Concise tips on selecting the right valve
A typical chemical plant contains miles of piping and hundreds, if not thousands, of industrial valves (Figure 1) that are essential for the plant to operate efficiently and safely. Unlike the simple consumer valves that are used to regulate water flow in your sink, shower or bathtub, industrial valves for chemical plants must be designed, manufactured, tested and maintained for reliable operation in rugged applications. For many applications, valves installed in chemical plants must be of the “severe service,” high-performance type.
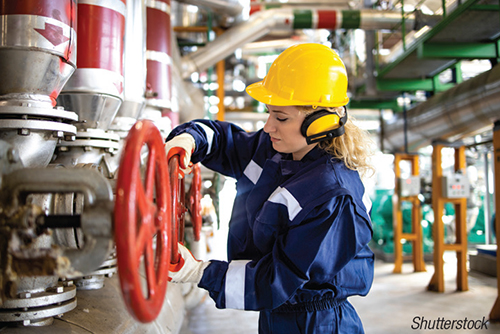
FIGURE 1. A typical plant in the chemical process industries will have hundreds of valves
Chemical plants are hostile environments with many kinds of hazardous acids, corrosive media and extreme pressures and temperatures. Reliable valves are essential to isolate equipment, control the flow of process liquids and gases, and provide reliable venting, draining and over-pressure protection.
Valves play a major role in assuring the safety of property, personnel and the public by preventing or minimizing harmful leaks, fires and, in extreme cases, explosions. Specifiers of valves for chemical plants have a serious responsibility to make sure that they select the right valve for the right application. The negative consequences of mistakes or errors in calculations can be serious and hugely expensive.
Cost considerations
In new construction, it is essential to avoid the temptation to specify lower-cost valves because the downside can be significant. The initial cost may be lower, but as time goes by, plant operators will pay a price (total cost of ownership) in terms of shorter life cycle, leakage, forced shutdowns, repairs, replacements and potential accidents.
The price differential between a low-cost valve and a quality valve may be as much as 25–40%, which may seem like a lot percentage-wise, but in real dollars, it is not. For example, if you have a choice between a $1,000 high-quality valve and a $600 low-cost valve, the savings achieved by installing a low-cost valve appear to be $400. Compare that with the cost of prematurely replacing a low-cost valve with a higher-quality valve. If you add up the replacement valve cost, labor cost, welding, post-weld heat treatment (PWHT) and non-destructive evaluation (NDE) costs and shutdown cost, just one valve replacement can easily cost $10,000 or more.
Part of the problem is that the engineering, procurement and construction (EPC) company that saves the $400 on the front end is typically not responsible for the resulting $10,000 expense incurred by the plant owner/operator during plant operation. When viewed from this perspective, installing the valve that provides the best value the first time serves the best interests of all entities involved.
Another problem with installing low cost valves on the front end is that these suppliers may not have a defined presence in supplying for maintenance, repair and overhaul (MRO) opportunities.
For most applications, any valve will eventually require repair or replacement. Therefore, it makes sense to specify quality valves that are easy and economical to inspect, repair or replace. Wherever possible, in-line serviceability is a significant advantage because you do not have to cut and re-weld connecting piping.
Since an increasing number of valves are being actuated and integrated into distributed control systems (DCS) to enhance real-time plant monitoring and improve plant efficiency, specifying longer-life, higher-quality valves will maximize the plant operator’s investment in these expensive, networked systems.
The valve selection process
When assessing which valves are best for each operation in a chemical plant, there are no quick short-cuts. You need to spend an appropriate amount of “think time,” aided by state-of-the-art software and computerized simulations, to make sure that every step in the controlled flow of liquids and gases is fully understood and taken into account.
Questions to ask. Key factors to consider can be addressed by asking the following questions:
- Can the valve “go with the flow?” Can the valve accurately and reliably handle the flowrate (Cv)?
- Is the valve in-line repairable?
- Are the materials of construction suitable for the intended application as a function of mitigating the effects of a corrosive media and fluids containing particulate matter that are abrasive (erosion)?
- Is the valve manufacturer and its sales channel active in supporting your plant once the valve is installed?
- Can the valve provide reliable, tight, leak-free shut-off at the intended pressures?
- Is the valve “pressure sensitive?” Has it been designed and properly specified to handle the pressures and temperatures for the applications in which it will be installed? (“Tight is might”)
- Can the valve be delivered to meet plant need dates?
- Does the valve meet applicable codes and standards imposed by federal, state, province or other jurisdictional requirements?
Pick the brains of manufacturers. As you evaluate your valve needs, don’t forget to tap into the wisdom and experience of established, reputable severe-service valve manufacturers and their authorized representatives. They have a wealth of understanding and knowledge that you can leverage to help you to make the wisest valve specification decisions.
Always adhere to standards. In all cases, careful specification of valves that meet applicable codes and standards is required. Determination that your valve supplier can meet these standards can be made by review of their catalog information, their websites or by audit. Note that these criteria can differ from state to state, province to province or nation to nation, so you will need to determine applicability accordingly. Common codes and standards include those published by the American Society of Mechanical Engineers (ASME), the American Petroleum Institute (API), the Manufacturers Standardization Society (MSS), the International Organization for Standardization (ISO), ASTM International, the American National Standards Institute (ANSI), the American Waterworks Association (AWWA) and the Instrument Society of America (ISA).
An example
Over a number of years, experience has revealed that, sometimes individually and sometimes working in tandem, misapplication or purchasing based on price versus required design features can provide poor results for valves in severe-service applications. This can happen both at the project purchasing level, as well as the MRO purchasing level.
A recent example involved a plant owner employing carbon dioxide sequestration in the manufacturing process. This plant was experiencing premature seat leakage, resulting in solidification of the process media, loss of CO2 and subsequent shutdown of the line, significantly impacting both cost and schedule. In some instances, this occurred only weeks after the original valve was installed. Working with a more experienced valve manufacturer, the root cause was determined and the valves were replaced with suitable alternatives that eliminated the problem. These valves have now been working for almost two years without a failure, and the owner has replaced all the original valves, resulting in significant savings in repairs, replacement valves/parts, and process downtime.
Final remarks
The reality of project purchasing, where an owner selects an EPC organization based on a fixed price estimate that the EPC submits for a scope of work (for example, a power plant) can result in the potential that the owner will have to deal with products that the EPC supplies that only marginally meet specification requirements. Because of this, the competitive nature of the bidding process drives a procurement philosophy of purchasing products that will “get them through the warranty period.” This can be mitigated somewhat by owner-driven approved suppliers lists and strong specifications reinforcing design requirements.
Valves are indeed some of the key “workhorses” in our industrial plants. Just as you would not harness a thoroughbred to a heavy cart or expect a plow horse to win a race around an oval track, you would not install a valve in an application for which it was not well suited.
Author
Don Bowers is the vice president of Conval, Inc. (96 Phoenix Avenue, Enfield, CT 06082; Email: dbowers@conval.com. Phone: 860-749-0761; Website: www.conval.com), a manufacturer of severe service valves for demanding industrial applications. Bowers’ experience and knowledge base spans four decades in the thermal-power and severe-service valve industry. His career has included positions at Graver Energy Systems, Bechtel Power, Crane, Velan, Weir and Conval. He is a member of ASME; chairman of the ASME Standards Committee IX; a member of ASME SCIX’s Subgroup General Requirements and Subgroup Welding Qualifications; and past chairman and member of the National Board Inspection Code’s Subcommittee on Overpressure Protection (NBIC-SCOP). He also serves on the Valve Manufacturers Association’s Valve Magazine Editorial Review Board.