A look back at the history of the digital transformation in the chemical process industries (CPI) can help guide current strategies for leveraging digital tools for the benefit of humans and the planet.
The main story in the chemical process industries (CPI) over the past four decades has not been about major new products or production processes, but rather about the industry’s digital transformation. Automation and digitization have made processes safer and profitable. While the safety of workers is non-negotiable, the strategy of continuing to extract the maximum production from the same resources to support the same revenue streams has had a hidden opportunity cost. The author suggests that now is the time for leaders in the CPI to ask larger and more complex questions of the data coming from digitization and presents a set of seven steps that the industry can take today to better align the next stages of the digital transformation with the needs of humans and the planet.
A historical perspective on the digital transformation
To change the direction of any transformation, it is important to know its current state. And to grasp the current state, it is helpful to understand how we arrived at the current state. Instead of using the IT-centric diagrams, in this work, I have opted to use the lifecycle of a process plant, which chemical engineers are familiar with, to share the snapshots (in time) of the transformation.
The 1980s
The focus of chemical engineering education in the 1980s was on thermodynamics, fluid mechanics, reaction engineering, mathematical modeling, and the emerging field of process control. Universities offered degrees in six or seven classical engineering disciplines. Degree names with hyphens and InterCaps did not exist. The role of computers in modeling and control began to accelerate in the late 1980s. In that decade, the focus of the industry was on process design and optimization. The field of CAD that began in the late 1960s had matured by the mid-1980s.
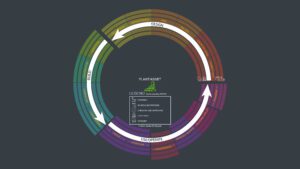
Figure 1. The process plant lifecycle from the 1980s is shown here, with parts operating as silos
In terms of the engineering work processes, the main stages of the process plant lifecycle were well established (Figure 1) but the design, build and operate parts of the cycle worked as silos. Key performance indicators (KPIs) were productivity and efficiency for engineering work and safety and uptime for operations. Paper and face-to face meetings were the main methods for capturing and disseminating knowledge.
Engineers (the author included) had to transition from using slide rules and handheld calculators to accessing mainframe computers via remote terminals and become proficient in computer languages like BASIC and Fortran. However, we continued to respect engineers with deep knowledge of equipment (steel) and molecules (processes), which could be thought of as process technology (PT).
The 1990s and 2000-aughts
In the 1990s, a consortium at Purdue University released the Purdue Enterprise Reference Architecture model (PERA) [1]. PERA was about computer-integrated manufacturing (CIM) operations. A derivative of PERA, the Purdue Reference Model “95” had five levels. As illustrated in Figure 2, the architecture linked the process (Level 0) to the monitoring and control functions (Levels 1-2) and extended it to manufacturing execution systems (Level 3) and business coordination systems (Level 4). The operational data flowed upward in terms of levels and the business directives flowed from the higher to the lower levels.
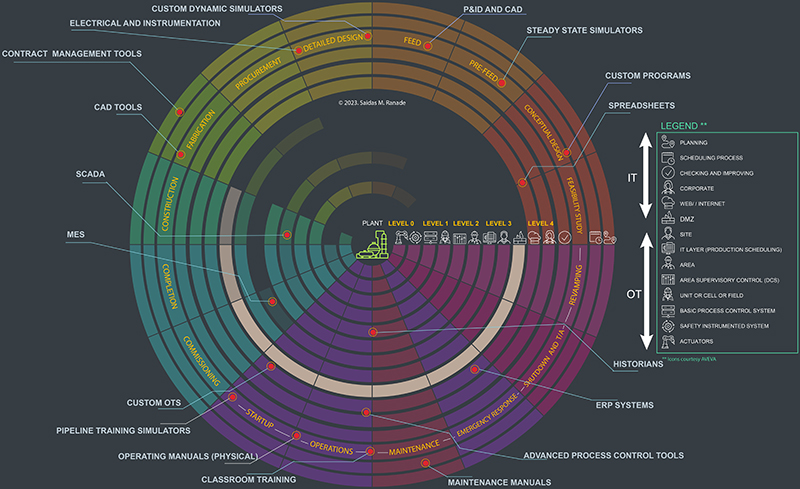
Figure 2. The diagram represents OT/IT integration with levels and stage-specific applications
Firewalls separated the operational technology (OT) systems from the IT systems to maintain the safety and integrity of critical operations. OT consisted of distributed control and supervisory control and data acquisition (SCADA) systems with a tight integration between the hardware (computation power), software and communication systems. Data transfer between the levels of the OT improved. The individual layers also had more computing power. Physical servers on premises were the norm, but the spread of the Internet and the growth in connectivity had begun to improve the supply chain.
