Compliance with industry- and machinery-specific safety standards and classifications is essential to make the safest possible environment for plant personnel, especially those working in potentially hazardous conditions
Navigating the world of industrial safety standards can feel like being in uncharted waters. In the sea of standards that need to be applied to machinery, systems, processes and facilities, companies can find a beacon of hope by cultivating machine safeguarding solutions to comply with standards (Figure 1). These standards may come from a wide range of global organizations, including the following:
- The International Organization for Standards (ISO; Geneva, Switzerland; www.iso.org)
- The American National Standards Institute (ANSI; New York, N.Y.; www.ansi.org)
- The Occupational Safety and Health Administration (OSHA; Washington, D.C.; www.osha.gov)
- The American Society of Safety Professionals (ASSP; Park Ridge, Ill.; www.assp.org)
- The National Fire Protection Association (NFPA; Quincy, Mass.; www.nfpa.org)
This article describes the experiences of a large global chemical manufacturer with locations around the world that recently navigated the implementation of safety standards and processes. Compliance with several industry- and machinery-specific safety standards was applied to make the safest possible environment for its employees. Some of these standards are listed in Table 1.
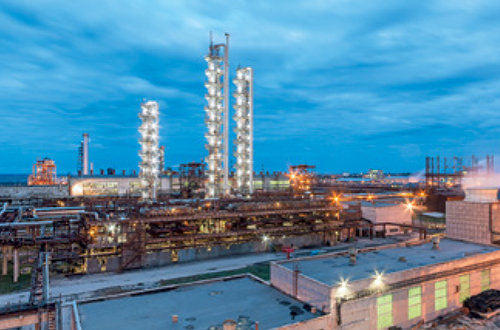
FIGURE 1. The vast array of equipment types and materials handled mean that chemical manufacturing facilities must comply with a wide range of industrial standards to ensure the safety of employees, equipment and the environment
This article outlines a step-by-step overview of how this chemical manufacturer applied these standards to make machinery safer for employees.
1. Conduct a risk assessment
When designing or installing a machine, any potential risks must be assessed, evaluated and mitigated. Where necessary, additional protective measures must be implemented to protect operators and other individuals from any remaining hazards.
Sometimes this process begins with an activity called machine safety prioritization, which provides manufacturers with a list that describes which machinery in the facility should be prioritized first for a safety upgrade and which ones can be completed later (Figure 2). Other projects start immediately with a more comprehensive risk assessment, which is a sequence of logical steps based on the systematic analysis and evaluation of risks.
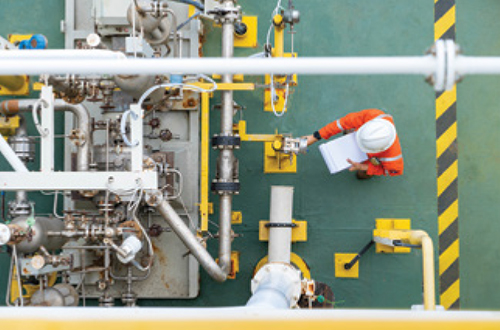
FIGURE 2. Machinery safety prioritization is often the first activity in the risk assessment process. It helps plants to determine which pieces of machinery are in most critical need of safety upgrades
The main goal of a risk assessment is to identify and document hazards for machinery, current manufacturing processes and other elements of the chemical production process. Risk assessments evaluate the tasks performed and help to identify potential hazards, the potential severity of hazards, the frequency of exposure to hazards and the specific strategies that can be implemented to mitigate those hazards and avoid harm to employees and the machinery.
This methodology will identify the potential hazards associated with a machine or group of machines and quantify the associated risk via the following measures:
- Identifying hazards during setup, operation, maintenance and cleaning
- Establishing minimum performance requirements for the safety-related parts of the control system
- Evaluating existing risk-reduction measures and providing recommendations for improvement
Although the many prerequisites for building safe machines and systems are diverse, all risks must be identified. Then, appropriate measures for minimizing risk need to be identified and their potential effectiveness at reducing risk defined.
A risk assessment enables manufacturers to identify gaps in safety compliance to begin the work to put together a plan to improve upon these gaps. After this large chemical manufacturer completed the risk-assessment process, discussions were commenced to develop a risk-mitigation strategy to bring the equipment into compliance with the applicable standards for the industry.
