Recent advances in gas-monitoring technologies can greatly increase worker connectivity and safety
With increased automation, expanding areas of operation and smaller teams of field workers, monitoring personnel and ensuring lone worker safety are serious challenges for the chemical process industries (CPI). When operators and technicians are in danger, it is crucial to know their location and react in a fast and effective manner.
Recent developments in portable gas detection leverage new technology for improved protection of the industrial workforce by connecting wearable detectors with the distributed control system (DCS) through the cloud to provide expanded visibility of plant floor operations — helping to keep workers safe and promoting better emergency response (Figure 1).
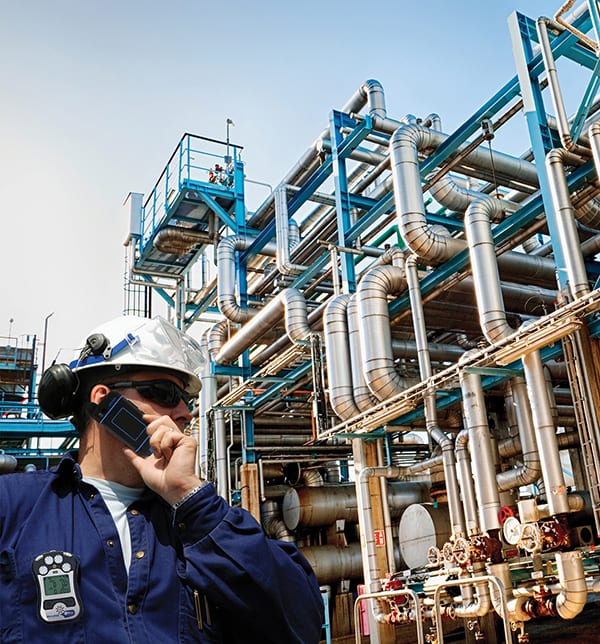
FIGURE 1. Gas detection has always been essential in CPI operations, but as manufacturing complexes have expanded and operations teams have shrunk, remote monitoring technologies are increasingly required to ensure safety
Today’s safety challenges
Process operations, such as those found in the CPI, often involve the use or manufacture of hazardous, flammable or toxic gases, which have the potential to escape and threaten those working within plants or possibly even those living nearby. Incidents may escalate, resulting in environmental damage, explosions or loss of life.
Plant workers have been carrying different types of portable gas detectors for years — one of them being their nose (Figure 2). So, it is already understood that detecting and avoiding noxious gases is a valuable capability. But some hazardous gases cause “olfactory fatigue,” meaning that the exposed person’s sense of smell diminishes over time.
Hydrogen sulfide (H2S) is a particularly hazardous gas commonly found at industrial sites. It has a distinctive “rotten egg” smell at low concentrations. H2S is relatively easy to detect at 0.01 parts per million (ppm), but above 100 ppm, it is no longer discernible. Olfactory fatigue can happen so fast that people can easily be overcome without realizing they are being exposed.
Low-oxygen areas are another significant threat to plant personnel. Human beings normally breathe air that is 20.9 vol. % oxygen under normal atmospheric pressure conditions. When the concentration of oxygen decreases even slightly, they immediately begin to feel the effects.
Tragically, there have been situations where a “lone worker” in an industrial facility succumbed to either a lack of oxygen or the presence of a toxic gas. By the time anyone became aware that the worker was in danger, it was too late.
