Although in many places in the world, freshwater is still viewed as a commodity, a paradigm shift of thinking has begun where water is increasingly considered a critical resource. This shift in mindset is accelerated when water stress rises. Available freshwater supplies can be limited in quantity or in quality for meeting the increasing demands of population growth and industry expansion [1]. In many arid and semi-arid regions, producing large volumes of freshwater is especially difficult. There is no doubt that water is precious, and its scarcity is emerging as one of the most serious natural-resource issues facing the world today. Water is directly related to health, safety and economy.
The chemical process industries (CPI) — important consumers of fresh water — can ease water stress by improving water use processes, and by using alternative water sources. The worldwide community of professional chemical engineers are playing, and will continue to play, a key role in sustainable industrial water use.
This article highlights various strategies that can be used in small-, medium- and large-scale chemical facilities to reduce raw water usage, and ways in which these methods can be adopted.
Reuse, reduce, resource
There are many ways to effectively reduce water consumption, and they can be categorized in the following way (Figure 1):
Reduce: Reductions in water consumption can be accomplished by making changes in the process design and equipment selection. For example, by maximizing air coolers, thereby reducing the cooling-water requirement
Resource: Find additional ways to source fresh water. Rainwater harvesting can be an excellent opportunity
Reuse: Utilize wastewater from one process unit as source water for another, or reuse water after treatment. For example, boiler blowdown can be put into the cooling-water circuit after little or no treatment
An important point to note is that the volume, quality, composition and importance of water in a particular industry segment varies. For instance, the paper industry requires large volumes of water, and it has different specifications depending on which unit operation is using the water. It is also important to realize that water quality requirements for different uses can be radically different. The quality requirements for water makeup, for firewater makeup or for utility water are less stringent than those for cooling-water makeup, boiler feedwater or process water makeup.
These variations in quality and quantity make it impossible to establish a single general water-management strategy that is applicable in all situations — there is no one “silver bullet” solution.
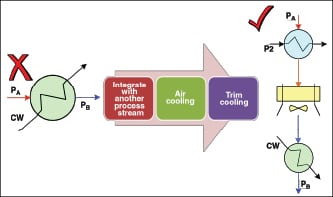
Reduce strategy
Here are some ideas to reduce water usage that are worthy of consideration (Figure 2):
1) Replace cooling-water duty by exchanging heat with another process stream. A pinch analysis will quickly realize maximum opportunities to exchange heat with other process streams.
2) Replace cooling-water duty with air cooling. The disadvantage is that the air coolers occupy more space and are more expensive. Modularization can mitigate the space constraints significantly.
3) Replace once-through cooling-water systems with closed cooling-water systems. In modern plants, closed cooling-water systems are the norm, but even they have make up for losses due to blowdown, evaporation and drift.
4) Replace the cooling tower for cooling duty with a heat exchanger and a once-through cooling-water system acting as a heat sink. At first glance, this would appear to be inefficient and expensive, but the advantages are that one can use seawater as a heat sink, coupled to a closed cooling-water system. The materials of construction for the process exchanges are no longer governed by the seawater quality, significantly lowering the cost of these exchangers. The pressure on using freshwater (or cooling water makeup-quality water) is lowered significantly.
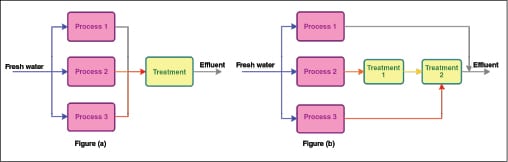
A combination of strategies 3 and 4, coupled with process changes, can totally eliminate the requirement of freshwater for cooling-water duty, at least.
5) Replace steam used for heating with electric heaters or direct-fired heaters. Although steam generation is the least expensive method for providing process heat, if the cost of sourcing freshwater or disposing of wastewater becomes prohibitive, then substituting electric or direct-fired heaters can be leveraged effectively.
6) Reduce water used for hose-cleaning spillages in the plant by increasing the velocity of the water used for cleaning. Particulates, dirt and oil can be loosened at a faster rate, which allows the length of rinse cycles to be shortened, saving water [4].

7) Instead of hosing the spillage area, first sweep up any spillages and washdown only when essential. This will not only reduce water use, but also reduce the concentration of contaminants entering the drain, because more of the waste can be disposed of as a solid.
8) In general, try to minimize the routing of water to the wastewater-treatment facility. This may include avoiding sending water-tank overflows or stormwater to sewers, if no extensive treatment is required.
Similarly, wastewater requiring extensive treatment should be segregated from water that requires only simple or conventional treatment methods. This reduces the load on the facility, which in turn reduces chemical consumption, power consumption, area footprint and water footprint.
9) Reduce potable water consumption by controlling waste with high-end fittings and by controlling supplies.
Resource strategy
Harvesting new sources of freshwater can come in many forms. The following are several ideas:
1) A common solution which can make sense in countries such as India, is rainwater harvesting. If rainwater can be collected and used as freshwater makeup, it reduces pressure on freshwater. Many industrial examples exist.
