Thermal oxidation is used to destroy tailgas from biogas-upgrading facilities. Presented here are guidelines for selecting the proper method
With the evolving economics of renewable energy credits comes increased interest in biogas-upgrading facilities. Renewable natural gas (RNG) plants are being designed and built at a remarkable pace. Many scholarly articles have been written to address the pros and cons of each popular method of biogas enhancement. The objective is to process as much of the methane into a high-purity form for injection into the natural gas pipeline, while efficiently removing all undesirable impurities from the raw gas. These impurities include O2, H2O, H2S, N2, CO2 and other trace amounts of volatile organic compounds (VOCs) that are present in the feed.
A combination of technologies is often used to accomplish this goal, and most of the facilities, at some point, must deal with the issue of disposing or destroying the impurities that are removed from the incoming raw gas. Since the tailgas contains VOCs, thermal oxidation is often employed. This article is a general guideline for selecting the proper method of thermal oxidation that will effectively and efficiently destroy tailgas produced by the typical biogas-upgrading facility.
Thermal oxidizer selection
Thermal oxidation is the controlled combustion of process gases. The process is governed by time, temperature and turbulence. The overriding parameter is temperature. Typically, for non-halogenated compounds, 1,500˚F is required to destroy VOCs when sufficient turbulence is present, and the mixture is retained at that temperature for 0.5 s or more, with the proper volume of oxygen for combustion. Evaluating the type of thermal oxidizer used is critical for optimal plant economics.
The selection process for thermal oxidizers is driven by the conditions of the incoming gas stream: volume and composition of gas to be treated, heat value of the stream (Btu/ft3), and temperature are important factors. Also needing consideration are the regulations for air permitting driven by the local regulatory body. Evaluation of all these factors will provide a solution to the question of which type of oxidizer is right for any given process.
By far, the most effective type of thermal oxidizer is a direct-fired unit (DFTO), which can achieve greater than 99.9% destruction of VOCs (Figure 1). Most often, DFTOs are the least costly type to procure, but depending on the contribution of thermal energy from the incoming stream, they can be the most costly to operate. DFTOs are best for processes where the tailgas has sufficient VOCs to support self-sustaining direct combustion, (typically equivalent to 6 vol.% methane).
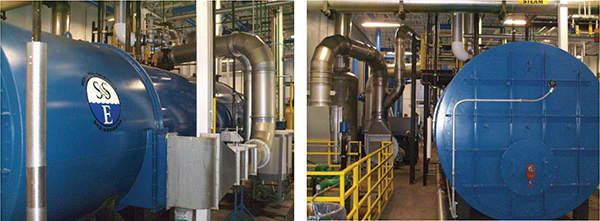
Figure 1. Direct-fired thermal oxidizers, such as those shown here, can destroy greater than 99.9% of volatile organic compounds in tailgas
DFTOs can be coupled with a variety of heat-recovery options, including heat-recovery steam generators (HRSGs), hot-water or hot-oil systems, and air-to-air heat exchangers. For applications with low volumes of incoming gas or high heating values, it is most often a cost-effective solution to destroy tailgas, as the cost of operation is directly related to the amount of heat required to raise the temperature of the incoming stream, along with required combustion air, to 1,500˚F.
A direct-fired unit is the most compact type of thermal oxidizer per cubic foot of incoming process gas. It is typically the least costly to purchase because the volumes required for retention of the gas are minimized by the simple nature of the process. A burner is provided to initially raise the temperature of the combustion chamber to the proper operating level of 1,500˚F. Once at this level, the process gas can be safely introduced to the chamber for destruction.
As internal temperature rises, the start-up burner proportionally reduces the supplemental fuel introduced and the process is managed by controlling the proper amount of dilution air to manage the chamber temperature at a setpoint. When the volume of gas changes, the amount of dilution air is proportionally adjusted to maintain chamber temperature. Should the heat content of the incoming stream fall below the level required for self-sustaining operation, the burner will fire and maintain proper destruction conditions in the chamber.
For applications where heat is required for plant operation, the supplemental fuel burner is configured to provide sufficient output of the system to meet the requirements of the process, while still effectively destroying the VOCs. The heat of combustion of the incoming waste stream thus becomes the supplemental fuel for the heating requirements of the plant.
