Achema 2012 — the 30th International Exhibition Congress on Chemical Engineering, Environmental Protection and Biotechnology that occurred in late June in Frankfurt am Main, Germany — took a decidedly forward-looking stance, focusing on a set of topics that the chemical process industries (CPI) will have to address in the future, including increased attention on sustainable processes and systems, as well as the transition to an economy based on renewable energy and biomass.
![]() |
By most accounts, Achema 2012 was considered a success, with 167,000 attendees visiting 3,773 exhibitors and listening to 900 lectures on various topics within chemical and biological processing. According to event organizer Dechema e.V. (Frankfurt, Germany; www.dechema.de), the proportion of exhibitors from outside Germany was almost half, with 56 different countries represented. Dechema also noted that 83% of Achema 2012 visitors rated the event’s quality as either “good” or “very good” in a post-event survey.
Among the themes that emerged from Achema was the key role to be played by the CPI in promoting a sustainable society and in utilizing renewable chemical feedstocks and fuels. These themes were reflected in many of the presentations at the event, as well as in the many of the exhibits featuring products for environmentally sound processes and bio-industrial processing.
The bio-based economy
With over 300 exhibitors specifically related to biomass processing, and a unifying feature known as “Biobased World,” Achema 2012 placed a heavy emphasis on examining the various implications of moving toward a world economy based on renewable biomass, rather than on fossil fuels.
Achema’s Biobased World was intended to be a venue in which companies involved all along the value chain of bioprocessing could come together to learn from each other. The event included a specific exhibition area, technology transfer sessions, and a conference program that included talks about a wide range of bioprocessing topics, including new microbial, enzymatic and catalytic production systems, process scaleup, downstream processing, biorefineries and more.
Biobased World featured a two-day conference within the wider Achema event that focused on the European bioeconomy, specifically. A presentation given by Maive Rute, director of biotechnology, agriculture and food in the European Commission (EC) Directorate-General for Research and Innovation, suggested that growing and implementing the bio-based economy in Europe depends squarely on research investment, stakeholder engagement and market enhancements. Toward improving bioeconomy markets and enhancing competitiveness, Rute said the EC Joint Research Center has set up a bioeconomy observatory to collect data that will inform policy decisions related to the bio-based economy. Further, her organization intends to help biorefinery networks develop, support solutions involving bio-based technologies for existing industries, and promote adoption of bio-based products.
In the research and innovation category, Rute commented that the goal should be to make the best use of funding, while continuing to increase investment in research. Among the EC initiatives in this area are to develop bio-based industry clusters to support innovation and to support entrepreneurship training.
Picking up on the theme of research and innovation in the bioeconomy, Martin Scheele, of the EC Directorat-General for Agriculture and Rural Development, spoke about closing the gap between research and practice. Research in Europe is very good, he explained, but often the results of that work are not fully exploited, and not translated into actual practice.
Bioeconomy hurdles
In most cases, there remains a price differential between petroleum- and biomass-derived hydrocarbons, but the gap is narrowing, and eventually, carbon atoms could have the same market value, whether they come from petroleum or biomass. The gap will likely be closed by overcoming the various technical hurdles to economic bioprocessing. These include developing processes with the ability to utilize multiple biomass feedstocks to produce the same product, a topic that came up often at Achema 2012. Other challenges mentioned in Achema presentations included the land constraints that must be considered in growing bioenergy crops.
Bio-based developments
In an example of how the bio-based economy is moving ahead in the real world, Beta Renewables (Rivalta Scrivia, Italy; www.betarenewables.com), a joint venture between the Chemtex div. of Gruppo Mossi & Ghisolfi and TPG, announced at Achema the planned startup in fall 2012 of the world’s first commercial-scale second-generation cellulosic ethanol plant in Crescentino, Italy. The facility is a 20-million gal/yr biorefinery that will produce both bioethanol and “green” electricity. The facility uses Beta’s Proesa technology, which converts energy crops, such as miscanthus and switchgrass, or agricultural waste, such as sugarcane bagasse, into fermentable C5 and C6 sugars, which are then processed into ethanol and other chemicals. Proesa’s enzymatic pre-treatment process runs significantly faster than other enzymatic hydrolysis technologies, the company says, and is free of acids and alkalis and produces minimal waste.
Beta Renewables recently signed an agreement with Gevo, Inc. (Englewood, Colo.; www.gevo.com) to develop an integrated process for cellulosic isobutanol. The project would integrate the Proesa enzymatic pretreatment technology with Gevo’s integrated fermentation technology platform for producing bio-based isobutanol and derivatives.
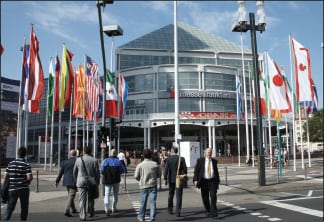
Sustainability science
Movement toward an economy based on renewable energy and biomass is closely related to the burgeoning field of sustainability. Achema served as a focal point for several aspects of sustainability, including the need to establish a robust body of science in the field. And developments at the June event in Germany complement the work of other sustainability experts going on elsewhere.
