Presented here are a few recent developments in filtration, including new cartridge design, automated self-cleaning systems and more
Used for everything from purifying a liquid product, or recovering a solid product from a gas or liquid solvent, to environmental applications such as air-pollution control and wastewater treatment, filtration is arguably one of the most widely used unit operations in the chemical process industries (CPI). As a result, no single filtration technology dominates the CPI. Instead, a wide variety of application-specific methods are constantly being developed and improved upon to handle a smaller class of filtration issues. Recent developments are presented here.
General trends
“Filtration and separation have many drivers,” says Chris Wallace, vice president of Technology, Filtration Technology Corp. (FTC; Houston; www.ftc-houston.com) “and at FTC we offer solutions across a broad range of industries and applications. The drive to develop new applications, such as carbon capture, reuse or sequestration, is definitely a hot topic. Also, we recognize increased demand for the products our customers in certain industries manufacture,” says Wallace.
“Just consider the impact COVID-19 has had on products related to PPE [personal protective equipment] and the chemical sanitizer supply chain, or on the reduction of demand for other products like fuels. Many facilities have redirected their processes to support this new demand, which impacts their filtration and separation challenges. Based on what we know today, I see the demand for products supporting PPE and sanitization chemicals continuing over the long term, with the reduction in demand for fuel being only a short-term trend. Of course, environmental legislation is a significant driver for all filtration and separation technologies. It has historically been a driver and will continue to be over the long term,” says Wallace.
“Even in tumultuous times, the one thing that remains the same with all our customers is a steady focus on process reliability and improved process efficiencies,” says Wallace. “As a result, the trend is for more reliable filtration performance, higher flow capacity, lower clean pressure-drop, longer online filter-life, smaller footprint, lower energy demand, minimal operator exposure to hazardous fluids, and the reduction of waste,” he says.
Improved cartridge design
When it comes to filtering liquids, cartridge technology has been a traditional way to remove solids from liquid products, such as fuels and water. “Developments in polymer and fiber technology, non-woven media technology and membrane technology, as well as advancements in filter-testing equipment capabilities have really raised the bar on what can be done,” says FTC’s Wallace. “These advancements in filtration media technology and cartridge technology, combined with our ability to analyze particle properties, capture mechanisms, loading and efficiencies on small- and full-scale test stands in our R&D center, have allowed us to redefine expectations upwards. This applies to new requirements driven by our customers’ ever-changing needs, as well as to legacy applications,” says Wallace.
“For example,” Wallace continues, “we see a lot of chemical treatments and additives added to fluid processes. These often-undisclosed additives can impact filtration performance or even cause degradation of a filter or filter media. Additionally, we see demand for fluid processes at higher temperatures, which results in complex chemical and thermal compatibility challenges. Our arsenal of filter media and element construction materials combined with our testing capabilities allows us to offer filter cartridge solutions with proper chemical and thermal compatibility to withstand more challenging environments, especially over the extended service life our customers demand,” he says.
“We spent many years in our R&D [research and development] center developing what we call Invicta technology,” Wallace continues. “After listening to our customers and understanding their challenges and goals, we worked to develop a cartridge technology that solved as many of their issues as possible,” he says.
“Before Invicta, the industry had been stuck on cylindrical cartridges, since they were first developed,” Wallace explains. “Even our previous patents and technology developments had been focused on cylindrical cartridges. With customer requirements in mind, we focused on the fundamental principles of filtration and disregarded all thoughts of industry norms, of what was expected. The result was a groundbreaking, patent-pending cartridge technology that broke with normal industry expectations and was inclusive of many filtration markets and applications,” boasts Wallace.
Invicta (Figure 1) offers a wide range of chemical and thermal compatibility, maximum effective surface area in the smallest footprint, reduced media face velocity to increase solids loading, and longest online life without sacrificing the reliable effluent quality, continues Wallace. “To top it off, lower pressure drop reduced energy costs, and Invicta’s unique coreless design lowered the disposal footprint for our customers, with minimal components and greater packing density in shipping and disposal containers,” he says.