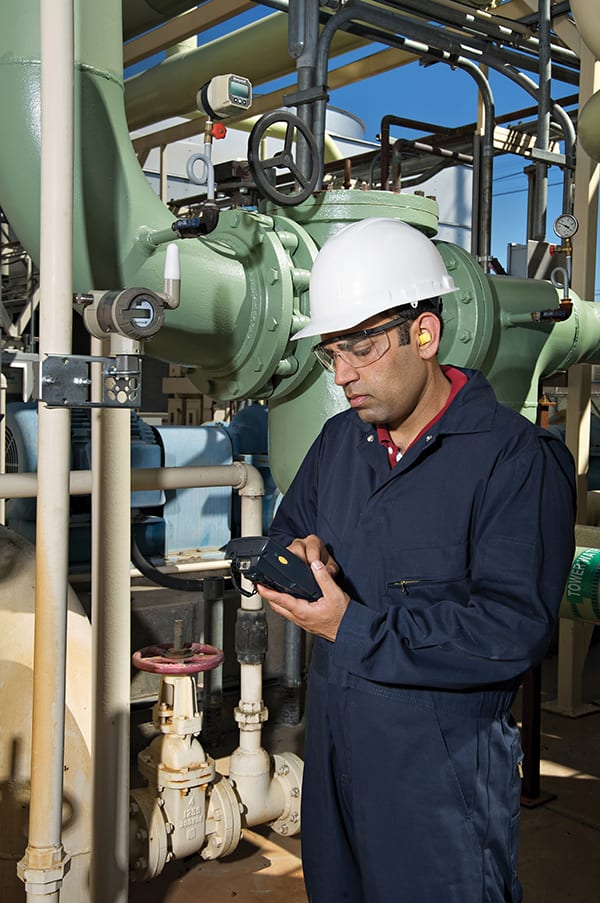
FIGURE 2. Workers in industrial facilities cannot always depend on their noses to detect unsafe gas situations, especially in remote areas where they might be working alone for long periods of time
Progress in gas monitoring
Portable gas monitoring was introduced over 50 years ago and has been evolving ever since. It is regularly used to detect toxic or combustible gas — or preferably to confirm the absence of such gases. Monitoring systems provide early warning of an abnormal situation before it becomes a significant threat.
Current technology has allowed the capabilities of portable gas-monitoring devices to be continuously extended. In the past, two detectors were needed to confirm there were no flammables, and the oxygen concentration was normal, before allowing entry into a confined plant space. Subsequent developments have allowed a single monitor to be set up with a pump and sampler to provide continuous indication with an alarm.
However, workers in many jobs face risks that require detectors that can handle multiple gases at once. These more complex multi-gas devices are also increasingly mandated by new regulations. A single detector measuring four or more gases can be worn by each person entering a confined space, giving them an audible alarm signal if there is a gas hazard right where they are standing. Furthermore, the price of multi-gas detectors has come down so far in recent years that many companies provide a personal detector to every worker in the plant.
Advancement of portable devices
Experience has shown that gas detection is a critical requirement in the CPI and many other industrial sectors. When it comes to portable gas detectors, device adaptability is a key factor. Since hazardous gases can present themselves in a myriad of environments — spanning different industries — detection solutions need to be able to identify a variety of threats.
Unfortunately, traditional gas detectors and lone-worker safety monitors function like smoke detectors, alerting only the wearer and those in earshot of a dangerous environment or incident, potentially leaving workers alone for hours without help. Furthermore, traditional employee-worn gas detectors are normally autonomous solutions, meaning safety personnel have no realtime awareness of what is happening with the device and the worker it is meant to protect.
In the control and instrumentation industry, research and development teams have been working on advanced detection technologies that are leading to the introduction of more connected gas-detection systems. Advanced wearable gas detectors have become a viable solution for alerting personnel to hazardous vapors in the workplace. They typically are designed to monitor H2S, carbon monoxide (CO), oxygen (O 2) and combustible lower explosive level (LEL) gases in a standard configuration, and can also be equipped to handle LEL, O2, CO and hydrogen cyanide (HCN), making them suitable for a wider range of applications. Connecting safety managers with field workers at all times using wirelessly connected devices greatly enhances visibility of worker hazards, status and location. Many of these newer devices may integrate not only gas-detection capabilities, but also decrease the risks to lone or remote workers by providing additional information, such as:
- Continuous worker location monitoring
- Movement detection for automatic man-down alerts to prompt automatic check and immediate notification when a worker is down
- Indication of compliance status for each gas detector
- A view of the site map in the event of critical alarms, showing the location and exposure status of personnel in the field
Increased connectivity
When it comes to industrial workers — especially those who do their jobs alone or in remote locations — the Industrial Internet of Things (IIoT) can do more than just get them better connected. Connected gas-detection solutions can enable plant- and enterprise-wide monitoring that harnesses the IIoT to provide realtime safety insights on gas threats, concentration, location, man-down and more.
