For decarbonization of chemical processing sites, electrification opens a new world of efficiencies and cost benefits
The industrial sector is responsible for one-third of the world’s end-use energy consumption, according to data from the U.S. Energy Information Administration (EIA; Washington, D.C.; www.eia.gov) [1]. Within that sector, the manufacturing industry emits 20% of the world’s carbon dioxide emissions [2]. Optimizing industry energy use will be a pivotal component of global strategies to limit greenhouse gas emissions and reach climate-saving goals.
The chemical industry is the second-largest consumer of energy within manufacturing sectors, according to EIA [3]. Chemical processing plants use natural gas and other energy sources to convert raw materials into a variety of products. Electrifying chemical engineering processes can be a cornerstone of emissions-reductions initiatives moving forward.
Electrification has the potential to significantly reduce reliance on fossil fuels and improve the sustainability of chemical manufacturing by replacing fossil-fuel-based processes with electricity generated by renewable sources — an obvious benefit for the environment (Figure 1). But the use of renewable electricity sources can also reduce the volatility and uncertainty associated with fossil-fuel prices, making the production of chemicals more predictable and cost-effective.
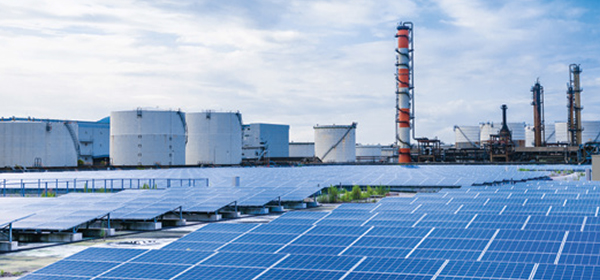
FIGURE 1. Electrification using renewable energy sources has obvious environmental benefits, but there are also opportunities for improvements in process reliability and reduced energy-cost uncertainty
Understanding emissions
A first step in decarbonizing industrial or chemical facilities is understanding emissions. Emissions are grouped by type or scope and must be addressed according to their classification. There are three scopes of emissions per the Greenhouse Gas (GHG) Protocol (www.ghgprotocol.org), illustrated in Figure 2.
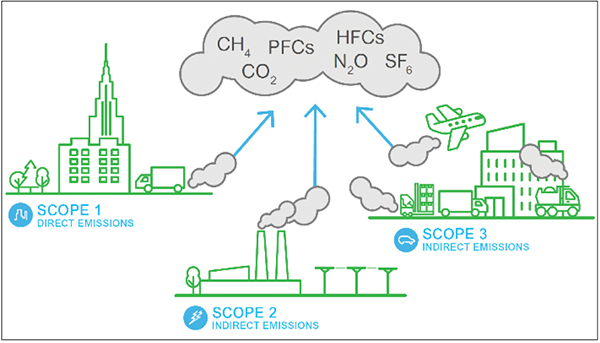
FIGURE 2. Manufacturing sites must consider the three scopes of emissions as described by the Greenhouse Gas Protocol
Scope 1 emissions are those emissions an organization is directly responsible for generating. Common examples include large compressors or pumps driven by gas or steam turbines and onsite sources of heat or power generation, such as boilers.
Scope 2 emissions are those emissions resulting from the grid-sourced generation of power. These emissions are considered outside the direct responsibility of the industrial facility (since it is the utility operator who determines the energy mix), but the company is still responsible for these emissions, because they are driven by demand.
Finally, Scope 3 emissions are all other indirect emissions. This broad category includes everything from the emissions generated through waste management to those generated in the value chain. For many cases, Scope 3 emissions not only make up the highest amount of a site’s total emissions footprint, but are also the most difficult to address.
The calculus of electrification
Industrial activity is a major contributor to GHG emissions. There is no one-size-fits-all solution to meet net-zero emissions targets, but rather countless opportunities for innovation. It can be said that electrification of assets requires a careful calculus.
There are two categories of processes that can be electrified that are the main consumers of energy in any industrial plant — motion-related processes and heat-related processes.
Scope 1 and 2 emissions can be optimized through a hybrid energy mix. Furthermore, zero emissions from power generation can be achieved via substituting energy from fossil fuels with “clean” energy sources. Process electrification and net-zero power-management hubs can help users in managing their energy mix, which in turn optimizes emissions.
A survey from 2020 found that 44% of energy consumed in industrial settings is fuel consumed for energy [4]. This includes generation of heat for processes like melting and cracking. Ref. 4 also estimates that 50% of that heat could easily be replaced with electric solutions that are available today. The concept of electrification in chemical manufacturing plants, then, is not about completely changing every process altogether. It’s about proper peaking and placing, especially for those processes that operate at temperatures less than 1,000ºC.
