Chemical regulatory compliance is growing in complexity as product sourcing and formulations proliferate and organizations expand into new markets on a global scale. Staying current with the requirements of international regulatory initiatives such as the Globally Harmonized System of Classification and Labeling of Chemicals (GHS) and the Registration, Evaluation and Authorization of Chemicals (REACH) adds to the challenge (CE, March 15, 2008, p. 38–47, and CE, June 15, 2008, p. 26–30).
A key compliance requirement of these initiatives is the proper management of Material Safety Data Sheets (MSDSs) and labels. Both GHS and REACH significantly impact the corporate strategy for MSDS management, as the regulations require affected companies to update these documents to maintain compliance. Comprehensive inventory management, thorough regulatory reporting and consistent MSDS and label authoring are three critical components of a REACH- and GHS-compliant MSDS management program.
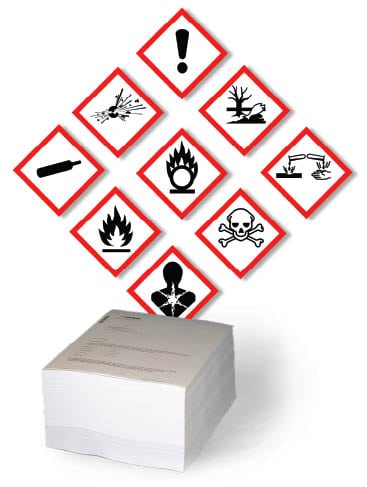
MSDS management
Accurate chemical inventory management is the cornerstone of any MSDS management program. Regulatory compliance mandates that companies obtain and maintain MSDSs for the raw materials, as well as for the full composition of mixtures. For REACH compliance, this requirement helps companies establish the category into which individual substances fall: manufactured within the European Union (E.U.), imported into the E.U., or purchased from a supplier within the E.U. For REACH, companies also must identify each substance’s tonnage and current classification.
Comprehensive regulatory reporting is also crucial to achieving GHS compliance. In addition to consistently tracking regulations, companies must track modifications made to ingredients, products, and quantities and inventories.
While authoring accurate and compliant MSDSs has always been a mission-critical obligation, the advent of REACH and GHS brings new challenges to this already highly demanding task. For higher-volume hazardous substances, REACH requires companies to attach an exposure scenario to the MSDS. The exposure scenario describes how the chemical can be used in a safe manner, with minimal risk, for the intended use. The exposure scenario can cover either each individual substance in the chemical product or describe the mixture as a whole.
The first registration deadline under REACH passed on December 1, 2010. Import or manufacture of high-volume chemical substances and of CMR- (carcinogenic, mutagenic and toxic-to-reproduction) classified substances is no longer possible unless the importer or manufacturer has registered under REACH. Many of the substances that were registered for the December 1, 2010 deadline have exposure scenarios. The registrant must attach the appropriate exposure scenarios to their MSDSs, and the company using these substances must then include the information from the exposure scenarios when they prepare and supply the MSDSs to their customers. The European Chemical Agency (ECHA) has recommended a four-section exposure-scenario format, but many different formats are being used. Work is ongoing to harmonize the information in the exposure scenarios and to establish a common XML format for data exchange.
As a step toward improved compliance, companies should obtain the necessary overview of the current regulations and detailed understanding of how they relate to their chemicals and their supply chain. Manufacturers, users and distributors should be aware not only of their own obligations but also of those to downstream customers and to employees. In addition, corporate product-stewardship staff must understand when these regulations are implemented by country in order to know how to properly plan.
GHS
GHS is the United Nations (UN) system for harmonization of classification and labeling of chemicals. GHS has already been officially adopted by certain countries in regions around the globe. Countries can choose to implement GHS in its entirety or implement only certain parts of the regulation, otherwise known as the “building block” approach.
The true complexity of the standard is realized when reviewing its implementation status in a sample of countries around the world. For representative comparison purposes, we have provided a brief overview of the status of GHS in the following areas: the U.S., Japan and the E.U.
The U.S. On September 30, 2009, the U.S. Occupational Safety and Health Admin. (OSHA; Washington, D.C.; www.osha.gov) released its proposal to modify the current Hazard Communication Standard (HCS) to conform with the GHS.
