Understanding the different classification methods is necessary to better select the explosion-protection techniques that will be used
Explosion protection is essential for many companies, and those companies have decision makers. But before any decisions can be made, there are some important factors one must consider. These factors include what is most efficient and economical, as well as knowing the basics of explosion protection; so the decision makers are headed in the right direction. We will highlight many of the different “things to know,” but first, let’s step back in time and take a look at the background of explosion protection.
Backdrop
After World War II, the increased use of petroleum and its derivatives brought the construction of a great number of plants for extraction, refining and transformation of the chemical substances needed for technological and industrial development.
The treatment of dangerous substances, where there exists the risk of explosion or fire that can be caused by an electrical spark or hot surface, requires specifically defined instrumentation located in a hazardous location. It also requires that the interfacing signals coming from a hazardous location are unable to create the necessary conditions to ignite and propagate an explosion.
This risk of explosion or fire has been the limiting factor when using electrical instrumentation because energy levels were such that the energy limitation to the hazardous location was difficult, if not impossible, to obtain. For this reason, those parts of the process that were considered risky were controlled with pneumatic instrumentation.
Moving forward
Now let’s move forward 70 years, where almost everything you can think of can be found at the touch of a finger. From pneumatics to quad core processors, information gathering has definitely changed, but the same principles for working or gathering information out of a hazardous area remain the same. Its just that today we have multiple options. In order to exercise those options, we must first determine if the danger of an explosion exists and how severe it may be.
What is a hazardous area?
Hazardous areas are most frequently found in places where there is a possibility of an emission of flammable gas or dust. A hazardous area can occur in normal operation, in the event of a fault, or due to wear and tear of seals or other components.
Now the risk of an ignition of an air/gas mixture in this hazardous area depends on the probability of the simultaneous presence of the following two conditions:
- Formation of flammable or explosive vapors, liquids or gases, or combustible dusts or fibers with atmosphere or accumulation of explosive or flammable material
- Presence of an energy source (electrical spark, arc or surface temperature) that is capable of igniting the explosive atmosphere present
Determining hazardous areas in a plant is normally performed by experts from various disciplines. It may be necessary for chemists, process technologists, and mechanical engineers to cooperate with an explosion-protection expert in order to evaluate all hazards. The possible presence of a potentially explosive atmosphere as well as its properties and the duration of its occurrence must be established.
Also understanding terms such as minimum ignition energy (MIE), upper and lower explosive limit (UEL/LEL), flash point, and ignition temperature in the evaluation of your hazardous area will also provide a clearer direction on how severe a hazardous area might be.
In any situation involving an explosive material, the risk of ignition must be taken into account. In addition to the nominal rating of materials under consideration, parameters related to the process involved are especially important in the evaluation. For example, the risk of explosion may be caused by the evaporation of a liquid or by the presence of liquid sprayed under high pressure. It is also important to know which atmospheric conditions are present normally and abnormally. The range of concentration between the explosion limits generally increases as the pressure and temperature of the mixture increases.
Divisions and zones
Once it has been determined that a hazardous area exists, it now needs to be classified. While the physical principles of explosion protection are the same worldwide and are not differentiated, there are two different and distinct models to define your hazardous area —divisions and zones — both of which are accepted and utilized worldwide.
In rather simple terms, we can differentiate between the International Electrotechnical Commission (IEC; Geneva, Switzerland; www.iec.ch) (zones) and the North American (division) procedures. The differences lie in the categorization of hazardous areas, the design of apparatus, and the installation technology of electrical systems. The categorization of these areas is carried out in North America in accordance with the National Electrical Code (NEC) NFPA 70, article 500. The European Zone practice is described in IEC/EN 60079-10.
So how does each work? First let’s start at the basics, and then we’ll cover each individually.
Defining the area
Hazardous location or area classification methods specify the danger of fire or explosion hazards that may exist due to flammable gases, vapors, or liquids within a plant or working environment. These are explained by defining the type of hazardous material present, severity of the hazard, and probability of the hazard. It may also depend on the likelihood of the hazard, risk of an explosion, and the boundaries of the hazardous location.
This is usually determined by a HAZOP (hazard and operability) study and documented on a set of electrical plot plans on record in every plant.
For divisions, the type of material is given by a class designation, as shown in Table 1. These can be broken down further into sub-groups, as shown in Table 2.