Electric motors and machines are often smaller, lighter weight, require less maintenance and have longer lifespans than traditional combustion systems. Electrified assets, therefore, are typically more cost-effective and use much less power than their fossil-fuel-burning counterparts. Manufacturers can also digitize electricity-powered assets, combining them with predictive solutions to reduce downtime and total cost of ownership. Full to partial electrification of processes can be achieved with three options, which are discussed in further detail in Part 1 of this Feature Report, Electrification of Industrial Facilities:
- Using heat pumps instead of reboilers and condensers
- Using electrical heating instead of steam or fuel-fired heaters
- Using electric motors instead of steam or gas turbines
- Using electrical boilers for process steam needs instead of coal-fired boilers
In these instances, commercial solutions already exist, and they do not necessarily require a significant process change. Chemical manufacturing organizations can focus on electrification as a series of quick wins, replacing a boiler or furnace running on conventional fuel within electric arc furnaces or powering compressors and pumps with electric motors, rather than as an all-or-nothing solution.
Looking at process specifics
A typical study to electrify a process can be outlined in five key steps [5]:
- Assess the current state, the energy demand and electrification opportunities
- Identify available solutions and study their fit
- Study implications through the full power system design
- Optimize electrical architecture
- Evaluate net impact and continue the cycle
In one case, a manufacturing organization was able to reduce about 100,000 metric tons of carbon dioxide equivalent (CO2e) emissions each year by switching from gas-powered turbines to more electrically driven solutions for large compressors and water pumps. The industrial facility’s energy needs were optimized by having a centralized power-generation and waste-heat recovery unit. With careful consideration of process needs, electrical drives were installed, which further optimized overall energy needs, creating cost savings in the process. Delving into more specifics helps exemplify how chemical manufacturing plants can electrify operations.
Steam cracking is a crucial process in chemical production. It’s also a large CO2e emitter, accounting for more than 300 million tons of emissions annually [6]. Steam cracking of hydrocarbons continues to be one of the main industrial processes employed to produce light olefins, building blocks for plastics, adhesives and detergents. Steam crackers operate at high temperatures (around 850ºC) to convert liquid or gaseous hydrocarbons into olefins.
While the technology to produce that kind of temperature using renewable energy sources is still being finalized, chemical manufacturers can begin planning to either retrofit existing steam crackers or replace gas-fired burners with electric heating systems. BASF SE (Ludwigshafen, Germany) and its partners recently began construction on a plant with “large-scale electrically heated steam-cracker furnaces” that will reach the 850ºC needed for continuous olefin production [7]. For less heat-intensive processes, electric heat pumps and boilers are available today that can take demand up to 350 to 400ºC. Electrification can also enable the use of carbon-free feedstocks for chemicals, which can further reduce the carbon footprint of chemical manufacturing processes.
Ideology barriers
Despite the many potential benefits of electrification, there are also challenges to its widespread adoption in the chemical industry. In fact, the industrial sector is considered one of the most difficult to electrify, in large part due to the complexity and diversity of its processes [8]. Add to those complexities worries about grid resiliency, and it is easy to see why chemical manufacturers stick with what is already working for them. The industry’s inertia comes from reasonable trepidation about mounting complexity, as well as technological, economic, regulatory and safety-related challenges.
Although many of the essential technological elements for electrification exist or are on the verge of being commercialized, every process requires tight integration with new assets and solutions and with other processes. Integration requirements can cause complexity to balloon because any process change creates a cascade of effects into various others. For example, researchers point to the fact that “using ethane from natural gas in steam cracking instead of naphtha from petroleum increases ethylene yields at the expense of lower propylene and aromatics yields [9].”
Moreover, converting electricity into heat and eventually chemical products is not currently an efficient or cost-effective process, as the steam-cracking example highlights. The good news is that plenty of technologies are moving along the maturation curve and should help reduce carbon emissions over the years to come [10]. Another challenge is the integration of electrification into existing chemical manufacturing processes, which may require significant infrastructure and capital investments. One firm reduced its CO2 output by electrifying turbines, but it only lowered its electricity consumption after optimizing its overarching energy architecture. Procurement and integration of electricity-powered technologies, as well as architecture redesign, can come with hefty upfront price tags, even if longterm costs eventually fall below a manufacturer’s fossil-fuel-powered baseline.