2. Craft a safety concept plan
Within this global chemical manufacturer’s numerous facilities around the world, people are constantly interacting with machines. The inherent hazards within the chemical process industries (CPI) make it essential that the employer properly address those concerns to provide a safe work environment for its employees, so it was an essential priority to raise the level of safety and awareness within its facilities.
The ultimate risk-mitigation strategy is designed according to the results of the risk assessment. If necessary, risk-reduction activities can follow a risk assessment. Risk reduction can include the completion of a safety concept or a functional-safety design of the control systems, as well as engineering the design of the suitable protective measures.
The safety standard level that the corporation required was identified as Performance Level d (PLd). A performance level is a value used to define the ability of safety-related parts of control systems to perform a safety function under foreseeable conditions. The required performance level is used to achieve the required risk reduction for each safety function. The performance level of safety-related parts of a control system must be equal to or higher than the required performance level. Performance levels range from a to e, and the Performance Level Requirement (PLr) is based on three parameters: severity of injury, frequency and/or exposure to hazard, and possibility to avoid hazard or limit harm.
With this global chemical manufacturer, the ISO EN13849-1 standard (see Table 1) was referenced to determine the necessary performance level to reduce risk on machinery in its facility. The company determined that PLd was the best option for its processes. In some cases, this performance level is higher than required, but the company believed that setting this requirement at PLd would provide a distinct advantage to protecting its employees while meeting the core values of the company. The next step involved determining the most efficient, optimal way to incorporate a compliant safety solution into the company’s complex applications. Safety is vitally important, but it is also critical to not unnecessarily hinder processes, productivity and uptime.
Many of the control components and devices at the manufacturer’s facilities are general-purpose, and therefore must be tailored for use in a Class 1, Div. 2 environment (for instance, installed into a purged cabinet or an explosion-proof enclosure). Other times, areas of the facility were unclassified to install certain components. Applying the correct products to meet the appropriate standards was critical, especially for a global organization with similar machines located in different facilities all over the world.
Market availability of differentiated solutions and services from third-party providers affords plants several advantages. This enables plants to use numerous products that may not be rated for Class 1, Div. 2, but still meet that certification by using multiple relevant products (Figure 3).
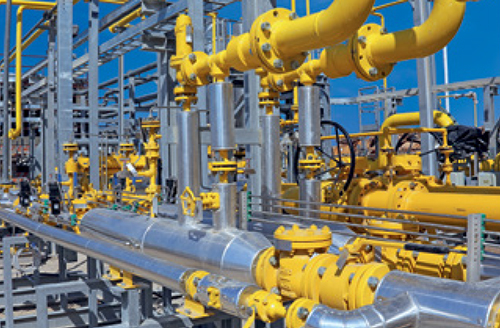
FIGURE 3. Plants may include a blend of generalpurpose and customized components, so companies must seek differentiated solutions to establish an overarching safety plan
3. Execute machine safeguards
As part of the manufacturer’s machine safeguarding solution, the risk-mitigation strategy from the risk assessment (Step 1) and functional safety design of the controls from the safety concept (Step 2) are integrated into the existing equipment to provide that final safe working environment for the plant. Typical safety-critical applications within the chemical industry include screen pack changers, box dumpers, pelletizers, drum lines, shrink wrappers and more. This global chemical manufacturer has all of these types of machinery and plans are in place to apply appropriate safety measures to each of them. More details about specific safety measures for each equipment category are provided in the following sections.
Screen pack changers.The chemical manufacturer utilized screen pack changers as a part of its process. This machine’s main purpose is to remove contaminants from a molten polymer stream. The screen changer consists of a hydraulic cylinder. The cylinder has two sections in the slide plate where the molten polymer flows through. The screen packs on the machine can often be changed during operation without interrupting workflow or reducing production time.
However, there are hazards associated with this machine that needed to be addressed. First, there is the potential for third-degree burns from the molten hot polymer that flows through the machine. Second, it provides a pinch-point hazard with the potential for amputation of limbs. Both of these safety hazards were addressed as part of the risk mitigation strategy, and the machinery was made safe to meet standards and ensure the safety of workers interacting with this machinery with Class 1, Div. 2 non-contact safety switches and other safety equipment.