An obvious, but under-recognized advantage of using harvested rainwater is that it needs minimum treatment to be used as boiler-feed makeup water, which requires superior water quality. Stormwater can easily be used with minimal treatment for firewater makeup, utility water or cooling-water makeup also.
2) Look for nearby industries, or even large, municipal wastewater-treatment plants that generate a wastewater stream, which may be much easier to treat for reuse. Secondary-treated municipal wastewater is generally acceptable for cooling-water makeup, even though it often contains phosphate and ammonia. Its use can be made possible by operating cooling towers at low cycles of concentration and by using pipes and heat exchangers with appropriate materials of construction. The blowdown of such cooling towers can be used in agriculture to take advantage of its high levels of ammonia and phosphate [2]. With tertiary treatment of municipal wastewater, ammonia and phosphate levels can be brought down.
Some water constituents can be beneficial to cooling systems. Nitrates protect against stainless-steel corrosion and phosphate protects against carbon-steel corrosion. Treated municipal wastewater may also contain traces of free chlorine, which controls microbiological fouling [2].
3) In cold climates, thawing snow also can be a useful source for freshwater.
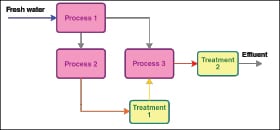
Reuse strategy
While there are several technologies available to minimize water consumption, each solution is unique to a plant and its site. The affordability of water treatment compared to the price of freshwater is a driver for reuse in areas where the two are similar. Water reuse also stabilizes the plant’s water supply, especially in drought-prone areas, and can help make a plant “drought proof” to the extent that it is able to reuse water. It also flattens out influent water quality and buffers the plant against sudden upsets in water supply that might arise, for example, in river water. The benefits to steady operation of water-treatment equipment, and thus to the process, is also significant.
The following items are examples of water reuse strategies:
1) By taking water from some of the cleaner operations, water that is not clean enough to be treated and reused in a cleaner area, can be used in areas that are “dirtier”. The water could be more than “clean enough” to serve its purpose in these areas. Always check the quality of each water source against the demand quality. The goal is then to provide water of required quality. For example, clean effluent from steam stripping of sour water can be used as makeup water for desalters, quench towers and water wash towers. It can also be used in hydraulic coke cutting of a coker drum.
2) In petroleum refineries and chemical plants, cooling-tower makeup water and boiler makeup water represent two of the significant freshwater users that have specific water-quality constraints. Significant water savings can result through the additional mild treatment of the environmentally acceptable wastewater treatment plant (WWTP) effluent as cooling-tower makeup water, or through further deep treatment as boiler makeup water (desalted water).
Reverse osmosis (RO) reject water contains high levels of dissolved solids, which makes it generally unsuitable for total replacement. However, it can replace a portion of makeup water with only a minor impact on water quality. If the RO feed has an upstream softening step, then the RO reject water will have little or no hardness, and hence less potential to cause scaling in the cooling-water system [2].
3) Boiler blowdown, with minimal treatment can also replace a portion of makeup water. An example of blending various water makeups is illustrated in Figure 6.
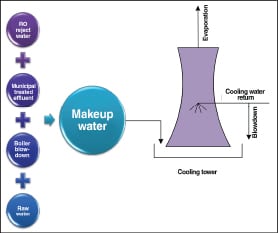
In Table 1, a comparison has been made between the water quality of cooling-water makeup when blended with RO reject water and boiler blowdown (Case 2) and cooling water without blending (Case 1).
Table 1. Replacing part of Fresh Water for Cooling Water (CW) makeup with other water sources | ||||||||
Max limit to be maintained in tower, mg/L | Typical CW makeup quality, mg/L | Cycles of conc. (COC) | Typical RO reject, mg/L | Typical HP boiler blowdown, mg/L | 5% | RO reject | COC | |
10% | Boiler blowdown | |||||||
85% | Freshwater | 3.4 | ||||||
4 | ||||||||
(a) | (b) | (c) | (d) | (e) | (f) | (g) | ||
Total suspended solids (TSS) | 150 | 35 | 140 | – | 2 | 30 | 102 | |
Total alkalinity as CaCO3 | 100 | 400 | – | 150 | 100 | 340 | ||
Total dissolved solids | 2,500 | 500 | 2,000 | 4,500 | 750 | 725 | 2,465 | |
Total hardness as CaCO3 | 500 | 110 | 440 | 20 | 0.1 | 95 | 321 | |
Chlorides | 300 | 70 | 280 | 350 | – | 77 | 262 | |
Sulfates | 50 | 200 | 150 | – | 50 | 170 | ||
Silica as SiO2 | 150 | 30 | 120 | 20 | 5 | 27 | 92 | |
Iron (Fe) | 0.1 | 0.02 | 0.08 | – | 0.02 | 0.019 | 0.0646 | |
Phosphates | 15 | 2 | 8 | 50 | 4.2 | 14 |
Table 2. Water Consumption based on Table 1* | ||
Type of makeup water | ||
100% raw water Case 1 | Blended Case 2 | |
Blowdown, m3/h | 41 | 53 |
Makeup, m3/h | 185 | 197 |
Freshwater usage, m3/h | 185 | 167 |
Wastewater load, m3/h | 71 | 53 |
