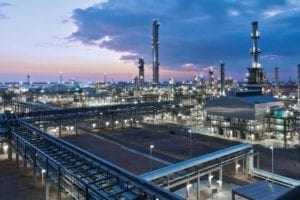
Propylene/polypropylene comples in Egypt (Source: thyssenkrupp)
Thyssenkrupp Industrial SolutionsAG (Essen, Germany) and BASF SE (Ludwigshafen, Germany) have signed a joint development agreement to expand their cooperation on the STAR process. This proprietary dehydrogenation process from thyssenkrupp produces propylene from propane feedstocks, or isobutylene from isobutane feedstocks, using an exceptionally stable catalyst. thyssenkrupp, focusing on process development, and BASF, focusing on catalyst development, together aim to significantly increase the resource and energy efficiency of the process through targeted improvements in catalyst and plant design. Plant operators can benefit from lower investment and operating costs as well as lower CO2 emissions in the future.
“We are very pleased about this cooperation which combines BASF’s expertise as a world-leading catalyst manufacturer with our plant engineering competence,” says Uwe Boltersdorf, chief sales officer of the business unit Chemical & Process Technologies at thyssenkrupp. “With our combined know-how we can further reduce consumption of energy and resources. New catalyst shapes will enable a smaller reformer design, which also lowers the investment costs of dehydrogenation plants.”
Detlef Ruff, senior vice president Process Catalysts at BASF, says: “The cooperation between BASF and thyssenkrupp is another example of our successful approach to collaboration with engineering companies and technology providers. We contribute our unique know-how as a world-leading catalyst manufacturer, and together with our partners, drive the implementation of new processes and innovative future technologies.”
“This project is a good example of how technology development can be accelerated through cross-sector collaboration,” says Adrian Steinmetz, vice president Global Chemical Catalysts & Adsorbents at BASF. “We will specifically address topics like reducing precious metal content. This lowers catalyst costs and additionally reduces feedstock and energy consumption through increased selectivity. This will contribute significantly to a reduction of the CO2 footprint.”
Propylene is one of the largest volume chemicals produced globally with projected further growth. A common use is as raw material for polypropylene, a component that is mainly used in the automotive, textile and packaging industries. Thyssenkrupp’s Steam Active Reforming STAR process offers an extremely reliable process with a proven plant availability of 98%, which means more than 8,500 hours per year.