The proposed OSHA revisions include both philosophical and tactical changes to hazard communications, which have far-reaching implications for MSDSs and the authoring, publishing, distribution and management of labels. The proposal also includes revised criteria for the classification of hazardous chemicals, as well as changes to definitions and terms used in the standards, and new training requirements for employees. When the final rule is promulgated, companies will face many challenges, including re-evaluating how their substances and mixtures are classified, re-issuing MSDSs and labels, and training staff as appropriate.
After having accepted public comments until the end of 2009, OSHA has estimated that a minimum of 18 months will pass from the notice of proposed rulemaking before the final rule is promulgated. Companies will have three years from promulgation to come into compliance with the final rule and two years to implement training requirements on the final regulation. Once the rule is final, companies can begin implementation. However, in accordance with a letter of interpretation from OSHA on October 6, 2009, companies can begin following the E.U. GHS-label format for their OSHA labels as long as the labels also comply with the current HCS.
In addition, 26 U.S. states and territories have their own OSHA-approved plans. The 26 are: Alaska, Arizona, California, Connecticut, Hawaii, Indiana, Iowa, Kentucky, Maryland, Michigan, Minnesota, Nevada, New Jersey, New York, New Mexico, North Carolina, Oregon, Puerto Rico, South Carolina, Tennessee, Utah, Vermont, Virginia, Virgin Islands, Washington, Wyoming. They will have six months from promulgation to adopt comparable provisions of the final standard. In the meantime, each individual state plan will remain in effect until it adopts the required revisions.
Provided the legal process proceeds as planned, companies would be allowed to issue MSDSs and labels for the U.S. market according to the changed rule, based on GHS classification, no earlier than July 2011, and all existing MSDSs and labels would have to be updated in accordance with the new requirements no later than July 2014. In comparison, MSDSs for the European market had to be in line with the E.U. GHS implementation no later than December 2010 for pure substances and by June 2015 for chemical mixtures.
The label requirements will involve changes in the printing process and most likely will require many companies to invest in new label printers. Labels on products that are shipped outside the U.S. must have the chemical hazard pictograms with a red frame, signal words and the required hazard and precautionary statements. It is still being determined whether or not empty frames will be accepted on the label and whether or not labels for products sold and used exclusively in the U.S. can have the frame printed in black.
Japan. In Japan, the Industrial Safety & Health Law (ISHL; December 2006) currently details requirements for MSDSs and labels. The ISHL provides a list of substances that are subject to MSDS and label requirements, and also provides a classification results list, which details the classification of about 1,500 regulated chemicals. The Japanese Industrial Standard (JIS), which specifies the standards used for industrial activities in Japan, also has requirements for labels (JIS Z 7251:2006) and MSDSs (JIS Z 7250:2005). Recently JIS Z 7252:2009 was published for the standard of GHS classifications for health and environmental hazards.
E.U. The European Union is currently in a transitional period with regard to GHS. The European Parliament finalized and issued the Regulation (EC No. 1272/2008 on classification, labeling and packaging of substances and mixtures — the CLP Regulation) in late 2008. An amendment bringing the CLP in line with the third revision of the GHS was drafted in 2010.
The CLP Regulation provides the following transitional periods for classifying and labeling hazardous substances and mixtures:
• Substances must be classified, labeled and packaged according to CLP from December 1, 2010 forward
• Mixtures can be classified, labeled and packaged according to the Preparations Directive until June 1, 2015
• Supplemental labeling information, in line with the old labeling system’s requirements, is still applicable under the CLP
The transitional periods for re-labeling and re-packaging of substances and mixtures placed in the supply chain before December 1, 2010 are postponed until December 1, 2012 and June 1, 2017 respectively.
REACH
The E.U.’s REACH regulation went into effect on June 1, 2007 — sometimes simplifying, but also complicating, the compliance work for companies manufacturing in, importing into or exporting from European countries. As a result of the new legislation, all companies manufacturing, importing, distributing or using chemical substances (on their own, in mixtures or in articles) in Europe, are required to closely examine their chemical inventory for substances within the scope of the regulation to ensure compliance.