“Because of its innovative design qualities, Invicta offers up to 275% more surface area over cylindrical filters,” says Wallace. “Although Invicta technology is just hitting the one-year mark in the market, it is already revolutionizing the industry. Our customers are calling it the ‘magic filter.’”
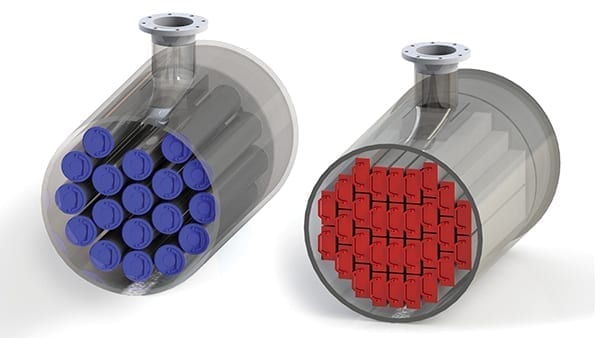
Figure 1. Invicta is said to offer up to 275% more surface area over cylindrical filters. FTC
Automated self-cleaning
“The trend in liquid filtration is getting away from manually cleaned filters,” says José Sentmanat, owner of Liquid Filtration Specialist, LLC (Conroe, Tex.; www.filterconsultant.com). “The old technology of manually cleaned filters, like the horizontal-plate filters, is losing popularity,” he says. “First of all, there are very few manufacturers that offer that type of filtration equipment, and the ones that still do are probably wondering where their future business will be,” explains Sentmanat. “Yes, there have been self-cleaning filters for a few years now, but the new technology is self-cleaning candle filters. The candle filters offer either a wet cake discharge by backwashing the filter cake off the candle elements or a dry cake discharge by simply blowing back the dried filter cake off the candle elements,” he says.
One company offering such technology is Sulphurnet (Culemborg, the Netherlands; www.sulphurnet.com). “In the last few years, we have seen a trend in the filtration market where users are changing from big, manually cleaned filters to smaller units and fully automated self-cleaning systems,” says Sulphurnet director Jan Hermans. “The result of this is more control of the process, less maintenance, more personal security and more space available on the plant. Besides this, we see a development of stainless-steel materials for fine (low-micron particle size) filtration that which can be cleaned and re-used,” he says.
Hermans points to a recent example: “Classically, liquid-sulfur-purification plants are equipped with horizontal pressure-leaf filters, which have to be opened and manually cleaned at the end of a filtration cycle. This work is labor intensive and is a safety risk due to the high temperature of the product. Recently, Sulphurnet has installed the first self-cleaning candle filter [Figure 2] for the filtration of liquid sulfur. This filter can discharge its filter cake in a fully automated way without completely opening the filter system. Since the installation, we have been monitoring the performance of the liquid sulfur filter and it currently shows that this filtration technology will be a very good replacement for the existing technology.”
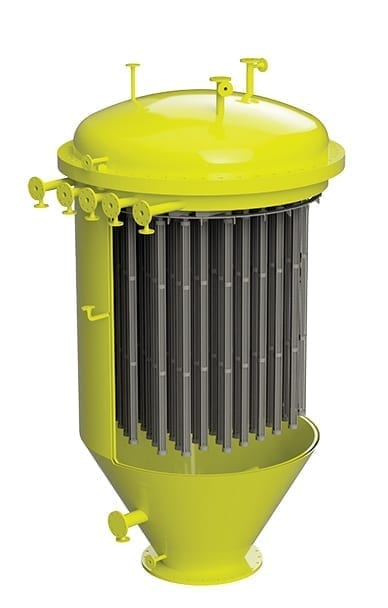
Figure 2. Automated, self-cleaning candle filters can now be used for filtering molten sulfur, for example. Sulphurnet
Automated self-cleaning filter systems are also becoming important for other types of filters besides candles. “We see a trend towards sustainability, increased purity, less waste with lower energy consumption and reduced emissions,” says Oskar Sieking, business manager Filtration at Outotec (Espoo, Finland; www.outotec.com). “These drivers push the industry towards fully automated filtration solutions,“ he says.
“Besides these drivers in existing processes, we see a wide range of developments in renewable processes utilizing raw material of natural origin rather than today’s oil-based chemistry,” continues Sieking. “These new processes have their specific processing and filtration challenges to the required filtration steps. One of the developments addressing all these drivers is our PF-DS,” he points out.