The focus of engineering work was on dynamic control and real time optimization of operations. The KPIs included reliability, yield, efficiency, and environmental compliance. Newer standalone lifecycle stage-specific decision support and automation software applications for engineering work had emerged (Figure 2). Information management systems further streamlined the handoffs between the various stages of the process life cycle. By the late 1990s, the practice of concurrent engineering had become the norm.
This was an opportunity for radical innovation in PT, but innovation and development continued in the world of data communication protocols in OT and enterprise resource planning (ERP) applications in IT. At the start of the new millennium, information management professionals were driving the changes. Chief information officers (CIOs) and chief technology officers (CTOs) were now in charge.
In the first decade of the millennium, PT, OT and IT systems started to merge. Access to computers for consumers improved. More consumers began to leverage the power of the Internet. For operations, real-time data capture and dissemination was still elusive because of bandwidth limitations and latency issues. This continued until the early 2010s. A momentous change happened around 2011 with the release of the Industry 4.0 Standards by the German Ministry of Education and Research [2].
The 2010s
Industry 4.0 was about the cyber-physical world. The idea popularized further in the mid-2010s as the “Fourth Industrial Revolution” focused on interconnectivity and smart automation [3]. Its primary focus was on further efficiency gains. The initiative later adopted by different governments led to improvements in the speed and quality of capture, transmission, storage and transformation of data (Table 1). Near-field communications (NFC), Bluetooth, Wi-Fi, and broadband began to address the bandwidth limitations. Virtualization and cloud began to mature. With the advent of Hybrid and Edge computing, the IT world began to disrupt the traditional OT-induced mindset of closed system architectures. By the end of the decade, talk about machines, molecules and IM seemed dated compared to talk about data. Chief digital officers (CDOs) were the new kings.
Table 1. Key developments: data lifecycle after 2010
Toward the end of 2010s, data and digitalization became the new craze and new graduates were swarming to careers in data sciences. Table 2 is a summary of the timeline of the digital transformation we have discussed so far.
Table 2. The table presents a timeline for the digital transformation in the chemical industry
Today
Thanks to the advances in digitization, virtualization, high speed interconnectivity, interoperability, and artificial intelligence (AI), we are now closer to making the notions of digital thread(s) and digital twins from the mid-2010s a reality (Figure 3).
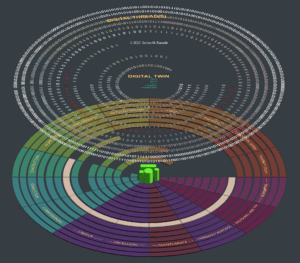
Figure 3. This diagram illustrates the rise of the digital thread(s) and digital twins
Due to cybersecurity concerns, critical OT assets continue to remain isolated from the Internet and this trend is likely to continue for a while. However, as illustrated in Figure 4, the levels-focused hierarchical pyramid information infrastructure and architecture of the Nineties is now slowly transforming to a flatter network model of data flow where every asset communicates or is ready to communicate in real time (or close to real time) with every other asset or device.
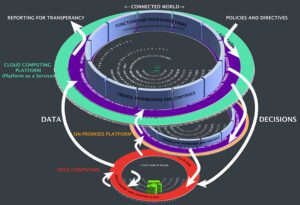
Figure 4. Post-industry-4.0 enterprise data architecture is characterized by a network of interconnections among assets and devices, where each is ready to communicate in real time (or close to real time) with all the others
Recent developments
The digital transformation of the process industries and digitalization of commerce has led to a rapid increase in electricity demand, which is projected to increase by 50% by 2030 cf. 2023 [4]. Pollution and landfills have continued to grow in the past two decades. The bigger income disparity between the rich and the poor has accelerated the digital divide, contributing to an increase in the workforce skills gap. Rampant automation has created a fear of AI replacing chemical engineers. Failing to question the old local objectives of optimization has made our critical supply chains more fragile.
The CPI is a big consumer of energy, but its digital transformation alone has not caused the above-described unintended societal trends. Government policies and consumer preferences have a significant impact on driving the strategy, investments, and research in the process industry. The good news is that on the policy front, there is an awareness of the limits of growth of the current approach to manufacturing and energy use. The Society 5.0 initiative from Japan in 2017 [5] and the recent Industry 5.0 from the European Union (EU) [6], which is a complimentary standard to Industry 4.0, have stated that it is time to include not just the planet, but also the people into development plans.