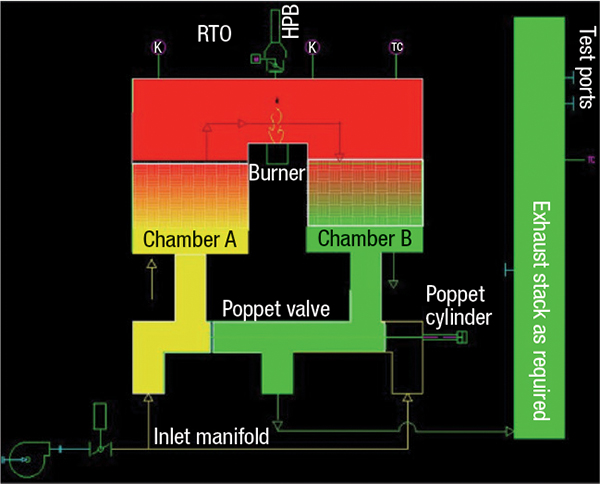
Figure 2. In an RTO, process exhaust enters the heat exchanger, where it is pre-heated
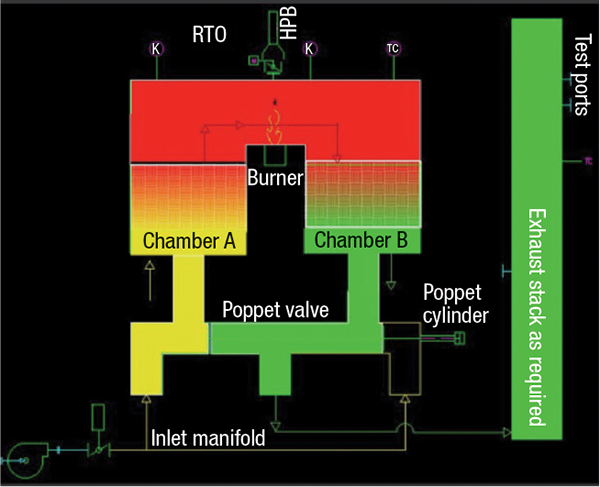
Figure 3. The energy value of the exhaust stream may be sufficient to sustain the oxidation process
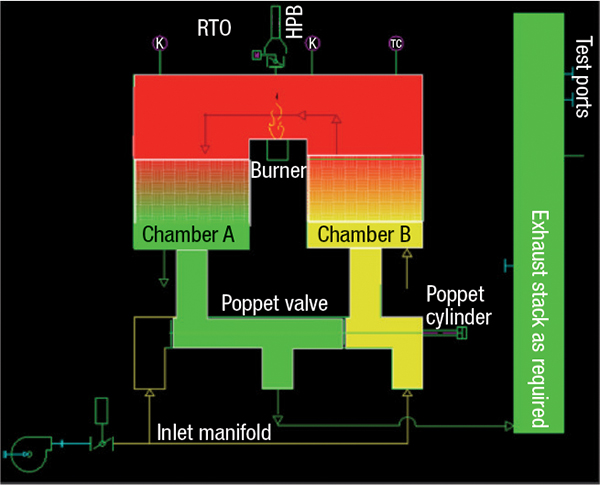
Figure 4. Poppet valves close off Chamber A on the inlet stroke
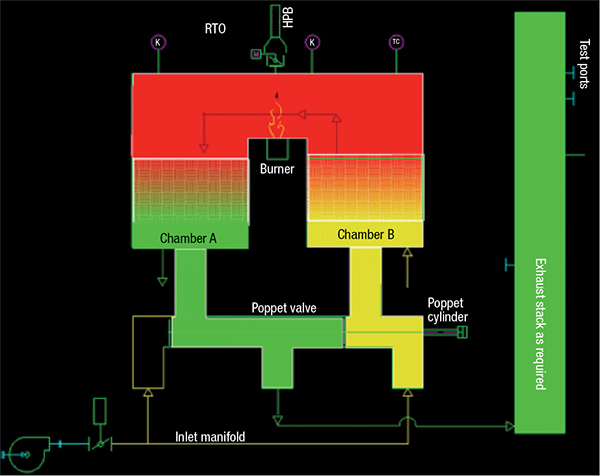
Figure 5. Pollutants are oxidized in the combustion chamber and the cleaned gas exits through Chamber A
Regenerative thermal oxidizers
On the other side of the process spectrum, situations where higher volumes of low-heat-content gas are present call for the application of different oxidizer technology. Regenerative thermal oxidizers (RTOs) are typically employed for situations where the heat content of the incoming stream is not sufficient for self-sustaining direct combustion, and where the use of supplemental fuels needs to be minimized. Understanding the operation of a typical RTO is valuable when considering the best equipment for plant operations. An RTO operation sequence is as follows:
- Process exhaust is preheated in the ceramic media heat exchanger as it migrates toward the combustion chamber
- Air temperature approaches oxidation temperature as it enters the combustion chamber
- Combustion chamber burner provides needed temperature to oxidize the pollutant
- Oxidized or clean air exits through the adjoining ceramic media RTO tower Chamber B (exhaust stroke)
- Heat energy is collected from the clean air stream in the ceramic media
- Clean air exits to the RTO exhaust stack and then to the atmosphere
- Pneumatic or hydraulically actuated poppet valves can be used
- Chamber A is now closed off on the inlet stroke (cool from previous pre-heating).