RO reject reuse, m3/h | 0 | 10 |
Boiler blowdown reuse, m3/h | 0 | 20 |
* Circulating water: 5000 m3/hr, Drift: 0.1%, ∆T: 15°C |
Table 3. Water Savings | ||
Water saved, m3/h | 18 | 10% |
Water saved per year, m3 | 154,956 | |
Wastewater reduction, m3/h | 18 | 25% |
Wastewater reduction per year, m3 | 154,956 |
Table 4. Suitability of various filtration technologies | |
Technology | Suitability |
Media filtration | Suspended solids removal. Use for firewater or utility water make up |
Ultrafiltration and microfiltration | Stricter suspended solids removal from 1 to 0.01 µm, but needs oil removal upfront. Firewater or utility water makeup |
Reverse osmosis | Removes dissolved solids, but requires suspended solids and oil removal upfront. Boiler water and cooling water makeup |
Nanofiltration | Removes dissolved solids in down to 0.001 µm. In combination with ultra- or microfiltration |
Column A provides the maximum permissible water-quality limits for a cooling tower. Columns B and C provide the cooling-water makeup quality and cycles of concentration (COC). Columns D and E provide the RO reject water and boiler-blowdown water quality to be used for blending. Columns F and G provide the water quality after blending and after COC is achieved.
Following on Table 1, Table 2 compares the various water consumption levels for both cases. Table 3 highlights the savings achieved by blending cooling-water makeup with RO reject and boiler blowdown water. A less obvious advantage is the result that less wastewater must be treated, and the potentially reduced size of the wastewater plant and volume of liquid effluents.
Current membrane technology has advanced enough to be used with confidence, and is used as a final step for deep-treating wastewater. Using ultrafiltration upstream of RO equipment for use in cooling water is now standard. Polishing of the RO-treated water by ion exchange or electro-deionization for the makeup of boiler feedwater can now be done with confidence. Finally, the use of membrane bioreactors (MBRs) as a direct pretreatment for RO is expected to be used more frequently in the future.
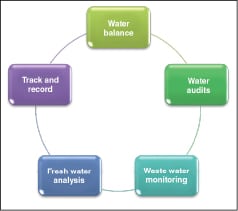
Water management
Establishing an overall water-management system is one of the most important steps in reducing a plant’s water footprint. This can be achieved by increasing efficiencies and minimizing losses. This includes developing a water balance, conducting facility inspections and water audits, sampling wastewater sources, monitoring usage and detecting leaks.
The major water consumers in many plants are the cooling towers. Hence, if tight control is applied to cooling-water usage, it is possible to save a significant amount of water. It is always a good idea to know a plant’s theoretical minimum freshwater use level. Water cascade analysis [3] is one way of determining this value.
Employee engagement
Each employee knows his or her area of the plant better than anyone else, so they are capable of identifying water saving opportunities within those areas. Inspiring and sensitizing employees to the importance of intelligent water management can result in significant water savings. One way to inspire employees can be to establish an award program that recognizes employees who propose or execute an action that significantly saves water or reduces water loss.
Water is a valuable resource in areas of high water stress or shortage. Various strategies, such as reducing water consumption, resourcing from alternate sources or reusing wastewater generated in the facility, can influence the amount of freshwater needed to run a process facility. Again, there is no single universal solution to this problem, so combinations of various strategies will need to be used. Finally, the tool of water management and employee engagement can be effective in reducing fresh water withdrawal.
Edited by Scott Jenkins
References
2. Puckorius, Paul R., Puckorius & Associates Inc.. Consider Recycled Water for your cooling water makeup. CEP Magazine (2013)
3. Foo, Dominic Chawan Yee; Manan, Zainuddin Abdul; Tan, Yin Ling, Universiti Teknologi Malaysia. Use Cascade Analysis to Optimize Water Networks. CEP Magazine (2006)
Authors

Rajiv Narang is a principal process engineer at Fluor Daniel India Pvt. Ltd. (DLF Cyber City, Phase II, Building 10, Tower A, 3rd floor, Gurgaon, Haryana, India; Email: [email protected]; Phone: +91 124 457 0700). He has over 25 years of experience in operation and design of petroleum and natural gas and LNG plants, as well as petroleum refinery units, pipelines, and power plants. He graduated from I.I.T Delhi in chemical engineering and holds an MBA degree. He is a Fellow of IChemE, a member of Indian Institute of Chemical Engineers (IIChE) and American Institute of Chemical Engineers.

Rashmi Jain is a process specialist at Fluor Daniel India Pvt. Ltd. (same address and phone; Email: [email protected]). She has more than 10 years of experience in process-system design of refinery units, and utilities and offsites. She has significant experience in designing wastewater treatment plants. She graduated from the Delhi College of Engineering with a degree in environmental engineering.