“With the new PF-DS [Figure 3], we can handle fully automatic applications like pigments, with very fine particles and thin cakes,” explains Sieking. “From the material-selection point of view, we are now able to offer full FDA [U.S. Food and Drug Administration] compliance for food-grade products like starch.”
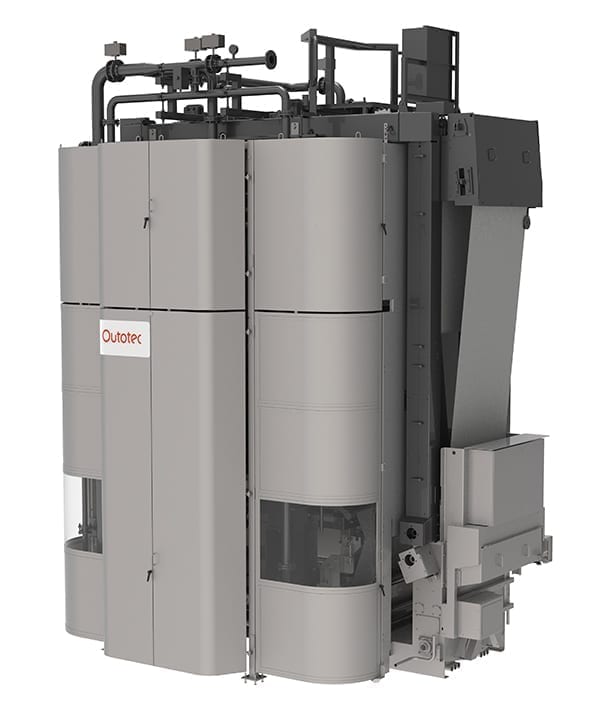
Figure 3. Outotec’s Larox Pf-DS double-side pressure filter handles challenging materials with difficult filtration or high cake-washing needs. Outotec
The PF-DS is a tower press filter where the plate pack is composed of polypropylene membrane filter plates stacked on top of each other. The cake forms between the closed filter plates on the top and bottom side of the filtration chamber — hence the term double-side filter.
The PF-DS combines two proven technologies into one unit. The mechanical operation and frame are shared with the Outotec Larox PF pressure filter while the unique filtration process is powered by the double-side plate pack from Outotec Larox DS filter (earlier known as Hoesch DS).
Key features and benefits of this technology include: excellent handling of difficult and slow-filtering materials; guaranteed cake discharge, even with challenging material; multiple cake-washing options: options for efficient and automatic in-situ cleaning in place (CIP); the ability to handle corrosive process conditions; and more.
Sieking also adds: “At our Dewatering Technology Center, we work on optimization of filtration and process parameters for new applications like the bio-based materials. On the filter cloth side, we cooperated closely to develop filter cloth qualities for a better and sharper screening of fine particles.”
Corrosion resistance
“Over the last few years, customers have been more and more asking for filtration technologies and processes that reduce operating costs and avoid production downtime,” says François Fevrier, Chemicals Business Development Director at Andritz Separation (Graz, Austria; www.andritz.com). “The latter has been one of our many focus areas, specifically the development of a corrosion-resistant filtration technology.”
To meet these challenges, Andritz recently introduced its CORES vacuum-drum filter (Figure 4). “The structural design of this new filter is, dependent on size, made out of steel or completely out of glass reinforced plastic (GRP),” explains Fevrier. “In addition, all parts in contact with the product are covered with a layer made of corrosion-resistant, non-reinforced plastic, which is commonly used in such industries like polypropylene (PP) or polyvinylchloride (PVC) manufacturing. Furthermore, some internal wetted parts can be completely designed out of resistant plastic and will be welded together with external surfaces made out of plastic to have a closed surface for these corrosive applications. No single screw will remain in the wetted process area; therefore a maximum on corrosion resistance in highly corrosive media is given,” Fevrier says.