Key components of REACH mandate the following:
• Registration of manufactured/imported chemical substances
• Increased information and communication throughout the entire supply chain
• Evaluation of some registered substances
• Authorization for use of substances of very high concern
• Restriction of the use of certain substances for specific applications
The scope of REACH is vast, and there are several issues that could impact a company’s ability to meet its obligations under REACH, including changes to the content of MSDSs. Under REACH, additional information from manufacturers is required and the information must be aligned with that associated with the registration of the substance. When an exposure scenario has been required as part of the REACH registration of a substance, every safety data sheet for a product containing this substance must have the exposure scenario attached.
Choosing the right tools
As many companies realize, establishing GHS and REACH compliance is difficult. However, there are service providers who can help companies stay ahead of the curve with solutions for identifying and managing the increasingly complex and changing global chemical-regulatory obligations associated with GHS and REACH. These vendors can help address the new requirements and associated chemical regulatory information needed for compliance management as they arise.
For example, there are several commercially available content tools that can be used to feed chemical regulatory data into corporate EH&S (environmental, health and safety) and MSDS authoring systems. These integrated data tools provide efficient change management and regular updates as regulations change and new ones are released. These tools can help ensure correct, consistent GHS classification and labeling according to the U.N. purple book and also take into consideration the national deviations and other national regulations. Document templates for producing MSDS, labels and other hazard communication documents and multilingual phrase libraries can complete the content suite for efficient production of accurate documents.
Companies also may choose to employ outsourced services for their GHS classification of substances and mixtures as a separate service or as part of outsourcing MSDS and label authoring.
In-house MSDS authoring staff may want to adopt an authoring platform that will help generate hazard communication documents to meet GHS-related, international-regulatory compliance and business requirements. Such a platform should provide full support of hazard communication, classification and labeling requirements to generate globally compliant MSDS and label documents as well as business- or user-definable documents, such as technical data sheets, product data sheets, hazard summaries and product stewardship summaries. The system should use algorithms to accommodate the requirements outlined in the GHS. This consists of the classification of substances and mixtures according to their health, environmental and physical hazards and hazardous communication requirements for labeling and MSDS.
For inbound vendor MSDS management, users will want to search, print, view and Email vendor and raw material safety data sheets in a company-specific database via a Web-browser interface. As GHS requirements increase the burden of vendor MSDS management, a robust MSDS management system can help reduce the time and resources necessary for effective compliance management.
Compliance help is available
Creating, analyzing and managing globally compliant MSDSs, product label content and hazardous materials transportation documents that reflect both GHS and REACH requirements can be extremely challenging. Strong processes, applications, systems and service providers are needed to support the various aspects of compliance management. Companies that are impacted by GHS or REACH, or both, can seek assistance from providers who are well versed in data and other content and information as they relate to global EHS regulations and who thoroughly understand the global regulatory environment. These providers will be able to assist in implementing GHS and REACH compliance activities into the organization, and can help facilitate compliance with these increasingly complex and changing global, chemical regulatory obligations.
Edited by Scott Jenkins
Authors

Jytte Syska is managing director of 3E Company Europe ApS (Lyngbyvej 20, 3, DK 2100, Copenhagen, Denmark. Phone: +1-760-602-8700; E-mail: [email protected]) and president of Ariel operations. Syska has more than 20 years of experience as an environmental, Health and Safety (EHS) regulatory expert. Prior to her present duties, she spent several years as 3E’s vice president of international operations. Syska has also held the position of director of occupational health and toxicology for the prestigious Danish Toxicology Center (DTC). Syska holds an M.S. degree in civil engineering from the Technical University of Denmark. She is fluent in Danish and English, and reads and understands German, French, Norwegian and Swedish.

Tamie Webber is director of product management at 3E Company and is responsible for product management initiatives, product planning and strategies and product development for 3E’s product line, including MSDS distribution and management, emergency response, regulatory reporting, training and waste services. She joined 3E after several years of marketing and product management experience in the chemical distribution and high-tech industries. She has worked for Great Western Chemical and Intel Corp. She holds a B.S. degree in finance and marketing from the University of Oregon.