An indicator of the growing interest in assessing sustainability in a more scientific way is the recent launch of a new peer-reviewed journal, titled ACS Sustainable Chemistry & Engineering, by the American Chemistry Society (ACS; Washington, D.C.; www.acs.org). The journal is intended to be a forum for research on reducing environmental harm and achieving sustainable processes. The journal’s editor-in-chief will be David T. Allen, chemical engineering dept. chair at the University of Texas at Austin. The first articles in the journal will be published online in autumn 2012, and the first full issue will appear in January 2013.
Measuring sustainability
As attention on sustainability and green chemistry builds, one of the major challenges for CPI companies will be how to assess and quantify their sustainability efforts. Valid models and metrics are needed to accurately determine the degree of sustainability associated with a process or product in order to make sound decisions for R&D, manufacturing and marketing.
“Sustainability only makes sense when a system is considered as a whole, from raw materials to end of life, and its interactions with society and the environment are also accounted for,” explains Alexei Lapkin, a chemical engineering professor at the University of Warwick (Coventry, U.K.; www2.warwick.ac.uk) who has made green chemistry and its measurement part of his research program. Gaining this level of understanding is not trivial — it is a time-consuming operation that requires a large volume of data that must be checked for accuracy and reliability, Lapkin adds.
Other scholars, including Michael Neuman and Stuart Churchill, collaborators from the University of New South Wales (Sydney, Australia; www.unsw.edu.au) and the University of Pennsylvania (Philadelphia, Pa.; www.upenn.edu), respectively have contributed to the discourse on sustainability metrics as well. “What has been missing in science, engineering and public policy is a rigorous definition of sustainability, and a theory to conceptualize and measure it quantitatively,” the pair writes. They have developed a model for measuring the sustainability of processes that adapts and integrates the first and second laws of thermodynamics with the concept of rate processes. The combination is necessary, the researchers argue, because while thermodynamics yields the limits of what can be accomplished within a system, the rate process framework provides a way to incorporate the rates of regeneration and replenishment of resources compared to the rates of depletion, extraction and consumption. A model based on both thermodynamics and rate processes can be generalized for physical and social-economic phenomena, the researchers suggest.
Neuman and Churchill’s work includes development of a set of equations that permit the calculation of the degree of sustainability of any process in a way that takes into account spatial and temporal factors. The equations permit empirical applications that correspond to complex, evolving conditions across space and time.
Existing approaches to quantifying sustainability have limitations. For example, cost-benefit analyses, have been shown to lack validity for decision-making in sustainability, Churchill says. And life-cycle assessment (LCA) approaches, can also be somewhat lacking, Lapkin says.
Achema sustainability session
At Achema, attendees heard about the launch of a new program designed to bring an aspect of third-party peer review to claims on the sustainability of a product, process or service. The International Certificate on Sustainable Standards for Engineering (ICOSSE) program was developed by the AIChE’s Institute of Sustainability, along with Dechema. Darlene Schuster, executive director of AIChE’s Institute for Sustainability, says the criteria for the certificate program are drawn from AIChE’s Sustainability Index, a tool that helps companies benchmark their sustainability performance against a group of their peers. It combines technical and engineering components with financial and social metrics traditionally employed in other sustainability measures.
Applications to the ICOSSE program are reviewed by an advisory board, which determines which applications will receive the recognition. There has been initial interest in the program, Schuster reports.
During the same session at Achema, Peter Saling, the head of sustainability evaluation at BASF SE (Ludwigshafen, Germany; www.basf.com) presented his company’s activities toward quantifying sustainability. BASF has developed Eco-Efficiency Analysis as a method to systematically assess the sustainability of products and processes in a holistic way. The tool uses a life-cycle assessment approach to evaluate the environmental impact of a product or process from the point of raw material extraction to end-use and recycling and disposal options. In addition to the LCA, the Eco-Efficiency Analysis also includes an assessment of the carbon footprint of the product or process, as well as the total cost of ownership.
A product or process is scored in each of a set of six categories, including energy consumption, toxicity potential, emissions, resource consumption, land use and risk potential. The scores are weighted to arrive at a single Eco-Efficiency profile that can be compared to alternatives to determine the degree of sustainability of the product or process.
BASF has enhanced the Eco-Efficiency Analysis with its SocioEcoEfficiency Analysis (also known as SEEBalance), which incorporates the impact of products and processes on society, in addition to the costs and environmental impact. The aim is to quantify the sustainability performance of a product or process on an ecological, social and economic basis.
Saling said the method has been used by BASF to compare alternative process technologies, product packaging materials and help make strategic decisions on investments, facilities, research and development, marketing and stakeholder relations. BASF has also applied the method, which has been certified by TÜV, the German Association for Technical Inspection, and NSF International, to other processes outside the company.
Resource management
In keeping with the sustainability theme, Achema also featured a keynote address about the challenges and opportunities of recycling metals that are used for specific functionality and performance in electronic and other high-tech devices. Christian Hagelüken, director of European Union government relations at Umicore AG & Co. explained that concentrations of several critical metals are higher in “urban mines” of collected electronics parts than those generally found in primary ore deposits. The challenges associated with recycling these technology metals include thermodynamic constraints on processes, societal organization for recycling consumer products and the accessibility of materials within the devices. Ultimate success in this area will depend on innovation on the material side, as well as on the product design side, Hagelüken said, including improved collection systems, new processes for difficult material mixes and improved education about this issue.