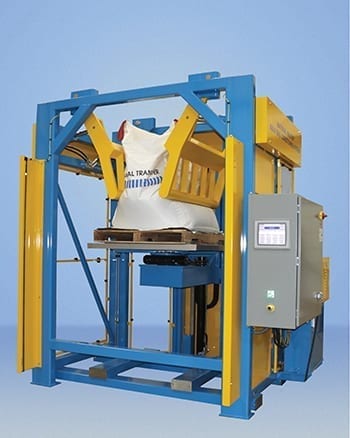
Material Transfer and Storage
This bulk-bag conditioner has a rotary lift platform
The new hydraulic bulk-bag conditioner with rotary lift platform (photo) quickly and safely returns solidified materials in bulk bags to a free-flowing state. The operator loads the bulk bag into the unit via forklift and activates a conditioning sequence controlled by a programmable logic controller (PLC). Twin pivoting conditioning arms with extended travel penetrate deeply into the material for effective results. A robust hydraulic rotary-lift platform positions the bulk bag during the conditioning sequence, ensuring the bag is thoroughly conditioned from top to bottom. Patented design returns even the most severely agglomerated materials to a free-flowing state. Units are custom designed. — Material Transfer and Storage, Allegan, Mich.