The COVID-19 threat has increased the urgency for implementing contagion-prevention strategies and controls for workers at industrial sites
Chemical process industries (CPI) companies are used to managing a range of worker health risks related to chemical exposure, extreme temperatures and noise, among others, but the global coronavirus pandemic has forced CPI facilities to elevate a broad set of infectious disease considerations to prominence among other process safety priorities. To reduce infection risk in industrial workspaces, companies are enhancing disinfection protocols, increasing use of respiratory personal protective equipment (PPE), implementing physical distancing at jobsites, relying on remote work, and other strategies. Industry consultants have provided some guidance for companies to use as they operate in the midst of a pandemic. Meanwhile, vendors and equipment providers have responded by introducing products to help reduce contagion risk in various scenarios.
Theresa McCollom, a certified industrial hygienist and environmental, health and safety consultant at the U.S. headquarters of Antea Group (St. Paul, Minn.; us.anteagroup.com) says that while the pandemic has impacted the chemical process industries unevenly — petroleum refining has seen reduced demand, for example, while chemical plants making ingredients for disinfectant formulations have seen a surge in demand — most companies and plant sites are taking whatever actions they can when it comes to preventing workplace infections. “Most employers in the industrial space are doing some sort of health screening, either asking questions for workers to self-report, or using thermal thermometers,” McCollom says, and “most sites are doing some sort of workplace reconfiguration, where it is possible, such as putting up barriers, as well as cleaning high-touch areas.”
Eastman Chemical Co. (Kingsport, Tenn.; www.eastman.com) senior vice president and chief manufacturing, engineering and supply chain officer Mark Cox confirms that there has been a sudden emergence of safety efforts focused on COVID-19 prevention at Eastman facilities. “We work with a zero-incident mindset in everything that we do, and this pandemic has been no different. We are doing all we can to keep our teams safe and healthy while still continuing to produce the critical products our customers need — many of which have been important in the battle against this virus.”
To help companies protect workers in the face of public health threats, there are many new product offerings available from simple to complex, and targeting a variety of public health risks. McCollom says many of her clients are looking for evaluations of new products. “They are asking: Is this ‘snake oil?’; Will this be effective?” she says. “Although there are many products that can help reduce public health risks, there are not really any ‘miracle widgets’ that can make the risks go away,” McCollom says. “If product claims appear too good to be true, they most likely are.”
Hazard exposure tools
For CPI sites, pandemic-related risks must be placed into a wider context of risk management. American Industrial Hygiene Association (AIHA; Fairfax, Va.; www.aiha.org) board member Nancy McClellan, the CEO of Occupational Health Management PLLC (Detroit, Mich.; www.oh-management.org), says “whether the hazard is chemical, physical or biological, hazard exposure and control banding (HECB) can assist organizations in wrapping their arms around the challenges of the hazard by identifying the highest risks and prioritizing the most appropriate solutions.” HECB tools can also provide key performance indices to measure an organization’s progress in mitigating the hazards, she notes.
To explain HECB in the context of COVID-19, McClellan says “In the case of a biological hazard, one needs to identify all of the relevant factors involved in risk. Since risk equals the likelihood of incidence multiplied by the severity of the hazard, we need to drill down to all of the factors influencing ‘likelihood’ and ‘severity.’” Likelihood of exposure to COVID-19 can include social distancing practices, building operations and cleaning practices. Severity of the hazard depends on factors that can include age and comorbidities of the individuals, she continues. “Once these factors are identified, assigned a risk level and mathematically weighted, risk scores can then be calculated. The risk score then directs the HECB tool user toward potential solutions or controls for mitigating the hazard.”
As an organization’s risk scores are reduced with proven solutions, the tracking of the scores from year to year can clearly illustrate progress in risk mitigation, she adds.
At industrial plants, there is now “more of a three-way conversation among industrial health and safety officers, engineers and ‘C-suite’ leaders about how to allocate resources to where they will have the largest impact,” McClellan says.
AIHA is among a number of industry associations and consulting firms that have issued guidance that is relevant to operating in chemical manufacturing plants with an added focus on public health safety. The AIHA has compiled a series of industry-specific plans for making workplaces as safe as possible. Other organizations that have come out with industrial workplace guidance include PPE supplier Protective Industrial Products Inc. (Latham, N.Y.; www.pipglobal.com), which has released the “PIP Essentials Safety Book,” and business consulting giant McKinsey & Co. (New York, N.Y.; www.mckinsey.com), which published the article “Managing a Manufacturing Plant through the Coronavirus” online.
Workplace reconfiguration
One main pillar in the fight against COVID-19, in all settings, is maintaining physical separation among workers to reduce exposure to infectious particles. There are multiple strategies to achieve this including altering team structures and working methods to limit contact across the workforce. The McKinsey guidance states: “Minimizing the potential future impact of infections will require companies to alter team structures and working methods in order to limit contact across the workforce. One way this can be done is by establishing ‘pods’ for all on-site personnel, organized for self-contained teams with clearly defined tasks and workspaces that can be physically and socially separated from each other as much as possible.”