The future
In the coming decades, research and investment priorities are likely to include commitments to achieve net zero carbon dioxide emissions by 2050, as well as provisions to address water security and the circular economy. The process industry will need to reimagine its products and processes. Chemical engineers will play a crucial role in the design, construction, and startup of plants for green hydrogen, carbon capture, biofuels and energy minerals. Safe use of nuclear micro reactors and making circular economy a reality will need engineering ingenuity.
The digital transformation has freed major engineering problems and opportunities from the confines of time and space. The computation tools and engineering resources do not have to be in the physical proximity of the problem. The focus on safety of workers and environmental compliance are non-negotiable and must continue but we must go beyond that to leverage digital technology for training workers and for increasing worker engagement.
Here are seven specific actions engineering leaders and chemical engineers in the process industry can take starting today to make a positive difference.
- With the availability of the digital twins and powerful simulation tools, evaluate more scenarios that include the wellbeing of the planet and the people.
- Use digital threads and data that span longer time windows for training AI/ML applications to make process plant lifecycles more robust.
- Continue automation of tasks, but prioritize effort on repetitive and boring tasks, tasks that are impossible for human beings to perform and tasks that are necessary, but put human lives in danger.
- In the past, we leveraged the idea of concurrent engineering for efficiency and cost reduction. Use the recent advances in digital collaboration to engage cross-disciplinary teams and leverage the world’s best minds to solve the hard problems.
- Improve the antifragility of supply chains by exploring opportunities to use renewable resources from diverse regions rather than exploiting one resource from a specific area, while considering the impact on local populations.
- Learn to learn faster by leveraging digital technologies, including AI. The energy transition to renewables means an opportunity for applying new skills in developing new sustainable processes and operational technologies. Leverage the power of data, connectivity and simulations to provide just in time micro-learning at the point of use.
- Strengthen social and cross-cultural awareness. Making the circular economy a reality is a daunting but an exciting problem. Chemical engineers will need to learn to work in multidisciplinary teams involving pure sciences, engineering, geosciences, social sciences, and economics.
In summary, this is an opportunity especially for chemical engineers to go beyond the lure of just repurposing data to fundamentally changing the reality the data represents. This is an opportunity to use data to pose different questions. It is the time to “Take the Road Less Traveled [7].” In the coming decade, engineering leaders will need grit, courage, and leadership to ask different questions, define novel solutions and implement the required changes. And the good news is we cannot easily digitize and automate grit, courage, and leadership. At least, not yet!
Edited by Scott Jenkins
Acknowledgements
The author has used in Figures 1 and 2 a few icons shared with him by the wonderful Content Design team of AVEVA (a part of Schneider Electric). However, the views and opinions expressed are solely of the author and not of any other entity mentioned in this article.
References
- T.J. Williams, “The Purdue Enterprise Reference Architecture”, IFAC Proceedings Volumes, vol. 26, no. 2(4), pp. 559-564, July 1993.
- H. Kagermann, D.W. Wahlster and J. Helbig, “Recommendations for Implementing the Strategic initiative INDUSTRIE 4.0,” Secretariat of the Platform Industrie 4.0, Frankfurt, Germany, April 2013.
- K. Schwab, “The Fourth Industrial Revolution: what it means, how to respond,” World Economic Forum, Geneva, Switzerland, Jan 14, 2016, [online] Available: https://www.weforum.org/agenda/2016/01/the-fourth-industrial-revolution-what-it-means-and-how-to-respond/
- M. Ahmad, “Schneider Electric: Electrifying the energy transition,” energydigital.com, April 4, 2023. [online] Available: https://energydigital.com/articles/schneider-electric-electrifying-the-energy-transition
- Society 5.0, “What is Society 5.0,” Cabinet Office, Government of Japan, Tokyo. [online] Available: https://www8.cao.go.jp/cstp/english/society5_0/index.html
- Industry 5.0: A Transformative Vision for Europe, ESIR Policy Brief No. 3, Publications Office of the European Union, Luxembourg, December 2021.
- R. Frost, “A Group of Poems,” The Atlantic, pp. 221-215, August 1915.
Author
Saidas Ranade is a principal consultant specializing in Learning and Competence Assurance Solutions for the Industrial Automation Services team of the Schneider Electric (SE) Company. Prior to joining SE, he was the director of training for PAS Global (now Hexagon). He received his Ph.D. in chemical engineering from the University of Houston, where he also taught thermodynamics to engineering students. He has published over twenty-five papers on a broad range of topics, including process modeling, organizational excellence, problem solving, competence modeling and competence assurance systems. As a professional standup comedian, he has entertained over 50,000 people. Ranade is a member of Tau Beta Pi and the Screen Actors Guild (SAG-AFTRA). Direct questions and comments about this article to Saidas M. Ranade (Email: [email protected])