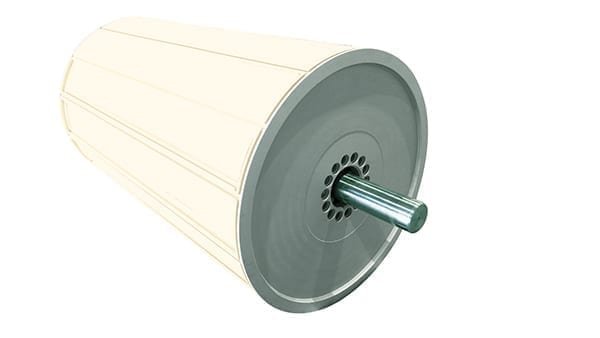
Figure 4. Andritz’s patented sandwich design of the CORES technology provides a permanently chemically resistant surface and can be made with different materials to ensure resistance to chemicals. Andritz
Water and wastewater treatment
“In the field of water filtration, the industry is driven by more and more huge projects in Asia for both water and wastewater treatment,” says Carsten Bachert, CEO at WTA Technologies GmbH (Gotha, Germany; www.wta-tec.com). “As one outcome, the price for water production dropped to $0.40/m 3 of desalinated water. One effect of reaching such price level is the eroding margin for contractors and suppliers. Consequently, the prices for filters went down over the last two years,” he says.
“To catch up with this trend, WTA Technologies decided to invest in a fully automatic production line for submerged membrane modules,” says Bachert. “This line was commissioned recently and ensures outstanding quality at low production costs. But the real challenge is not to standardize productions for huge quantities, it is more to use such a tool and still offer a customizable product for a price of a standardized one,” he says.
“It is not a new application, but for the first time, we are able to retrofit submerged filtration plants with our membrane blocks,” says Bachert. “Usually, the genuine supplier gets an order automatically from his client for changing the membranes,” explains Bachert. “As these submerged membrane module markets do not know anything about “me-too” products, the spare business is secured just by being selected as supplier during the construction phase.”
What WTA Technologies does differently is to manufacture membrane blocks that fit into the frame of the genuine supplier. “Just by changing the membrane blocks and adopting the permeate connection, the membrane module can be retrofitted with latest state-of-the-art filtration technology,” says Bachert. “As the membrane block can be operated by gravity or by use of a permeate pump, with or without back-wash the process control and process philosophy is not touched,” he says.
The company’s latest product is MYTEX Blocks (Figure 5), a customizable, textile-based, flexible and back-washable flat sheet. These self-supporting, stackable blocks allow the highest packing density. They consist of 2-mm membrane sheet with an 8-mm channel between the sheets; no extra frame is needed to support the membrane blocks for up to six blocks stacked on each other. A membrane-block intensity of 174 m²/m³ is said to be one of the highest available for plate/sheet configurations. The blocks are easy to service, because they open from all sides, and are easy to handle without special tools, cranes and so on. Despite the high packing density, the blocks have a low propensity for clogging due to the wide (8-mm) channels between the sheets.
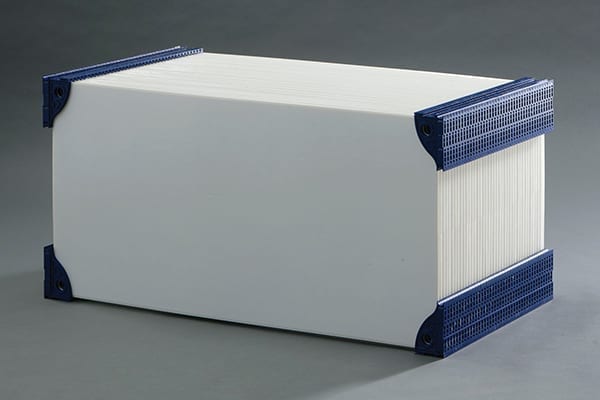
Figure 5. MYTEX Blocks incorporate customizable, textile-based, flexible and back-washable flat sheets that are formed into self-supporting, stackable blocks. WTA Technologies
The MYTEX submerged membranes have been used in a number of applications. Some examples include: integrated for use as a membrane bioreactor; sequential use as a polishing step in tertiary treatment; sequential use as sludge thickener in aerobic digestion; and for direct filtration of medium- to high-solids water and wastewater.