Eastman, for example, is adapting this concept for its own sites. Cox says shift schedules at the company sites were changed to minimize the interaction between production crews and have minimized contact between production staff and others by restricting access to control rooms, for example, to only those needed for critical operations. The company has also used remote work where possible and works with employees to understand travel outside of the areas where they live and operate to reduce the spread of the virus upon return.
Mentioning another separation strategy, Dean Alcott, market development manager at RedGuard USA (Wichita, Kan.; www.redguard.com), says modular buildings, such as those offered by his company, can allow a quick and safe space to increase separation among workers. “Not only can we provide safe space close to the process hazards, but we can arrange it as needed for separation,” Alcott says. “We also provide non-blast buildings, known as a SiteBox, that can be quickly available and are very flexible, allowing workers to spread out on job sites.”
Connected technologies
Social distancing strategies can also be supported with modern industrial internet of things (IIoT) technologies. EmbedTek LLC (Waukesha, Wis.; www.parirange.com) has introduced PariRange, a peer-to-peer social distancing and contact-tracing device.
Employees wear the PariRange device, which monitors the distance from other devices. Ultra-wideband and time-of-flight technology measure distance between devices with a rated accuracy of four inches. When an employee comes within six feet of another device, PariRange sends a vibration alert. Date and duration of close contacts are recorded whenever multiple devices come within the 6-ft range. Each day, the duration of close contact a user’s device has with other devices is aggregated and stored for 14–28 days. Data are easily viewed through a PariRange Log Reader, which can be connected to a computer via USB, or placed throughout a facility to pull data from employee devices automatically as they walk by.
If an illness occurs, the device can identify employees who have had close contact with the infected individual. This allows businesses to take action quickly and follow recommended protocols to curtail infection spread, the company says.
With the pandemic causing many plant employees to need or want to work from home, there is an increased need to get timely safety diagnostic information remotely. Fire and gas safety system provider Det-Tronics (Minneapolis, Minn; det-tronics.com) offers an example of this. Det-Tronics systems product manager William Crosley says “Because travel and onsite field visit restrictions have limited the number of people on plant sites, integrating the process control and life safety systems can be critical. A certified, documented fire and gas safety system that can communicate appropriate messages to the process control and emergency shut-down systems enables the plant to monitor both systems’ parameters simultaneously through fixed and remote operator stations. When integrated with the process control system, our Eagle Quantum Premier fire and gas safety system can provide continuous real-time status of its flame and gas detection devices, as well as the suppression system.”
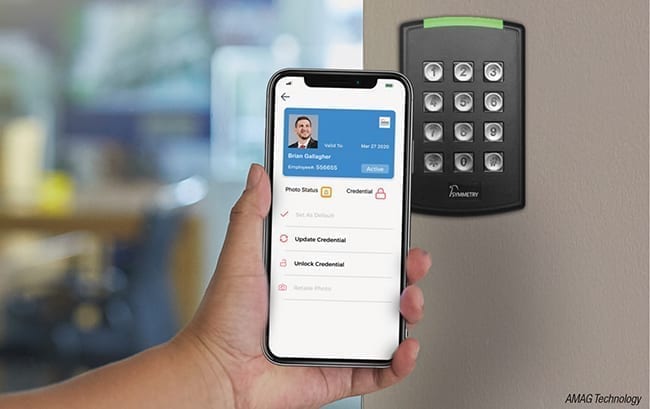
Figure 1. The Symmetry Mobile product for access management allows users to credential visitors and workers for access to various areas in a way that does not require any in-person contact
Access management and health
Access to industrial sites has always been a priority from a security perspective, but the public-health concerns have added a new dimension. A new technology product that is addressing this area is Symmetry Mobile (Figure 1), a product developed by AMAG Technology Inc. (Hawthorne, Calif.; www.amag.com). Symmetry Mobile is an internet application that lets its users credential visitors without necessitating any in-person contact. It provides full central control over credentials, photos, devices and configuration all from the app, including multi-factor authentication.
“By using a smartphone instead of access cards, a site can eliminate the need to visit a badging office and stand in line to physically interact with security staff,” explains AMAG product director Jonathan Moore.
AMAG provides both software and hardware for the system, which can manage access to various areas of a plant site to visitors, Moore says. Symmetry Mobile allows central management of the credentials, photos and devices remotely.
Adding another dimension to access-management systems are recently launched products that can support building entry with health screening systems that can detect elevated body temperatures. Among them is the Siveillance Thermal Shield (Figure 2) from Siemens AG (Munich, Germany; www.siemens.com). This package quickly measures the body temperature of a person seeking to access a building and enables the results to be integrated into the video and access systems of corporations. Thermal imaging cameras are used to measure, in a contactless way, the body temperature at a distance of up to two meters, ensuring the safety of monitoring staff. If the camera screening indicates an elevated body temperature, a second reading must be taken using a medical thermometer to confirm the finding.