Once we have determined the hazardous material we are working with, the probability of an explosion and boundaries must also be taken in to consideration. The division method is divided into two areas: Division 1 and Division 2 (Table 3). These were created in 1947 when the NEC first recognized that different levels of risk exist in hazardous locations. Figure 1 shows a typical example of a Class I hazardous area utilizing Division methods of area classification.
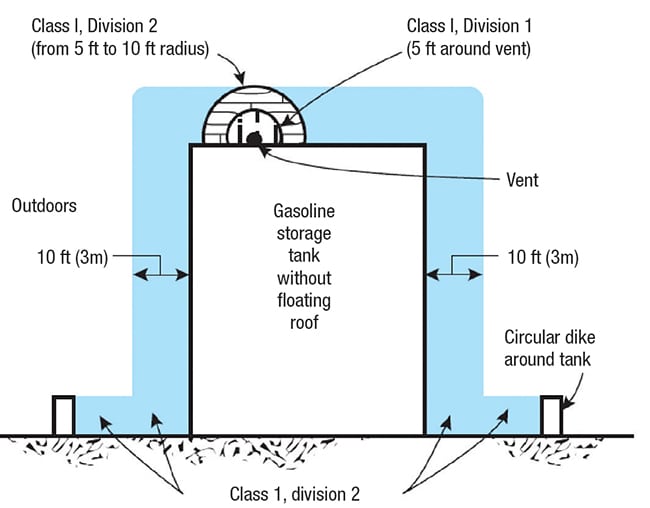
FIGURE 1. Shown here is a typical example of a Class I hazardous area utilizing division methods of area classification
In comparison to the division-based area classification, which is prevalent throughout North America, the zone-based architecture prevails in the rest of the world.
Zones are similar in nature to divisions where type of hazardous material present, severity of the hazard, and probability of the hazard and boundaries must be determined. Zones are in accordance with IEC/EN 60079-10, which states that any area in which there is a probability of a flammable gas or dispersed dust must be classified into one of the areas shown in Table 4.
Similar to the division method of area classification, zones can be better rationalized by looking at the example shown in Figure 2.
With a slightly different approach, IEC 600079-0 requires apparatus to be subdivided into two groups, as shown in Table 5.
The groups indicate the types of danger for which the apparatus has been designed. Group I is intended for mines. Group II concerns above-ground industries (electrical apparatus for hazardous areas with potentially explosive gas (dust) atmosphere except firedamp hazardous mining areas) and is subdivided into II G (gases) and II D (dusts).
Similar to divisions, the zones offer a sub material classification as well. Table 6 shows how this approach compares to the North American equivalent.
Finally, when classifying your hazardous area, whether it be division or zones, you must also classify the maximum surface temperature that can go in to the hazardous area. The maximum surface temperature must be below the minimum ignition temperature of the gas/dust present.
In North America as in Europe, six temperature classes are differentiated, T1 to T6. The classes T2, T3 and T4 are divided into further subclasses, as indicated in Table 7.
In Europe, the apparatus are certified on the basis of design and construction characteristics. From a practical point of view, the two systems are equivalent, even if there are minor differences, but before you run out and choose the most convenient method for you, it is important that you consult your local authority having jurisdiction to learn what method is allowed or, in fact, preferred.
The initial steps to determine whether a hazardous area exists and classify that area may seem rudimentary to some, but they are important as they now open up the multiple methods of protection, which may or may not be allowed, depending on whether you classified your area by divisions or zones.
Protection methods
There are three basic methods of protection — explosion containment, segregation and prevention.
Explosion containment. This is the only method that allows the explosion to occur, but confines it to a well-defined area, thus avoiding the propagation to the surrounding atmosphere. Flameproof and explosion-proof enclosures are based on this method.
Segregation. This method attempts to physically separate or isolate the electrical parts or hot surfaces from the explosive mixture. This method includes various techniques, such as pressurization, encapsulation, and so on.
Prevention. Prevention limits the energy, both electrical and thermal, to safe levels under both normal operation and fault conditions. Intrinsic safety is the most representative technique of this method.
My application requirements
Now the questions really start racing in: Which should I use? Which one offers the best protection? What if all of my equipment is not low powered? My plant is already using a technique; can I use another protection method? Can they co-exist? Who makes that decision? Why should I use one method over the other? Can I use two methods at the same time? So many questions, all of which are very important, and with a little understanding of your process, they will guide you to best method(s) to use.