Finally, the regulatory landscape is one without official standards or frameworks for the electrification in chemical manufacturing. Unclear guidelines for how to proceed with new process changes can leave manufacturers concerned about the safety implications of new technology implementation in a holding pattern.
A mindset shift
Industrial organizations also tend to lack agility, a key ingredient for successful business transformations — in this case, catalyzed by electrification. Making strides in electrification will require a mindset shift as much as it will require procuring and integrating new assets and technologies.
Chemical manufacturers must do away with the all-or-nothing mentality and become comfortable with incremental changes. To enjoy the nimbleness of other industries, chemical manufacturers must first gain better visibility into their operations.
For example, today’s digital technologies allow manufacturers to match energy consumption to actual demand and look at grid performance and forecast consumption targets. This visibility can enable a more transitional approach. Rather than trying to make a binary swap away from fossil fuel to electrification, manufacturers can instead incrementally electrify areas that are “low-hanging fruit” or will provide the biggest impact for their investment. From there, they can measure success and repeat it with a new process or application.
Incrementally using the combination of digital technologies, such as monitoring sensors and software, and electricity, can also help to reduce business risks. Electrified processes can mitigate uncertainty related to the availability and cost of fossil fuels, in part through onsite microgrids that improve energy efficiency.
Chipping away at low-hanging fruit with electrification and digital technologies can also help manufacturers to gradually infuse their operations with more durable industrial equipment, resulting in lower maintenance costs and even opening the possibility of remote monitoring. Taking a slow and steady approach offers manufacturers a valuable multi-pronged tool against electrification challenges, many of which stem from upfront costs or lack of an available solution.
The electrification of chemical processing facilities has the potential to significantly reduce environmental impacts and improve the sustainability of the industry. However, plant owners must overcome the inertia that is an obstacle to modernize operations. To break out of a state of rest, firms can employ “Electricity 4.0” — the confluence of digital tools and electrification — to drive efficiency and sustainability. This approach to energy management, coupled with a mindset shift toward incrementalism, can set the stage for improvements for years to come. ■
References
1. U.S. EIA, Use of Energy Explained, June 2022; www.eia.gov/energyexplained/use-of-energy/.
2. The World Bank Group, World Development Indicators: Carbon Dioxide Emissions by Sector, 2017; https://data.worldbank.org/indicator/EN.ATM.CO2E.PC.
3. U.S. EIA, Manufacturing Energy Consumption Survey, Chemical Industry Analysis Brief, 2020; https://www.eia.gov/consumption/manufacturing/briefs/chemical/.
4. Roelofsen, O., Somers, K., Speelman, E. and Witteveen, M., Plugging In: What Electrification Can Do For Industry, McKinsey & Co., May 2020.
5. Chetty, S., Finol, R., Process Electrification and Application of Net-Zero Power Hub Solution, PCIC Energy Conference, Nov. 2022.
6. Van Geem, K., How to Reduce CO 2 Emissions of Steam Cracking Furnaces: The Million Dollar Question, AIChE Academy, April 2021.
7. BASF press release, BASF, SABIC and Linde start construction of the world’s first demonstration plant for large-scale electrically heated steam cracker furnaces, Sept. 2022.
8. Cleary, K., Electrification 101, Resources for the Future, March 2022.
9. Mallapragada, D., and others, Decarbonization of the Chemical Industry through Electrification: Barriers and Opportunities, Joule, Vol. 7, Issue 1, Jan. 2023.
10. International Energy Agency (IEA), Global CO 2 emissions reductions in heavy industry by technology maturity level in the Sustainable Development Scenario relative to the Stated Policies Scenario, 2070, Oct. 2022.
Authors
Poonam Narang is the director of product management for Motor Management Solutions for Schneider Electric, North America ([email protected]). She is passionate about solving customer problems through digital and sustainable solutions while moving her customers forward in their Industry 4.0 journey. Narang has over 15 years of combined experience in sales, strategy, business development and product management and has been with Schneider Electric for 4.5 years. Poonam holds a M.B.A. from Wake Forest University and a Bachelors in Engineering from Mumbai University.
Shailesh Chetty is a technical leader at Schneider Electric, located in Singapore ([email protected]). He has over 14 years of industry experience and has been with Schneider Electric since 2018. Prior to joining Schneider Electric, he held roles at consulting firms where he engineered large projects in the oil-and-gas sector, as well as power-plant projects in a number of industrial sectors. Chetty’s primary focus is to lead innovation in the new energy landscape for critical process industries, with special interest in process electrification, green hydrogen and energy efficiency. He holds an M.S. in power systems and electrical drives from Thapar University and a System Engineering L1 certification from Cesames in France.