In July, Honeywell Performance Materials and Technologies (Houston; www.honeywell.com) announced a complete, modular software solution to help industrial companies enforce compliance with key health and safety requirements as their employees return to the workplace, including body temperature checks and automated entry management processes.
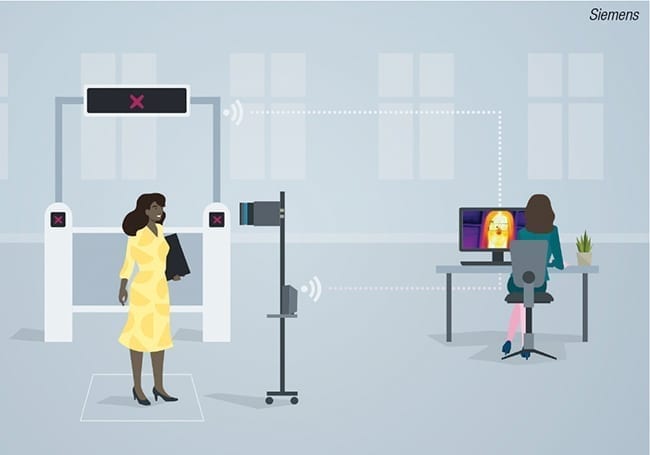
Figure 2. Body temperature of individuals entering buildings can be measured by the Siveillance Thermal Shield
The system leverages the company’s existing digitized workforce platform, and facilitates site monitoring compliance in accordance with social distancing policies. It also enables contact tracing and monitoring of worker safety and includes remote collaboration capabilities to empower company operations with a reduced workforce.
The system can support Honeywell thermal cameras that can be used with systems compliant with NDAA 2019, Section 889 to check for elevated body temperatures and provide input to the access control system. This can enable operators to restrict entryway access if an elevated temperature is detected helping to automate the preliminary screening process and reducing manual tasks, the company says.
FLIR Systems, Inc. (Arlington, Va.; www.flir.com) recently announced the multi-application FLIR A400/A700 Thermal Smart Sensor and Thermal Image Streaming fixed cameras. FLIR designed the A400/A700 cameras with two configurations, one of which is recommended for measuring elevated skin temperatures. It incorporates advanced measurement tools and alarms with edge computing to enable faster critical decisions, FLIR says.
Eastman’s Mark Cox comments that along with social distancing, good hygiene practices, enhanced cleaning protocols and mask wearing, temperature screening has been a part of keeping teams healthy at Eastman facilities.
Respiratory PPE
Since the onset of the pandemic, respiratory PPE has been an important tool for reducing disease spread. Because new cohorts of workers that previously had not used respiratory PPE, such as N-95 respirators (filtering 95% of airborne particles), now required it, the demand for this type of PPE has been surging. Although the industry responded with increased supply this summer, there remains stress on the supply of N-95 masks, especially in the medical sector. Because of this, industrial sites seeking to equip workers with N-95 masks should look at the full range of N-95 respirators, such as re-usable elastomeric respirators, suggests Charles Johnson, president of the International Safety Equipment Association (ISEA; Arlington, Va.; www.safetyequipment.org), a trade association for safety equipment manufacturers. “The medical community remains somewhat hesitant on reusable elastomeric N-95 masks, because, for example, those with exhalation valves cannot be used in most medical settings,” Johnson says, “But these types of respirators can be a viable alternative for use by personnel in industrial settings.” 3M, Honeywell and MSA Safety are among the several manufacturers supplying this type of reusable mask.
HVAC and ventilation
Studies investigating the transmission of the novel coronavirus have pointed to the importance of indoor air ventilation. The Association of ASHRAE Epidemic task force recently developed guidance on mitigating potential health risks during reopening of buildings closed during the COVID-19 pandemic.
“Key elements of a strategy to limit the spread of the COVID-19 virus are to perform needed heating, ventilating and air conditioning (HVAC) system maintenance, including filter changes, and to run HVAC equipment, prior to re-occupancy,” says ASHRAE Epidemic Task Force chair Bill Bahnfleth.
Disinfection
Cleaning in industrial settings has also received renewed focus in the pandemic, and disinfection solutions have become more widely used, especially in high-traffic areas and on high-tough surfaces. Madison Chemical Co. Inc. (Madison, Ind.; www.madchem.com) recently provided research confirming the effects of its 4-chain quaternary surface sanitizer on the novel human coronavirus. Madison Chemical’s Brad Sims says MADISAN 75 disinfectant, mildewstat, and virucide for hard, non-porous, and inanimate surfaces is ideal for a wide variety of installations, including industrial and manufacturing environments.
When companies want to detect and limit the number of people in a given area, they may also desire an alarm system that can alert them when a limit is reached. Alarm LED lights such as those from Pfannenberg USA (Lancaster, N.Y.; www.pfannenbergusa.com) can provide this type of support. Pfannenberg recently introduced a color-changing light-emitting diode (LED) alert light that consist of a single light with a wider voltage range designed to replace stack lights. The Pyra-S LED lights can be integrated with audible signals so that personnel can be alerted when a limit is exceeded, Pfannenberg product manager Jake Vernon says.