Shrink/stretch wrapper. The shrink/stretch wrapper machine consists of a spinning table for finished product on pallets to be wrapped in stretch wrap. There are a number of hazards associated with this type of machine. There is the potential for crushing hazards, pinch-point hazard, and thermal hazard. All of these can lead to broken bones, potential amputation and burns if not addressed properly with safety measures. In order to protect people from these hazards, safety light curtains can be implemented at the entrance and exit of the machine with a request-to-enter locked door. When someone requests to enter, the rotating arm that wraps the product will stop moving when the door is opened.
Filter press.The filter press machine consists of frames of cloth filters that remove solids. The frames become full of the solids and must be manually cleaned. This is a high frequency activity carried out by workers of the global chemical company. Hazards associated with this machinery include crushing hazards, nip-point hazards and impact hazards. These have the potential for amputation or fractures of limbs. These safety hazards will be addressed to ensure the continued safety of workers. This is done by using a moveable interlock guard to provide access to the machine, but still allowing access to the machine when necessary. When someone enters the work area, an output indicates a stop to the hydraulic cylinder.
Palletizer. A palletizer machine utilizes electric and pneumatic actions to move and load finished product onto wooden pallets (Figure 4). Similar to other machines, the palletizer has a crushing hazard and a pinch-point hazard, with the potential for broken bones or amputation. Safety measures are planned to prevent these from happening. A robot palletizer is one option to meet safety standards in this application.
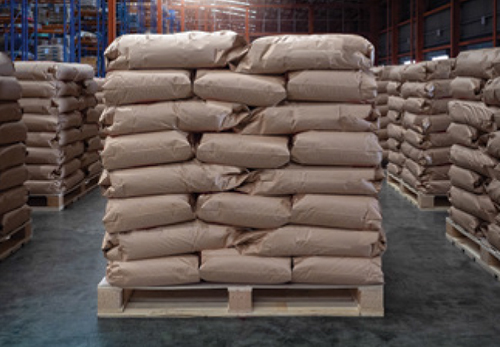
FIGURE 4. Chemical products are loaded onto pallets for shipping. This process carries the risk for personnel injuries and product loss if certain preventative measures are not taken
Overcoming major challenges
Throughout this ongoing project, there have been a few challenges to overcome. The biggest challenge was that this was a large, ongoing international project with more than one standard that needed to be implemented across several international and U.S. locations. This required an in-depth knowledge on the intent of all the standards, as well as how to properly implement them within these complex applications. This also proved challenging when finding suppliers for the project. Some manufacturers may certify to FM standards, but not to ATEX standards, meaning that certain items could not necessarily be used globally.
In light of these challenges, the company put together a team with third-party partners that have branches in many countries and include broad expertise and knowledge in the safety industry internationally, with active members on a wide range of safety standardization committees. Another important factor was to develop vendor-agnostic solutions that meet safety standards regardless of what type of equipment has been installed in each facility. A final challenge is ensuring that the proper validation is carried out for the developed risk and safety plans. The validation phase is a comprehensive point-to-point check to ensure everything identified in the risk-mitigation strategy and engineered during the functional safety design of controls has been implemented properly during installation.
Authors
Carolyn Reifsteck is the manager of business consulting for safe productivity at SICK, Inc. (6900 W. 110th St., Minneapolis, MN 55438; Phone: 800-325-7425; Email: info@sick.com). For over seven years, Reifsteck has provided support for customers at SICK on safety solutions and services. She is currently the manager for the safe productivity team, focused on providing safety services, including risk assessments, engineering consultations, validation and commissioning consults and more.
Paul Hensy is a safety solution specialist at SICK, Inc. With over 25 years of experience in the industrial safety industry, Hensy is an experienced safety specialist with a demonstrated history of providing support for process control, engineering, control systems design, business development, and process automation. He has been with SICK for over 11 years.
Chris Liston is a sales manager at SICK, Inc. In this role, he is responsible for working with key international customers and top-tier engineering firms in the process automation space. He has spent most of his career working in the oil-and-gas industry, with the last seven years specifically in process automation. Before joining SICK, Liston was the regional sales manager of HIMA Americas, Inc.