Hazardous-area protection method selection depends on three important factors: (1) area classification, (2) the application and (3) the cost of the protection method solution.
Area. Area classification depends on the type of hazardous substances used, operating temperature, and explosion risk due to how often the dangerous substance is present in the atmosphere and the boundary of the substance from various parts of the process. Area classification is determined by either the division method or zone method.
Application. Application characteristics also affect which protection method is used. For example, some methods are more appropriate for large equipment protection, while others are more appropriate for high-power applications.
Cost. Cost is also an important factor for many engineers. For example, if their application requires Division 2 protection, they may not want to purchase more expensive equipment rated for Division 1. For that reason, it is important to understand the interplay of all three factors — classification, application, and cost — in helping users find the ideal solution to match their needs.
In addition to considering the normal functioning of the apparatus, eventual malfunctioning of the apparatus due to faulty components must be a consideration. And finally, all those conditions that can accidentally occur, such as a short circuit, open circuit, grounding and erroneous wiring of the connecting cables, must be evaluated. The choice of a specific protection method depends on the degree of safety needed for the type of hazardous location considered in such a way as to have the lowest probable degree of an eventual simultaneous presence of an adequate energy source and a dangerous concentration level of an air/gas mixture.
None of the protection methods can provide absolute certainty of preventing an explosion. Statistically, the probabilities are so low that not even one incident of an explosion has been verified when a standardized protection method has been properly installed and maintained.
The first precaution is to avoid placing electrical apparatus in hazardous locations. When designing a plant or factory, this factor needs to be considered. Only when there is no alternative should this application be allowed.
Choosing the best method
After carefully considering the above, we can look at three more popular methods of protection, XP (explosion proof/flameproof), purging and pressurization, and intrinsic safety. Although these are the most commonly used methods in the division area classification, there are many other options when an area is classified using zones, but for now we will concentrate on the above as they are most commonly used.
XP. The explosion-proof protection method is the only one based on the explosion-containment concept. In this case, the energy source is permitted to come in contact with the dangerous air/gas mixture. Consequently, the explosion is allowed to take place, but it must remain confined in an enclosure built to resist the excess pressure created by an internal explosion, thus impeding the propagation to the surrounding atmosphere.
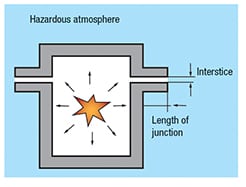
FIGURE 3. Explosion-proof protection is based on the explosion-containment concept, whereby the enclosure is built to resist the excess pressure created by an internal explosion
The theory supporting this method is that the resultant gas jet coming from the enclosure is cooled rapidly through the enclosure’s heat conduction and the expansion and dilution of the hot gas in the colder external atmosphere. This is only possible if the enclosure openings or interstices have sufficiently small dimensions (Figure 3).
In North America, a flameproof enclosure (in accordance with IEC) is, as a rule, equated with the “flameproof” designation. In both considerations, the housing must be designed for a x1.5 explosion overpressure. The North American version Explosion proof (XP) must withstand a maximum explosion overpressure of x4.
Furthermore, in North America, the installation regulations (NEC 500) specify the use of metal conduit for the field wiring installation. It is also assumed here that the air-gas mixture can also be present within the conduit system. Therefore, the resulting explosion pressures must be taken into consideration. The conduit connections must be constructed according to specification and sealed (that is, lead seals) with appropriate casting compound. The housing is not constructed gas-tight. Of course, large openings are not permitted on the enclosure, but small ones are inevitable at any junction point. Some of these gaps may serve as pressure relief points. Escaping hot gases are cooled to the extent that they cannot ignite the potentially explosive atmosphere outside the housing. Ignition is prevented if the minimum temperature and minimum ignition energy of the surrounding potentially explosive atmosphere is not reached. For this reason, the maximum opening allowed for a particular type of joint depends on the nature of the explosive mixture and width of the adjoining surfaces (joint length).
The classification of a flameproof enclosure is based on the gas group and the maximum surface temperature which must be lower than the ignition temperature of the gas present.
