For chemical companies, supply chain success demands optimized, GHS-compliant labeling practices
Safety and compliance are top priorities in the chemical process industries (CPI) and heavy-duty industries, with proper storage and handling of chemicals — especially hazardous ones — a prominent and ongoing concern. While industry professionals certainly recognize that labeling plays a critical role in handling chemicals safely, not everyone is aware of the pivotal subset issues associated with labeling. The simple fact is that the substrates selected for chemical labels, as well as the labels’ proper storage and application, are every bit as essential to safe, compliant chemical documentation as the information they contain. Following is a set of best practices that can ensure mission-critical labeling success for CPI companies.
GHS compliance
Several factors are involved in chemical labeling compliance per the Globally Harmonized System for Classification and Labeling of Chemicals (GHS), which the United Nations (New York, N.Y.; www.un.org) formally adopted in 2003 to standardize the classification and labeling of globally transported chemicals. To meet compliance, chemical labels must include signal words, product identifier verbiage, hazard and precautionary statements, supplier information and pictograms — all standardized by the GHS.
Above all, GHS-compliant labels must contain clear and consistent content, be durable, and stay affixed to the drums or containers to which they are applied — even when exposed to harsh or high-temperature conditions. While GHS is not a codified law, the U.S. Occupational Safety and Health Administration (OSHA; Washington, D.C.; www.osha.gov) adapted its Hazard Communication Standard to align with GHS labeling guidelines.
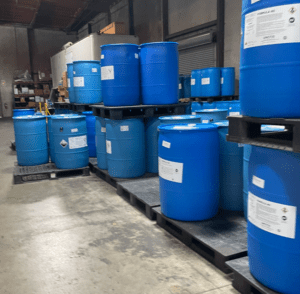
FIGURE 1. Labels for chemical containers require sound material science to perform under harsh conditions (Source: Reliance Label Solutions)
Meeting these guidelines requires sound materials science. While exact compositions differ, GHS-compliant labels generally comprise several layered components. Starting from the top down, first is the appropriately named topcoat, a unique surface optimized for a specific printing process. A well-designed topcoat allows for printer ink or toner to transfer properly to the print surface. Coupled with the proper corresponding inks, an ideal topcoat increases print durability to best ensure GHS standards are met.
Next is the face-sheet, the matter-of-factly-named material comprising the label face. While face-sheet substrates can range from paper to a variety of polymers, those for GHS-caliber labels are typically composed of vinyl (PVC), polyethylene (PE), polypropylene (PP) or polyethylene terephthalate (PET). These polymers offer the best blend of chemical resistance, heat resistance, tensile strength and cost.
After the face sheet, the next component is the material that adheres the label to the substrate, typically an acrylic-based adhesive. Most labels subject to GHS will utilize permanent acrylic-based adhesive, although other adhesive types such as removable acrylics, cold-temperature acrylics and hot-melt rubber are also available. Concerning durability, acrylic-based adhesives bring several advantages. For one, this type of pressure-sensitive adhesive, characterized by its heavy-duty strength, powerful adhesion and extraordinary mechanical performance, can adhere to a wide variety of surfaces including plastic, glass and metal. And since they are often composed of high-performance methyl methacrylate (MMA), acrylic adhesives have excellent resistance to both environmental stressors and chemicals.
When selecting a particular adhesive, it is critical to consider the material of the surface on which the label will be applied, as well as the temperature at which the label will be applied and the temperature to which the product (with its label) will be subjected.
The last material to consider is the release liner, the backing that is peeled off before the label is applied. Sometimes referred to as a “carrier” or “backing,” this liner can be made from either paper or film, and is designed to serve as a protective barrier between the pressure-sensitive adhesive and the label product, until the label is ready for application.
Best practices for hazardous chemical documentation, then, involves not only ensuring required information is printed on labels, but also that the selected label material, ink, and adhesive are compatible with both printers and each other, and can withstand the environmental conditions typical of the specific application. In addition, labels should be stored in a manner that prevents exposure to elements that might damage their adhesives, liners and other components.
Since chemical labeling compliance is critical to safety, and noncompliance can result in regulatory fines and risk of litigation, personnel responsible for chemical labeling operations should create and follow a set of best practices relevant to their company’s chemicals niche. Often, a key first step is collaborating with other experts in the chemical labeling field — namely, trusted vendors.
The right chemical labeling solutions provider will partner with customers to tailor tried and true best practices to specific, on-the-ground circumstances. Among other benefits, having these in-depth discussions from a project’s onset yields the highest potential for selecting the labels’ optimal compositional attributes, as well as determining proper storage scenarios and application techniques. Once these ideal parameters are created, reinforcement is key: for example, best practices for storage should be printed directly on the box in which the labels are contained, providing users with a visual reminder of proper procedure.
Overcoming common labeling compliance challenges
Durability is the most critical attribute in BS 5609 and GHS-compliant labels. Such specialized solutions must withstand exposure to high temperatures, humidity, chemicals, oils, greases, solvents and moisture, and be resistant to tears and abrasions.
In this context, perhaps most concerning are the potential for spills. If the chemical in question is harsh enough, it may cause labeling images and text to bleed off — a scenario that carries a spill’s adverse effects from its immediate area to the entire supply chain. Encouragingly, to prevent the likelihood of such unacceptable outcomes, next-generation GHS-compliant labels can incorporate a special coating designed to counteract just such a precarious scenario.
However, even if labels are composed of suitably robust materials, storage can be a considerable challenge. High temperatures, humidity and moisture are typical conditions at chemical and petrochemical facilities, as are dirt, dust and debris. Each of these can have an adverse effect on the label material, adhesive and liners.
Chemical labeling solutions suppliers should stress to users that unused labels must be securely stored in an area removed from harmful conditions; ideally, they should also remain in their original box and plastic wrapping until needed. And again, use and storage guidelines should be printed on the box as an evergreen reminder and refresher.
Looking ahead to a more compliant future
Like many business practices, the keys to continuous labeling compliance improvements in the chemicals sector come down to innovation and collaboration. Regarding the former, new materials, adhesives and liners that not only survive but thrive in harsh conditions are perpetually being developed; some labeling suppliers even have laboratories where various materials constructions and printers are designed, tested and honed. Such infrastructure also comes in handy for providing live or virtual demonstrations, as well as troubleshooting the types of unforeseen adverse issues that inevitably arise in an industry as complex as chemicals.
And naturally, there are established “do’s and don’ts” that should form the foundation of any solid chemicals labeling process. Critically, because label composition, storage and application may differ depending on the chemical and container, these basics must be malleable enough to accommodate new products, new environments and new horizons in general.
To help ensure hazardous chemical labeling operations are following compliance best practices, companies should look for a labeling partner that can provide guidance and expert-driven services to do just that. For instance, on-site assessments that evaluate labeling compliance, application infrastructure maintenance, storage temperature and other issues that affect label performance can provide valuable insight into the challenges — and subsequent solutions — for optimized label operations.
Edited by Scott Jenkins
Author
Troy Lucas is product engineer for Reliance Label Solutions, a Kansas City-based specialist in manufacturing hazardous container labels for the petroleum, chemical and environmental industries. The company’s labels are designed to thrive in harsh environments and include chemical drum labeling solutions that meet stringent GHS, HazCom and IMDG labeling requirements. Reliance Label’s other GHS-compliant solutions include label printing software, color printers and printer consumables. www.reliancelabel.com