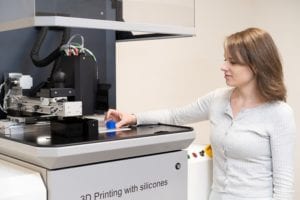
Wacker Chemie
Wacker Chemie AG (Munich, Germany; www.wacker.com) is launching its first U.S. based ACEO Open Print Lab. The new facility, located at Wacker’s Silicone R&D facility in Ann Arbor, Mich., is equipped with 3-D printers able to process a broad range of silicone rubber with different Shore A hardnesses and in varying colors. Following the success of Wacker’s ACEO Open Print Lab in Burghausen, Germany, and the high demand for additive manufacturing solutions in North America, the print lab will offer first-hand tutorials and hands-on training allowing customers to experience 3-D printing with silicone rubber.
“We are pleased to announce another milestone in ACEO’s history with the launch of the Open Print Lab in Ann Arbor,” says Dr. Bernd Pachaly, head of Project 3-D Printing at Wacker Silicones. “North America is one of the leading markets in additive manufacturing. Our new facility brings 3-D printing with silicones much closer to potential customers in the region.” In 2017, Wacker set up its first ACEO Open Print Lab in Burghausen. It helps customers understand how 3D printing with silicones matches their needs by offering first-hand experience.
Wacker introduced the world’s first 3-D printing web shop in 2016 ( for more details, see Chem. Eng., May 2016, p. 7; https://www.chemengonline.com/making-complex-silicone-parts-3-d-printing), making ACEO technology and services available to customers worldwide. However, education about a pioneering technology such as ACEO needs a local presence. “Our business partners in the region want to understand how their ideas and products can be brought to market with our support. Wacker’s Silicone R&D Center in Ann Arbor was designed to develop advanced and forward-looking solutions for silicones. With the new Open Print Lab we can significantly expand our local portfolio and contribute to the growing demand of the market,” says Ian Moore, vice president Wacker Silicones at Wacker Chemical Corp. in Adrian.
The new Open Print Lab is headed by Lab Manager Sarah Burke, who previously worked at the Silicones R&D Center in fundamental product research for construction applications and consumer care. The lab will be equipped with two 3-D printers, each of which will be able to process a broad range of silicone rubber with different Shore A hardnesses and in varying colors. ACEO’s unique additive manufacturing technology for silicone elastomers enables unprecedented product designs and complex geometries for rapid prototyping purposes. It is also suitable for serial manufacturing and cost-efficient production of replacement parts.
The ACEO team will also offer workshops open to small groups of up to four people. After signing up, customers and the team will be able to define dates, expectations and goals of the workshop. Participants will go through personalized trainings, consisting of theoretical and printing sessions from additive manufacturing basics to advanced design.
Interested parties such as existing and prospective Wacker customers can register for a tailor-made Open Print Lab training at the ACEO Campus in Ann Arbor, MI, at www.aceo3d.com/open-print-lab. Workshop fees will depend on the number of participants and contents.
Wacker’s 3-D printing technology ACEO is the world’s first industrial-scale technology for the additive manufacturing of liquid silicone rubber components. The unique drop-on-demand technology allows design freedom and the printing of highly functional parts while maintaining the outstanding properties of silicone rubber such as temperature and radiation resistance or biocompatibility. Printed silicone rubber components can be used in a wide range of applications and in several key industries such as the automotive, aerospace & aviation, healthcare and equipment industry as well as in mechanical engineering.