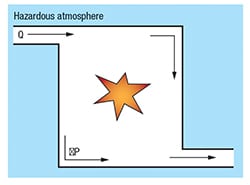
FIGURE 4. In purging or pressurization protection, a dangerous air/gas mixtures is not allowd to penetrate the enclosure containing the electrical parts that can generate sparks or dangerous temperatures
Purging or pressurization. Purging or pressurization is a protection method based on the segregation concept. This method does not allow the dangerous air/gas mixture to penetrate the enclosure containing electrical parts that can generate sparks or dangerous temperatures. A protective gas — air or inert gas — is contained inside the enclosure with a pressure slightly greater than the one of the external atmosphere (Figure 4).
The internal overpressure remains constant with or without a continuous flow of the protective gas. The enclosure must have a certain degree of tightness; however, there are no particular mechanical requirements because the pressure supported is not very high.
To avoid pressure loss, the protective gas supply must be able to compensate during operation for enclosure leakage and access by personnel where allowed (the use of two interlocked doors is the classical solution). Because it is possible for the explosive atmosphere to remain inside the enclosure after the pressurization system has been turned off, it is necessary to expel the remaining gas by circulating a certain quantity of protective gas before restarting the electrical equipment.
The classification of the electrical apparatus must be based on the maximum external surface temperature of the enclosure, or the maximum surface temperature of the internal circuits that are protected with another protection method and that remain powered even when the protective gas supply is interrupted.
The purging or pressurization technique is not dependent upon the classification of the gas. Rather, the enclosure is maintained at a pressure higher than the dangerous external atmosphere, preventing the flammable mixture from coming in contact with the electrical components and hot surfaces inside.
In the U.S., the term pressurization is limited to Class II applications. This is the technique of supplying an enclosure with clean air or an inert gas, with or without continuous flow, at sufficient pressure to prevent the entrance of combustible dusts. Internationally, the term pressurization refers to a purging technique for Zones 1 and 2.
The divisional model of the purging protection method is based on the reduction of the classification inside the enclosure to a lower level. The following three types of protection (X, Y, and Z) are identified in relation to the hazardous-location classification and the nature of the apparatus.
- Type X: reduces the inside of the enclosure from Division 1 to a non-hazardous state that requires an automatic shutdown of the system in case of pressure loss
- Type Y: reduces the inside of the enclosure from Division 1 to Division 2
- Type Z: reduces the inside of the enclosure from Division 1 to a non-hazardous state, requiring alarm signals only
Intrinsic safety. Finally, intrinsic safety is based on the principle of preventing an effective source of ignition. The electrical energy is kept below the minimum ignition energy required for each hazardous area (Figure 5).
The intrinsic safety level of an electrical circuit is achieved by limiting current, voltage, power and temperature; therefore, intrinsic safety is limited to circuits that have relatively low levels of power. Of critical importance are the stored amounts of energy in circuits in the form of capacitance and inductance. These energy storage elements must be limited based on the voltage and current levels present in a particular circuit or make-break component.
In normal operation and in the event of a fault, no sparks or thermal effects may occur that could lead to the ignition of a potentially explosive atmosphere. Intrinsically safe circuits may therefore be connected and disconnected by experts during operation (even when live), as they are guaranteed to be safe in the event of a short circuit or disconnection.
Intrinsic safety is the only ignition-protection class that allows connectors to be opened and intrinsically safe apparatus to be removed and replaced by an equivalent device in a hazardous area. Because of the level of freedom this brings, intrinsic safety has become one of the most important methods of protection in the industrial automation industry.
Final remarks
Each method offers its own advantages and disadvantages, and in most cases no one method will be or can be the only method used in a process plant. Generally, this mixed system does not present installation difficulty if each of the protection methods is appropriately used and is in compliance with the respective standards.
No matter how you classify your plant or which method of protection you chose, it is always important to remember that the method you choose today may not necessarily be the appropriate choice tomorrow. Evaluate, choose and protect not only to keep your plant safe, but to keep your personnel safer.
Edited by Gerald Ondrey
Author
Robert Schosker is the product manager/team lead for intrinsic safety (IS), remote I/O, HART, signal conditioners, power supplies and surge protection at Pepperl+Fuchs Inc. (1600 Enterprise Parkway, Twinsburg, OH 44087; Phone: 330-425-3555; Fax: 330-425-4607; email: [email protected]). Since joining the company in 1995, Schosker has been focused on technology and product-related support, and is involved in a wide range of activities and roles including certifications, sales, and marketing. He has been the key lead in many IS and HART projects resulting in the development of new products for intrinsic safety and HART infrastructure. Schosker holds a B.S.E.E. from the University of Akron.