- Chamber B is now open to the process exhaust inlet stream (hot from newly stored heat)
- Exhaust air is now preheated in Chamber B
- Pollutants are oxidized in the combustion chamber
- Clean air now exits through Chamber A, where combustion heat is stripped
- Clean air exits to the exhaust stack to atmosphere
With the shifting of the valves comes a small amount of the incoming stream, which does not encounter destruction conditions. The resulting destruction effectiveness is 98–99%. However, the reduction in supplemental fuel is dramatic for low-heat-content streams. This is achieved by the high degree of heat recovery (95–97%) possible with this technology. High amounts of inert components in the tailgas often suggest selecting RTOs for destruction of VOCs with minimal use of supplemental fuels. After all, the point of a biogas-upgrade facility is to put methane in the pipeline, not consume it in the process. It is understood that small amounts need to be used for startup and for safe, efficient operation of the process.
Like any other form of thermal oxidation, a startup burner is employed to raise the temperature of the unit to proper destruction conditions. Once at proper temperature, the process gas can be introduced, blended with the correct amount of dilution/combustion air and the RTO cycles through the sequence of operation previously pictured. The burner will provide supplemental fuel to maintain the combustion chamber temperature should the heat content fall below that required for self-sustaining operation. Utilizing a hot-gas bypass can expand the range of possible operating conditions by diverting some of the combusted air directly to atmosphere, rather than sending it through the heat-recovery media.
Utilization of RTOs can assist with optimizing the economics of plant operation (Figure 6). While an RTO unit costs more to purchase per cubic foot of incoming gas than a DFTO, the savings in supplemental fuel for low-heat content streams normally result in the technology paying for itself rather quickly. Important considerations for the use of an RTO in the process include the following: variability of the incoming stream volumes’ heat content; temperature; and the presence of substances that can foul the ceramic heat-transfer media used in the chambers. Siloxanes will produce SiO 2, which can deposit on the media, reducing its effectiveness. While silica-resistant ceramic heat-transfer media can be employed to minimize this potential, it is a factor when considering the use of an RTO for tailgas destruction.
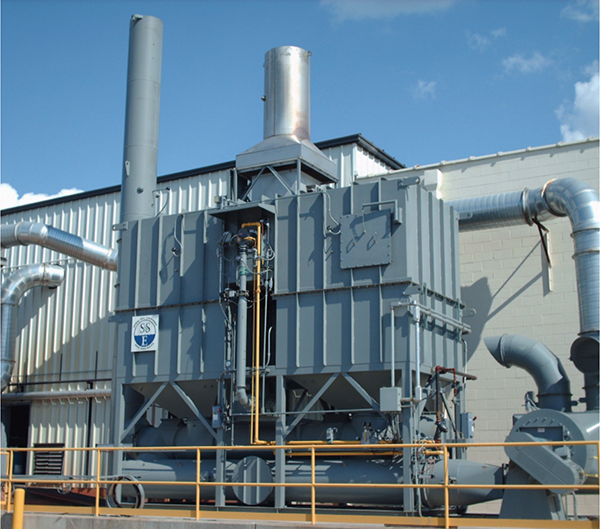
Figure 6. A typical RTO, like the one shown here, can help to optimize the economics of plant operation
Careful monitoring of the incoming stream is required. LEL (lower explosive limit) sensors and proper programming of the temperature controls and air introduced will keep the process in the safe-operating zone. Annual inspections will keep the valves and seats in the proper condition required for effective destruction.
When choosing a vendor for a thermal oxidation process, it is wise to seek out a company with expertise in all forms of oxidizers. A one-size-fits-all mentality will result in a system that either costs too much to purchase, operate or maintain. A complete understanding of not only the normal operating variations, but all of the potential upset conditions, is critical for the long-term, efficient, economical and safe operation of any thermal oxidation system. Vendors should have extensive process knowledge, and the mindset to match technologies to each facility’s process conditions. n
Edited by Scott Jenkins
Authors
Anoosheh Oskouian is President and CEO of Ship & Shore Environmental, Inc. (S&SE; 2474 North Palm Drive, Signal Hill, CA 90755; Phone: 562-997-0233; Email: [email protected]), a woman-owned business specializing in air pollution capture and control systems for industrial applications. Ship & Shore helps manufacturers meet volatile organic compounds (VOC)-abatement challenges by providing customized air pollution abatement systems for various industries. Oskouian is the environmental industry’s only female CEO. She has expertise in air-pollution abatement and waste-heat reovery, with two decades of experience in industrial and commercial project construction of air design and fabricating combustion equipment, including thermal and catalytic oxidizers, boilers, burners, carbon and zeolite absorption mechanisms.
Mike Pawlowski is senior technical sales engineer at Ship & Shore Environmental (Email: [email protected]). Pawlowski brings almost four decades of experience in sales and engineering of sustainable energy solutions, thermal oxidizers, maintenance and plant engineering in commodity chemicals within several markets. Pawlowski oversees Midwest sales activities across many industries and handles engineering of challenging applications globally. Prior to joining S&SE, Pawlowski was a project engineer at PHG Energy, where he provided sales and engineering support for downdraft and fluidized-bed gasification processes, and developed a strategy for gasification of municipal solid waste. He holds a B.S.Ch.E. from Michigan Technological University