One of the major trends in plant operation has been the evolution of smartphones and other handheld devices from potential distractions to effective productivity and safety tools. Some wireless multi-gas monitors can be paired with ruggedized, intrinsically safe smartphones to transmit gas readings over a cellular or satellite network (Figure 3). The phone can act as a personal communication hub for a worker, and can collect readings and alarms from, and send the data to, a remote system. Mobile devices and applications can also transmit worker information and location to the remote system, allowing safety managers to quickly react and provide necessary assistance in case of an emergency. The ability of safety managers in remote locations to access realtime safety and location data from a worker’s wireless gas detector decreases safety risks for offsite or lone workers and can help to expedite required intervention if an incident does occur.

FIGURE 3. Some gas-detection solutions feature connectivity with smartphones or tablets to transmit data over a satellite or cellular network
Other practical applications extend to carrying out a man-down rescue or plant egress with greater confidence and better outcome, or identifying an equipment malfunction in its early stages so that costly downtime can potentially be averted.
This safety intelligence enables users to do the following: immediately determine the location and severity of a gas alarm; get instant awareness of a worker in distress; make better decisions about rescue and evacuation; and proactively monitor their plant’s safety, compliance and productivity.
Furthermore, the location and gas status of workers, whether they are in a confined space during planned maintenance or walking throughout a process unit during normal operations, are always being monitored. Safety personnel are notified of any threats, while giving team members assurance that someone always has their back.
Lastly, as with any IIoT technology, robust cybersecurity technology can ensure that data remains protected from increasing external threats. Secure remote connections to networks employed for gas detectors require a solid defense-in-depth strategy. Plant operators must also have a proactive strategy for managing firewalls, intrusion detection and a host of other items.
An integrated approach
Portable gas-detection systems can now be securely integrated with the plant DCS via the cloud to help safeguard workers and speed up emergency response. Data from wearable gas detectors play a key role in revealing hazards, enabling proactive steps to improve safety and assist with learning from incidents.
With this integrated approach, for instance, control-room operators can identify and stop trace gas leaks, flag non-compliant or malfunctioning gas monitors for removal from the field and more quickly generate safety reports for regulatory compliance, as well as help reduce maintenance costs. In addition, safety teams can take advantage of powerful tools embedded in the DCS to provide detailed trending, reporting and data analysis of the gas detectors to further ensure safe operations.
By unifying connected wearable gas detectors with their DCS, and thus enabling two-way communications between field workers and operations and safety personnel, CPI engineers can gain effective safety monitoring from the control room console. This includes access to critical alarm reporting from wearable gas detectors for hazardous gases and radiation exposure. This allows operators to enhance their situational awareness and leverage control-room resources for faster initiation and support of emergency responses. More robust detection solutions also serve to eliminate extra load in the control room under non-emergency conditions.
For the CPI, the safety of plant assets and personnel is a crucial concern. Facilities must meet their safety needs while optimizing operational and business performance. Faced with this reality, they are seeking to utilize advanced gas-safety technologies to help ensure the lowest risk and highest level of protection for their most important resources. ■
Edited by Mary Page Bailey
Authors
Tony Downes is the global process safety advisor for Honeywell Performance Materials & Technologies (115 Tabor Rd, Morris Plains, NJ 07950; Phone: 973-455-3216; Email: [email protected]). He has been involved with process safety since 1979 when — while working at DuPont — he helped investigate an explosion due to a human error. He has launched process safety programs at Bayer Canada and Westlake Group and has worked at the corporate level in FMC and Honeywell to improve many aspects of their health, safety, security and environment (HSSE) and process safety programs. Downes is one of the first to receive the certified process-safety professional credential from the Center for Chemical Process Safety (CCPS).
Thomas Negre is currently the global marketing director for Honeywell Analytics (Javastrasse 2, 8604 Hegnau, Switzerland; Phone: +41 44 943 4339; Email: [email protected]). He manages the global product portfolio of BW Technologies and RAE Systems portable gas-detection solutions, as well as the fixed gas-detection lines, including wireless and software solutions. Negre joined Honeywell through the RAE Systems acquisition in 2013, where he was the vice president of product and marketing. He has been working for RAE Systems since 2004. Prior to joining RAE Systems, he was employed by General Electric (GE) in France, first as regional sales manager and then as a product manager for the Gas Detection & Process Instrumentation product line. Negre holds a M.S. degree in scientific & technical subjects from Marseille University and a M.S. in business and marketing from Marseille Management school.