units in the plant and avoid doing NOx control on smaller units while still meeting the overall NOx reduction of the plant. A few large SCRs are more cost efficient than doing NOx control via methods such as ultra-low NOx burners on all units.”
Not only is the technology proven and improved, but it is also possible to easily retrofit SCR to existing facilities. SCRs have successfully been installed on practically all types of furnaces, according to the experts. And, the continued design improvements mean it’s also possible to reduce the pressure drop that used to be associated with SCR, making it possible for processors to keep and use most of the existing equipment in their facility. The catch in a retrofit, however, is the process temperature and its effect on the catalyst. Some catalysts perform better within a specific temperature range, says Dale Purdy, sales and marketing manager with Turner EnviroLogic (Deerfield Beach, Fla.). “Performance will drop off dramatically if the process temperature is too high or too low. We see it best between 400 and 800°F, so in an existing facility or process that generates that temperatures it’s a perfect fit.”
However, if the temperature is above or below this sweet spot, steps can be taken to boost catalyst performance. “We have used assist heaters to raise the temperature of the waste stream to get it within the right range. If the process is too hot, we can bring cooler air or outside air into the waste stream to get it to a more favorable operating temperature,” explains Purdy. “It takes some extra planning, but it is possible to do a retrofit and get the operating temperatures to a place where the catalyst will operate best.”
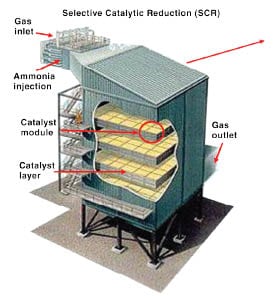
Reducing ammonia slip
Whether it’s a new application or a retrofit, reducing or eliminating ammonia slip is a big deal for SCR, as Lindenhoff indicated above, so providers are working on different methodologies to achieve this improvement. “Ammonia slip is a critical problem for SCR users because ammonia slip is a very evident issue due to its odor. Often putting out ammonia can be worse than NOx emissions,” says Ben Velazquez, engineering manager with Ducon (Farmingdale, N.Y.).
Ammonia slip — where expensive unreacted ammonia is exhausted to the stack — occurs when too much ammonia is injected. In some regions of the U.S., the amount of ammonia slip is also part of a plant’s operating permit restrictions.
To avoid the problem, Ducon is using heavily engineered calculations to determine the proper amount of ammonia to be injected into a system. The company uses instrumentation to track flow, pressure, temperature and other inputs that vary within a system. These inputs are monitored and factored in to achieve a more accurate ammonia calculation. “If you don’t use the right amount of ammonia in relation to the amount of catalyst you need for NOx concentration, then you end up with excess or unreacted ammonia, so getting the amount right the first time goes a long way toward avoiding slip,” he says. The company also monitors the output of the SCR, so if there is an ammonia slip, it can make necessary adjustments in the formula.
The folks at Turner EnviroLogic offer an ammonia-vaporization system that uses waste heat from the process itself to vaporize the ammonia in conjunction with a distinct method of ammonia distribution. “We use a self-balancing ammonia-injection grid instead of a series of valves and regulators that typically need to be worked by the Wizard of Oz behind the curtain pulling all sorts of cranks and levers to keep things moving along,” says Purdy.
He says the company’s inherent self-balancing design provides an equal flow of ammonia across the catalyst with minimal effort. The combination of these two features helps reduce ammonia slip because if ammonia is properly distributed across the catalyst, there’s a much better chance of reducing the amount of unused ammonia. “You don’t have to flood the system with ammonia to make it work,” he explains.
Catalyst providers, too, are working to reduce ammonia slip. Randy Sadler, director of marketing and sales with CoaLogix (Charlotte, N.C.) says his employer is working on a multi-pollutant reduction system that could possibly remove NOx, SOx, PM, mercury and ammonia slip via catalyst. “We’ve been working with different technology leaders to use their products in conjunction with our regenerated SCR catalysts and sell them as a complete system to remove a variety of pollutants for the end user.”
He says the company is a few months away from a technology that would reduce ammonia slip via a catalyst. Sadler further says the technology would likely feature banks of regenerated SCR catalyst and, at the tail end, a thin strip of “what we’ll call ‘ammonia catalyst’” that would clean up the excess ammonia emitted from the SCR. “It doesn’t take much to clean up ammonia at the tail end.”
Topsøes Lindenhoff agrees that this technology is probable for the future of SCR. “Fifteen years ago we developed the DNO catalyst, a combined NOx and CO removal catalyst. With the development of lower limits for ammonia slip, it looks like the units in the future will have a DNO catalyst downstream from the SCR to reduce the NH3 slip together with CO and VOC removal,” he says.
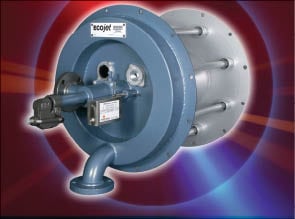
Moving SCR to the end of the pipe may help reduce NH3 slip in more ways than one, according to Brad Morello, technical services manager with CRI Catalyst (Houston). “Success in reducing NH3 slip is more favorable when designing an SCR system at lower temperatures. One of the reasons for lower slip at lower temperatures relates to the enhanced adsorption capability of SCR catalyst in general.”
And the temperatures are typically lower at “end of pipe” installations since lower temperatures are found farthest away from the heat source and nearer to the exhaust stack. Plus, in many situations, closer to the stack yields more space and residence time available for NH3 mixing, thus increasing the possibility for a homogeneous mixture of NOx and ammonia to be established at the SCR catalyst inlet. This is also key in the effort to minimize ammonia slip. As a bonus benefit, this location may also be preferred for low-to-no N2O formation. Like CO2, N2O is considered a greenhouse gas. In the near future, suppressing the formation of N2O will likely be a secondary goal to NOx reduction, says Morello. It is believed that at a sufficient temperature window, N2O formation occurs from the partial oxidation of ammonia in the presence of certain metallic compounds commonly present in and around an SCR system. In the chemical process of SCR, ammonia is often injected as a reducing agent. At certain conditions and at lower temperatures, minimal-to-no N2O formation has been demonstrated. Therefore, the lower temperatures at the end of pipe may be preferred for low-to-no N2O formation, as well as reduced ammonia slip.
Joy LePree