The integrity of pipelines, valves, vessels and other components made from carbon steel and other metal alloys depends on the material composition being exactly the same as specified, since excessive levels of trace elements, such as chromium, copper, nickel, molybdenum, vanadium, lead and others can impact material strength, hardness and corrosion resistance. As a result, “residual element analysis is a major concern in both installed and newly purchased materials,” says Peter Faulkner, regional sales manager at Thermo Scientific Niton Analyzers (Booth 736; Billerica, Mass.).
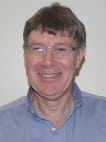
“We’ve all seen the horrific industrial accidents that can happen when material failure and explosions occur because of improper material specification,” he says, adding: “The specific content of metal alloys must be verified not just at the manufacturing facility, but at the user’s site, too (both at the warehouse for new components, and at the point of use for components already in service).”
Today, easy-to-use, handheld tools, based on non-destructive X-ray fluorescence (XRF) are available to capture and store data to verify trace amounts of unwanted constituents in metal alloys. Faulkner will be presenting a hands-on workshop, entitled “Alloy Grade Verification Made Simple” ( Tuesday, November 17, 11:00 a.m. in Theater A), during which he will encourage attendees to use a range of devices to conduct blind testing on a variety of alloy samples.
In an XRF analyzer, a miniature X-ray tube or radioactive isotope excites the material for inspection, and a high-resolution detector provides fast analytical chemistry results, which are then automatically compared with an onboard library of material composition signatures. The results are archived and electronic position indicators allow such readings to be tagged and recorded to an exact location within the facility.
One of the latest models Faulkner will be discussing, the Niton XL3 900 GOLDD (Geometrically Optimized Large Area Drift Detector), provides light element detection without helium or vacuum purging. It is able to detect tramp elements, such as chromium, copper and nickel at levels of 0.02% and below to ensure that they are present below a desired maximum threshold. This is important, says Faulkner, because the presence of these three elements at combined levels greater than 0.2% has been blamed for corrosion-related failures in HF alkylation plants in the past.
Such tools are also important to help users comply with requirements of the National Emphasis Program (NEP) for Process Safety Management (PSM) for Highly Hazardous Chemicals from the U.S. Occupational Safety and Health Administration (OSHA; Washington, D.C.), and API 570 (piping-inspection codes), API 510 (pressure-vessel code), and API RP-578 (material-verification program) from the American Petroleum Institute (Washington, D.C.).
“These devices allow users to get a reading in under 10 seconds,” says Faulkner. “Ease-of-use and near-instantaneous feedback are key for many industrial settings where the reading must be taken by a worker who is literally perched on scaffolding. The easier we make it for the operator, the better.”
Suzanne Shelley